TNO develops method to produce biocarbon
TNO has developed a method to make clean carbon. The "EnerChar" method enables large-scale production of biocarbon with different properties. At the same time, heat is produced during this process and CO2 can be captured. The scalability and ability to produce biocarbon "on demand" makes the technology multi-purpose. The clean carbon is made by gasification of biomass (wood residues but also residual streams from the food industry). Many of today's products contain carbon from fossil sources. The use of biocarbon can make a major contribution to reducing fossil carbon and thus reducing CO2 emissions.
New carbon sources needed
With the technology developed by TNO, waste residues from the gardening, forestry and food industries are gasified on a grid similar to those used in waste incineration. TNO researcher Rian Visser: "With this method, we are creating a clean and sustainable alternative to fossil carbon. In the production of this biocarbon, heat is also generated at the same time and the CO2 from the chimney can be captured and stored. We need carbon anyway, for example for steel, horticulture and batteries. By using clean biocarbon for this purpose, we can reduce the proportion of carbon from fossil sources."
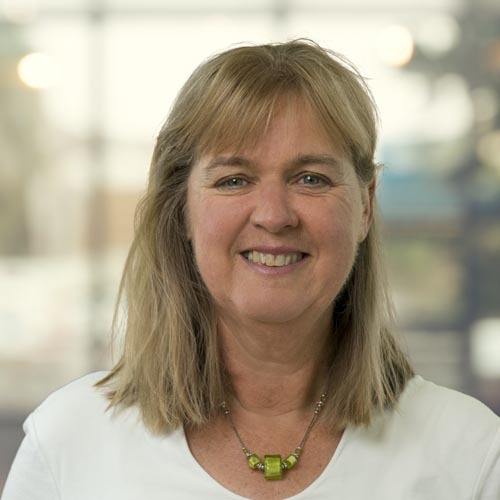
“Potentially, its use can contribute significantly to climate goals. We would therefore like to scale up our Enerchar method so that biocarbon can soon be produced on a much larger scale.”
Possible applications of biocarbon
Infinite applications are conceivable for the biocarbon because with the Enerchar method "biocarbon is tailor-made," that is, specific to the desired application. Besides direct application as a negative emission option in soil, there are also possible applications for industry. Some examples:
1. Greening steel production
Making steel from iron ore requires large amounts of carbon because steel is an alloy of iron and carbon. To green this process, biocarbon is ideally suited. Because large quantities are needed, scalability of the technology is important. The Enerchar method can be easily scaled up. On a smaller scale, the technology has already proven itself. The next step is to demonstrate in a demonstration project that it can also be done full-scale and cost-effectively.
2. Biocarbon for batteries
The graphite used in batteries is also a form of carbon. The anode of batteries is usually made from natural graphite from mines, but that is of limited availability. It is also produced with a lot of energy and chemicals from fossil oil residues. TNO has therefore recently started making bio-graphite, biocarbon for batteries.
3. Alternative to peat in horticulture
Biocarbon may even play a role in the potting soil used in large quantities by Dutch horticulture. For this purpose, peat is now being excavated on a large scale. Because peat can store a lot of CO2, even more than the tropical rain forest, an alternative to using peat will make a substantial contribution to CO2 management.
Trials conducted in recent years by TNO with Wageningen UR and the Flemish research institute ILVO have shown that the biocarbon produced in the pilot can replace between thirty and fifty percent of the peat in potting soil. After use, it can be returned to the soil with compost and is suitable for storing CO2 from the air in this form as fixed carbon in the soil. This allows for negative emissions.
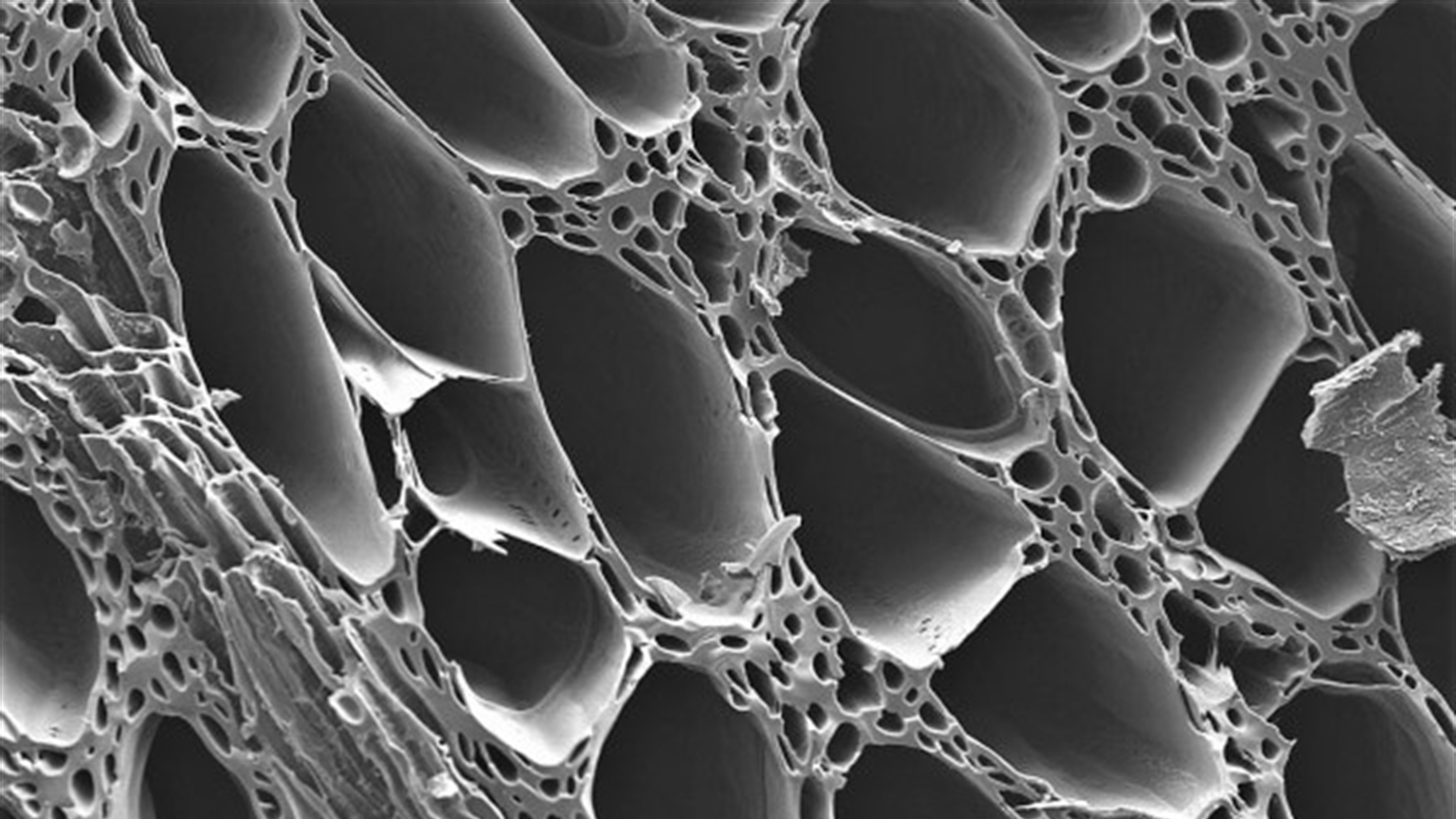
Explanation of biocarbon production
When wood or other biomass is heated, it will degas. This means that first water, in the form of water vapor, leaves the material but then also all kinds of conversion products in the form of hydrocarbons. In fact, wood residue contains a lot of carbon and hydrogen. Hydrocarbons are flammable (think of oil, natural gas and coal which also consist of hydrocarbons as well). If there is not too much water in it, a combustible gas is created from the heated wood residue and biomass that can serve as a substitute for fossil sources such as oil or natural gas.
Electrical heating without oxygen leads to a process called pyrolysis. But if a small amount of oxygen is used then it is called gasification. The advantage of gasification is that a small portion of its own gas is used to heat the process itself. Therefore, no external energy source is needed and, in a sufficiently large plant, even a large amount of energy remains.
Depending on the duration of the process and the temperature used, the solid that remains, after degassing, contains more and more carbon and fewer and fewer other elements such as hydrogen and oxygen. As the wood residues are heated at higher temperatures, the proportion of carbon in the remaining solid increases to as much as 85%. The energy content of the biocarbon also increases substantially as the amount of carbon in the solid increases. This solid retains the old structure of the biomass which provides a large surface area and porous material.
It is lightweight (fine for horticulture), it can store water in its pores (good for soil) and it can also bind materials to itself and do work like activated carbon in all kinds of purification processes. With the Enerchar method, "custom biocarbon" can be made. For example, in horticulture, hydrocarbons may no longer remain in the carbon product, but it is less critical for use in steel production because residual hydrocarbons are converted later in the process.
The Enerchar process is unique because it has a wide temperature range (350-850 degrees) and can work with different gases such as air and steam (as well as flue gas recirculation and CO2). By varying this, it is possible to make biocarbon of different quality for various applications.
Get inspired
The North Sea as Europe's energy heart requires smart choices
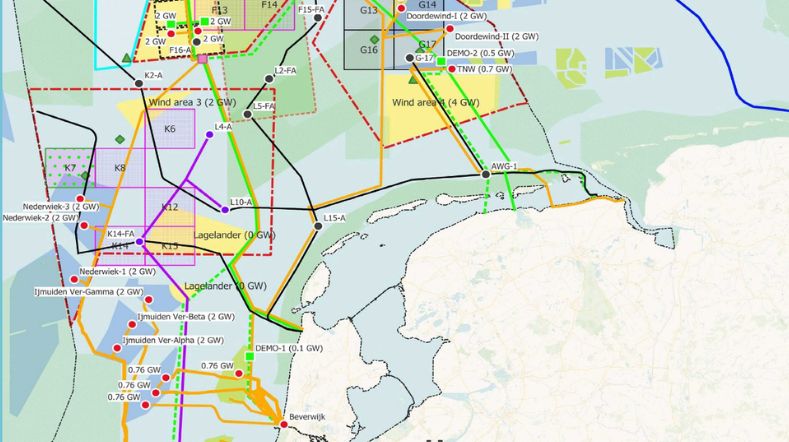
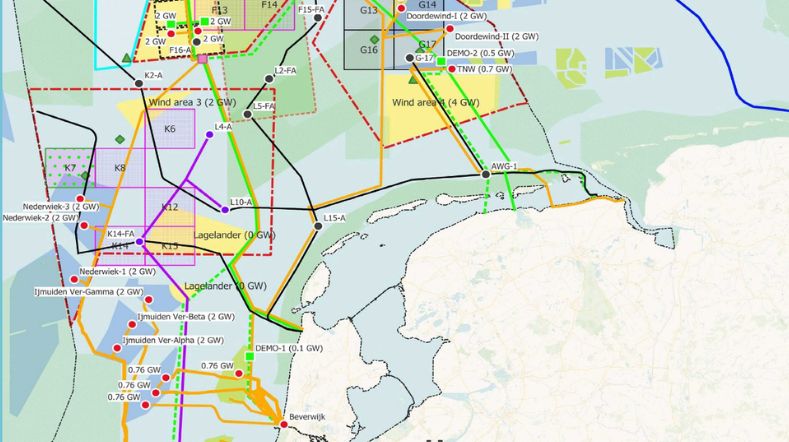
Tomorrow’s hydrogen production and infrastructure: building towards a secure and robust energy system
World Hydrogen Summit 2025
Scaling-up electrochemical technologies for renewable ethylene production
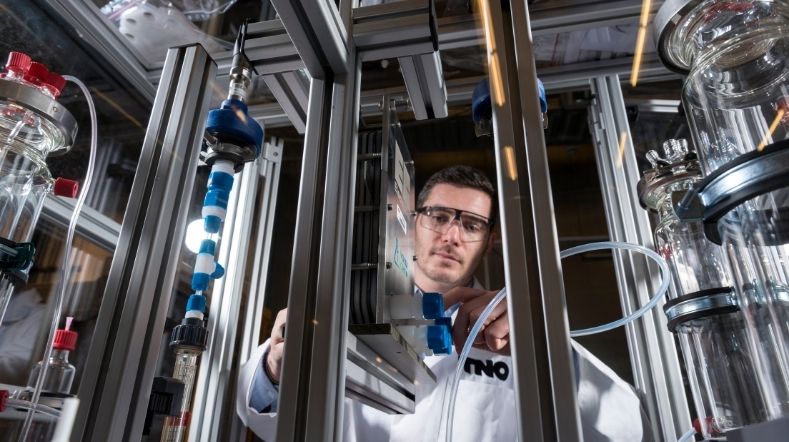
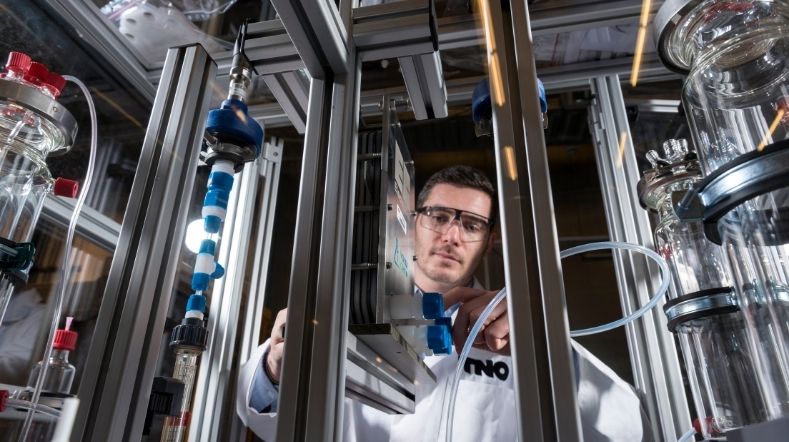
CO2 infrastructure and transport


How TNO Green Print helps industry become more sustainable
TNO provides knowledge, innovation and concrete solutions for companies, government and suppliers. In summary, we call it TNO Green Prints: a blueprint for radical greening of value chains in the industrial sector.