Data sharing to achieve smart production
Anyone who wants to produce competitively must ensure that their production process is both flexible and efficient. This demands smart combinations of data from machines and IT systems. But collecting this data is not the only essential consideration. It must also be possible to share the data with partners, securely and confidentially. TNO uses Data Sharing for this very purpose.
In a smart factory, the production process is controlled and adjusted by means of data, to ensure that machines are used efficiently. However, factories do not operate in isolation. They rely on data exchanges with customers and suppliers, with regard to customisation and just-in-time deliveries. One example is digital procurement, another is the use of 3D drawings as a basis for the production process.
However, big data sharing is embedded in some entrepreneurs’ organisations, but not all. Some still find the collection and use of data very challenging. In many cases, systems from different suppliers do not interact smoothly with one another. Nor is data sharing a casual matter, as guarantees must be put in place before data can be accessed and used.
Smart data sharing
One major challenge is to make solutions scalable. Many applications are limited to a single company or to just a few machines. “Smart data sharing is a critical precondition for many Smart Industry applications”, concludes TNO’s Matthijs Punter. “Thus we have to ensure that these solutions become scalable. That is the only way to achieve a ‘smart supply network’ – a network of flexible and interconnected factories.”
Improving production processes
In the context of Data Sharing, TNO is working on solutions that will facilitate data sharing within individual factories and between separate factories. One such application enhances cooperation between customers and suppliers, another is used to achieve smarter production. This includes improved production planning, optimising production planning, or OEE (Overall Equipment Effectiveness) improvements. The focus here would be the availability of machines, output, and the quality delivered. Other factors include the prevention of errors, and cutting maintenance costs. TNO never shies away from the challenges involved, even when this involves dealing with machines or software from a range of different suppliers.
It is vital for manufacturing companies to keep a hand on the wheel. In this way, each party can decide for themselves who receives which data. Initiatives such as Europe’s International Data Spaces (IDS) and new cloud technologies, such as GAIA-X , play an important part in this.
Blueprint for big data sharing
Mr Punter goes on to say that “We have seen that many applications for collecting, analysing, and using data are a real hurdle for companies”. “You have to roll your sleeves up and cooperate with technology suppliers to get everything up and running. However, many smaller SME manufacturing companies lack the necessary resources and capabilities.”
That requires further standardisation. To this end, TNO is working on a blueprint for data sharing in the manufacturing sector. This will offer manufacturing companies a list of the standards and technologies for their technology suppliers. That will also be helpful for the suppliers. The standardisation of interfaces will enable them to expand their market and to deliver new, innovative products more rapidly.
Joining field labs
TNO is actively involved in the field labs that are developing various parts of this blueprint. One specific example is the Smart Connected Supplier Network , which is developing standards for supply-chain cooperation (digital procurement and sales). Other examples are the BIC (Brainport Industries Campus) Digital Factory and SMITZH (the Smart Industry Hub for the Dutch province of Zuid-Holland) Data Sharing , in which standards are being developed for connecting smart machines and production lines. In this context, TNO’s work is in line with international developments, such as the German ‘Industry 4.0’ platform. An open test & development environment is available for testing these new standards and approaches.
Technology update: BIC Digital Factory
In the context of the BIC Digital Factory [MP1] project, TNO and its partners are developing a blueprint for a smart and connected factory. This will address questions such as which standards should you use, how can different systems be linked, and what is the role of the cloud?
GAIA-X for the manufacturing sector
A hot topic in Europe is ‘GAIA-X’, a new cloud environment designed to enable entrepreneurs to keep control of their data. Even though GAIA-X is still in its infancy, TNO is already investigating its potential role in the manufacturing sector. That is explained in this webinar by the Data Value Center - Smart Industry.
Sharing data in the chain
What is the relationship between smarter production logistics with automated guided vehicles (AGVs), data-driven production planning, and data sharing in the chain? That is the subject of this technology update from the Brainport Industries Campus.
Get inspired
TNO spin-off Scenexus secures 1.6 million euro investment


Scale up: manufacturing throughput and quality
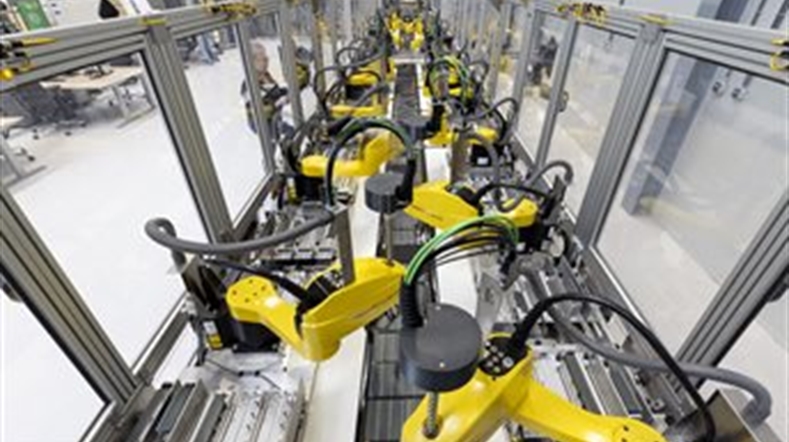
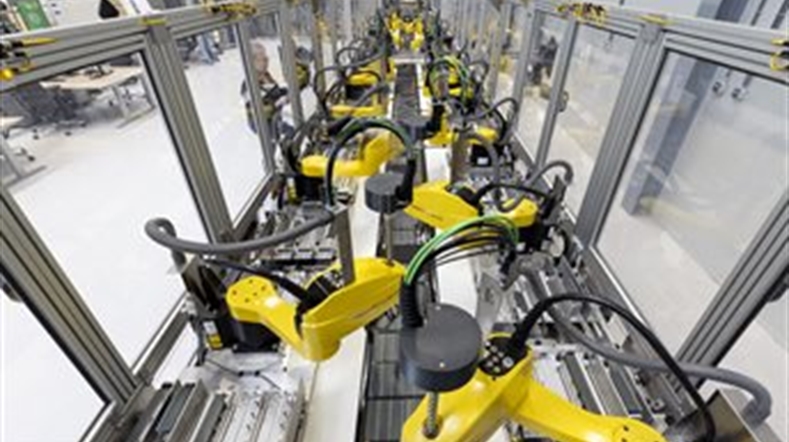
Non-destructive inspection
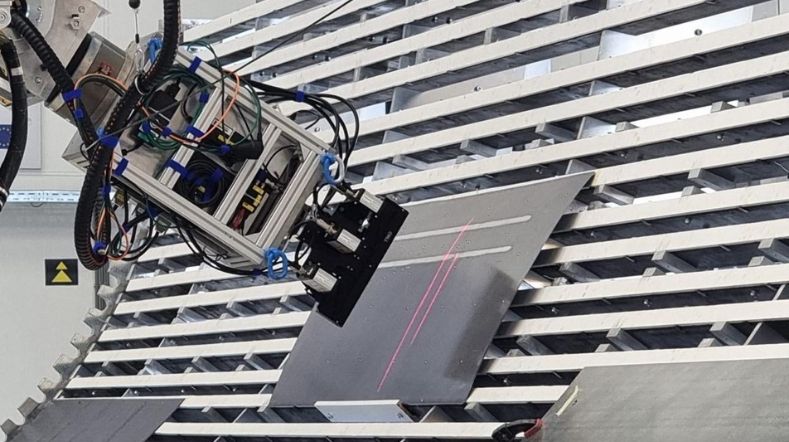
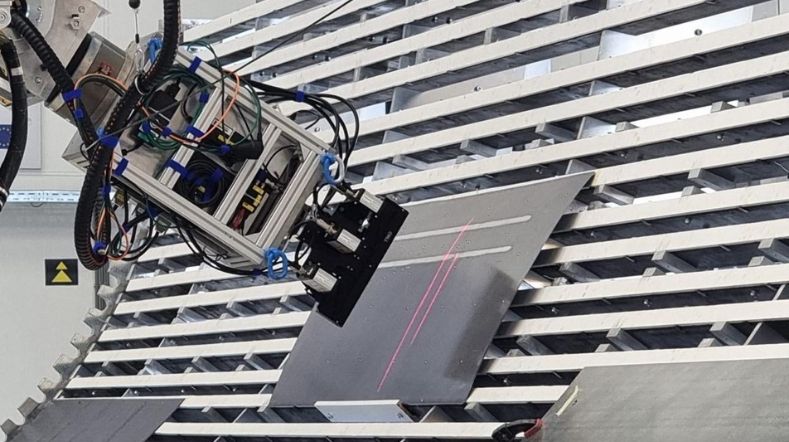
Strategic autonomy: digitalisation and value chain integration
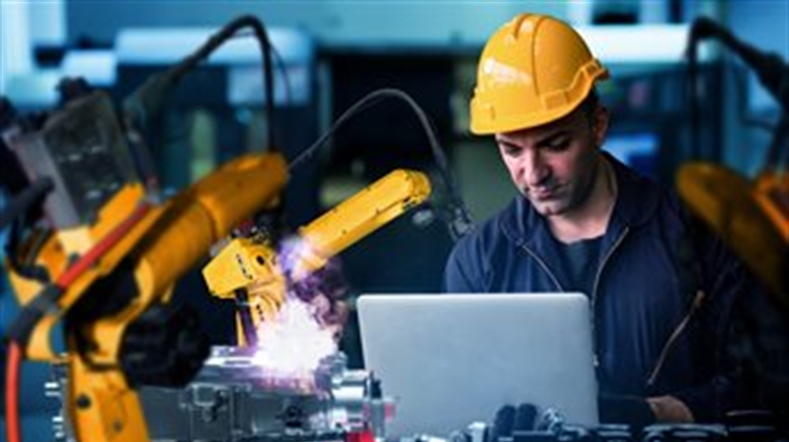
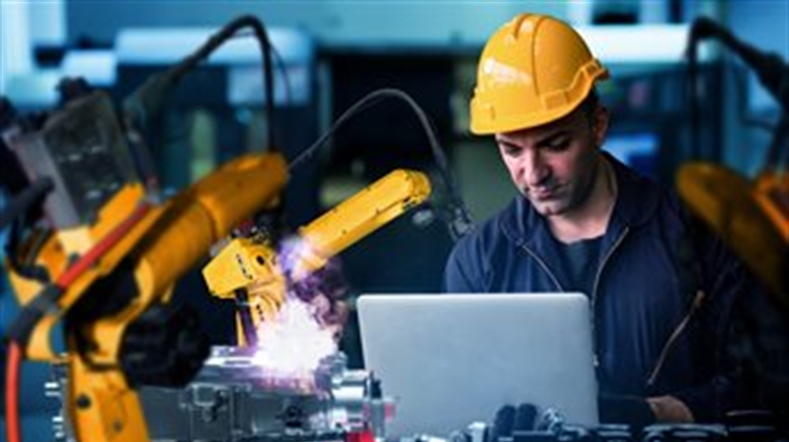
Productivity: manufacturing variability
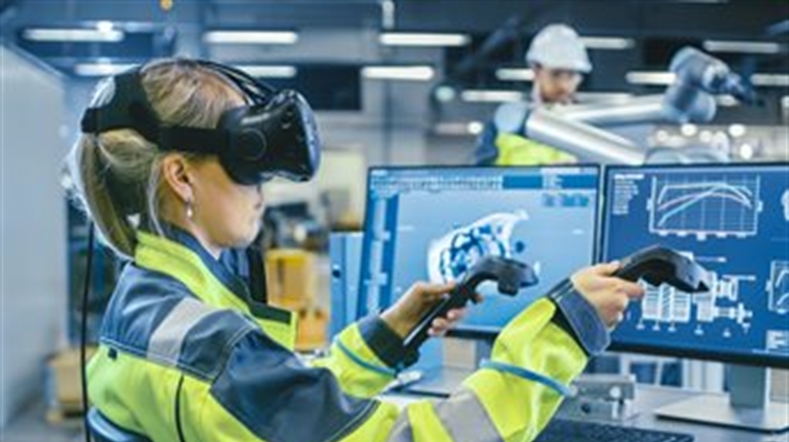
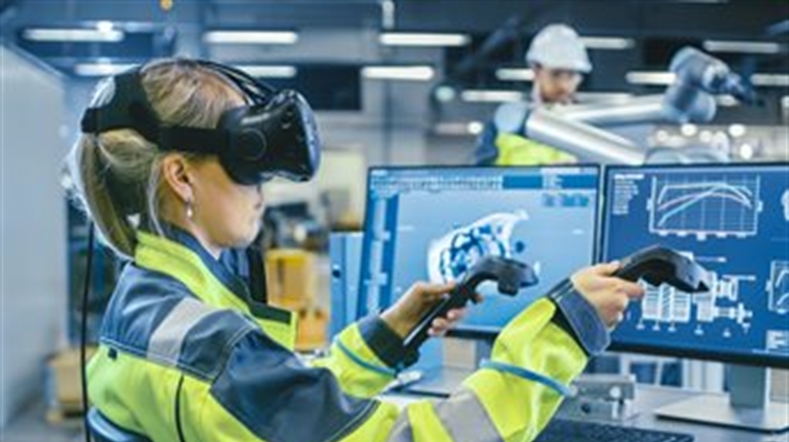