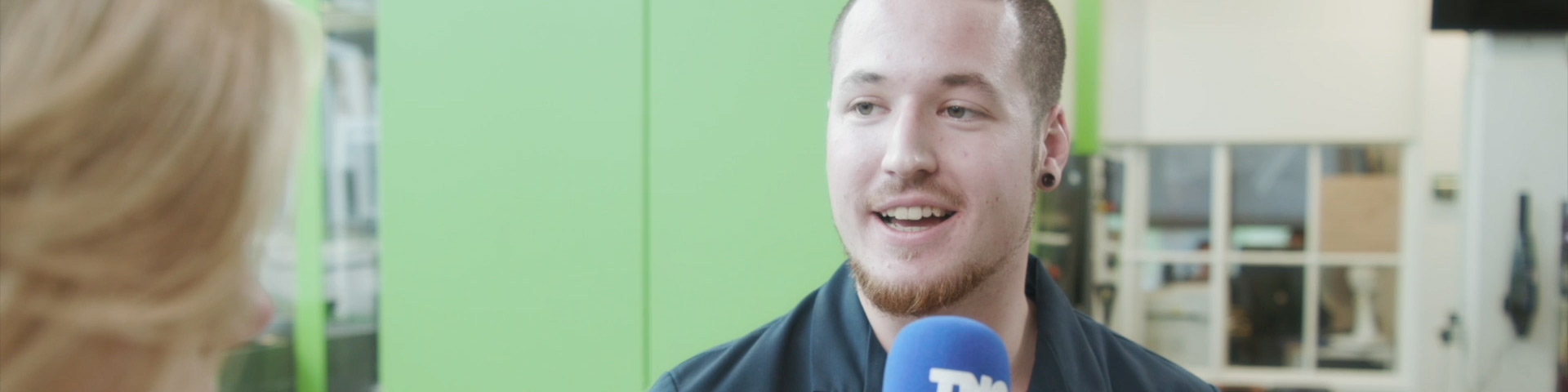
Time setters: Safely recycling dirty food packaging
At TNO, we make a mark on our time. In this series, you’ll meet the TNO employees behind the innovation – the time setters. What do they do exactly and what impact does their work have on society? In this episode, we talk to time setter Max Vanhouttem, who’s dedicated to research at TNO on making plastic food packaging more circular. Max shows how we at TNO are investigating the best way to recycle plastic buckets that have contained, for example, mayonnaise or frying oil.
Why circular plastic food packaging?
‘The European Union wants to be climate neutral by 2050 at the latest. The transition to a circular economy can contribute significantly to meeting climate goals. To accelerate this transition, new rules have been developed for various sectors, including food packaging.
New European legislation states that by 2030, all food packaging must contain at least 10% recycled material, and by 2040, this must be 50%. We’re currently only at 0.5% for widely used PP and PE packaging, so there’s still a long way to go to meet the quota requirement. Food packaging producers are eager for solutions to meet the requirements. Unfortunately, it isn’t that easy.’
‘We’re studying the possibilities for recycling plastic buckets that have contained mayonnaise and frying oil. These packaging has little to no recycling value and these buckets are often incinerated.’
What makes it so difficult to develop circular plastic food packaging?
‘To make plastic packaging circular, we ultimately need to move away from fossil raw materials and make packaging from old packaging and/or from renewable materials. To achieve this, the quality of recyclate will have to be drastically improved, among other things.
In this project, we’re studying the possibilities of recycling plastic buckets that have contained mayonnaise and frying oil. We focus on this type of packaging in particular because it currently has little to no recycling value and these buckets are often incinerated.
Because the buckets are used in the food industry, you have to deal with especially strict requirements regarding hygiene and food safety. The problem is that fat residues soak into the plastic and you can never remove them 100%. This means that after each reuse, the plastic becomes increasingly saturated. If the percentage of old fat becomes too much at some point, you aren’t allowed to reuse the bucket.’
What does your work involve?
‘In this project, we’re investigating mechanical recycling. The buckets are recycled by chopping them into small pieces in our lab using a shredder and processing them into new buckets. In doing so, we try to find answers to various questions, such as: How much fat remains in the buckets? How many times can you recycle these buckets? What are the properties that determine whether the recyclate is still suitable for making new buckets?
Using models, we make calculations in advance and then test them in practice. It really is a hands-on research project, which is very time-consuming but in which we’re making steady progress. We aren’t doing this alone, but together with various partners in the value chain. The project involves the bucket manufacturer (Dijkstra Plastics), polymer supplier SABIC, and Milgro as logistics partner. We get the buckets from the hospitality industry.’
Arriving at the ideal ratio
‘It’s currently still hard to predict what effects contaminants, for example, have on your product. Ultimately, we want to accrue knowledge to find out the ideal ratio of recycled materials to new materials for producing these food buckets. That will enable us to deal with this kind of food packaging in a more environmentally conscious way, because we’ll use fewer petroleum-based raw materials and incinerate fewer materials. The knowledge we’re now gaining about these buckets can be applied to other food packaging in the future.’
‘To meet the European requirements for using recycled material in food packaging on time, we need to put a lot of momentum behind developments. This requires cooperation from all parties within the food packaging value chain, as well as starting this kind of case study. The time to wait and see is over,’ Max concludes.
Become a time setter at TNO
Would you like to work on innovations that you can really use to create the future? Then become a time setter at TNO like Max and make your mark on our time.
Get inspired
Biobased materials
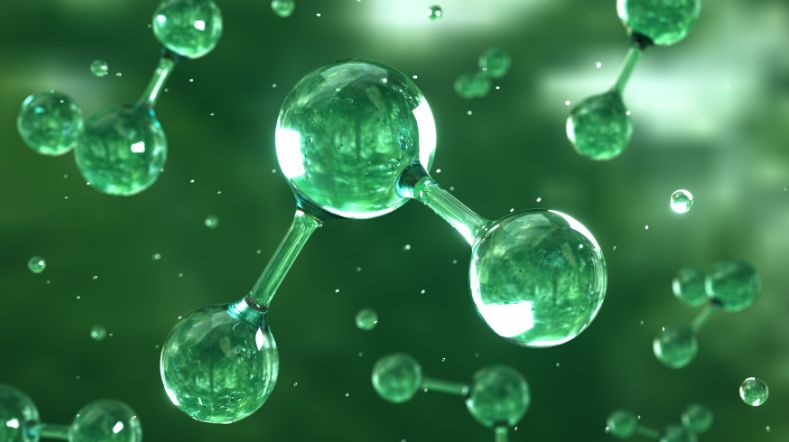
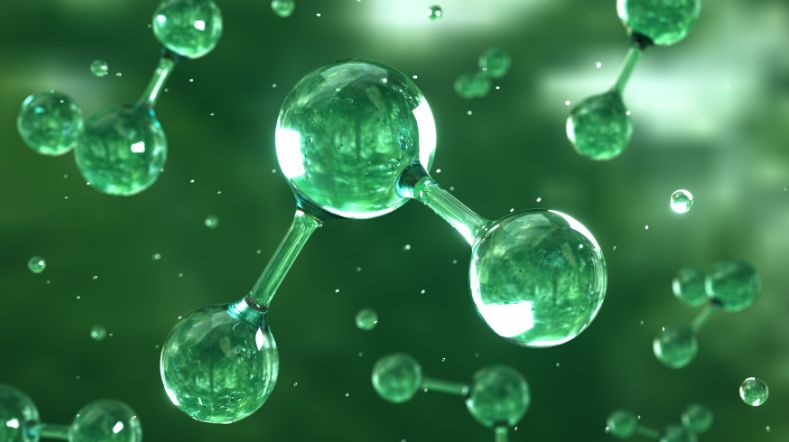
Enhanced solvolysis contributes to the future of composite recycling
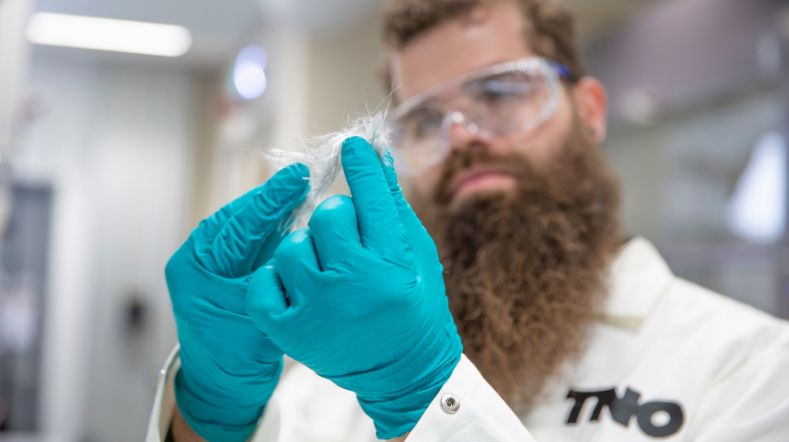
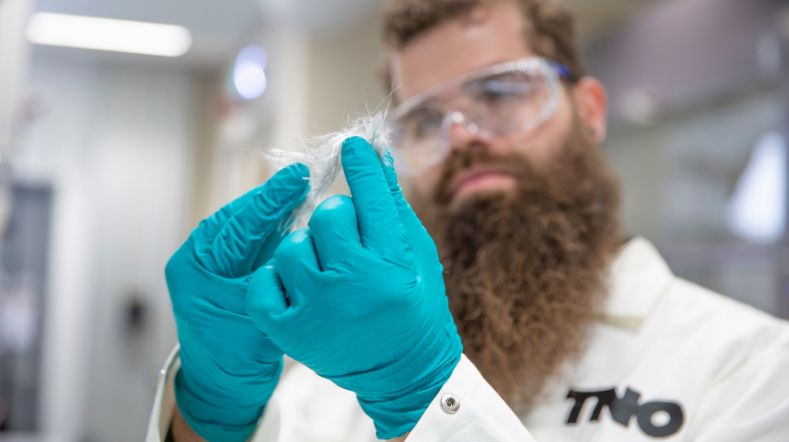
Collaboration for sustainability: better results through joint innovation
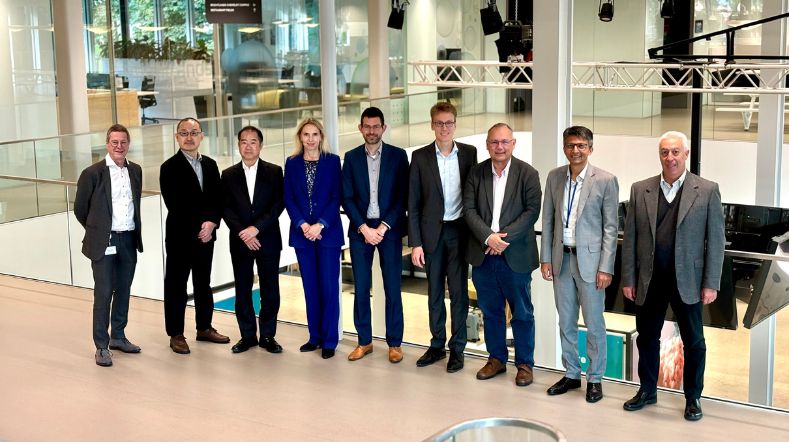
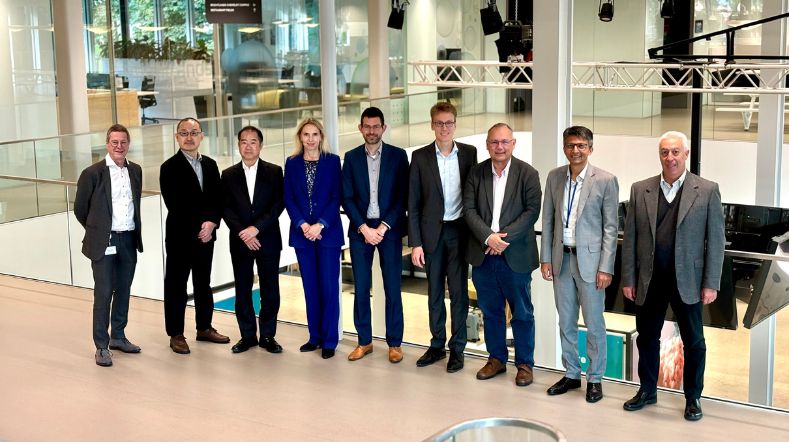
Webinar: Biobased plastics in a sustainable future
Biobased plastics
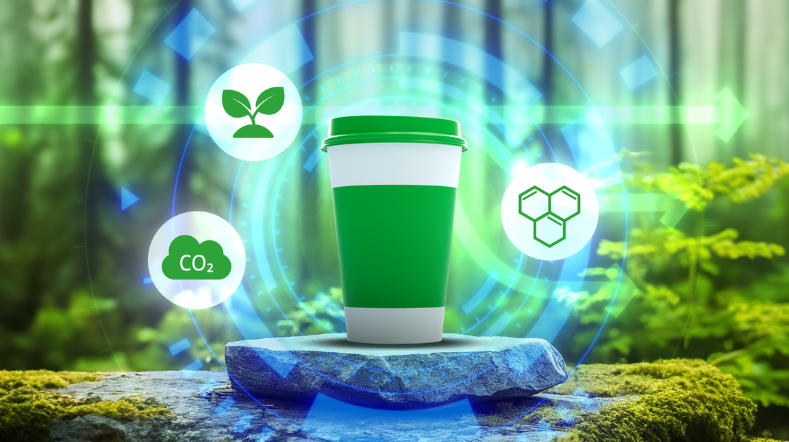
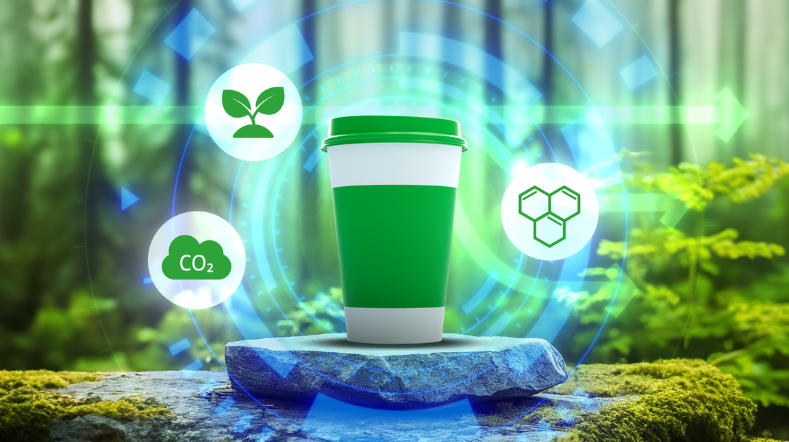