
No energy transition without raw materials transition
From cobalt and lithium for producing batteries, to iridium for producing hydrogen. The success of the energy transition is determined to a great extent by the availability of scarce raw materials from a small number of countries. To reduce that dependence, a materials transition is needed in addition to an energy transition. Four examples showing how TNO is working on alternative raw materials and production processes for even better batteries, electrolysers for hydrogen, solar panels and wind turbines.
Four examples of material transition:
- Electric driving with cobalt-free batteries
- Smarter raw material usage for mobile phones
- Breakthrough in hydrogen production upscaling
- Circular solar panels are more sustainable
Green Deal and material transition: What is required to achieve that?
Meeting climate targets and limiting global warming will require an energy transition on an unprecedented scale. But to ensure that fossil-free future, raw materials are needed. A whole lot of raw materials, according to Belgian university KU Leuven.
For example, if the European Union wants to meet the target of climate neutrality by 2050, 35 times more lithium will be needed than is currently consumed in Europe. Supplies of aluminium, copper, silicon, nickel and cobalt must also be drastically increased for the production of electric vehicles and batteries and for renewable wind, solar and hydrogen technologies.
Not only are there concerns about the availability of raw materials, but also about security of supply. Europe is becoming dependent on a small number of resource-rich countries. As each government seeks to secure its energy supply, competition for raw materials will put geopolitical relationships on edge.
Materials transition in 4 examples
For the energy transition to succeed, we at TNO are looking at all aspects of raw materials. We pinpoint which materials are essential and how to secure them. We are also developing sustainable technologies based on alternative materials, and production and recycling techniques that use scarce raw materials even more efficiently.
These four examples show how we at TNO are working on this materials transition.
1. Electric driving with cobalt-free batteries
From 2035, all new cars sold in Europe must be electric. This means that the automotive industry will become heavily dependent on the availability of lithium and cobalt needed to produce batteries. To reduce that dependence and build a competitive knowledge edge in sustainable battery technology in the Netherlands, the Battery Competence Centre has been set up.
Knowledge institutes like TNO collaborate with technology companies on innovative battery materials, such as silicon anode, and advanced thin film production technologies. About two-thirds of mined cobalt comes from the Congo. Apart from the fact that mining requires a lot of effort from the miners, there are reported abuses of child labour and environmental pollution.
COBRA (CObalt-free Batteries for FutuRe Automotive Applications) is a joint research and innovation project aimed at developing a new generation of cobalt-free lithium-ion batteries. As an alternative, the common metals nickel, iron and aluminium are used, making this battery system and therefore electric driving cheaper.
2. Smarter raw material consumption for smartphones
More than a billion smartphones are sold worldwide every year. These are full of all kinds of metals, some of which are scarce. Indium is used for the touch screens, neodymium is needed for the vibration function, and lithium is in the battery.
A lot of gains can be made in the battery in particular, according to LionVolt. This spin-off from TNO at Holst Centre is working on 3D solid state batteries. This technology brings to market the next generation of batteries, which are intrinsically safe (solid state cannot explode) and lightweight, charge at lightning speed and have a much longer lifespan.
Moreover, making them also requires fewer raw materials. LionVolt uses thin film processes familiar from the production of flat panel displays for this purpose.
One such patented process is spatial Atomic Layer Deposition (sALD), a technology developed by SparkNano, another TNO spin-off at Holst Centre. sALD allows you to apply very thin layers of material with high precision. This technology contributes to producing even better batteries more efficiently and to a much reduced use of iridium in electrolysers producing green hydrogen.
3. Breakthrough in scaling up hydrogen production
The availability of large quantities of affordable green hydrogen is essential for the success of the energy transition. It can be used to store surplus wind energy, to make heavy industry more sustainable, and as a buffer to provide security of energy supply in all seasons.
To produce green hydrogen, you need an electrolyser, which uses a membrane coated with iridium or platinum as a catalyst to separate hydrogen and oxygen. Those extremely rare raw materials are precisely the bottleneck for scaling up hydrogen production. Because to meet hydrogen demand by 2050, we need to increase electrolysis capacity worldwide by a factor of 25,000.
With current technology, that ambition is not viable. Therefore, TNO is working on three solution approaches:
- Reducing dependence on critical raw materials
- Intensifying the use of current electrolysers
- Recycling critical raw materials
4. Circular solar panels are more sustainable
We are increasingly generating energy from the sun. The more than 14 gigawatt peak (GWp) of installed solar power capacity for electricity generation in the Netherlands is expected to increase toward 50 GWp by 2030 and 200 GWp by 2050.
However, this renewable energy source could be a lot more sustainable. For example, solar panels still end up in the shredder on a large scale to serve as filler material for road and other construction work. By 2050, this would involve 10 billion solar panels worldwide, weighing 60 million tonnes.
Moreover, scarce and valuable materials such as silicon, silver, and copper are hardly being recovered. That is why TNO is working on a circular design for recyclable solar panels, which allows almost all materials to be recovered at the end of their useful life and reused for other high-value applications.
In the EU Horizon Europe project PILATUS, 19 companies and research institutions are working together to organise the entire chain, from design and production to disposal, disassembly and recycling, in a circular manner. TNO is also working with partners on alternative materials that are less harmful and more readily available.
Get inspired
Urban mining crucial: more critical and strategic materials from electronics and electrical devices
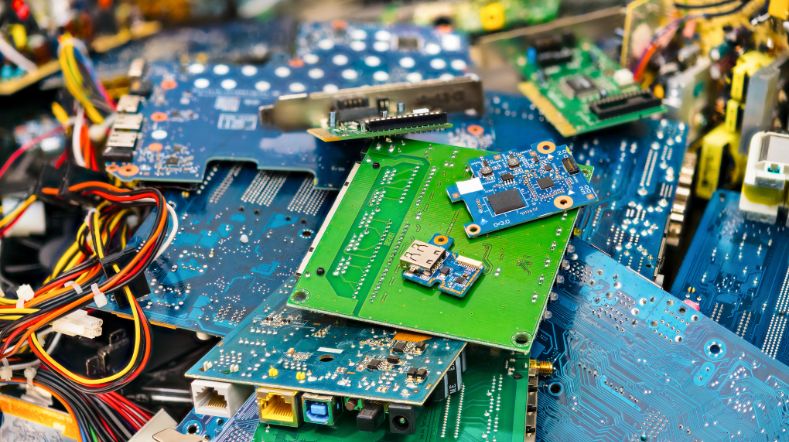
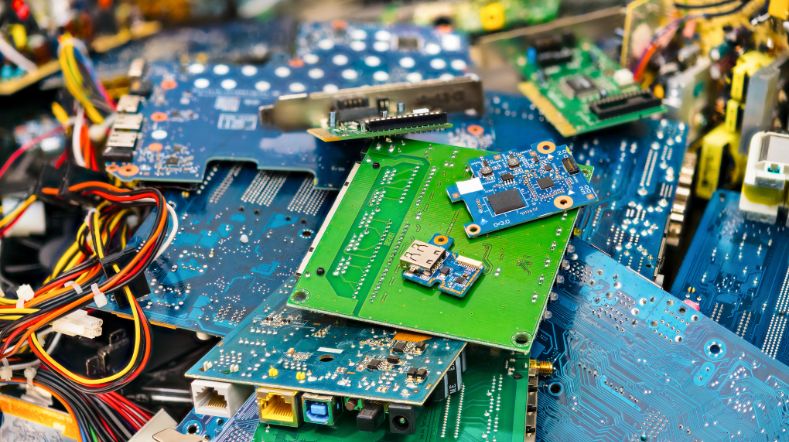
Prospective Life Cycle Assessments for future-proof product design
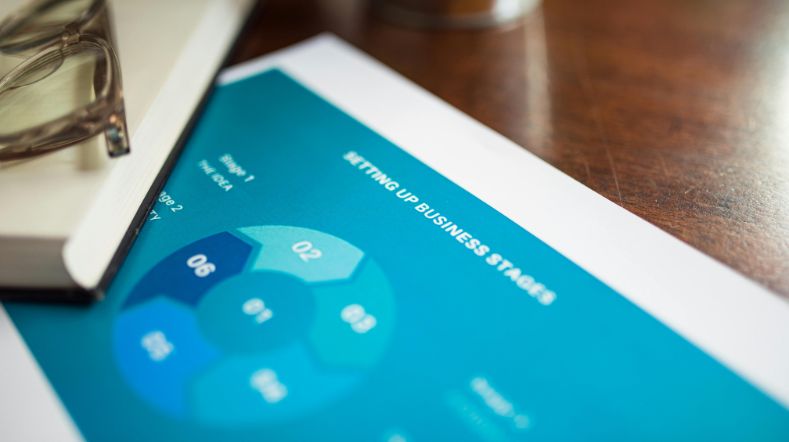
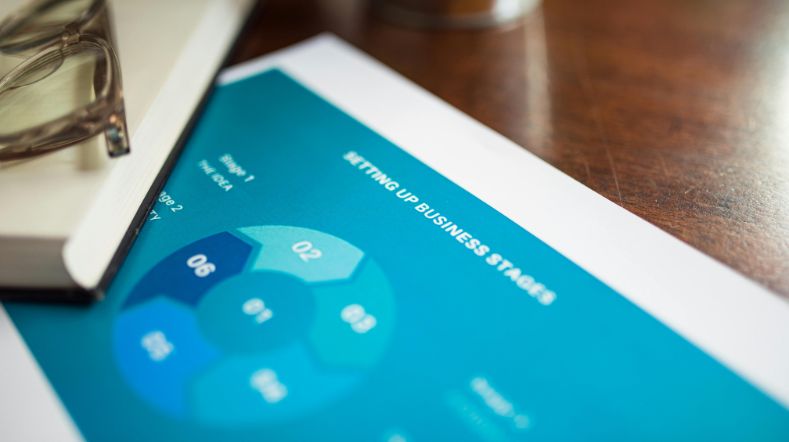
Netherlands Materials Observatory (NMO) officially opened
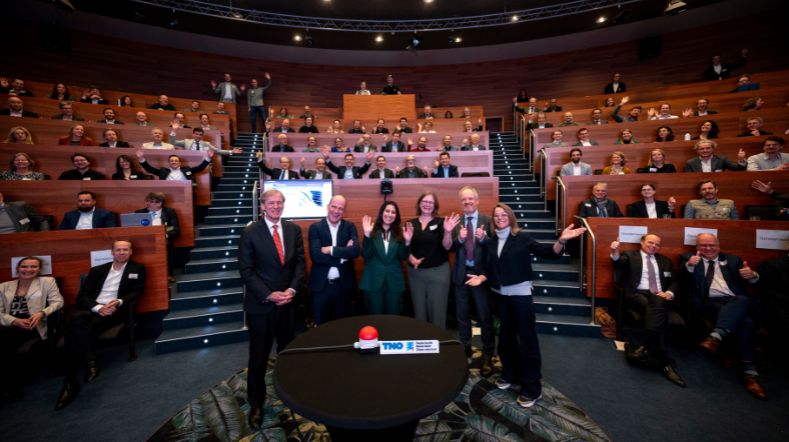
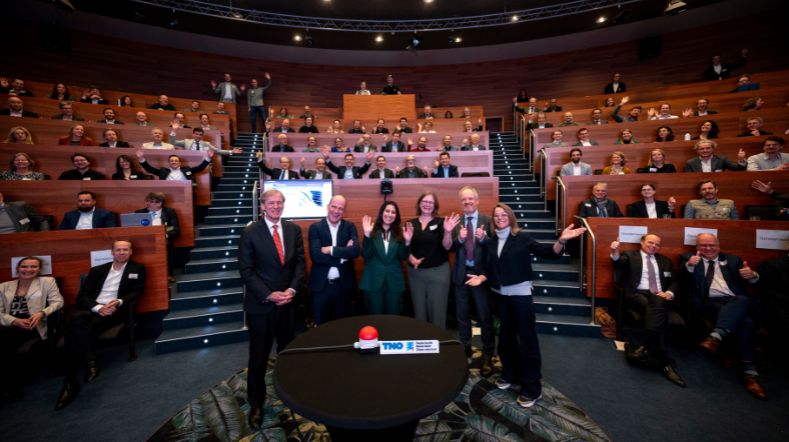
Recovering critical raw materials from LFP Batteries
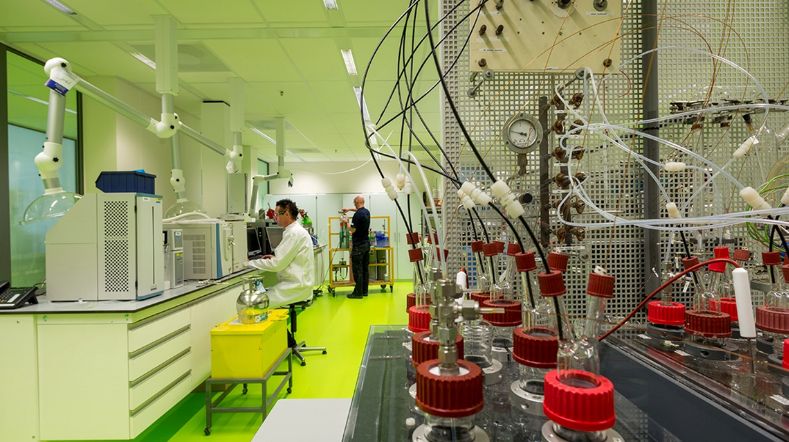
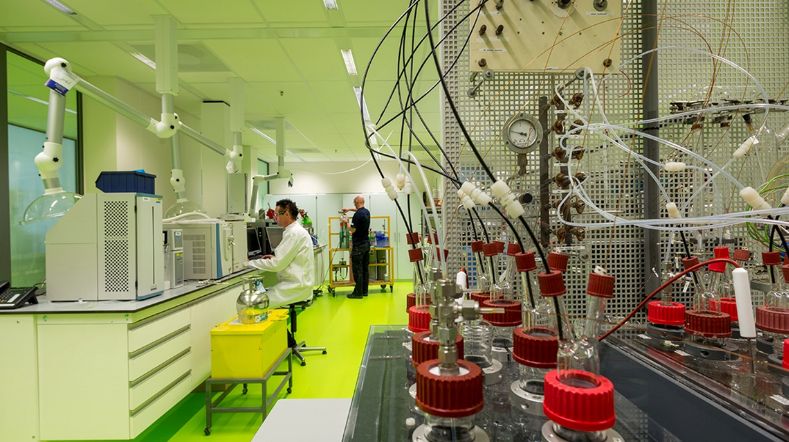
Critical raw materials

