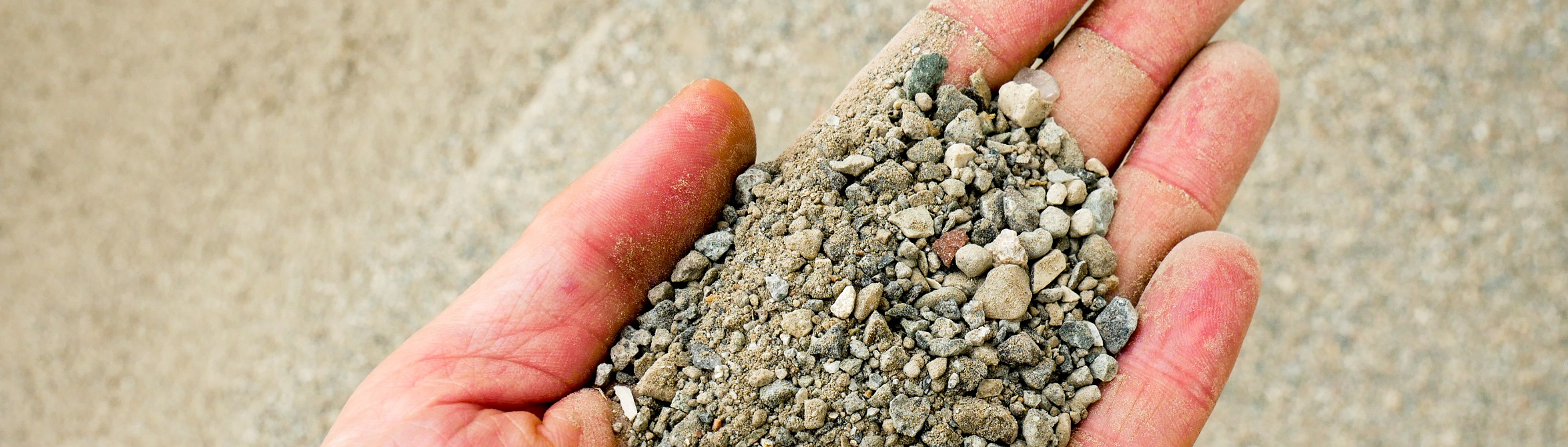
Searching for the best recipe for circular concrete
The production of concrete is responsible for 5 to 8 percent of global CO₂ emissions. Together with the construction industry, TNO is diligently searching for solutions to this problem. So much is currently happening in this area that we are devoting two articles to the subject. Part 1 focuses on the search for the best recipe for circular concrete.
Concrete as construction material
If you are building something, there is a good chance it will involve concrete. Concrete has already been around for a few thousand years. For example, the Romans were able to make a surprisingly strong and durable type of concrete using a mix of lime, volcanic sand and water, which they then used for quay walls, bridges and aqueducts.
Now, in 2021, a world without concrete is almost unthinkable. This is due in part to the invention of reinforced concrete in the mid-nineteenth century, which allows concrete structures to bear much heavier loads. Today, concrete is the most widely used construction material worldwide. It is also a relatively cheap material. After all, to make it you only need sand, gravel, cement and water.
"Cement is responsible for no less than 90% of the total CO₂ emissions from concrete."
High CO2 emissions
As stated before, the production of concrete is responsible for 5 to 8 percent of global CO₂ emissions – much more than the emissions caused by air traffic. The biggest challenge for the sustainability of concrete is the cement. The production of cement actually requires extremely high temperatures of up to 1,450 degrees and the conversion of limestone results in high CO₂ emissions. Cement is therefore responsible for no less than 90 percent of the total CO₂ emissions from concrete.
Concrete shame
Concrete is subject to strict requirements and the concrete sector has been quite unwilling to change for a long time now. However, even the world of concrete is starting to realise that things really do have to change. For example, Dorien Staal caused quite a stir in 2019 when she introduced the term 'concrete shame' during the Betondag (Concrete Day).
In doing so, she was speaking not only as general manager of Voorbij Prefab, a precast concrete factory in Amsterdam, but also as the new president of the Dutch Concrete Association. She called on the Dutch concrete sector to work together to find ways to reduce CO2 emissions from concrete as quickly as possible.
Up to 44 percent CO2 reduction
Her words were soon followed by actions when, a year later, Staal announced that her company, together with engineering firm ABT, had developed a new concrete mixture that uses a combination of traditional cement and geopolymer activation. That new approach means a CO2 reduction of up to 44 percent can already be achieved during the production of concrete precast elements for homes.
Open source
"In our new concrete mix, we not only use cement but also blast furnace slag as an ingredient for the binder. In the Netherlands this has, of course, been going on for quite some time. The point is that we use a huge quantity of blast furnace slag and a minimal amount of cement. We get the blast furnace slag through alkaline activation. The only problem is that at some time in the future there will not be enough blast furnace slag to make this process sustainable on a very large scale," Staal concedes.
"In order to be able to scale up our new concrete production method, we will have to look for alternative materials."
"And when Tata Steel switches to a production method based on hydrogen, this will also have immediate consequences for the availability of blast furnace slag. In order to be able to scale up our new concrete production method, we will have to look for alternative materials. We have now set up a consortium to tackle this, in which we are working closely with TNO, BTE, VBI and 2 'R' Recycling. The rule is that the participants must be willing to share their knowledge of concrete technology. And that’s precisely what we are doing. Everything we do in the field of sustainable concrete is open source. And it should be. Because if we, as a concrete sector, do not work together in this field in an open way, it will be very difficult to achieve the climate objectives."
Possible candidates for replacing the blast furnace slag in the more sustainable concrete could be calcined clay, for which different types of clay can be used, and volcanic material, which is a raw material that the Romans even used to make concrete. In the present twenty-first century, that material would, however, be used for the largely automated production of sustainable concrete that meets all modern-day requirements.
Laboratory experiments
If we look a bit further ahead, the following problem looms large, namely that as long as cement is the only binding agent in concrete, it will be impossible for the concrete sector to achieve the desired neutral CO2 emissions by 2050. This means that a low-cement or cement-free concrete must be developed. Currently, numerous parties are already searching for the right recipe.
One of them is TNO. In addition to carrying out laboratory experiments on cement-free concrete, TNO is trying to determine, as accurately as possible, the sustainability impact of these new types of concrete. “This is often quite difficult,” says Elisabeth Keijzer, researcher in sustainable construction & infrastructure.
“In order to be able to provide a true picture of CO₂ emissions, you don’t just need to include the production methods and materials used in the calculations – you also need the expected lifespan and recycling possibilities. And all that even though you can only guess at how people will reuse the concrete in 50 or 100 years’ time. We try to avoid counting our chickens on the basis of assumptions about something that is only going to happen way into the future.”
Concrete from waste material
Research into cement-free concrete based on alternative binders such as geopolymers looks promising. These geopolymers can be extracted from mineral waste streams, and this new type of concrete binder can be produced at lower temperatures.
“It’s an extremely positive development,” confirms Agnieszka Bigaj-Van Vliet. At TNO, she is the expert in the field of circular concrete constructions and welcomes the fact that, after years of research into new binders, a new generation of concrete sorts is finally going to become available.
“But we don’t want to draw up new design rules for each type of concrete. That would make things unnecessarily complicated. So that’s why we’re now developing flexible design models for concrete structures, for which there is immediate clarity regarding the limit load and lifespan of the structures created using various new types of concrete. We are also applying the same safety philosophy in the design method for circular concrete structures as in the current design rules for structures using traditional types of concrete.”
"A concrete structure that you build today can last for up to a hundred years. The fact is that the CO₂ problem exists in the here and now."
The big challenge today
“We’re forgetting something!” says Siska Valcke, who has been working as a TNO researcher on technical developments in the field of circular concrete for more than ten years. “The fact that more sustainable types of concrete are being developed is a good thing, of course, but that’s something for the future. A concrete structure that you build today can last for up to a hundred years. The fact is that the CO₂ problem exists in the here and now."
"That’s why we advise the construction industry not to demolish existing concrete structures until they really are at the end of their lifespan. If a building, bridge, or some other infrastructure no longer meets the requirements of the times, but the concrete structure is still fine, we recommend using that structure, or parts of it, as the basis for a new structure.”
In terms of reuse, a lot is already possible. So much so that we are devoting an additional article to it!
Want to know more about TNO's initiatives in the field of circular concrete? Please contact Jeroen Kruithof.
Get inspired
Scaling-up electrochemical technologies for renewable ethylene production
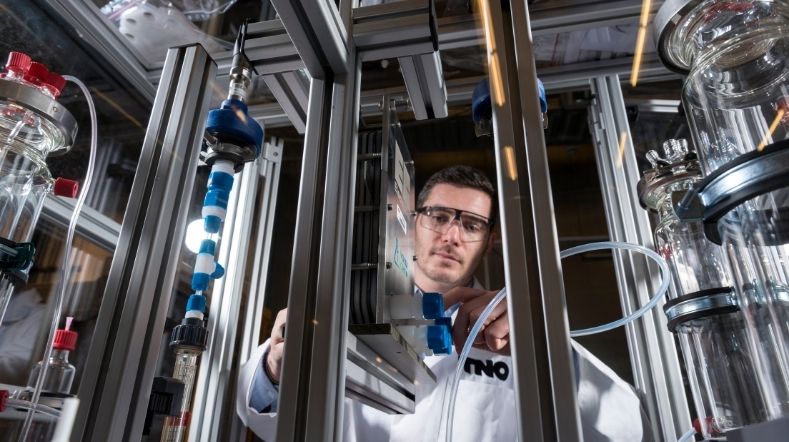
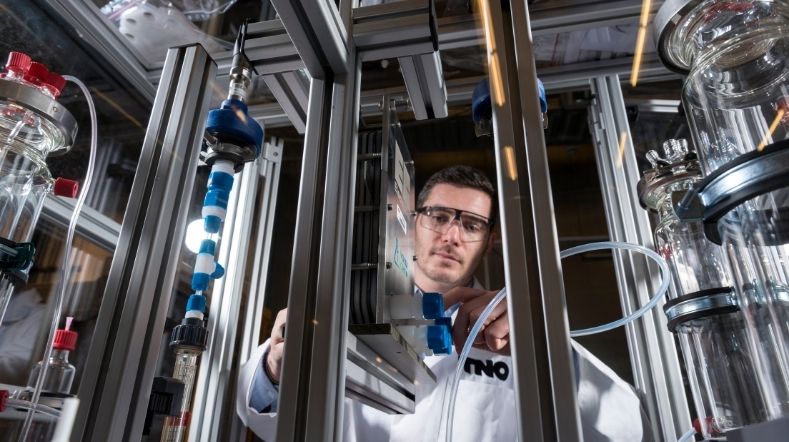
CO2 infrastructure and transport


Carbyon: the TNO spin-off innovating in CO2 filtration technology
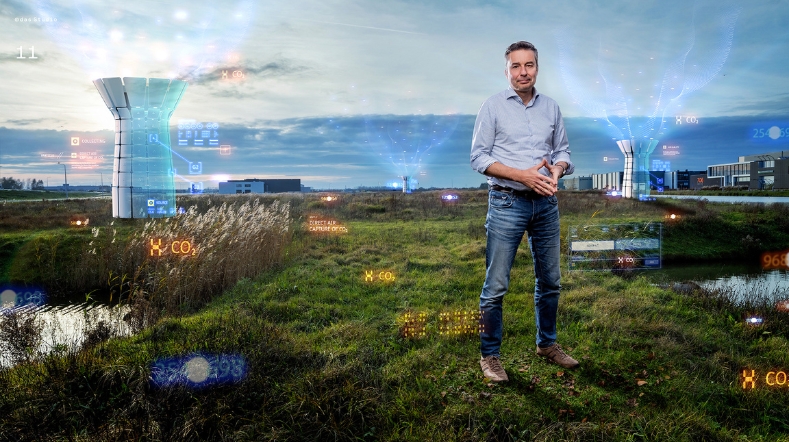
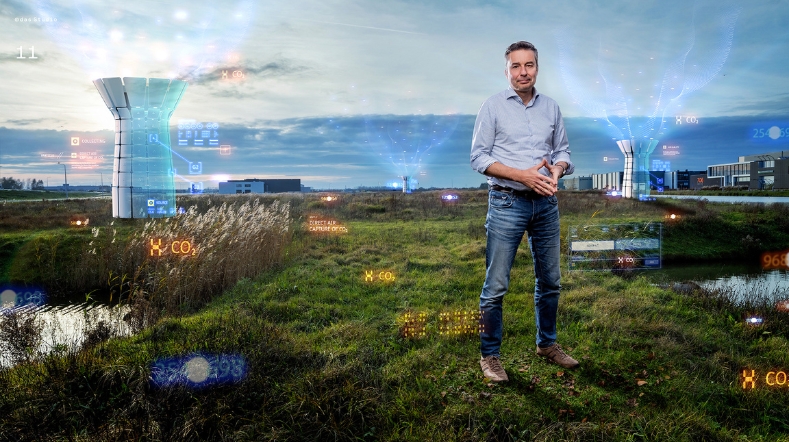
TNO’s next generation biorefinery accelerates material transition
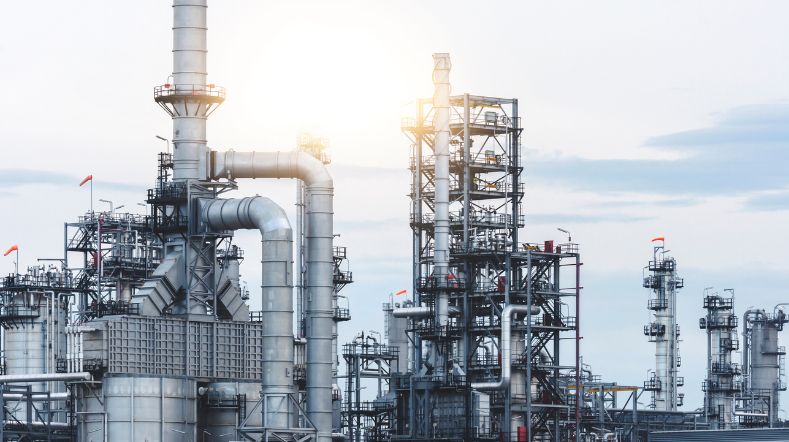
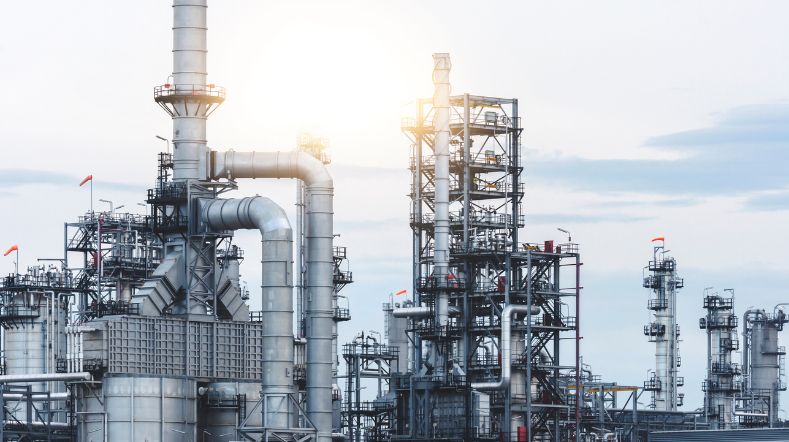
Port of Rotterdam as a key European hub for sustainable carbon
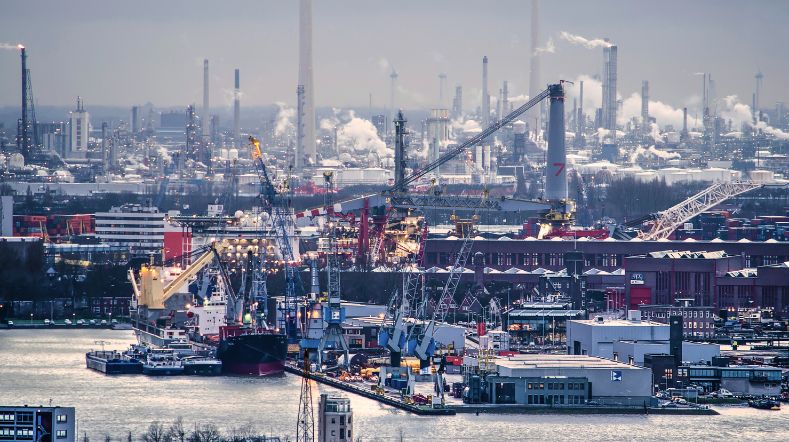
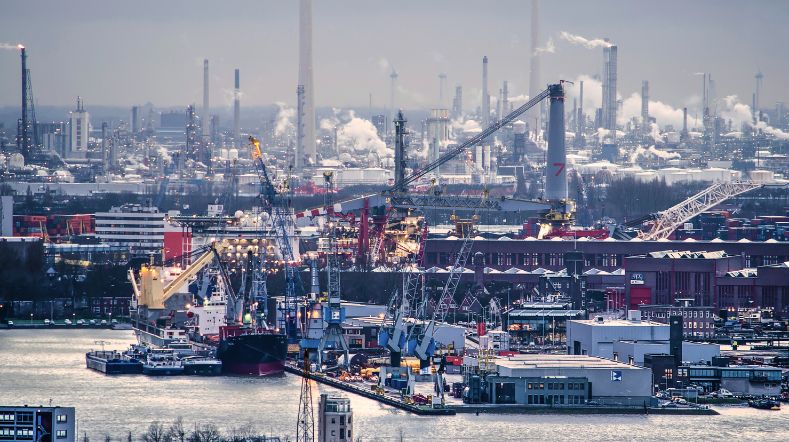