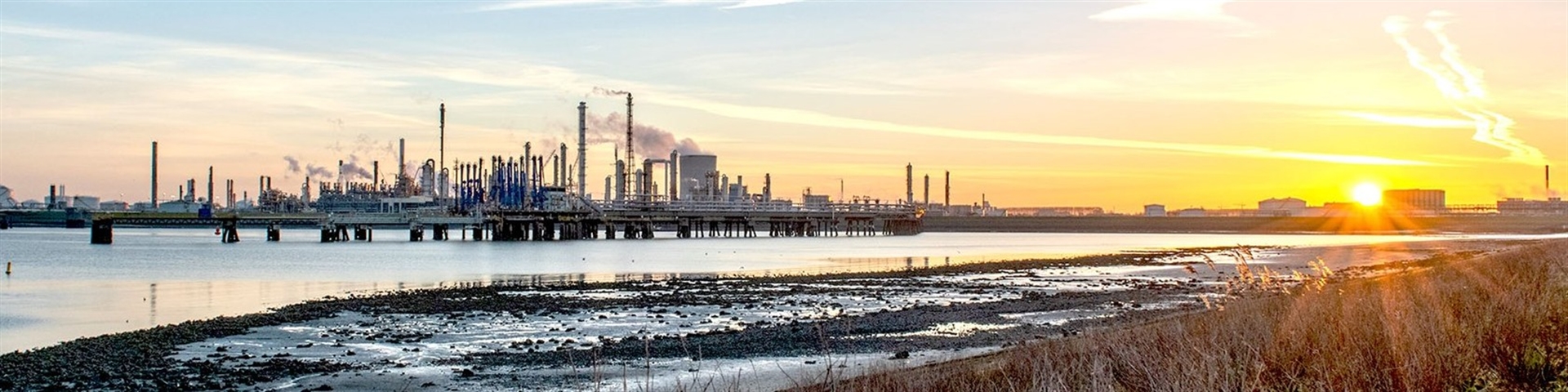
E-mission MOOI: TNO supports dow and Shell in electric cracking
Status project
June 2021 - present (4 years)
Shell and Dow have joined forces to study how to electrify the furnaces of their ethylene steam crackers. TNO is supporting the chemical companies in making the heating processes as efficiently as possible. At the same time, the partners are working together to look for a breakthrough technology for new concepts that will make electric crackers even more efficient over the longer term.
In early June, Shell and Dow signed a cooperation agreement for research into the electrification of their cracking processes and they received a grant of 3.5 million euros from the Dutch Mission-driven Research, Development and Innovation scheme [Missiegedreven Onderzoek, Ontwikkeling en Innovatie] (MOOI). The chemical companies chose TNO and ISPT as knowledge partners.
E-missi0n MOOI
In the e-missi0n MOOI project, Shell, Dow, TNO and ISPT will do research over the next four years on the possibility of electrifying existing gas-fired crackers. In parallel with the retrofit project, the partners will study the use of breakthrough technologies for the longer term. This is because new and more efficient electric cracking methods could pave the way to a completely carbon-neutral chemical industry by 2050.
Five megatonnes of CO2 savings
The cracking furnaces in the Netherlands together emit five megatonnes of CO2 per year. Replacing gas-fired furnaces with electric alternatives would immediately reduce those emissions. Dow and Shell account for 68 per cent of these emissions. Therefore, they could save 3.4 megatonnes of emissions per year, which represents 1.5 per cent of total annual CO2 emissions by the Netherlands.
In doing this, the companies would make great strides towards meeting the targets in the climate agreement for 2030 and 2050. However, the impact of the research could be even greater, as worldwide there are 300 similar crackers emitting some 200 megatonnes of CO2 per year. This is 1.3 per cent of total world CO2 emissions. TNO applies research in four pioneering routes for a CO2 neutral industry.
Ethylene crackers
To make the chemical building blocks (olefins) out of feedstocks, Shell and Dow crack the long molecules into shorter molecules using steam and high temperatures. After cracking, the gases are gradually cooled. At each step of the cooling process, products such as ethylene, propylene and butadiene liquefy one by one and can be separated. These products are important building blocks for plastics that support the energy transition. Feedstocks, today, are mostly from fossil raw material, but can also be extracted from biological or recycled sources.
The cracking furnaces are still heated by means of gas-fired burners, fed partly by the gases released by the cracking process. This burning emits CO2 into the atmosphere. Electrification of this process would immediately prevent these emissions, provided the electricity originates from renewables.
Two paths
The e-missi0n MOOI project focuses on two research paths: an electric retrofit in the short term and breakthrough technologies for the longer term. A retrofit will enable the companies to electrify the existing processing plant more rapidly than building a fully new facility. This accelerates the process of decarbonising, because the companies can continue to use the bulk of their existing plants. However, achieving carbon neutrality by 2050 requires breakthrough technologies that use green electricity even more efficiently.
Waste heat recovery
TNO is supporting Shell and Dow on both transition paths. In the first project, TNO is studying new heat recovery equipment and configurations to reuse high-temperature heat within the process. As a result, the efficiency of the plants will increase significantly and they will use less electricity.
The second path concentrates on entirely new methods of electric heating. Whereas the electrical elements currently heat the medium indirectly, there are also techniques that enable direct heating. This could considerably reduce the power consumption of the cracking process.
Reason for this collaboration
TNO already has extensive experience with high-temperature heat transfer techniques and plays a leading role in identifying innovative electrification technologies that can be applied in industry. In addition, TNO has sufficient research facilities to test the technology in practice, such as the Carnot Lab in Petten and the Field Lab Industrial Electrification in Rotterdam.
Facts and figures
Project name: e-missi0n
Start of project: June 2021
Project duration: 4 years
CO2 emission savings potential: 3.4 megatonnes
Goals:
1. Electrification of Shell and Dow cracking furnaces
2. New breakthrough technologies for electric cracking
Get inspired
Ten things to know about carbon capture and storage (CCS)
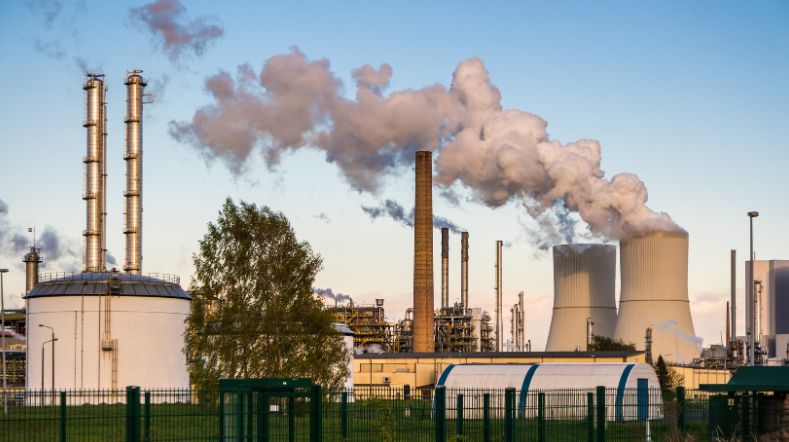
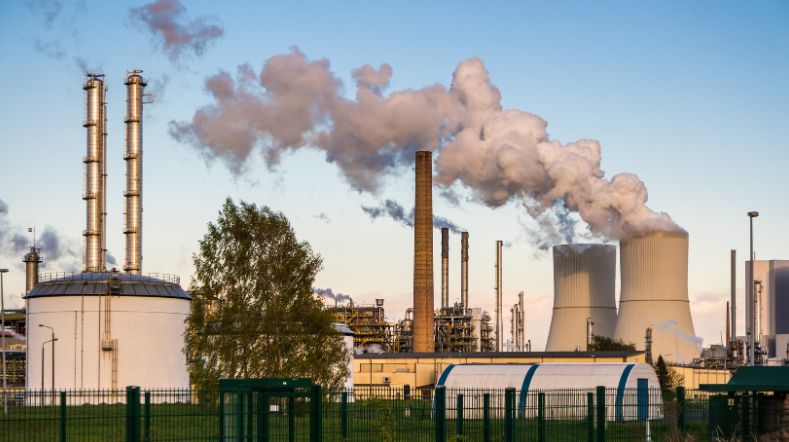
Unique test installation for CO2 capture and conversion to green chemicals
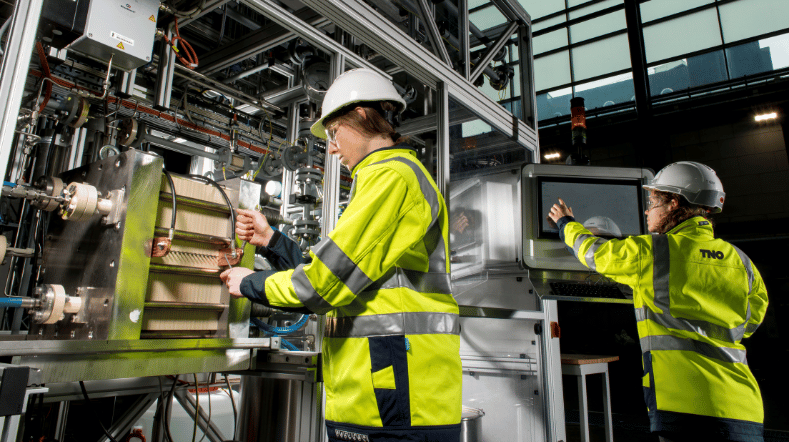
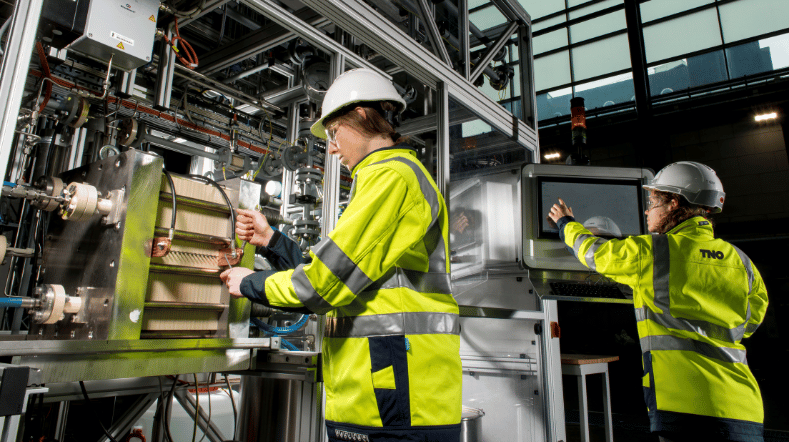
SEWGS: revolutionary CO2-reduction technology
SEWGS
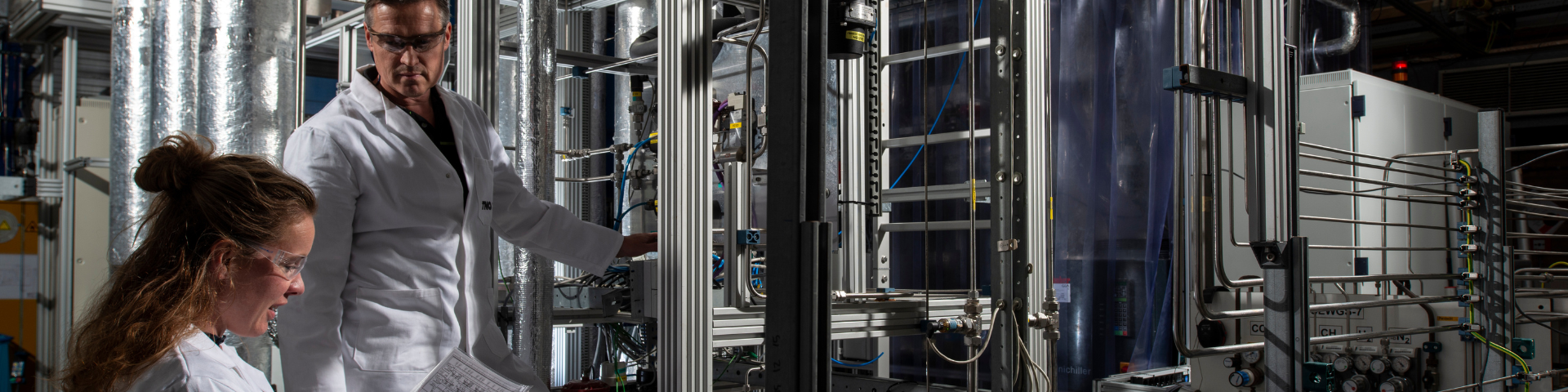
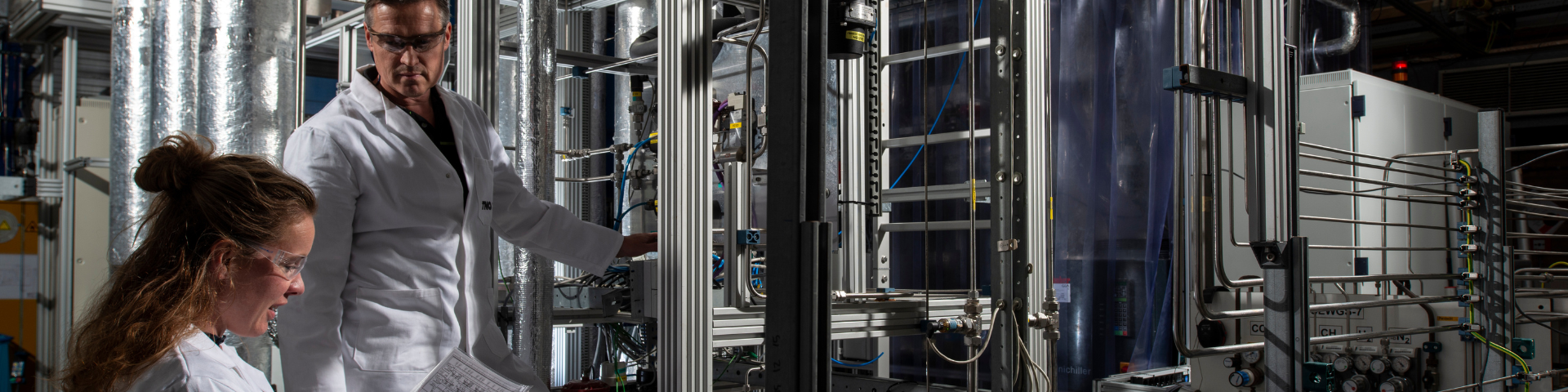
Capturing carbon emissions from industry
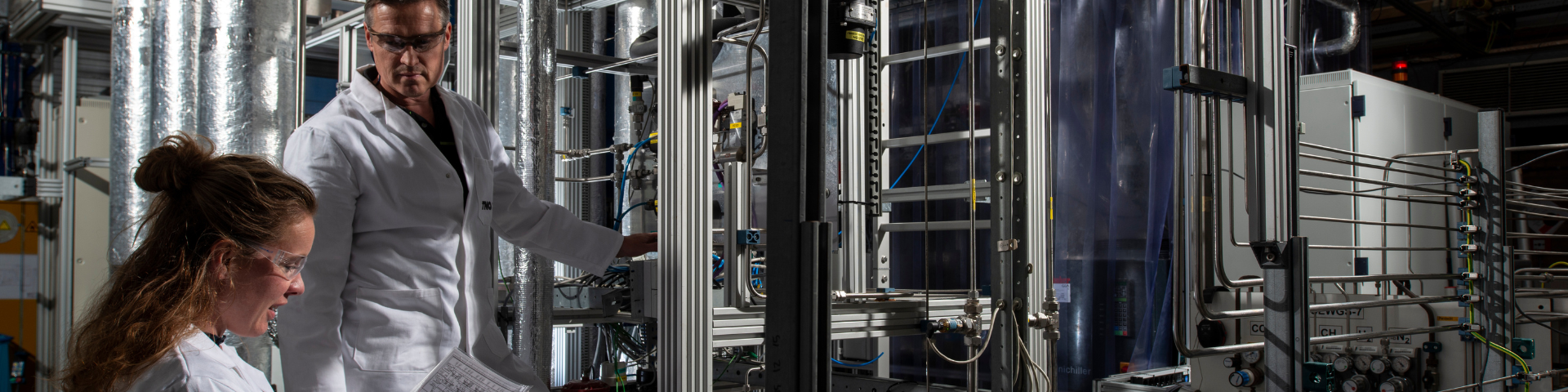
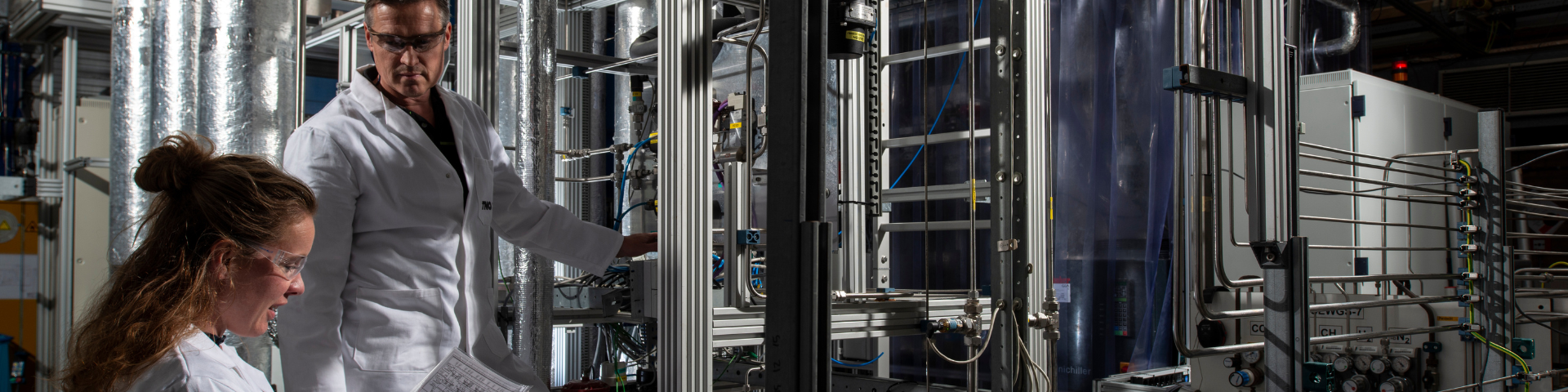