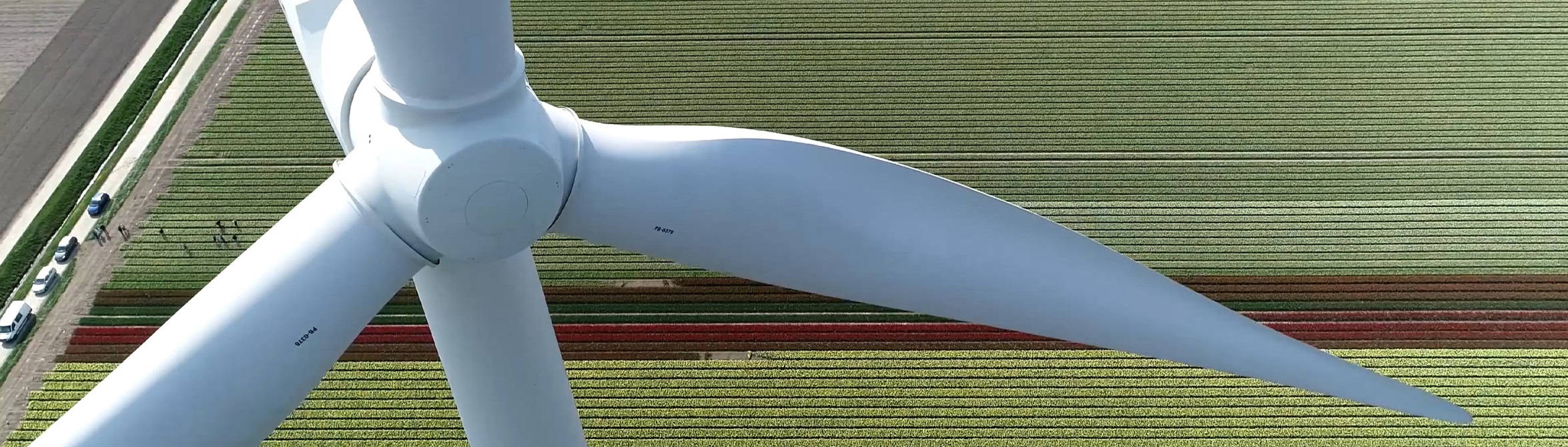
Making windturbine blades of 120 meter possible
To make wind power more competitive wind turbines must be enlarged. However, the connection of the rotor blade is a limiting factor. This has consequences for the maximum dimensions of the rotor blades, or the windmill blades. ‘Root bushing’, a Dutch technology, is destined to change the situation. Rotor blades of 120 meter enable the power generation to supply 26.000 households of electricity.
Largest wind turbine of the world
The largest wind turbine of the world is located at the Maasvlakte. With blades of 107 meter and a height of 260 meter the colossus delivers 12 to 14 Megawatt electrical power, enough for 16.000 households. The Danish Vestas is currently working on a 15 Mw wind turbine, enough to power up 20.000 households.
Can we still go bigger? Yes, thanks to a technical innovation of the Dutch company We4Ce from Almelo the 20 Mw turbine comes within reach. This turbine has rotor blades of 120 meter length and is able to generate electricity for 26.000 households. Put a number of these together in a wind park – for example at sea - and a city like The Hague can be completely supplied by wind energy when the wind blows.
Gigantic forces
In wind turbines, especially the connections of the blade to the rotor hub pose challenges. These connections encounter gigantic forces. “To assemble the blades to the rotor hub T-bolts have traditionally been used,” says project leader Michiel Hagenbeek from TNO.
“To fixate the wind turbine blades to the rotor 80 to 160 T-bolts are necessary. The larger the blades, the more T-bolts needed. But this has a limit. We are now at the point that the number cannot be increase anymore. Thus, the blades cannot be enlarged beyond the current length. Thereby, the maximum power is reached that wind turbines can generate.”
“More connections means more loads can be transferred and thus blades can become larger”
More efficient wind turbine blades
The company We4Ce, established in 2007, brought change to the situation. The company developed another method to connect the blade to the rotor: ‘root bushing’. The bushing is a toothed steel plug that is fixated in the composite blade root by means of vacuum infusion.
Managing director Arnold Timmer from We4Ce explains: “The advantage of the bushing technology is that it requires less space, and thus 30 percent more bolts can be used. More connections means that more load can be transferred and blades in future turbines can become larger. When using root bushing in current wind turbines, it means a significant reduction in costs and weight with respect to a T-bolt connection.”
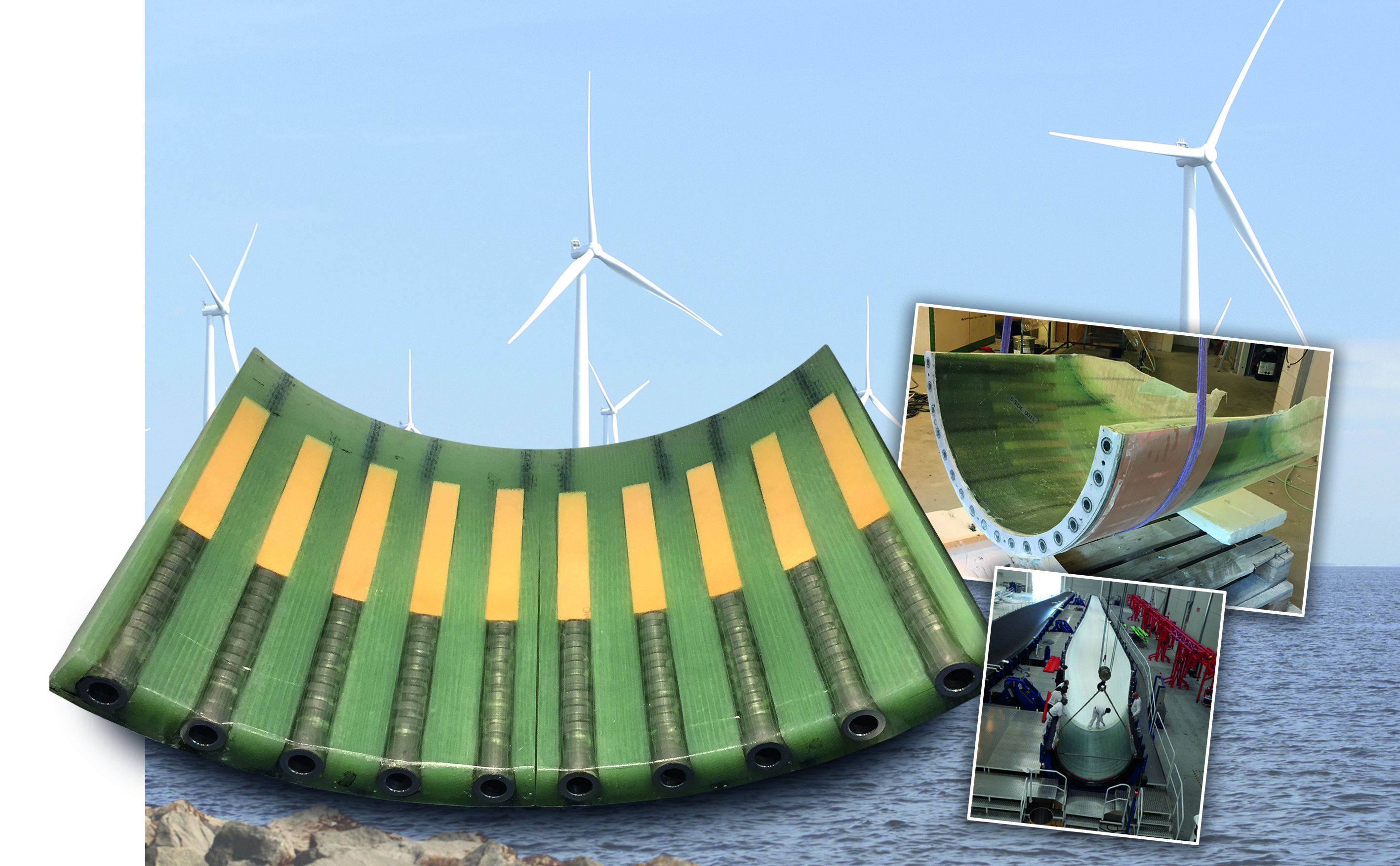
Coupon testing
Over the last two years the bushing-technology has been developed further on a fundamental level together with TNO and thereafter tested. Hagenbeek: “Testing a structure at full scale is expensive and only delivers knowledge of that specific combination of materials. We have chosen to test all components of the structure separately. The advantage of these coupon and medium-scale tests is that you are able to test precisely one aspect of the structure.”
Timmer adds: “That’s how we explored amongst others how steel and composite related to each other. We performed shear tests, in which you pull from two sides on materials that are adhered to each other. The life time of the structure has been assessed as well. A turbine must be able to spin for 20 to 30 years. In a test setup we exposed enormous cyclic loads to parts of the structure. In total more than 100 tests have been performed.”
Cameras and software
Root bushing connect steel to composite, a structure that is not yet commonly used and much knowledge is still to be gained about it. Timmer: “TNO is one of the few knowledge institutes in the world that is able to test new materials and connections on a fundamental level. That is why the choice for TNO was logical. With the test results we have improved our insight in the connection between steel and composite. It turned out that the structure was even stronger than we had expected, which results in the fact that we can use less bushings per rotor blade.”
Hagenbeek: “In these tests the deformations and failure sequences of the steel-composite connections have been carefully captured with special cameras and software. The shape of the bushing- conical or straight – has been investigated as well. The research showed that a trapezoid gives the best result. Meanwhile this shape has been patented. The root bushing is loaded cyclic in reality as the blades turn around. Both bending-, tensile- and compressive forces are loading the structure."
"To determine the behaviour of the bushing under these continuously changing loads a series of fatigue tests have been performed. We test at which load and number of cycles the structures fails. Fatigue curves have thus been determined. These curves happened to lie much higher for the selected bushing-concepts than for other connections. In simple words: they are much stronger.”
“From test results it turned out our structure was even stronger than we had expected”
Staying in the lead
The test have been executed in such a way that the investigated technology is ahead of the development of future wind turbines. Timmer: “We have tested technologies that not only enable larger blades, but also come at an interesting and cost-efficient price. In a follow-up project we will be testing even stronger connections, that is bolts with a diameter of 42 millimeter. It will take some years before that new ‘M42 bushing-technology’ will be used in wind turbines.
The aim of We4Ce is to stay ahead. By testing on a fundamental level, we stay ahead of the competition. Foreign competition is another reason to work together with TNO. We could have had our bushing tested in Denmark or Spain. However, Vestas and Siemens Gamesa are active there. And we do not want to share our knowledge directly with these competitors. In that case it feels better to work together with a Dutch partner.”
Mega wind turbines
The maximum length of wind turbine blade on shore is currently around 110 meter. Thanks to the bushing-technology blades can become even larger. Why is this so important? Hagenbeek: “The power generated by a wind turbine is determined by the covered area of the blades during turning. That area increases quadratically with the blade length. Blades a couple of meters longer are thus able to yield tremendously more.”
Timmer: ‘That might be socially sensitive. Not everyone is enthusiastic about large wind turbines in the land scape. But larger turbines are necessary to increase the competitiveness of wind energy. The cost price has to decrease. Of course it is up to politics to decide on the right locations for mega wind turbines and parks”
Want to know more about research on mega structures and the possibilities of our innovative test facilities? Please contact Michiel Hagenbeek.
Get inspired
Improving wind turbine maintenance with the sensor installation robot
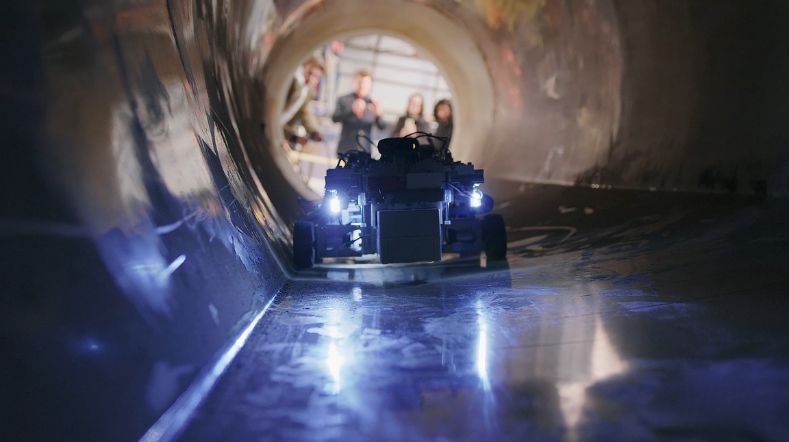
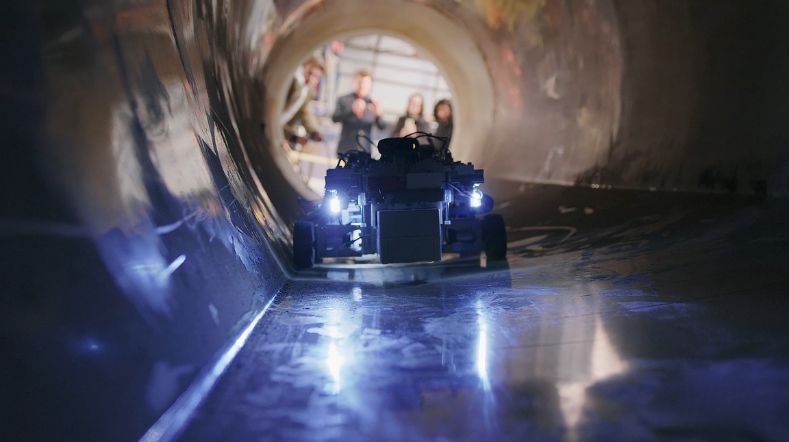
Project launched for recycling wind turbine blades
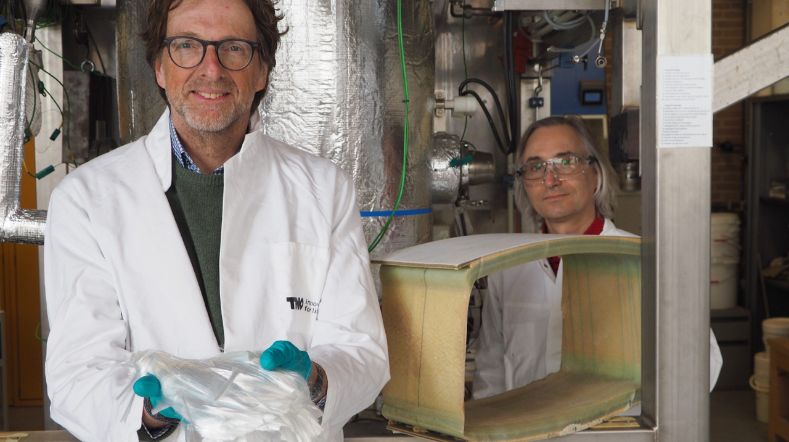
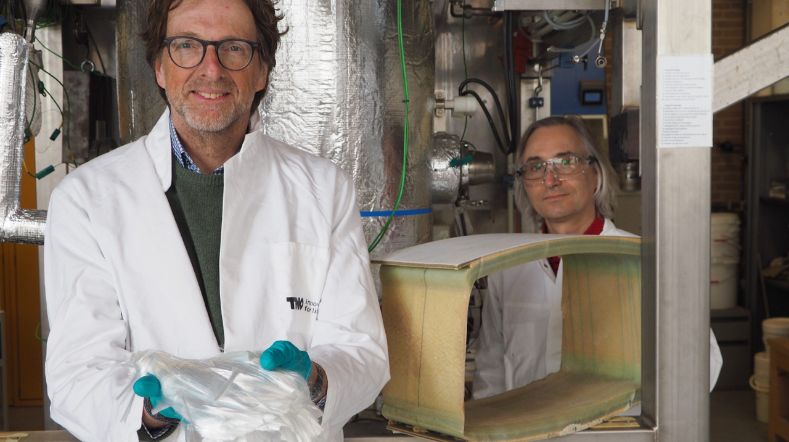
Shade screens with rollable solar foil combines energy generation with climate control in greenhouses
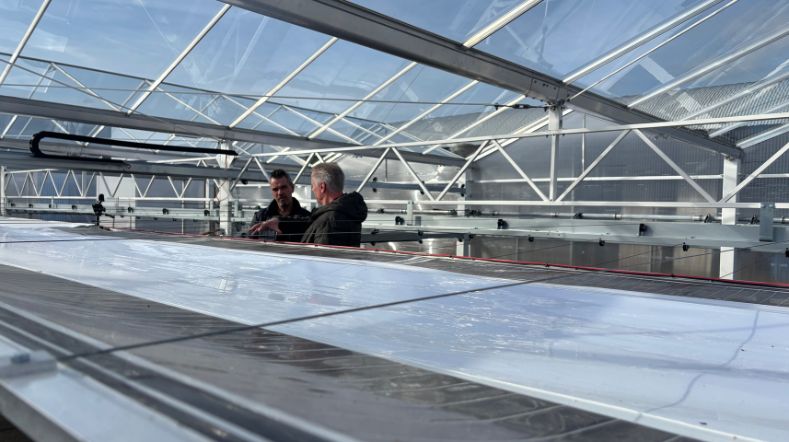
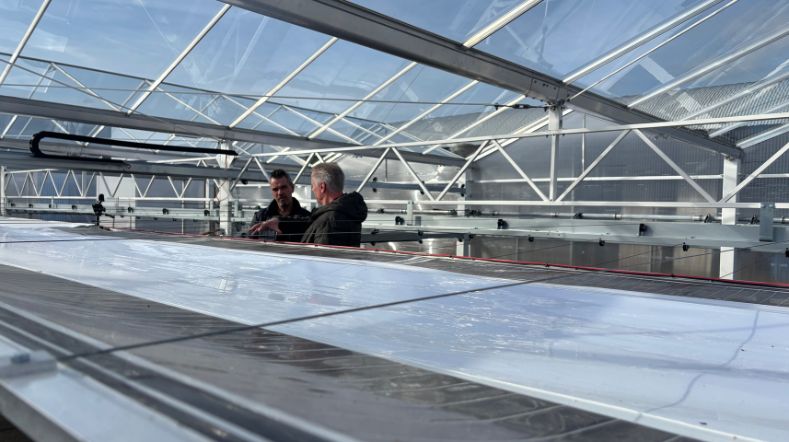
TNO research leads to better damage prediction for offshore wind turbine blades
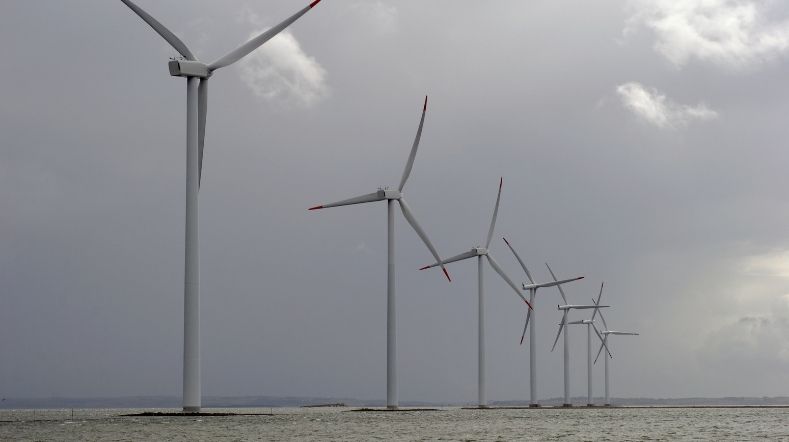
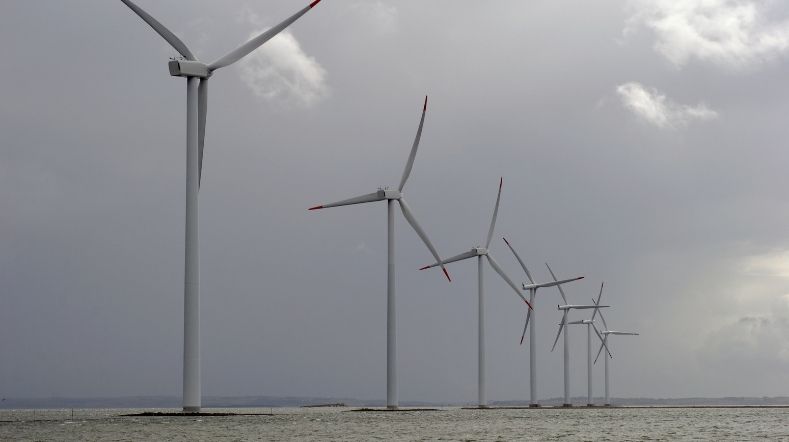
Better damage prediction for wind turbine blades through unique weather measurements at sea
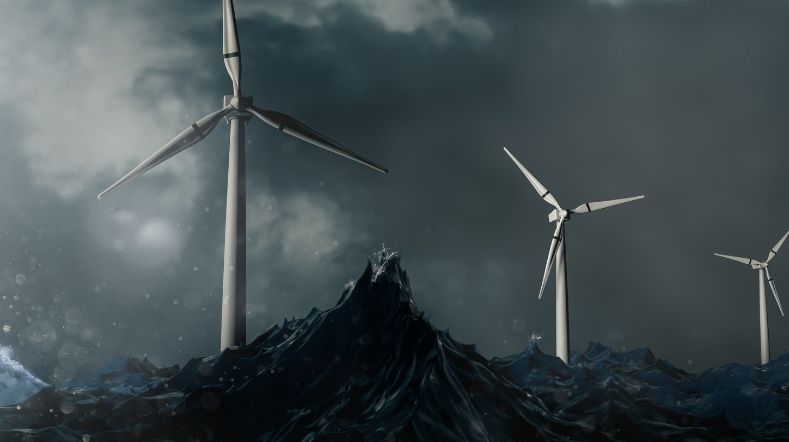
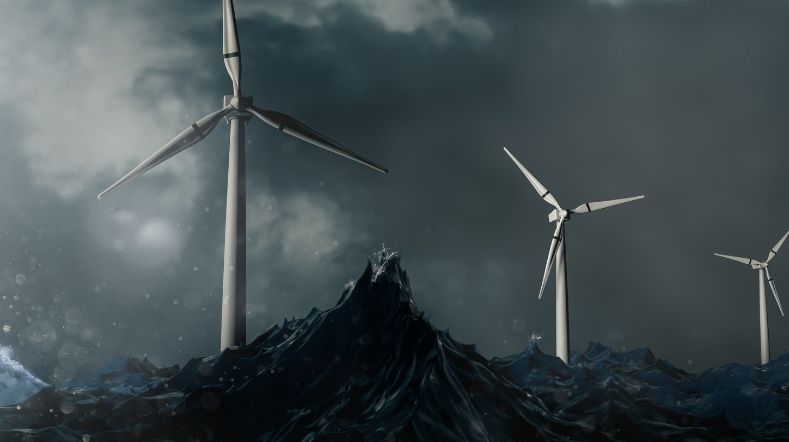