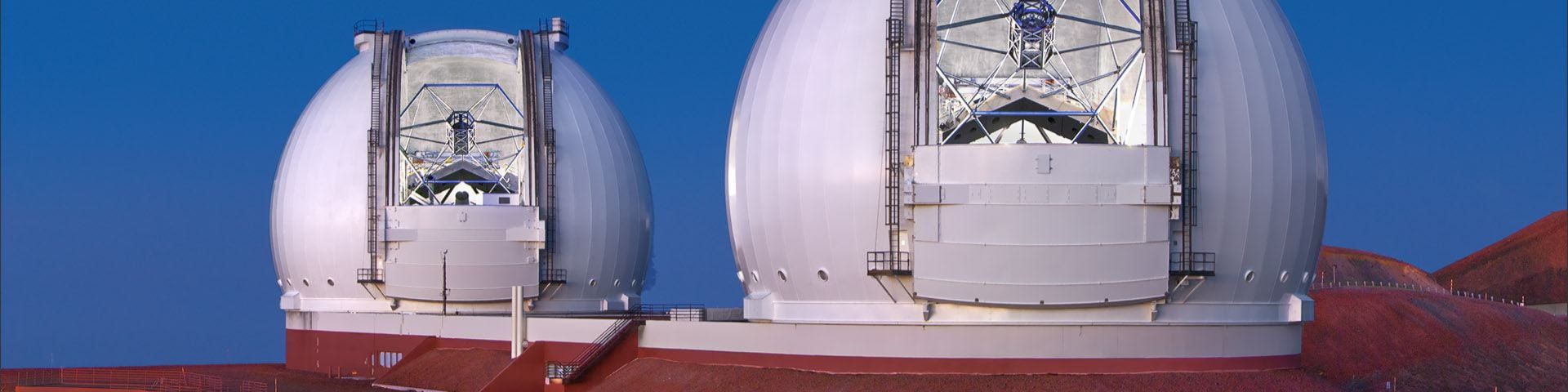
Deformable mirrors
Deformable Mirrors (DMs) are key components in Adaptive Optics (AO) systems employed in astronomy and laser communications to compensate for shape errors in optical elements and optical atmospheric disturbance, as well as for defense applications using high-powered lasers. Until now, deformable mirrors have suffered from inefficient and/or low-reliability actuators, with an inability to service system components. TNO has developed a Hybrid-Variable-Reluctance (HVR) DM technology which is reliable, serviceable, durable, scalable, modular, accurate, efficient and powerful.
Adaptive optics systems utilize optical signals, such as from laser guide stars, to measure atmospheric optical disturbance for ground-based telescopes. Deformable Mirrors (DMs) are used in a closed-loop with these signals to compensate for this disturbance for both astronomy and laser satellite communications, to correct the vision of the systems in real time and improve optical throughput. Within the context of space-based astronomical programs, AO systems are also key to achieving high-contrast imaging capabilities (e.g. exoplanet science) and compensate imperfections of the optics due to manufacturing flaws, misalignments, gravitational release and stress during launching and deploying phases.
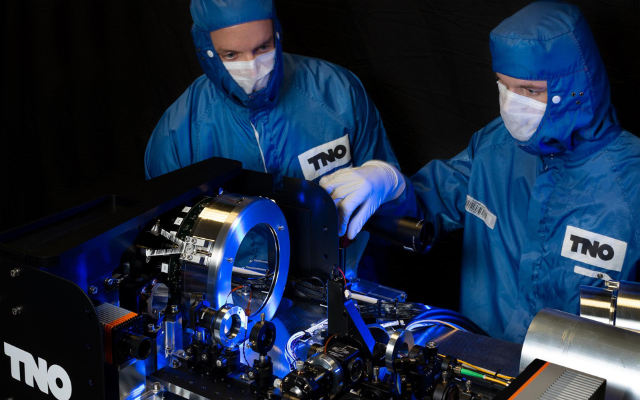
OFELIA Laser Communications Breadboard
Deformable Mirror DM2 used in OFELIA Laser Communications Breadboard – proved that beam-shaping (atmospheric pre-correction) can significantly improve signal quality through atmospheric turbulence.
Applications
Design studies have shown applicability for the following telescopes and applications:
- European Solar Telescope (EST)
- Keck Observatory
- Gemini North Telescope
- Thirty Meter Telescope
- Automated Planet Finder
- High Power Laser (HPL) for Defense
Conceptual Design of the KECK Adaptive Secondary Mirror, with ~3000 actuators, and a 1,4m diameter.
European Solar Telescope ASM, preliminary design (and breadboard): 2000 actuators; Ø0,8m,cooled optical surface.
Further (technical) details about deformable mirrors
TNO focusses on development, prototyping and performance testing. We have worked with the following development partners on the Hybrid-Variable-Reluctance (HVR) DMs:
- University of Hawaii (US): advisor and launching customer
- University of California (US): test and research partner, facesheet development
- VDL (NL): actuators & support structure manufacturing
- AAC Clyde Space (NL): electronics development
- Fraunhofer (DE): facesheet pre-forming
- NOVA (NL): facesheet finishing
To overcome drawbacks of existing DM technologies, TNO has developed systems with the following design features:
- Patented Hybrid-Variable-Reluctance (HVR) actuators, with high linearity, high force and high efficiency for power and volume, and no need for active cooling in most applications
- Highly reliable due to lack of wear/aging, redundant actuator windings and serviceable parts
- Modular and scalable for various actuator counts, configurations and pitches in the range of 5 - 50 mm
- Use of thicker mirror shells (2-4 mm) which are more durable and lower cost
- Adaptable for space environment, including cryogenic
The key ingredient to TNO’s Hybrid-Variable-Reluctance (HVR) DM technology is the actuation principle, which generally has the following qualities:
- Highly linear response (>99%), low hysteresis
- High reliability: No wear/aging, compliancy, redundant windings
- Low power dissipation (~ few mWatts per actuator)
- Compact, low power electronics (PWM)
- High force per volume; Scalable to large apertures, and actuator pitches (~40 times higher than a same size voice-coil)
HVR Actuator – Performance: Maximum force output ± 14N; Linear range of ±8N; 99% linearity; hysteresis <1%.
HVR Actuator – stroke and force range versus voice-coil and piezo actuators.
Latest HVR Actuator – DM16. Performance specs: Linear force range >30N PV; Displacement range >30µm PV- (up to 100µm PV, TBC); Internal resonance >2kHz; Efficiency; 60N/√W.
Get inspired
First Dutch hybrid quantum channel for secure communication successfully established
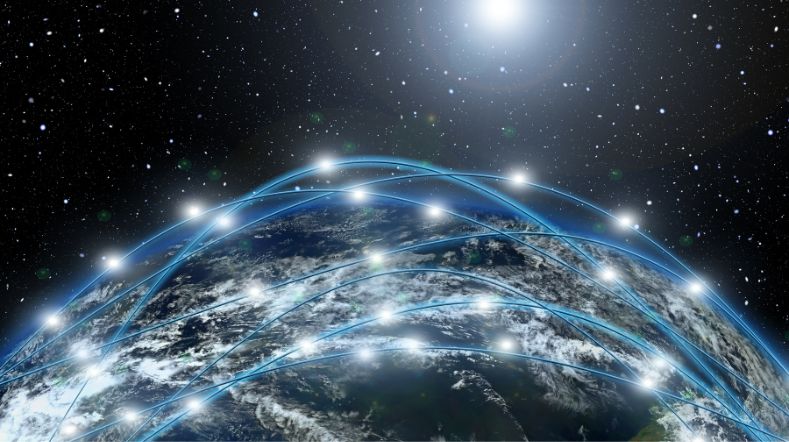
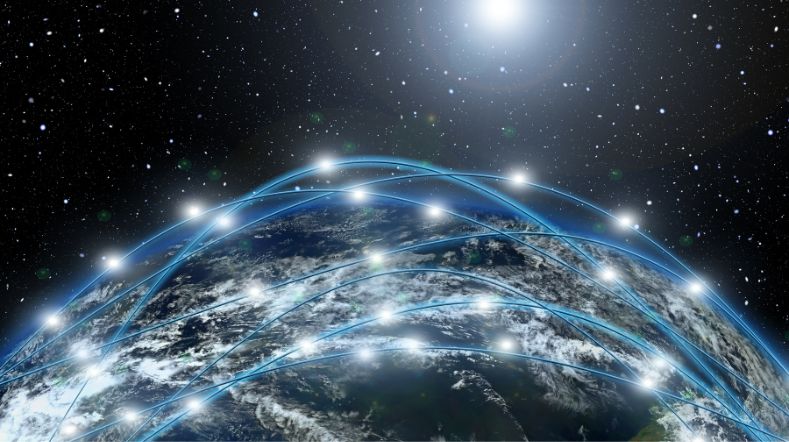
Deep sea telescope detects highest energy neutrino ever observed
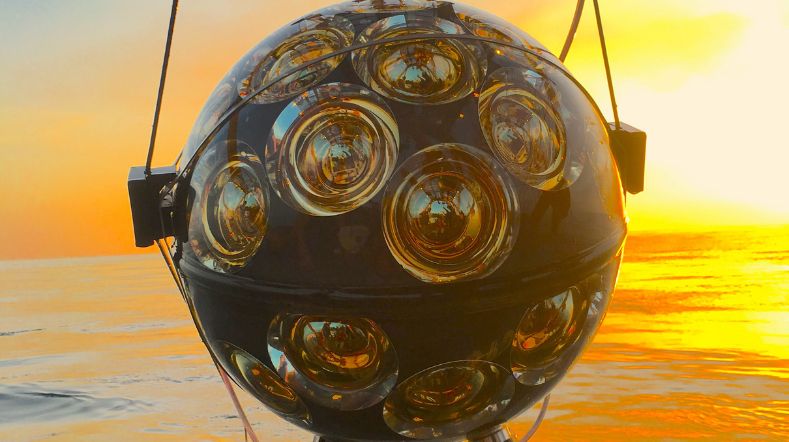
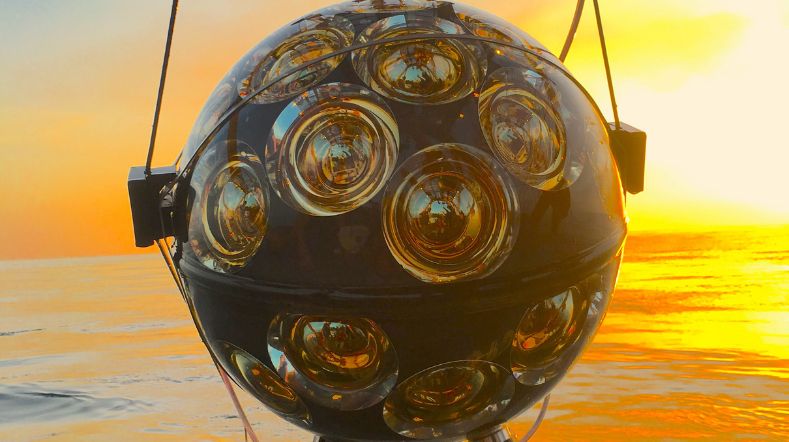
TU/e appoints TNO’s Niek Doelman as professor for control of optical waves
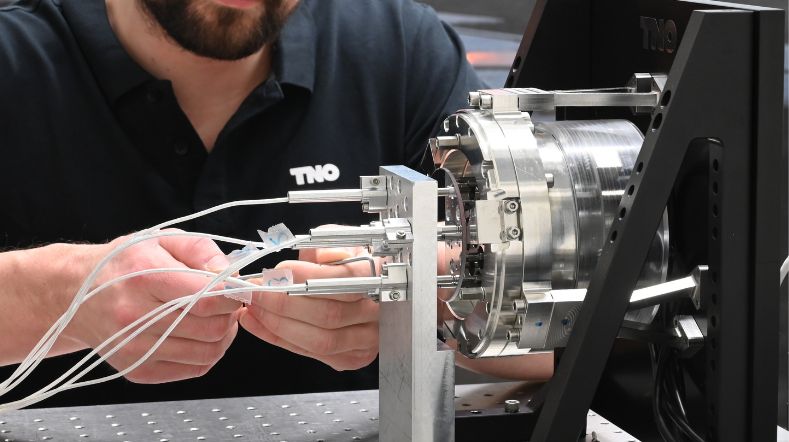
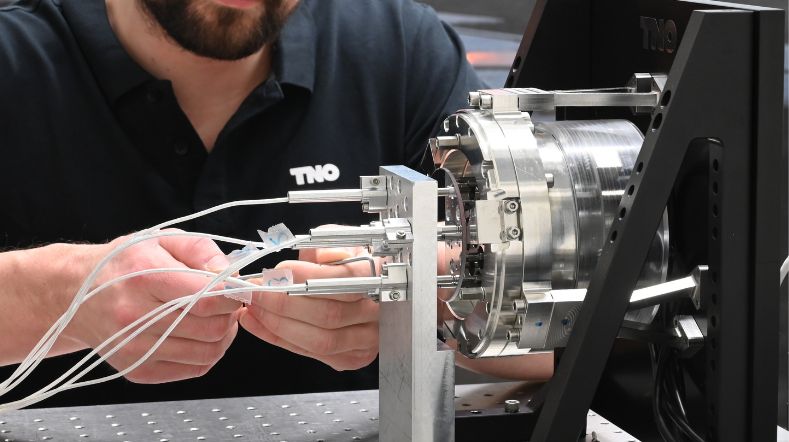
Instrument realisation and verification


60 Years of Space Innovation: Pioneering Beyond Earth
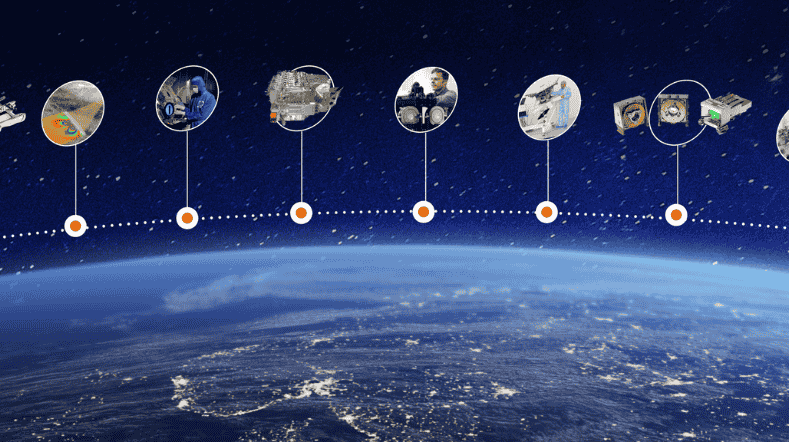
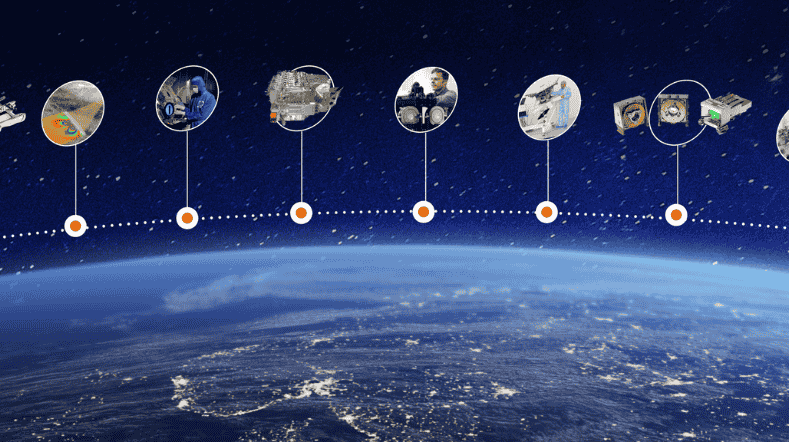