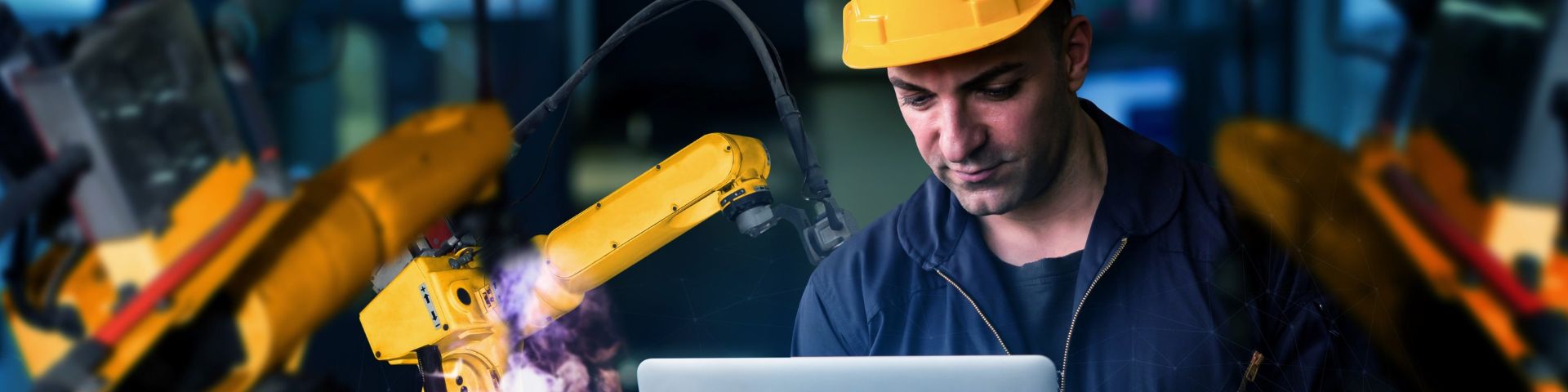
Strategic autonomy: digitalization & value chain integration
Which production processes lend themselves to far-reaching forms of automation? What kind of digitalisation shift is needed to achieve more efficient or higher quality production? And what does that mean for the design and implementation of production processes? And how can we easily and securely share data with suppliers, service providers, and clients? These are important questions for manufacturing companies looking to move to smart manufacturing. We help companies on the path towards their desired digital and autonomous production environment.
Cyber Physical System
TNO focuses on unlocking data through a so-called digital plug, modular data architecture, cyber security, and AI applications that bring together the models and processes of a manufacturing company in a cyber physical system, or ‘digital twin’. The challenge is to build a digital replica of an industrial process that is so good that companies can see in advance on the screen what an appropriate solution would be, and then base their decisions for the real process on that.
Future-oriented approach – digital twinning
The added value of a digital twin depends largely on what a company wants to achieve with it. Creating such a digital replica only makes sense if it generates new insights that contribute to the intended goal. Is that actually the case? Then TNO will deploy the following three components of the digital factory to help a company move forward:
- Structuring: during this consultancy phase, TNO specialists will look at what is needed to get the clearest possible picture of the digitalisation approach.
- Specifying: what machinery and software will be needed to achieve the desired production method? And how should they be installed to get the best results?
- Vision: here, we look a little further into the future, painting a picture of what an ideal autonomous factory would look like. In other words, a concept study, with the great advantage that it also immediately formulates future requirements, so that they can be taken into account at an early stage.
Turning digital knobs
Is the goal to make as many products as possible in as short a time as possible? In this case, a different approach is needed than when there is a strong focus on quality. This is where being able to turn some knobs beforehand in the digital world of the digital twin can be useful. Without too great an investment, this will quickly reveal which adjustments will lead to the desired production process, while also immediately revealing, for example, the impact on the degree of robotisation, efficiency, lead time, and costs. And these are all areas where companies want to have as clear a picture as possible before making the necessary investments.
Smart data sharing
Those who want to produce competitively must design their production process flexibly and efficiently. This requires smart combinations of data from machines and ICT systems. But it is not just about collecting data. You need to also be able to share the data securely and confidently with partners. A significant challenge is making solutions scalable. We make this possible with data sharing. The result is a ‘smart supply network’, a network of flexible and connected factories whose application is not limited to one company or a few machines.
Improving production processes
With data sharing, we are working on solutions to share data within or between factories. Applications include better collaboration between clients and suppliers and achieving smarter production processes. Think of improved production planning, optimised production scheduling, or overall equipment effectiveness (OEE) improvements that consider machine availability, output, and quality delivered. But which also prevent errors and reduce maintenance costs. We rise to the challenge of making this happen, even when different machine or software vendors are involved.
It is important that manufacturing companies are in control, so that each party can decide who gets what data. Technologies such as the European International Data Spaces (IDS) and new cloud technologies such as GAIA-X play an important role here.
Blueprint for data sharing
In many applications where data is collected, analysed, and used, we see that companies have to cross a threshold. This is why it is important to work together with the technology provider. Smaller manufacturing SMEs do not always have the same resources and options as larger companies.
Therefore, more standardisation is needed. We are working on a blueprint for data sharing in the manufacturing industry. This blueprint will provide manufacturing companies with an overview of standards and technologies for their technology suppliers. But it will also help suppliers; by standardising interfaces, they can expand their market and deliver new innovative products faster.
Artificial Intelligence and real-world challenges
One of the key technologies that will need to be strategically deployed concerns data and AI. A technology that requires radical change and innovation in the primary process of the entire manufacturing value chain. Manufacturing companies must now anticipate how to adequately unlock data in production processes to harness the power of AI applications. This can be achieved with the deployment of a so-called ‘digital plug’ to make the data interoperably accessible and applicable in a digital twin.
Real-time insight into the stage of the production process, continuous analysis to identify potential bottlenecks, and specific instructions to help human operators run the process optimally. And that is just a fraction of what is already possible thanks to robotics and digital technology. After all, these are real-world challenges and real prototype solutions.
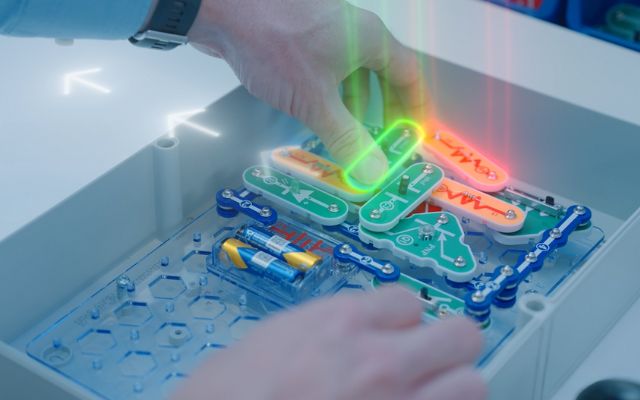
Remanufacturing lab
With the remanufacturing lab we offer a test and experimentation facility to AI technology providers, system integrators and end users to develop and test AI technologies that will enable industry to transition to digital and circular operations.
Practical examples and business cases
TNO advises companies on digitalisation and is involved in projects as an advisory and R&D partner to help develop the manufacturing industry. Some examples of these projects:
The smart connected supplier network (SCSN) enables effective and simple data sharing in the supply chain.
Harnessing the power of data requires interoperable data from the factory shop floor, the enterprise, and the supply chain. To this end, TNO is working with industry to develop digital connectors.
A digital product passport (DDP) is essential in the transition to a circular economy. A DDP is used to monitor the carbon footprint and environmental impact of a product throughout its lifecycle – from design, production and use to end-of-life, including repair, reuse, and recycling of the product.
Modelling with AAS and RDF in Industry 4.0. The asset administration shell (AAS) is a key building block in creating unified data architecture. It makes data management quickly accessible and enables data to add value to achieve improved business results.
AI is going to cause disruptive change in the manufacturing industry. The white paper, AIM-NET AI IN MANUFACTURING, provides insight into the different application areas and stages of implementation.
TNO has developed a low-threshold digitalisation programme for SMEs, scale-ups, and start-ups. Together with a number of other companies, a company-specific digitalisation roadmap is being developed, and the first steps towards digitalisation on the shop floor are being taken. Instant results by using data smartly for your business.
The NXTGEN programme will work hard over the next seven years to develop smart solutions within six core domains: agrifood, biomedical production technology, energy, composite, laser-satellite communication, and semiconductors. At the crossroads of these domains, systems technologies, systems engineering, and smart industry, play a crucial role.
View the webinars
Watch various webinars on topics such as a blueprint for a smart and connected factory, the European cloud for the Dutch manufacturing industry, and more.
In the BIC Digital Factory project, we are working with partners to develop a blueprint for a smart and connected factory: which standards to use, how to connect different systems, and what should the role of the cloud be? We provide some initial examples in this webinar.
In Europe, there is talk of ‘GAIA-X’, a new cloud environment that should allow entrepreneurs to stay in control of their data. Although it is still in its infancy, we are exploring what role GAIA-X could play for the manufacturing industry. We go into more detail in this webinar of the Data Value Center for Smart Industry.
Webinar on GAIA-X, which focuses on the question: ‘Should we move towards a European cloud for the Dutch manufacturing industry?’
Sharing data with clients and suppliers – what is involved? What role can new developments such as the smart connected supplier network (SCSN) play here?
The webinar’s programme contains three parts on the theme: Achieving added value using data:
1. Data cases for SMEs
2. Lifelong learning
3. Sharing data in the supply chain
How do smarter production logistics with AGVs, data-driven production planning, and data sharing in the supply chain relate to each other? We address this question in this technology update from the Brainport Industries Campus.
Progress in circular packaging for soups and sauces
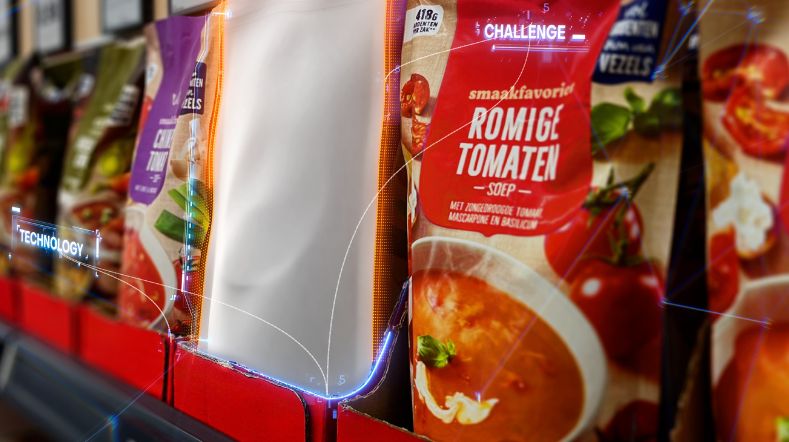
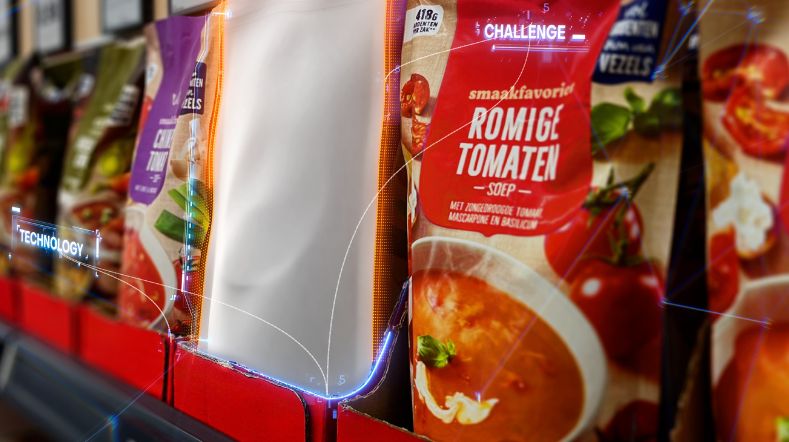
Gas production shows a slower decline than in the past decade
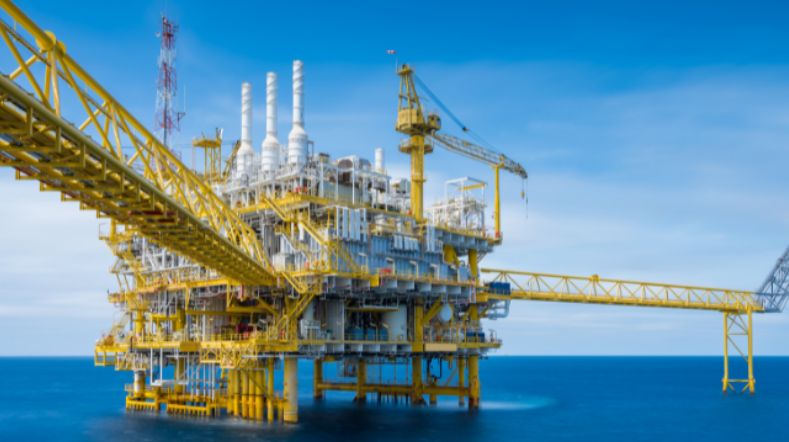
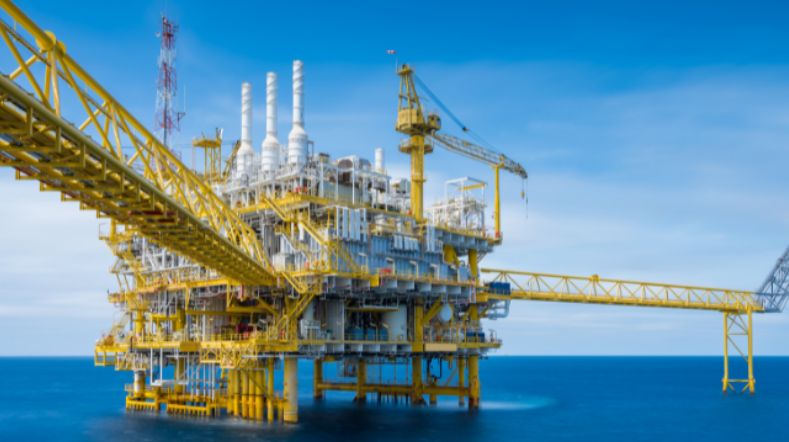
Biobased plasticizers: from compliance to competitive edge
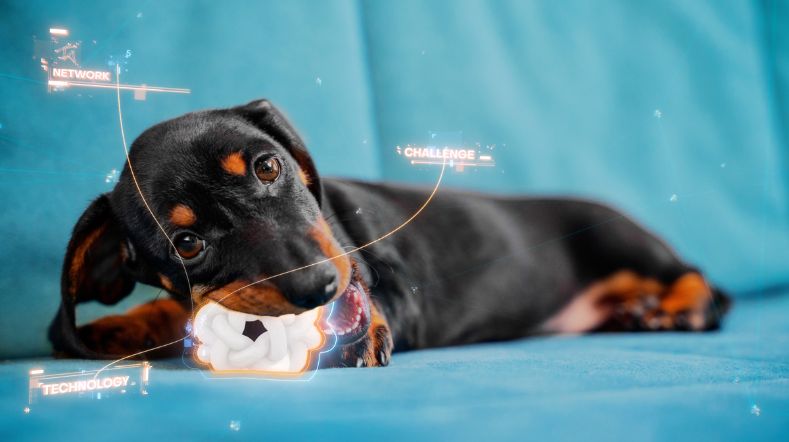
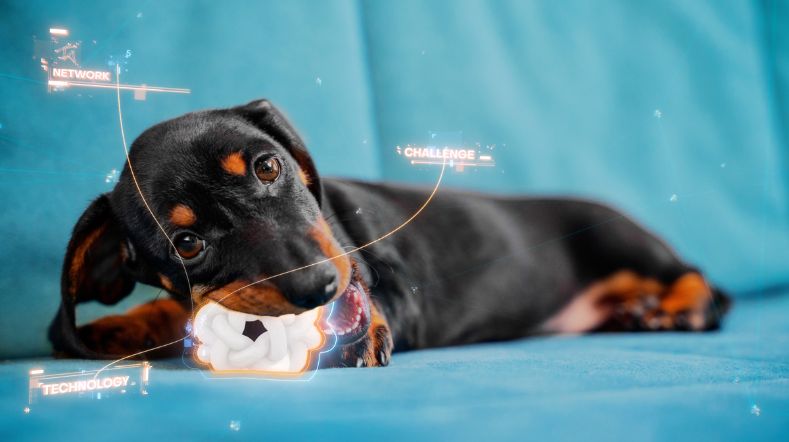
Microplastics in clothing
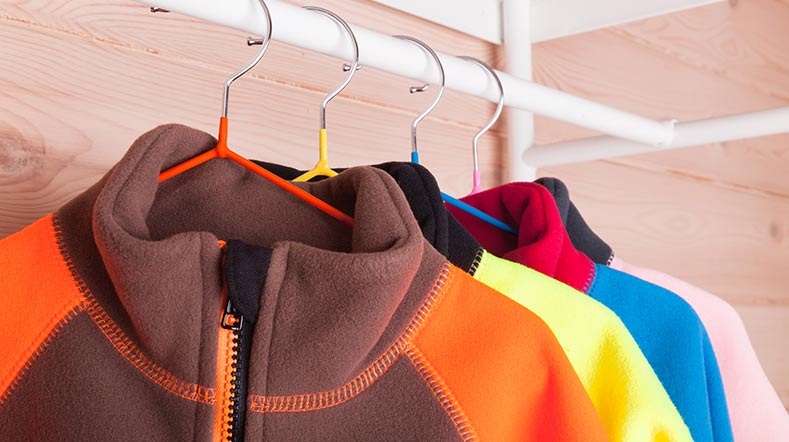
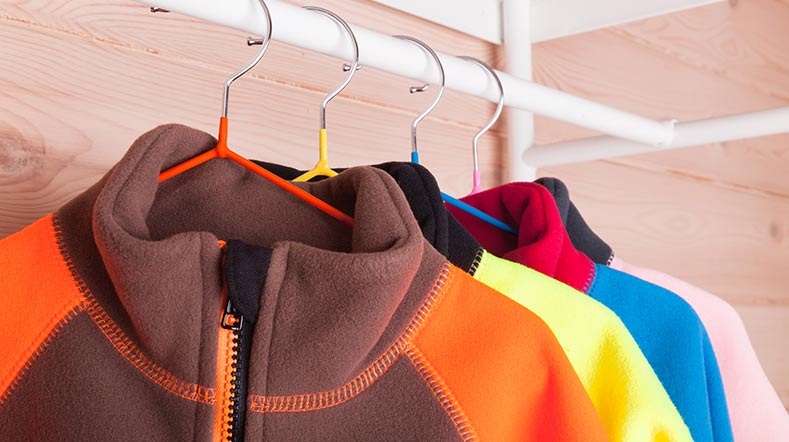
Japanese DNP opens Dutch R&D hub in partnership with TNO
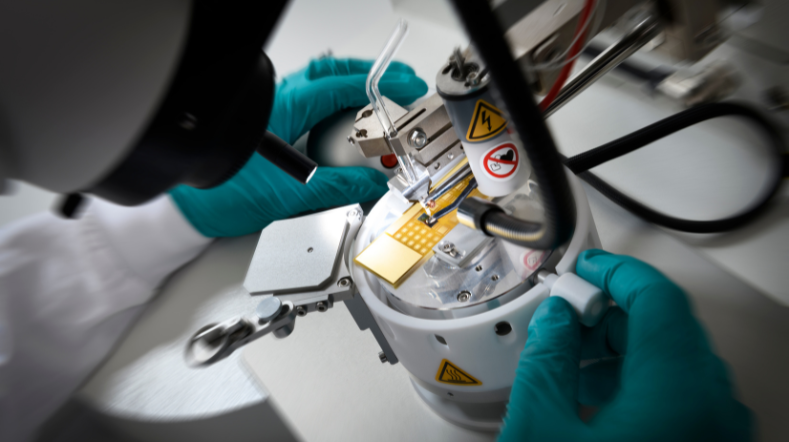
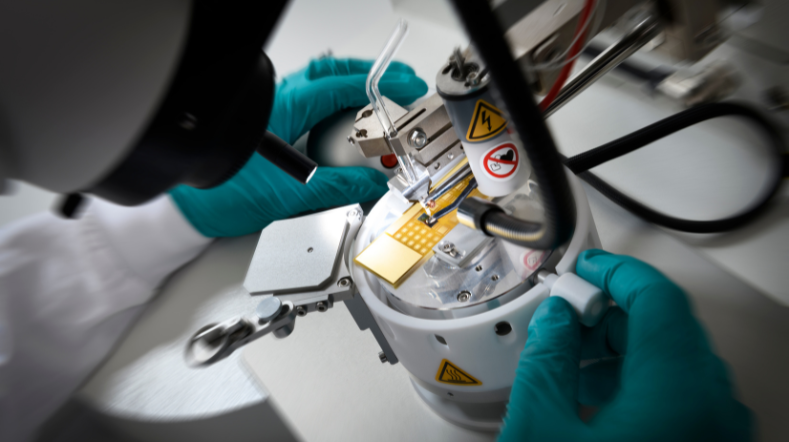