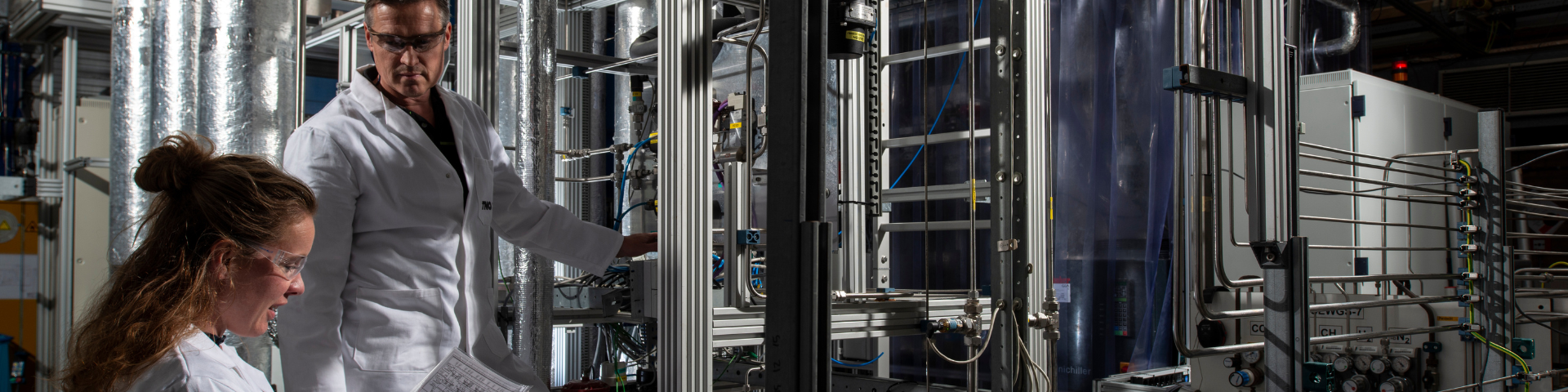
Capturing carbon emissions from industry
Sectors such as steel, cement, and waste processing contribute to current huge emissions of CO2. The great challenge is to reduce these emissions and this can be done through carbon capture. We’re tackling this challenge, collaborating with partners on carbon capture, storage, transport, and practical use.
Carbon capture is the only solution for now
For the time being, we still need fossil fuels and fossil raw materials in industry. Carbon capture is therefore currently the only solution. We’re working on methods for removing CO2 early in the process (pre-combustion) or capturing it from flue gases after burning gas, coal or waste (post-combustion). If possible, the CO2 will be reused or stored underground.
Carbon capture projects
We’re working at national and European level on research and demonstration projects for reducing CO2 in industry. Many companies have plans for carbon capture but they do not know how to implement them technologically and economically. We help them with our knowledge and facilities, carefully considering the risks, the economic feasibility, and legislation.
National projects
In national projects, such as Carbon Capture Transport and Storage (CATO) since 2004 and the Rotterdam Storage and Capture Demonstration project (ROAD), we’ve done a lot of research with partners and acquired knowledge about the opportunities and risks of capture and storage.
International collaboration
At European level, we’ve been working for a long time on research and demonstration projects that focus on specific sectors. Examples of these are STEPWISE, FReSMe and BOF2UREA for CO2 reduction in the steel industry; CEMCAP in the cement industry; and ALIGN-CCUS, which focuses on decarbonisation in six European industrial regions. We’re leading this last project, which combines carbon capture, transport, use, and storage. Our involvement is based on our expertise in these four areas, the connections between them, and the energy system as a whole.
Carbon capture in industry
Carbon capture is taking place in the industrial process and we’ve already worked on two successful projects:
1. AVR waste-to-energy plant
In the eastern Dutch town of Duiven, our expertise has contributed to a world first for waste processing company Afvalverwerking Rijnmond (AVR): large-scale carbon capture from their waste-to-energy plant. With an on-site mobile installation that we had designed and built, we conducted trials of carbon capture from various flue gases. These trials have put AVR in the forefront of the waste-to-energy sector. In this way, they’re cutting carbon emissions by 60,000 tonnes a year, making them an inspirational example worldwide. Horticulturalists use the CO2 to boost the yields of their glasshouse crops. Currently, their CO2 often still comes from their gas-fired heating systems
Scaling up from a few hundred kilos of captured CO2 to thousands of tonnes is a huge achievement. And capacity can be expanded even further. Our goal is to capture as much carbon as possible. If horticulturalists obtain the CO2 they need for their glasshouses from other sources, for example from waste processing, they can switch more easily from natural gas to renewable energy. This will reduce total emissions.
2. Steel plant in Sweden
In Sweden, carbon capture from the blast furnaces of a steel plant has been successfully demonstrated. The installation, called SWEGS, captures 14 tonnes of carbon per day at a lower cost than with the current carbon capture technology. With this achievement, we demonstrated that the SEWGS technology for carbon capture is ready for the next step. We’re in talks with parties about commercialising the technology.
Installation to test carbon capture
Our mobile carbon capture pilot plant is the only one of its kind in the world. It’s a test set-up for trialling carbon capture from various flue gases at your location. This enables us to help companies reduce their emissions and find out what is technically feasible and economically responsible. The mobile carbon capture pilot plant was also used at AVR in the testing phase.
Design of the installation
We subsequently outlined for AVR the basic concept for the design of the complete installation. There’s now interest in the test installation in the Netherlands and abroad. Its advantage is that you can capture carbon on a small scale and test and analyse the process. The resulting knowledge will enable you to design a future carbon capture installation.
Transporting CO2
Captured CO2 also has to be transported and the Port of Rotterdam is making plans for this purpose. The Port of Rotterdam Authority, Gasunie, and EBN are collaborating on the Porthos project. Porthos will provide a new system of pipelines for companies to transport captured CO2 from the port to empty gas fields under the North Sea. There’s a similar plan, called Athos, for the North Sea Canal area. We’re collaborating with these consortia and investigating the optimum technological and economic feasibility.
Carbon storage
It’s possible to store CO2 safely in empty gas fields under the North Sea. This gives oil and gas installations there a new lease of life. In the ROAD project, in which TNO was actively involved, a system was designed to store CO2 safely in an empty gas field.
Reusing CO2
With special technologies, you can also use CO2 to make raw materials and fuels. It can be a source of carbon for producing new, synthetic hydrocarbons. We’re developing technology to produce this efficiently. Aircraft, lorries, and ships may be able to use such products in the future. Houses and other products could also be made using synthetic building materials.
Looking to the future
We’re continuing to work with industrial and knowledge partners on further developing techniques for carbon capture, transport, use, and storage. We’re working on and supporting large-scale demonstration projects and doing everything possible to reduce CO2 emissions.
Get inspired
Ten things to know about carbon capture and storage (CCS)
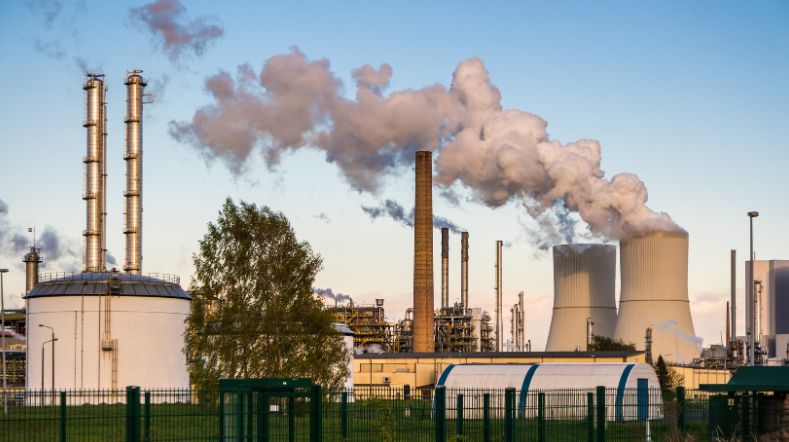
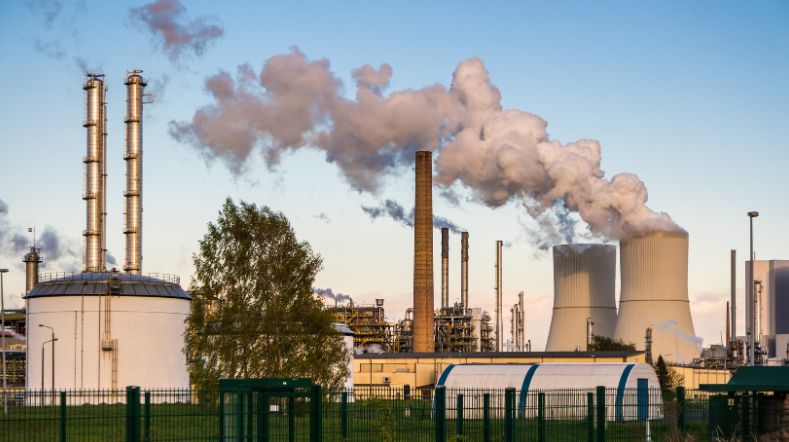
Unique test installation for CO2 capture and conversion to green chemicals
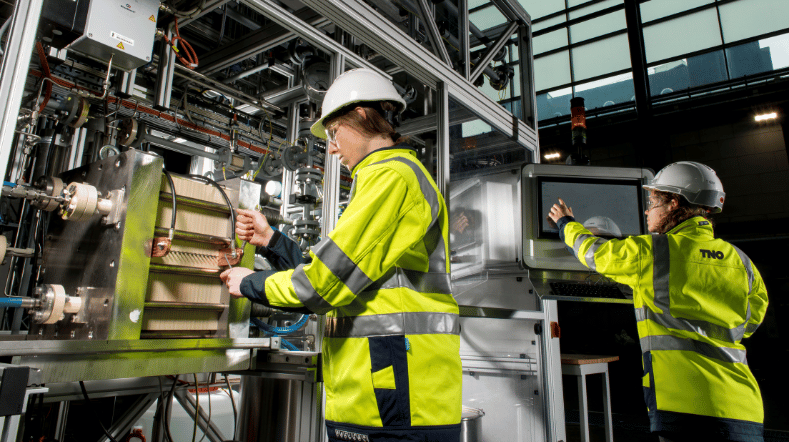
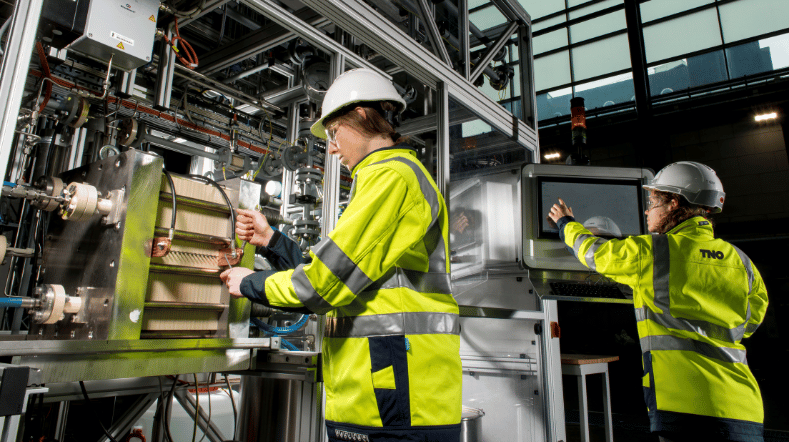
SEWGS: revolutionary CO2-reduction technology
SEWGS
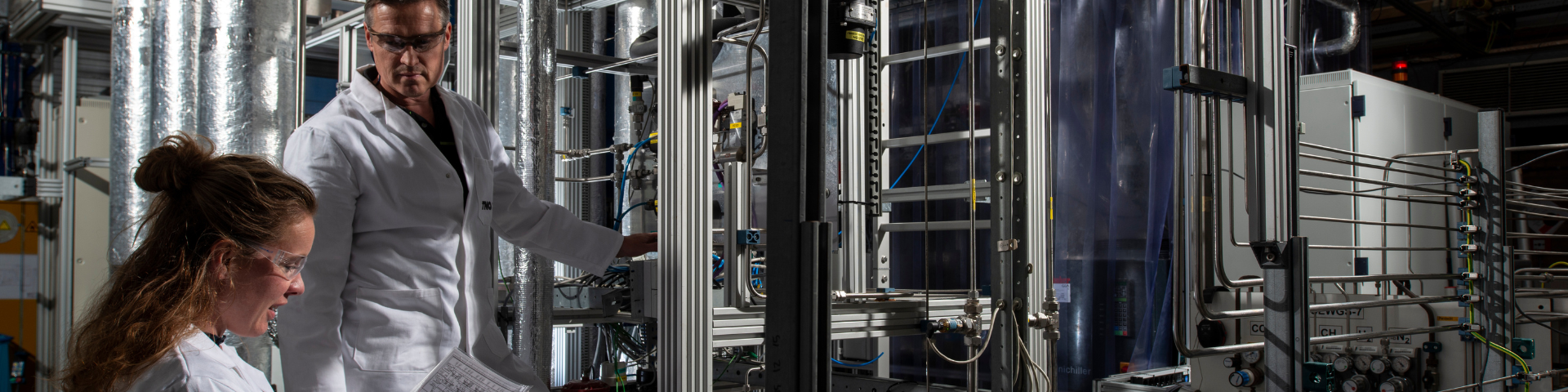
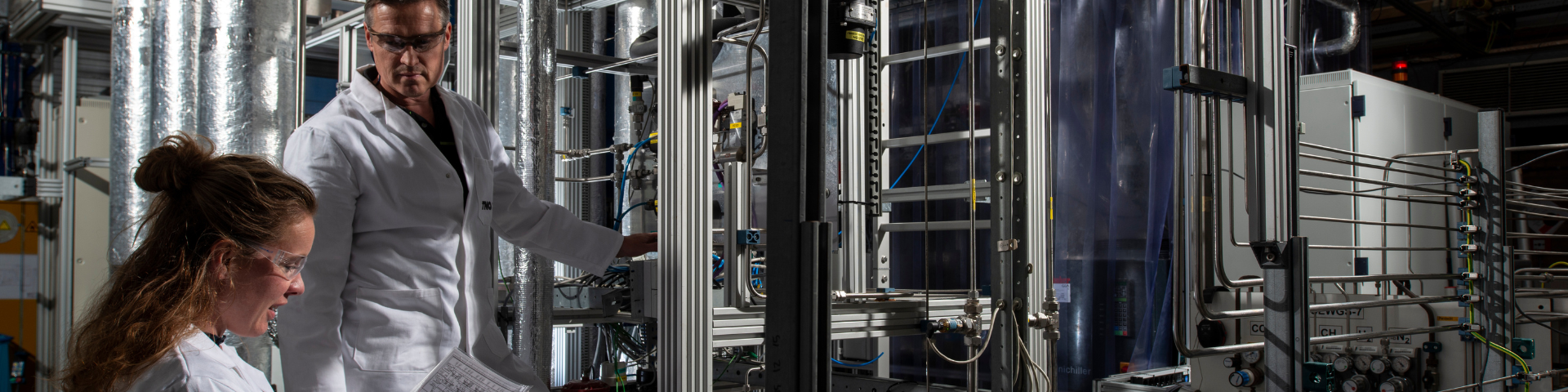