Time setters: 200 times less iridium needed for green hydrogen production
At TNO, we make a mark on our time. In this series, you’ll meet the TNO employees behind the innovation – the time setters. What do they do and what impact does their work have on society? In this episode, we speak to time setter Lennart van der Burg, Cluster Manager for Green Hydrogen, about the breakthrough development in electrolysers and how we can produce green hydrogen on a larger scale.
What is electrolysis?
“The electrolyser is the device used to produce hydrogen through electrolysis, the process by which water is split into hydrogen and oxygen, using electricity and a membrane. Although the technology is a century old, it was never really fully developed because cheap natural gas eliminated the need to produce hydrogen. The current climate crisis has created an urgent need to cut CO2 emissions to zero. Green hydrogen is seen as an important means of moving towards a completely climate-neutral energy system.”
Why is hydrogen needed?
“There are three main reasons to use hydrogen:
- Integration of offshore wind: wind turbines in the North Sea currently generate 3 gigawatts of wind power, but by 2030, this could rise to 21 gigawatts. At some point, we’ll produce so much electricity that there will be a surplus. It will be possible to convert this into hydrogen, which could be stored in, for example, empty salt caverns, to be used when renewable energy is not available.
- Making industry sustainable: the second goal is to make heavy industry more sustainable, such as the steel, aviation, and shipping industries, where direct use of electricity is not an option.
- Security of energy supply: the third objective is to ensure security of supply. In winter, we currently rely heavily on fossil natural gas, which could potentially be replaced by hydrogen in the future.”
“To achieve these goals, it’s important that electrolysers become cheaper, more efficient, and more sustainable. A key point is that the PEM type of electrolyser uses the scarce raw material iridium as a catalyst. To produce the huge amount of hydrogen that the European Union has set as a goal, and to become climate-neutral, we need a large number of electrolysers and therefore a lot of iridium.”
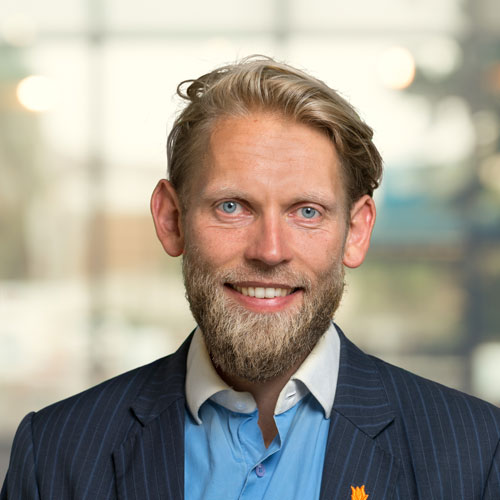
“We’ve succeeded in developing a method that requires 200 times less iridium and which already achieves 25%-46% of the performance of the current generation of electrolysers.”
“The entire hydrogen production chain can benefit from this breakthrough. From the parties that make the machinery, through the coating technology, component developers, and electrolyser manufacturers, to the end user that will ultimately produce the hydrogen through electrolysis: heavy industry. Everyone’s goal is to ensure that we can produce hydrogen as sustainably and efficiently as possible, using as few materials as possible.”
How do you manage to use 200 times less iridium?
“At TNO Holst, we previously developed the spatial Atomic Layer Deposition (sALD) technology – a method for applying extremely thin layers of functional materials to large surfaces. It was intended for use in developing a new generation of displays for TVs, tablets, and smartphones. We’ve now also made the technology applicable to electrolysers, applying atomically thin layers of iridium to the electrolysers, so that we need much less than before.”
How did the idea come about?
“Two years ago, the two TNO departments in Petten and Eindhoven joined forces. They started a joint internal research project, in which this idea emerged as the most promising.”
Can hydrogen production be made even more sustainable?
“Water electrolysis to make hydrogen is close to being market-ready because there’s already a whole industry that needs hydrogen. But existing ‘grey’ hydrogen production based on fossil natural gas has very high CO2 emissions of more than 10 kg of CO2 per kg H2, which is not sustainable.”
“A further step in development is CO2 electrolysis, which we’re working on in the TNO Voltachem programme. The aim here is to make new chemicals from green electricity, water, and CO2 from the air or from biomass. We’re studying what chemicals we can make and which types of electrolysis are needed to do so.”
“There are still challenges, such as a stable membrane and the right catalyst for optimum conversion. By using electricity directly to manufacture new products, plastics, and chemicals, we can make the future more sustainable and meet the needs of society.”
Want to work at TNO? Become a time setter
Would you also like to join Lennart in contributing to smart solutions like these?
Get inspired
World Hydrogen Summit 2025
Hydrogen in the energy system: The future of sustainable energy in the Netherlands and Europe
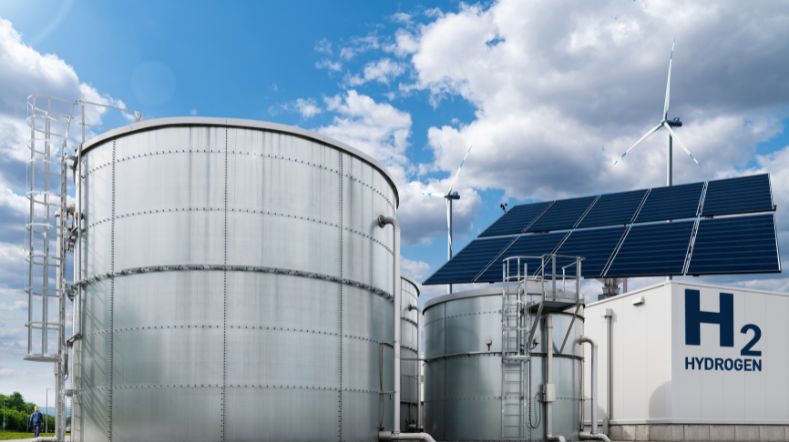
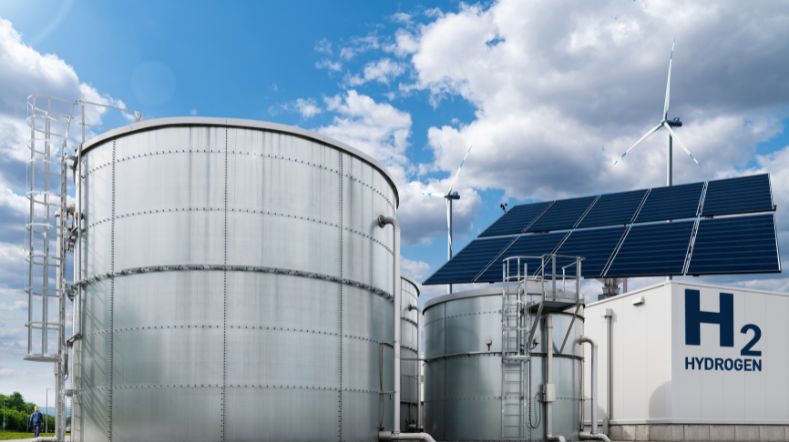
NORCE and TNO are entering into a strategic partnership on hydrogen developments
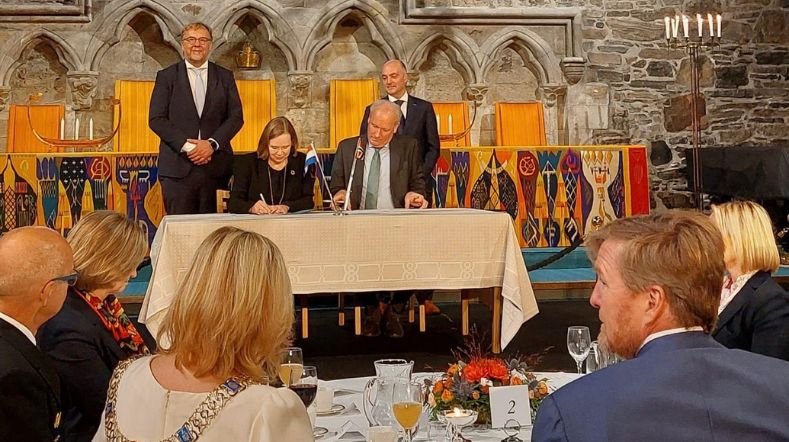
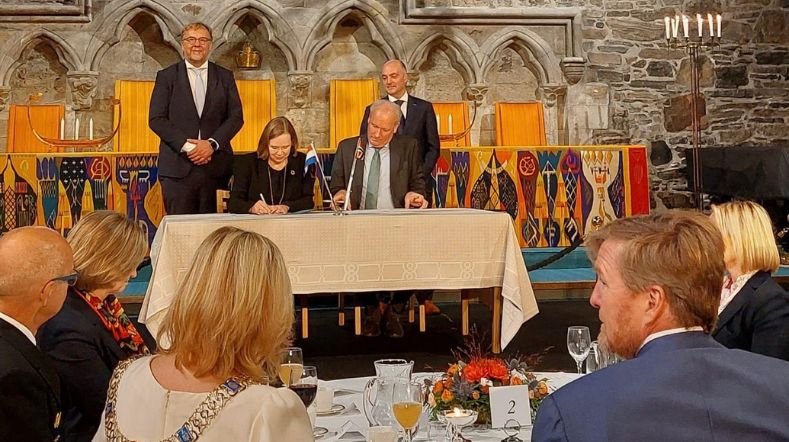
Dutch consortium participates in EU research project on large-scale hydrogen storage in depleted gas fields
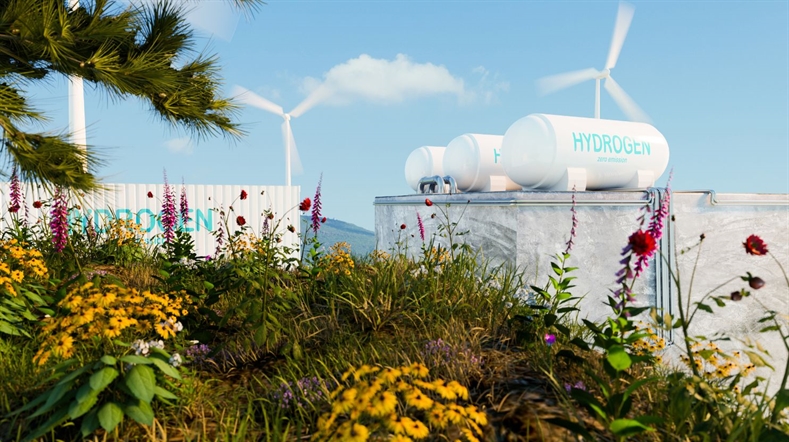
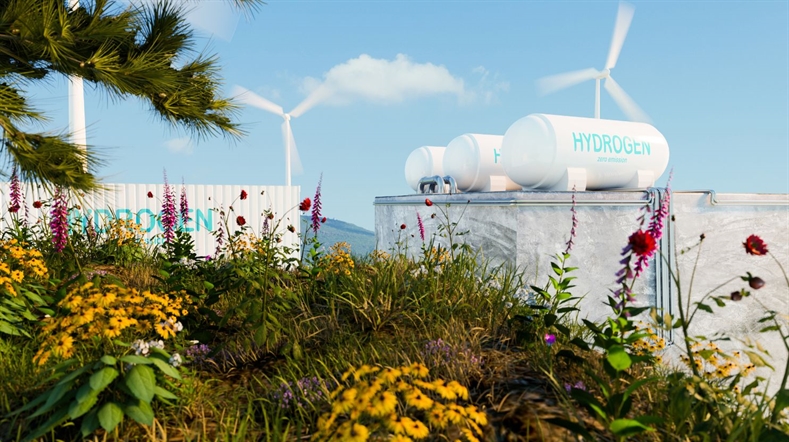
Underground hydrogen storage
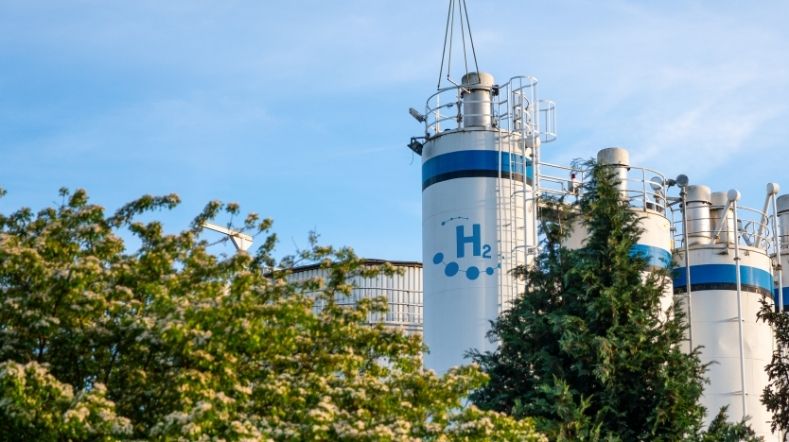
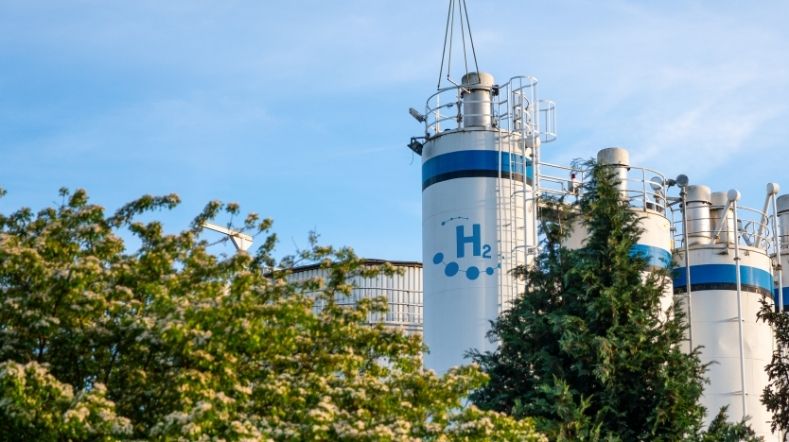