10 questions and answers about CO2 capture in industry with SEWGS technology
To keep the energy transition feasible and affordable in the short term, it is essential to use blue hydrogen. The Dutch breakthrough innovation SEWGS enables steel producers and refineries to convert their process gases cheaply and easily into blue hydrogen. The platform technology is already available and it has proved itself in practice. Jurriaan Boon and Soledad van Eijk answer 10 questions about SEWGS.
1. What is SEWGS?
SEWGS stands for Sorption Enhanced Water-Gas Shift. This revolutionary combination technology converts synthesis gas into hydrogen and carbon dioxide. The SEWGS process also splits the carbon dioxide from the hydrogen gas in the same reactor. The combination ensures a more energy-efficient conversion and the virtually complete removal of CO2.
2. What possibilities does it offer?
SEWGS has prospects for the future, it can be developed further and be applied in many more areas.The SEWGS process combines a water-gas shift reaction with CO2 adsorption. In this reaction, steam ensures the conversion of carbon monoxide into carbon dioxide and blue hydrogen. The adsorption step prevents hydrogen from reacting back to carbon dioxide. An additional advantage is that the process takes place at high temperatures and under high pressure.
3. What distinguishes SEWGS from other capture techniques?
Perhaps the greatest prerequisite for the success of SEWGS was the development of a solid adsorbent material. The first SEWGS patent dates back to 1915. At that time, however, scientists failed to develop the right material with the required active surface area. Eventually, hydrotalcite enriched with potassium carbonate proved to have the best adsorbent properties. But it was not until the advent of 3D printing technology that this material could be given the right shape.
Thanks to the unique properties of the material, TNO was able to make the columns eight times more compact. An additional advantage is that the material does not degrade, which in turn prevents emissions. The SEWGS adsorption material is also catalytically active for the water-gas shift reaction. As a result, only one material is needed for both conversion and capture.
4. What are the advantages of SEWGS?
The main difference compared with other existing technologies is that SEWGS combines blue hydrogen production with CO2 capture. Combining these processes in a single reactor results in a much more efficient process, with less energy wasted. For example, during a trial at steel producer SSAB, TNO proved that capturing one tonne of CO2 from steel gas required 62 per cent less energy than conventional CO2 capture technology.
The treated steel gas therefore had a very low cost price of about 33 euros per tonne of CO2 captured, which is less than the current emission trading price (June 2021). And that while SEWGS is already 28 per cent cheaper than the benchmark. Thanks to the low cost price, applications with a positive business case have a Return on Investment of 5 to 7 years.
5. Who can use SEWGS?
During their processes, the petrochemical and steel industries produce waste gases that are similar in composition to synthesis gas. The companies often use these waste gases as a source of energy for other processes or for electricity generation. With the SEWGS technology, these companies can continue to use the gas, without the negative effects on the environment. However, TNO also sees applications for SEWGS in other gas streams.
6. Wat is synthesis gas?
Synthesis gas is a mixture of carbon monoxide and hydrogen. Many waste gases also contain a lot of carbon dioxide. Nearly all organic substances, both fossil fuels and agricultural waste streams, for example, can be converted into synthesis gas through gasification. In the case of waste streams from agriculture, the gas is a sustainable alternative to natural gas. If the CO2 is also captured and stored, this can actually result in negative CO2 emissions. SEWGS makes this possible.
7. Has the technology already proved itself?
Yes, TNO has already successfully demonstrated the operation of the SEWGS process on an industrial scale at Swedish steel company SSAB. In a pilot environment of the project Stepwise in Sweden, there is a 10-metre-high SEWGS installation with a diameter of 40 centimetres, containing 3000 kg of adsorbent material. The cyclic capacity of this installation is 14 tonnes of CO2 per day.
8. What is blue hydrogen?
In order to distinguish between different methods of producing hydrogen, colours have been assigned to the same molecule: green, grey, blue and turquoise. Green hydrogen is produced by splitting water molecules into hydrogen through electrolysis. For grey hydrogen, natural gas is split into hydrogen and carbon dioxide. Grey hydrogen with CO2 capture and storage is called blue hydrogen.
9. What happens to the captured CO2?
In Norway, CO2 is already captured and stored in an underground aquifer. In the Netherlands, there are plans to store CO2 in depleted gas fields in the North Sea. The greenhouse horticulture sector is already using CO2 to promote the growth of flowers and plants. CO2 is also a chemical building block for various chemicals and plastics. The residual CO2 from SEWGS is of such quality that TNO could make 20,000 litres of methanol from steel gas. But the technology is also suitable for making a mixture of hydrogen and nitrogen for ammonia synthesis.
10. Can I order a SEWGS installation?
SEWGS has already proved itself in practice. In two years’ time, there will be a SEWGS installation with multiple columns in Sweden that will capture 150.000 tonnes of CO2 per day. By using multiple columns, it is possible to continuously generate more than 95 per cent pure CO2 and hydrogen. TNO will subsequently license the technology. The configuration and cost price of an installation depend on the specific environment in which the installation will have to operate. The same applies to the cost and energy benefits, which depend on the exact situation.
More information about CO2 capture industry? Reach out to Soledad van Eijk directly.
Get inspired
Ten things to know about carbon capture and storage (CCS)
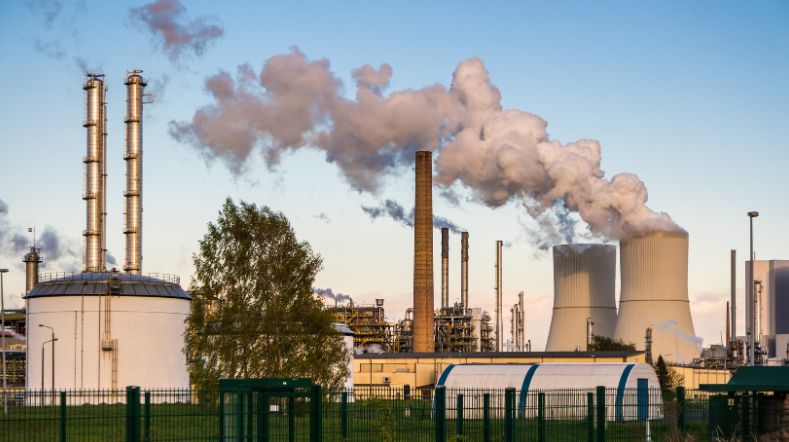
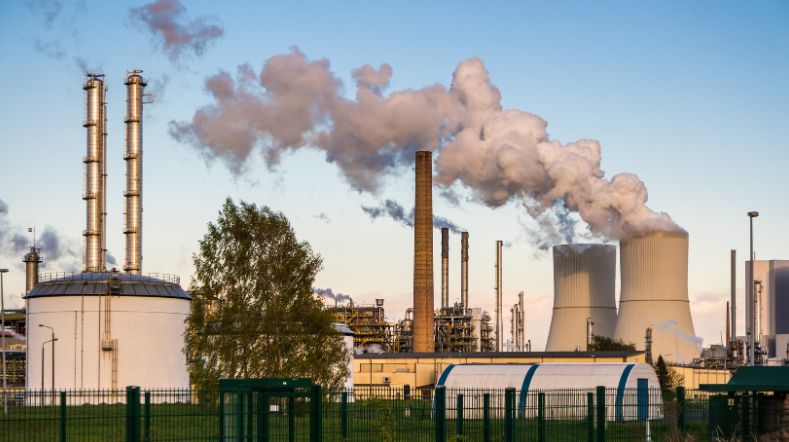
Unique test installation for CO2 capture and conversion to green chemicals
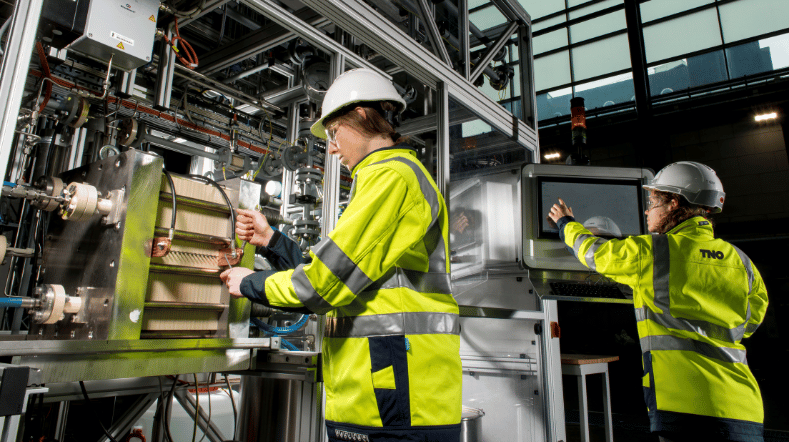
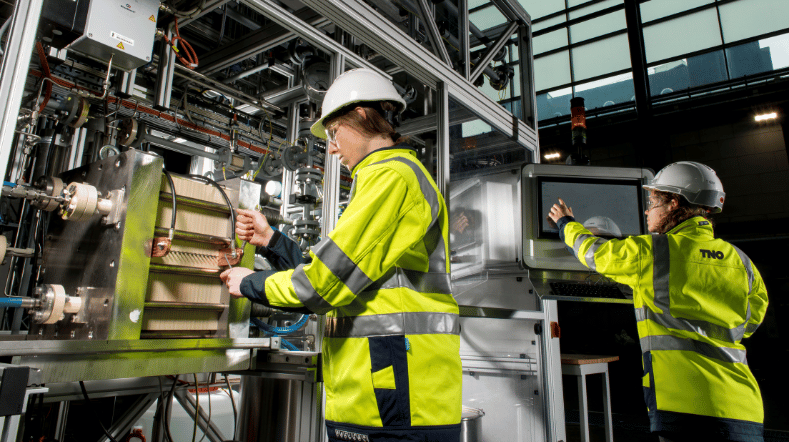
SEWGS: revolutionary CO2-reduction technology
Capturing carbon emissions
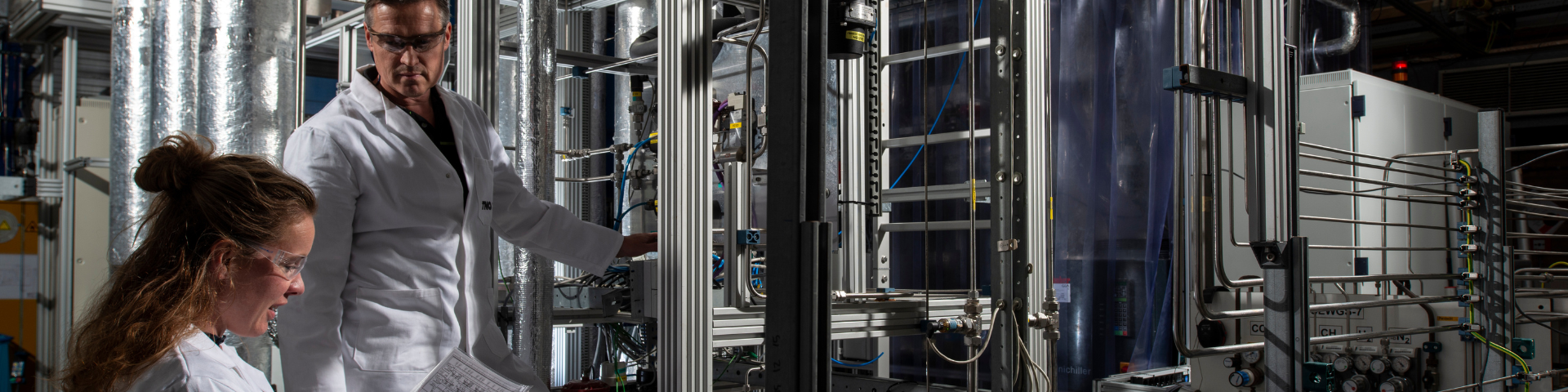
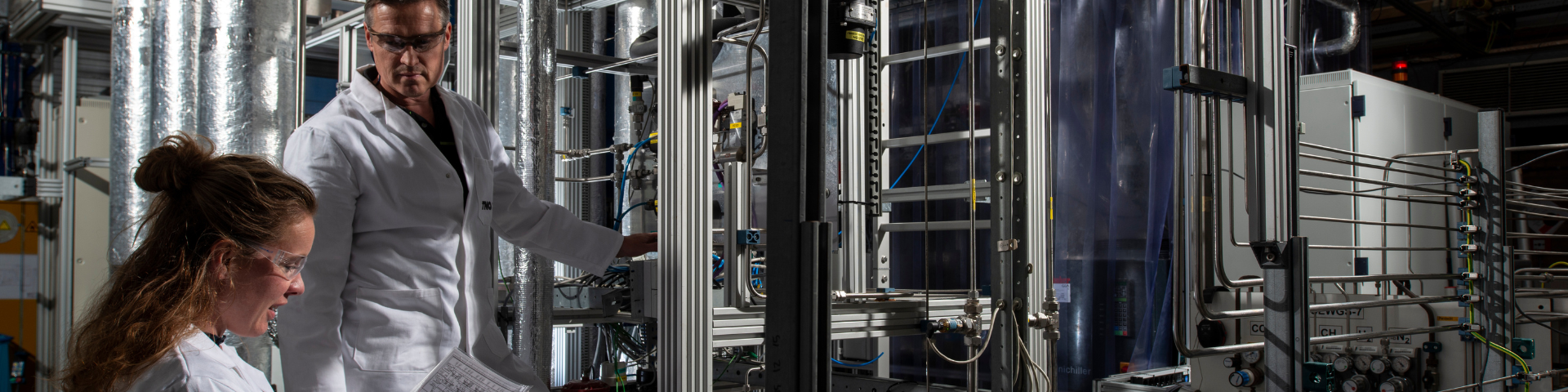
Award-winning excellence: CO2 capture applied
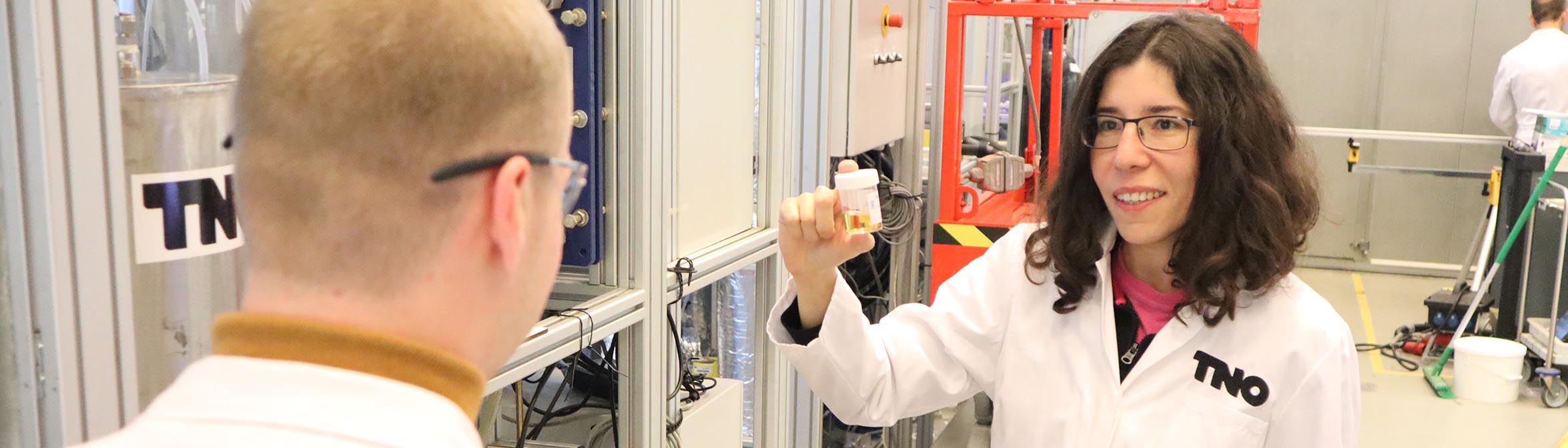
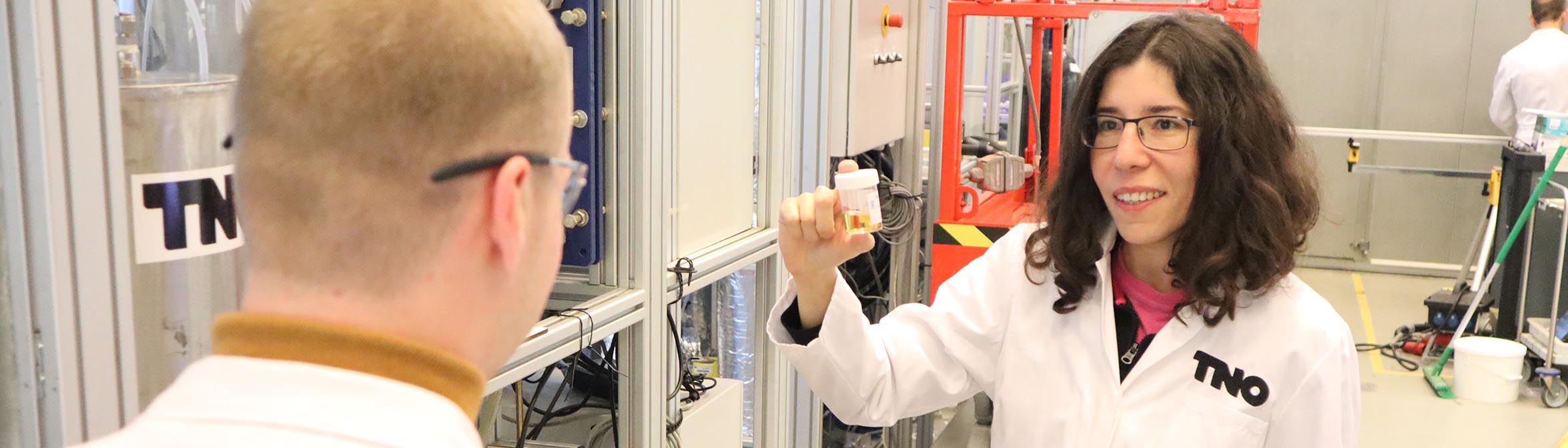