Flexible manufacturing
Enabling the production of one-off products at the same cost as mass production. That’s what Flexible Manufacturing is all about. The main challenges are to ensure that smart robotics, software, smart sensors, cells, and production machines all operate flawlessly in unison. And that they are able to adapt to situations without human intervention.
The transition to flexibility is one of the greatest challenges facing manufacturing industry. Factories must be able to switch production without making any errors, i.e. with zero defects. Nor do they want to waste any time, which means zero programming. All of this in combination with a product range characterised by low volume, high mix, and high complexity.
Combining automation with flexibility can be very tricky
Robotics is a major innovation that can benefit manufacturing industry. But programming can be quite time consuming, so manufacturers tend to favour human workers over robots when it comes to a small series of products. Thus, TNO staff have noticed that company robots are often standing idle, while this very technology could enable the manufacturing company to produce goods with no loss of time.
However, combining the automation of production with flexibility can be very tricky. Many of the adjustments needed when switching from product A to product B are done manually. These include reconfiguring a production line, reprogramming robots for a different task, generating new assembly instructions, and rerouting the logistics of components.
Digitisation is the ultimate key
Digitisation can offer a solution in situations where manual adjustment is still common. “The future of manufacturing industry lies in increasing autonomy,” says Gregor van Baars of TNO. “That is the ultimate key to the challenge of successfully combining automation and flexibility. We are convinced that it is feasible for companies to operate competitively using autonomous flexible production.”
Help from intelligent robots
TNO is already working on the realisation of that vision. Firstly, we develop practical solutions and use these to meet the first-line needs of manufacturing industry as quickly as possible. For instance, a zero programming solution that automatically plans the robot paths needed for each new product is already having a significant impact on productivity.
At the same time, TNO is pushing ahead with knowledge development. Our approach is to close any gaps in the total solution and to merge partial solutions into an integrated whole. By this means we are paving the way for the digitisation of manufacturing industry. If robot applications are supplemented with camera vision, for example, this enables intelligent robots to ‘see’ what is happening while they are performing their tasks and to react, if necessary. This refinement of flexible production represents another step towards autonomy.
Linking technology to applications
But there is more to robotic solutions than robots alone. Mr van Baars explains: “This is not something that can just be dropped off at the factory and left to get on with things all by itself. There is more to it than that, such as integrating the technology into the existing workflow. TNO is committed to developing integrated solutions and to actually linking the technology to the application.”
Coming up with workable solutions
In recent years, people have come to realise that we need to take advantage of these opportunities. A number of projects are being launched. Meanwhile, in various field labs, TNO and all of the parties involved are jointly seeking workable solutions. We invite companies to come and take a look at what we are doing, to see for themselves what is already possible. In addition, they can make use of this safe environment to test new solutions and to ask questions.
Get inspired
Partnering for mutual progress


TNO spin-off Scenexus secures 1.6 million euro investment


Scale up: manufacturing throughput and quality
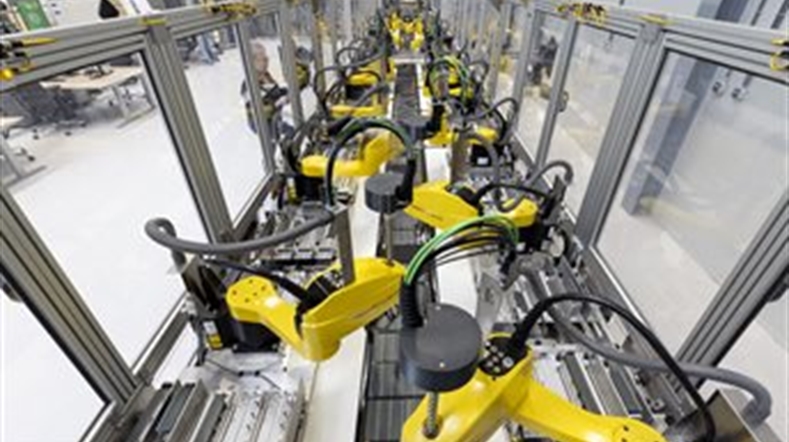
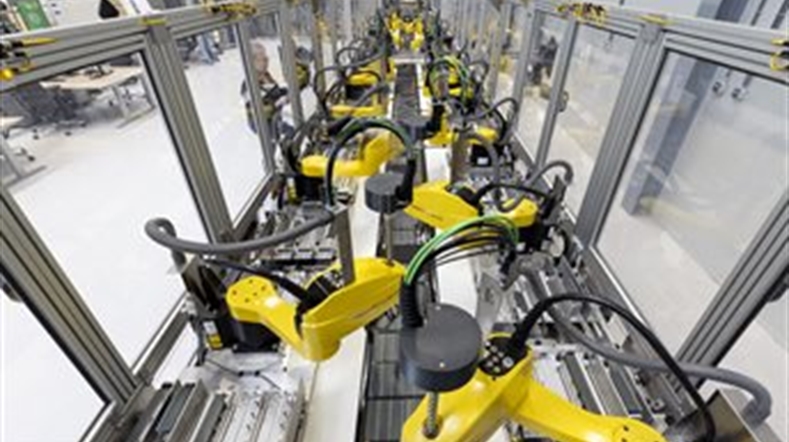
Non-destructive inspection
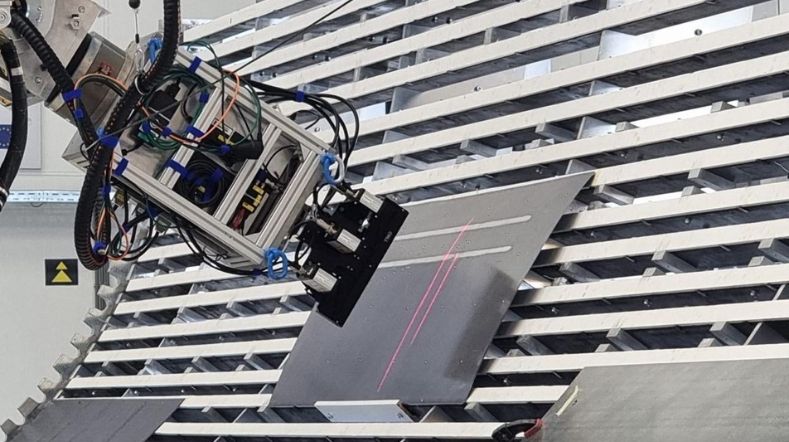
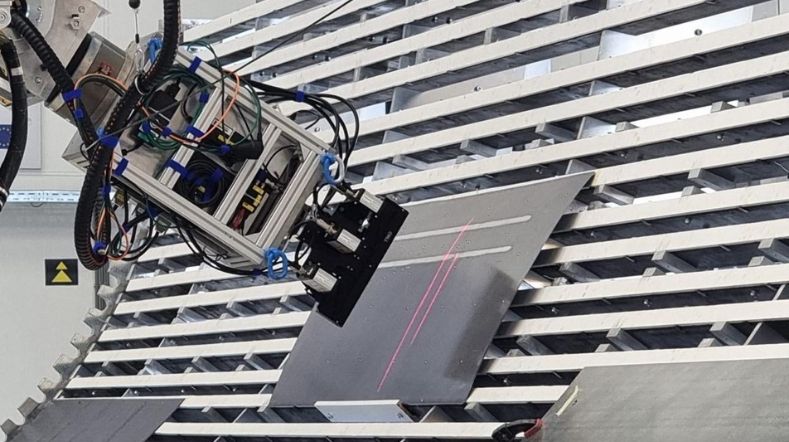
Strategic autonomy: digitalisation and value chain integration
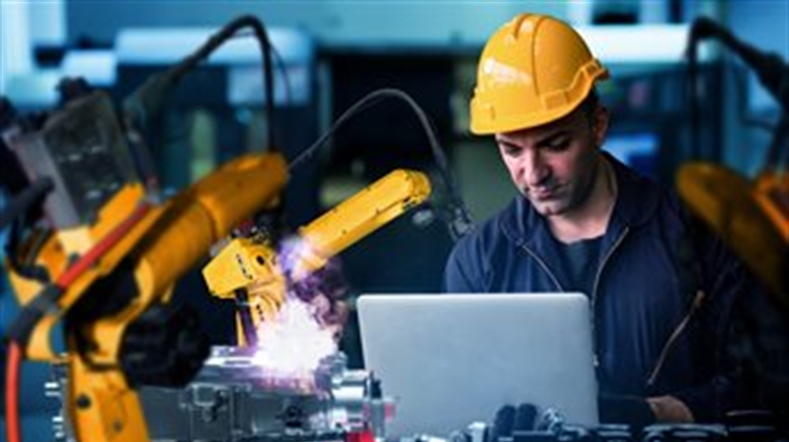
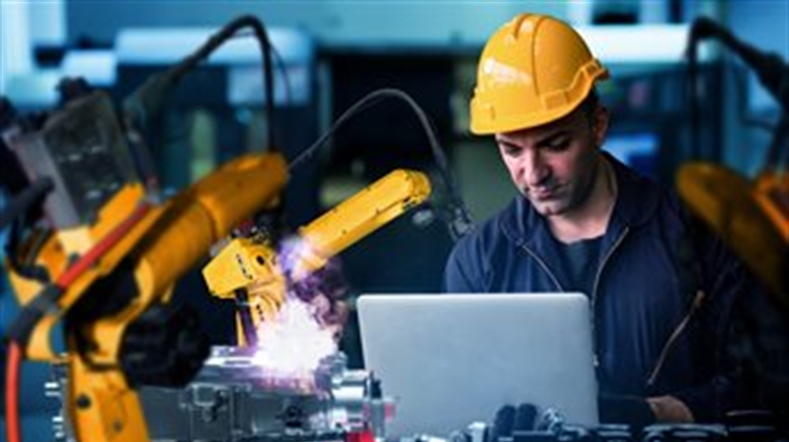