Digital Twinning
Building a digital replica of an industrial process which is so good that manufacturing companies use it for making decisions on the real process. This is possible. In Digital Twinning, as this is known, we bring together data, models, and the business process, and create a digital life cycle alongside the physical one.
From factory data to flexible programming, everything revolves around digitalisation these days. As long as the Dutch manufacturing industry uses smart methods to connect products, machinery, and people, and applies state-of-the-art technologies, it will be able to maintain its international competitive position. Digital Twinning is one of the focus areas that enables us to achieve this.
What is Digital Twinning?
‘With Digital Twinning, we conduct research in order to do things digitally, so that we don’t have to carry something out in reality. Or we use it to prevent situations from arising in the real world,’ explains Jeroen Broekhuijsen of TNO. ‘Take a dyke that you’re doing research on. You’re not going to breach it for your research, with all the terrible consequences that would bring. With a Digital Twin, you do breach it, but digitally.’
Steps towards creating a Digital Twin
The central question that precedes Digital Twinning is what an entrepreneur wants to achieve. One person may want to analyse a virtual product very precisely in a 3D animation. So they know for sure that it will stay in one piece during use. For another, it’s the chance to monitor and analyse a production process, and compare it with the twin, which calculates the optimum process. This helps optimise the schedule and shorten throughput times.
Once the goal has been established, the entrepreneur needs to decide on the component for which a Digital Twin has to be made. We’ve developed a 7-step method for this purpose. Among other things, we investigate what information is needed to make a Digital Twin, how we ensure that it’s accurate enough, and what decision the entrepreneur is going to make with the results from using Digital Twin technology.
In workshops, we look at the step-by-step plan together with entrepreneurs. ‘After a couple of afternoons, you’ve got your plan ready and you can get down to work. So it’s really practical. We also have in-house expertise to help develop models or access data from machines.’
Practical work with field labs
Companies that want to do practical work in order to learn from it are very welcome in our field labs. The Digital Factory Composites field lab, for example, focuses on the digitalisation of the production process for composite products. The aim is to slash costs dramatically and enable the use of composites in many more products.
We’re also active at European level. ‘We’re one of the coordinators of a large EU project, in which we look at what’s necessary to get SMEs to embrace the Digital Twin technologies,’ adds Broekhuijsen. ‘Moreover, we offer an assessment tool that companies can use to define their vision of digitalisation. Because without that vision, you can’t really make a start.’
Many varieties of Digital Twinning technology
Digital Twinning can be deployed in various ways. For example, with a company, we can make all the data required for control accessible outside the machine in programmable logic controllers (PLCs). This allows a technician to make the correct diagnosis in the event of a malfunction. Another example is replicating a machine virtually in 3D, so that the company can simulate the production process and optimise it.
‘So, there are many varieties of Digital Twins,’ says Broekhuijsen. ‘We set up the IT in order to link data to models. With these, you can calculate all kinds of scenarios and make the right decisions based on the results. Sometimes companies have their own model and sometimes we build it. Sometimes they have their own data and sometimes we help them obtain it. Everything’s possible.’
Want to know more or join in?
As an integrator or end user in the manufacturing industry, would you like to work with us to get results with Digital Twinning for the digital factory of the future? Contact Jeroen Broekhuijsen directly.
Get inspired
TNO spin-off Scenexus secures 1.6 million euro investment


Scale up: manufacturing throughput and quality
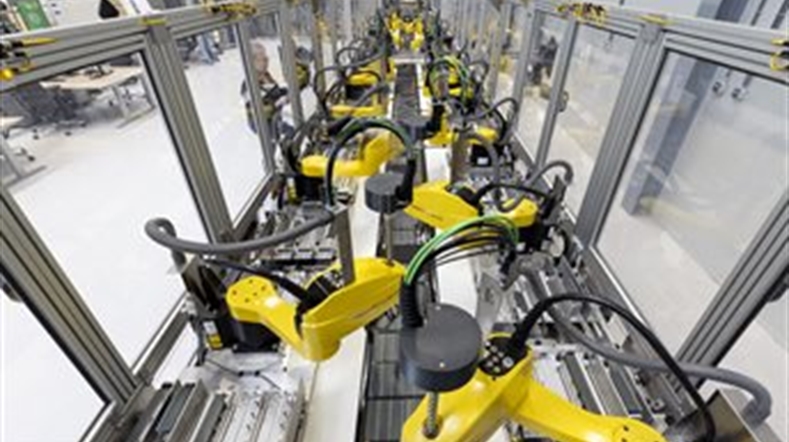
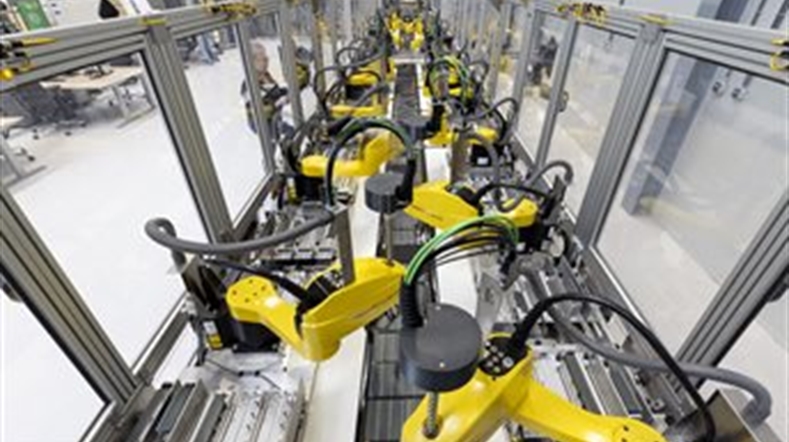
Non-destructive inspection
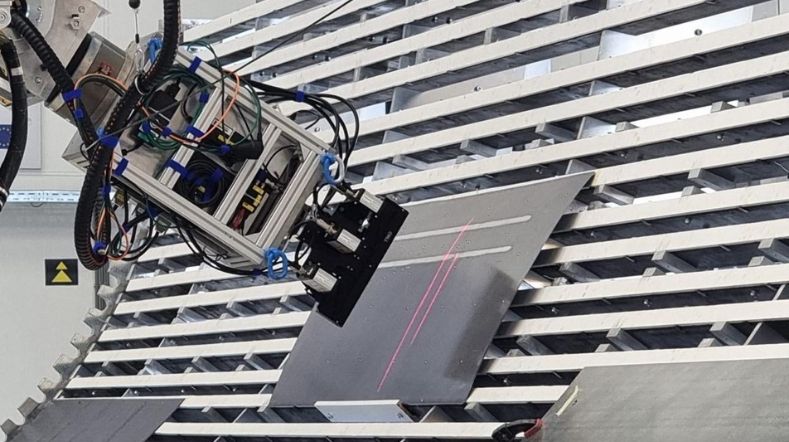
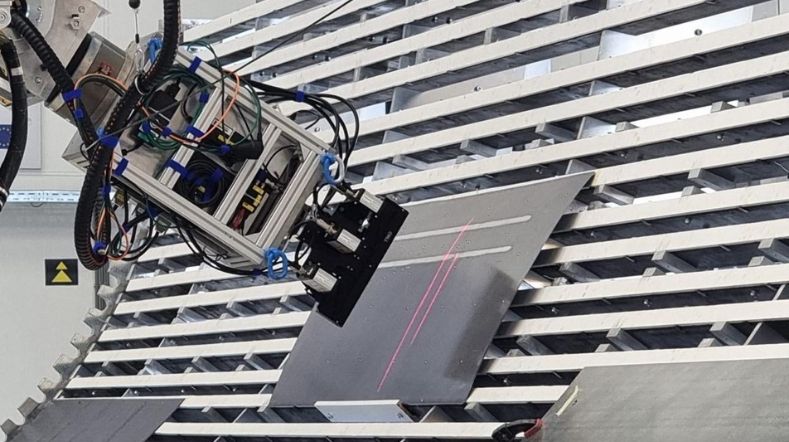
Strategic autonomy: digitalisation and value chain integration
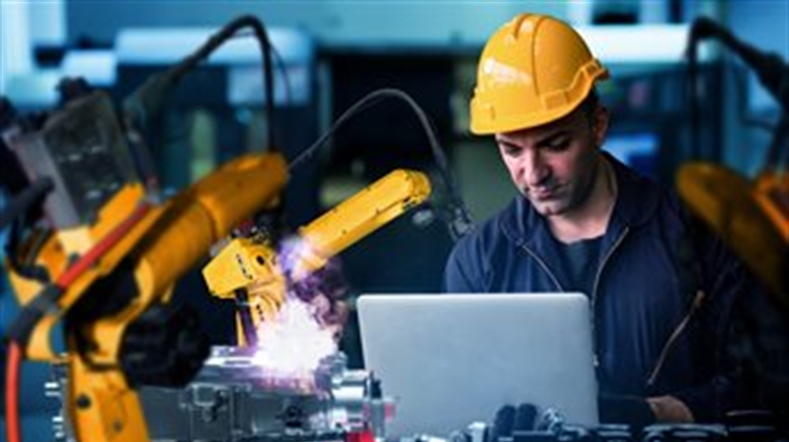
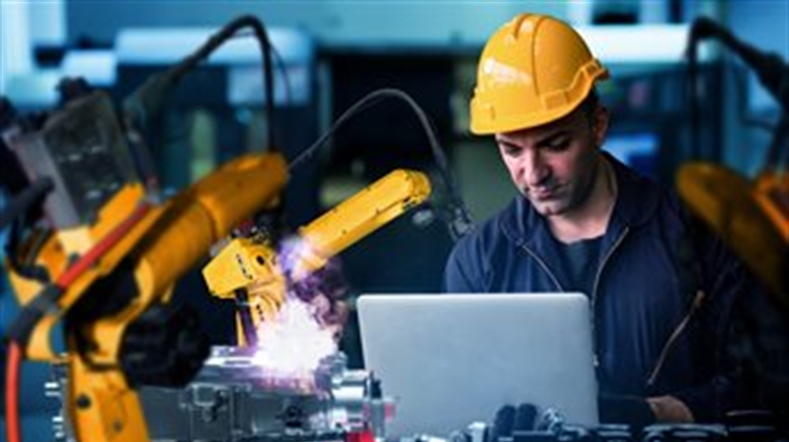
Productivity: manufacturing variability
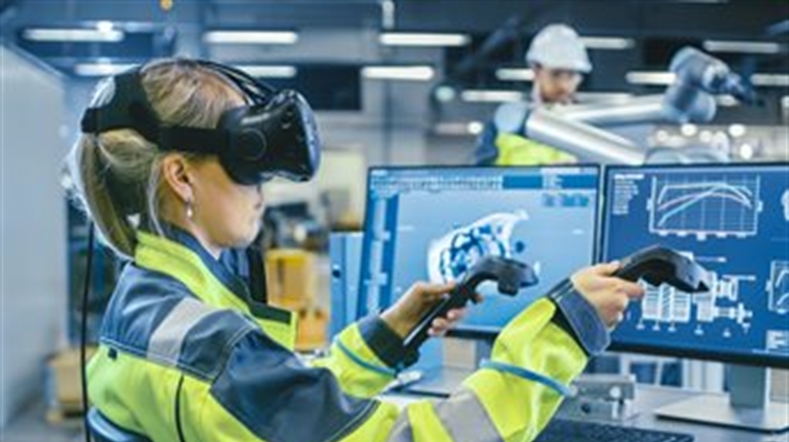
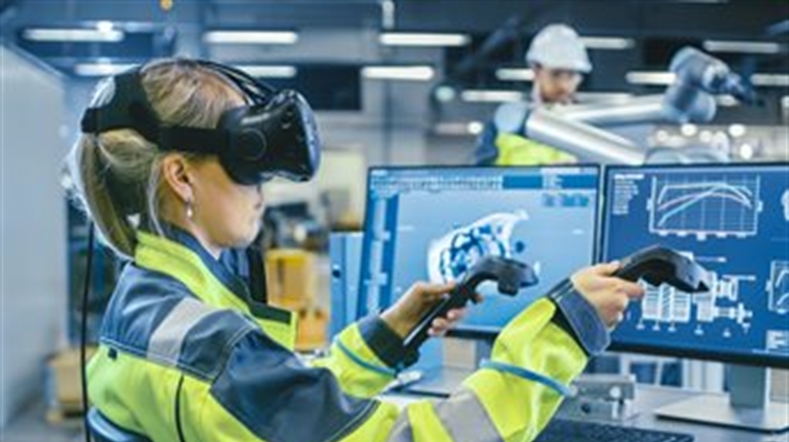