Is the race between protection and weight of Defence vehicles changing?
Military vehicles are subject to extreme requirements, given their function and application. But protecting occupants with ever thicker and heavier material is now hitting its limits. Armoured steel has traditionally been used to protect the occupants of Defence vehicles, but for the future, other materials are also being considered.
‘Supporting the armed forces with knowledge and innovation is one of our main tasks,’ says Mark, an employee at the Ministry of Defence, working in the Ground-Based Weapon Systems department. ‘In this role, we continuously explore new technologies that can improve our weapon systems in areas such as protection, mobility, and firepower. To give a practical example, this could mean better armour for a military vehicle, the ability to drive farther and faster, and the capacity to carry a larger cannon.’
‘If we want to achieve the mentioned improvements for a military vehicle, we can't go any further with steel constructions; we simply run into weight problems. The vehicles become too heavy due to the addition of more steel, making them no longer practical for field deployment and, legally, they are no longer allowed on public roads. Therefore, we are focusing our efforts on a different type of material that is lighter in weight and is already being used in various forms for safety applications such as bulletproof vests and doors.’
‘The development of these materials has been our focus for years, and we are now at the point where we may be able to use them for manufacturing parts of Defence vehicles. In this research, which is being conducted at a European level, TNO is one of the partners we are working with.’
What alternatives to steel are usable for Defence?
TNO experts Dennis van Veen and Lucas Amaral, who work in the Platform Protection and Advanced Materials (PPAM) department, are both involved in the study. ‘In our project, we are exploring possibilities of constructing parts for an armoured military vehicle weighing 10 to 13 tonnes using lightweight composite materials,’ says Van Veen, who has been working on the research for several years. 'The ultimate goal is to increase operational capability by reducing weight. The name of the study is L-AMPV, which stands for ‘Lightweight constructions for Armoured Multi-Purpose Vehicles.’
‘A composite is a material made up of different types of materials,’ Van Veen further explains. 'Combined, these materials provide properties that are better than those of the individual components. Often, composite refers to lightweight, fibre-reinforced plastics, such as those used for racing bicycles, but in fact, reinforced concrete is also a composite. In the L-AMPV project, we are looking for a composite with properties such as high stiffness, impact resistance, and toughness. It must be lightweight yet as strong, if not stronger, than armoured steel, so that it can better protect our soldiers in combat situations.’
What phases have been completed so far in L-AMPV?
‘The first phase of the research was a feasibility study; we wanted to know in advance whether this project has a realistic chance of success before we invest more time and money into it. The result was positive, which led to the establishment of L-AMPV 2. The goal of this second phase was to investigate whether it is possible to create composite vehicle parts that meet the requirements set by the armed forces.’
‘In the collaborative project L-AMPV 2, research teams from various European countries focused on the possibilities of making a component for a military vehicle from lightweight composites,’ Amaral continues. ‘TNO conducted research on manufacturing a floor plate; the ‘underbelly’. The floor plate must be strong enough to provide protection against landmines in war zones, such as we have seen in Afghanistan, for example.’
‘We structured the research step by step. Based on the knowledge from the feasibility study, we first tested various composites on a small scale. Certain combinations were eliminated, and we continued with others. In each step, we first performed calculations and then progressed to testing with increasingly larger and more realistic elements.’
‘Ultimately, we tested a complete floor plate, onto which a casing was mounted that simulates the real dimensions, weight, and dynamics of an armoured vehicle. The casing contained sensors and cameras to gather as much information as possible about what happens inside the vehicle when it drives over something like a landmine. We succeeded in creating a lightweight floor plate that remains intact in the outlined situation. Some deformation occurs, but the occupants would be safe.’
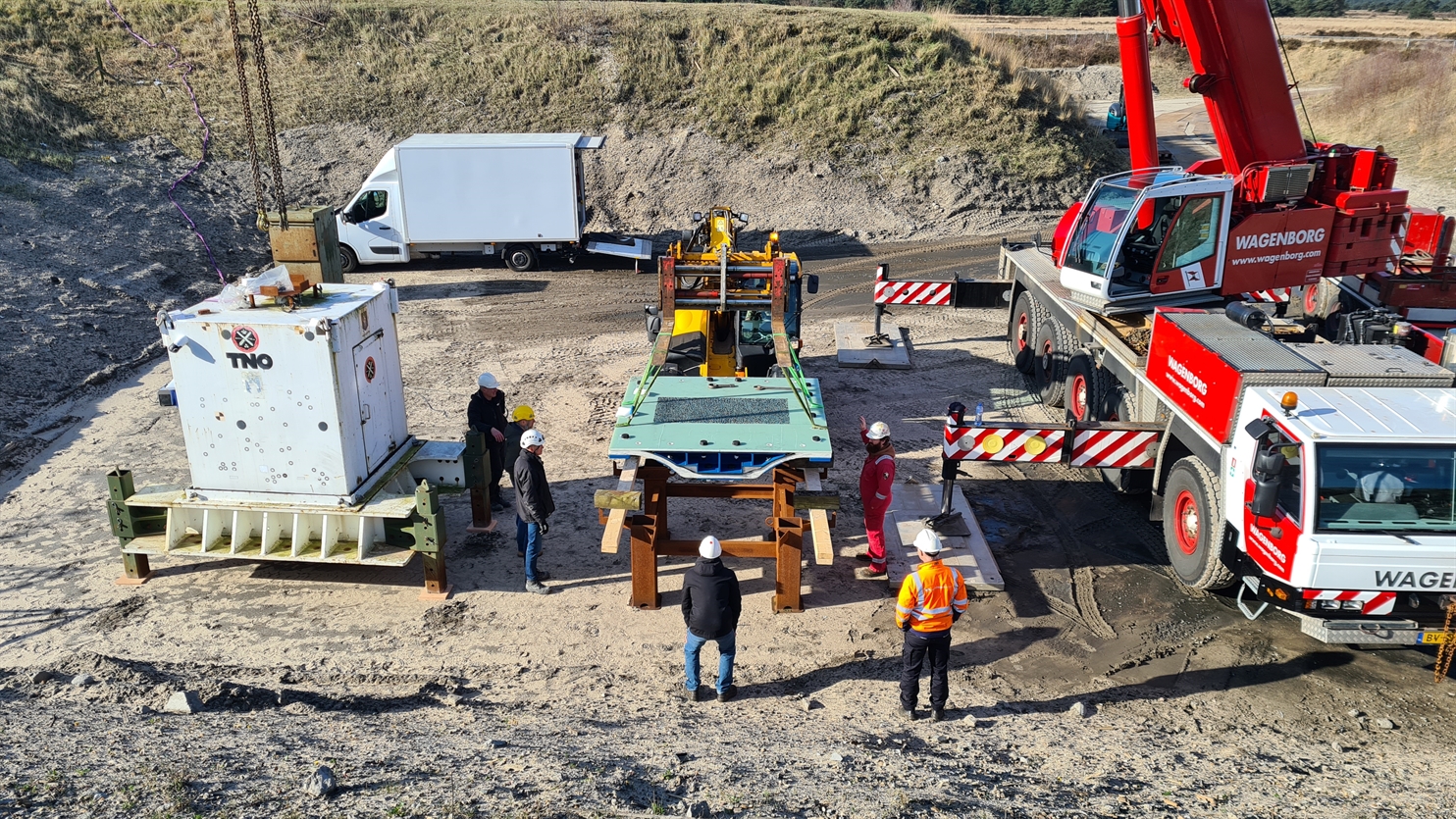
What are the costs of composite constructions?
‘A study like this is, of course, quite expensive, which is why we share the costs with our European partners,’ Mark explains. ‘However, when we look at what the eventual manufacturing and operational costs will be compared to the current steel-armoured vehicles, there is significant potential for savings.
Manufacturing costs will be lower, among other reasons, because lightweight parts are simply easier to handle. Additionally, various shapes and designs can be realised much more simply and thus more economically, as composite materials allow for the relatively easy creation of complex shapes that would not be possible with steel. Moreover, the key raw materials are readily available locally. This means we are less vulnerable regarding the supply of these materials in the event of escalating geopolitical tensions. Finally, maintenance and replacement costs are likely to be lower in practice, as composites simply do not rust. Of course, there is also significant potential for savings on fuel costs.’
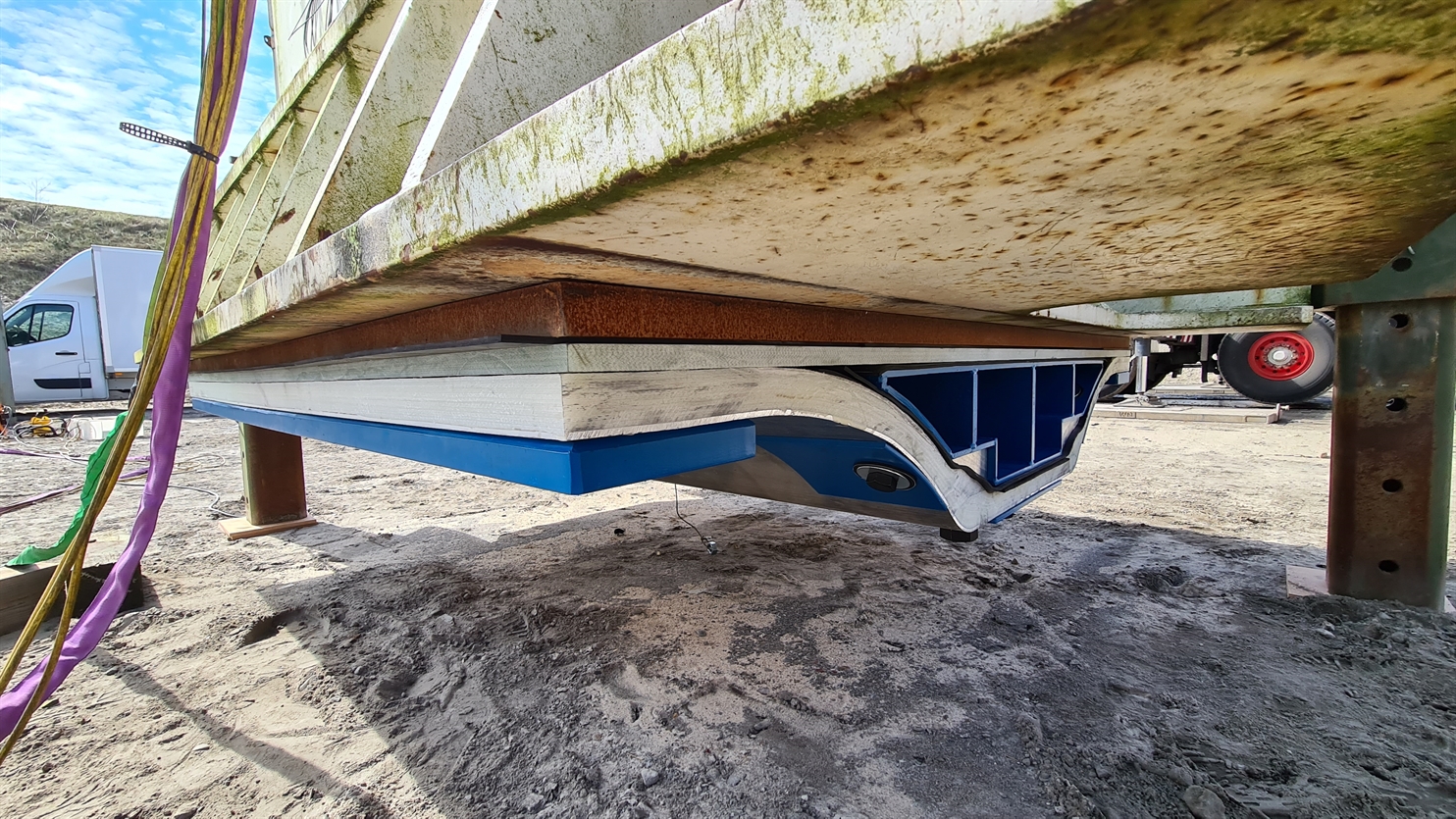
Get inspired
TNO’s Unit Defence, Safety & Security strengthens ties with South Korea
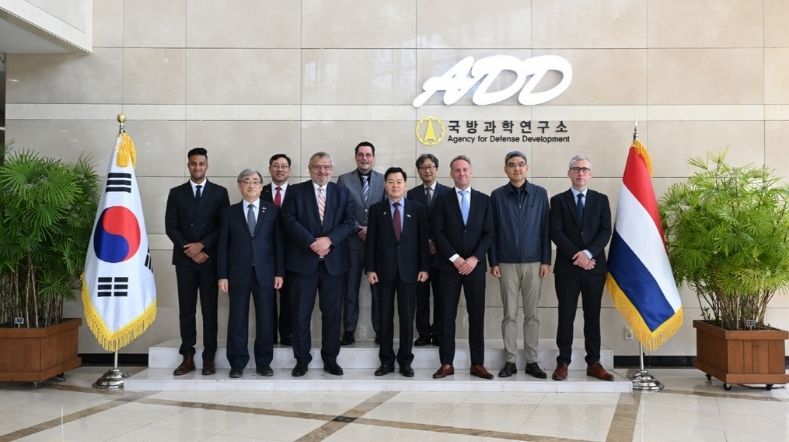
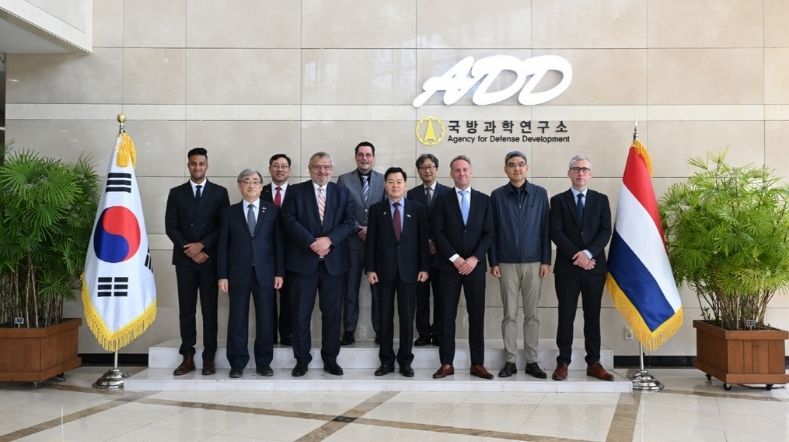
How the use of passive radars and satellite signals can detect and identify aerial threats
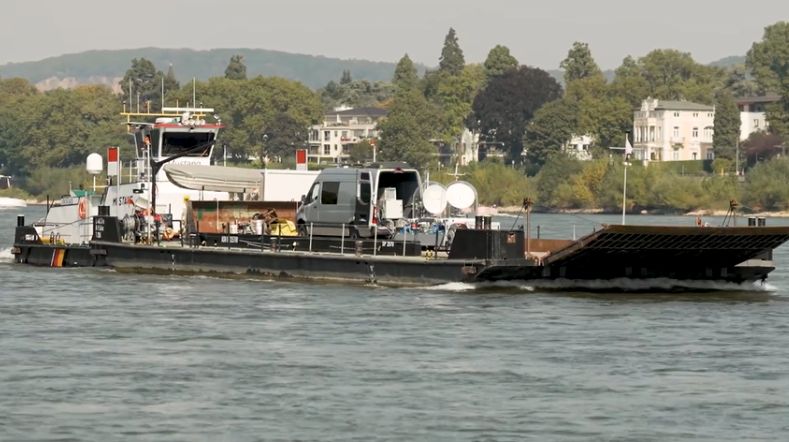
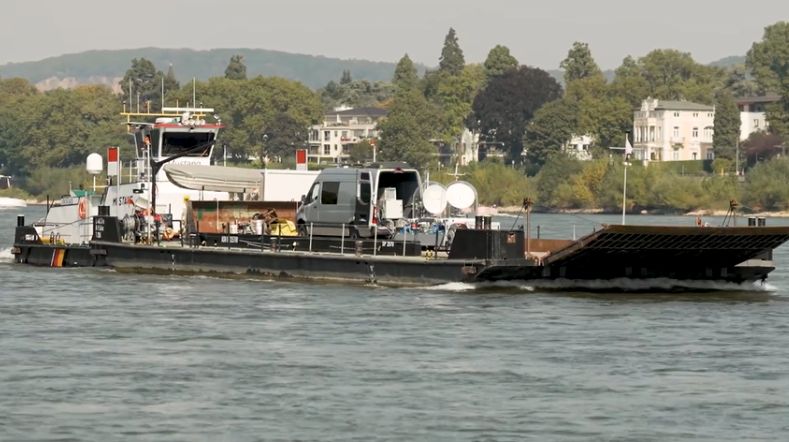
Responsible for safety: the crucial role of the range operator in bulletproof protection
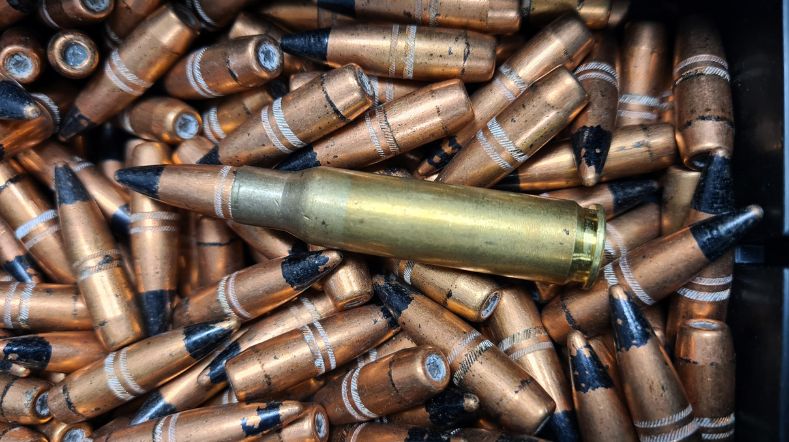
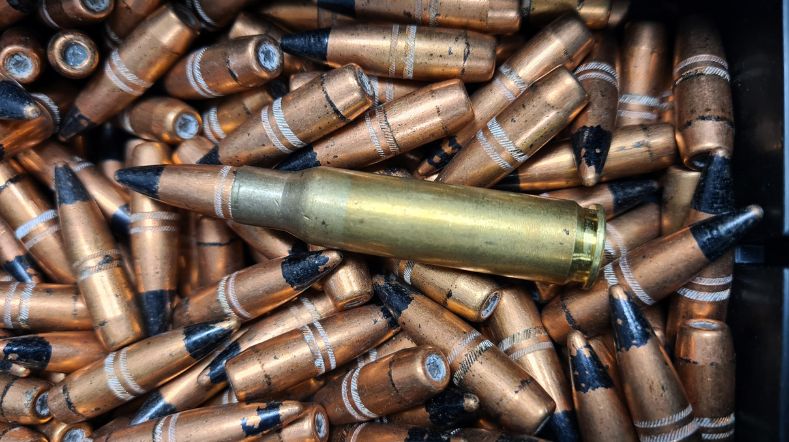
Prevent mild brain damage (mTBI) in the military? TNO is helping to build knowledge
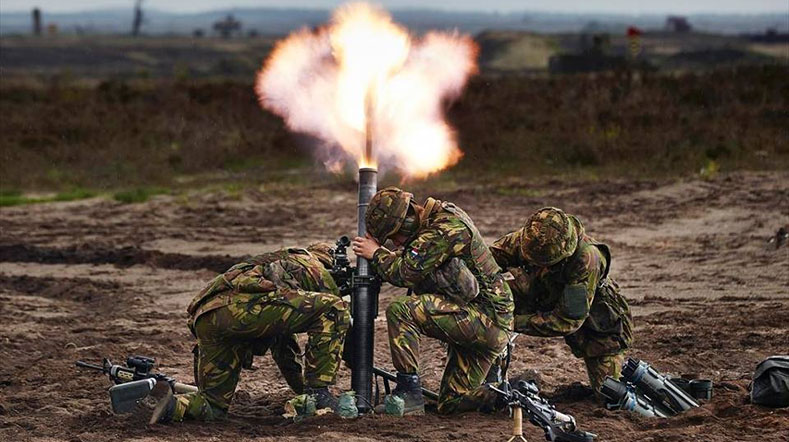
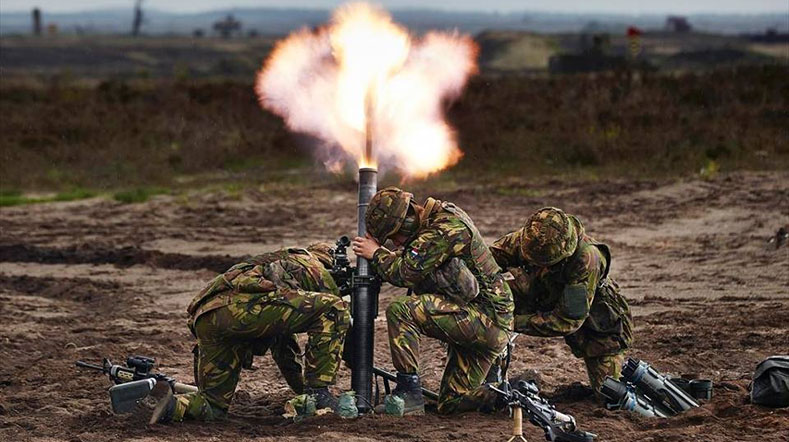
How does TNO help protect us from hypersonic weapons?
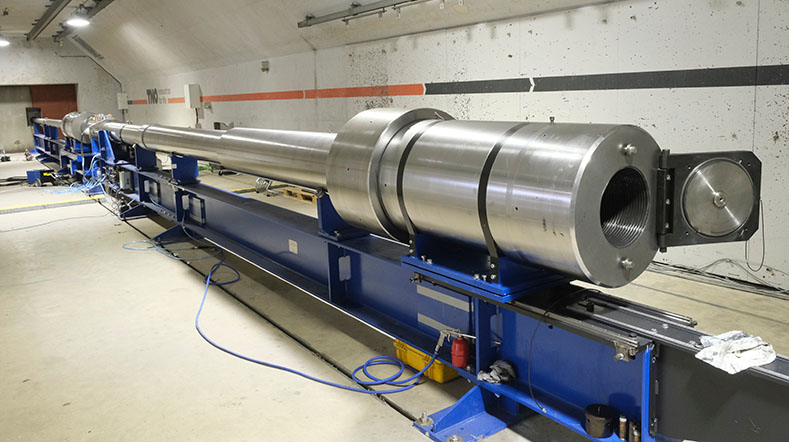
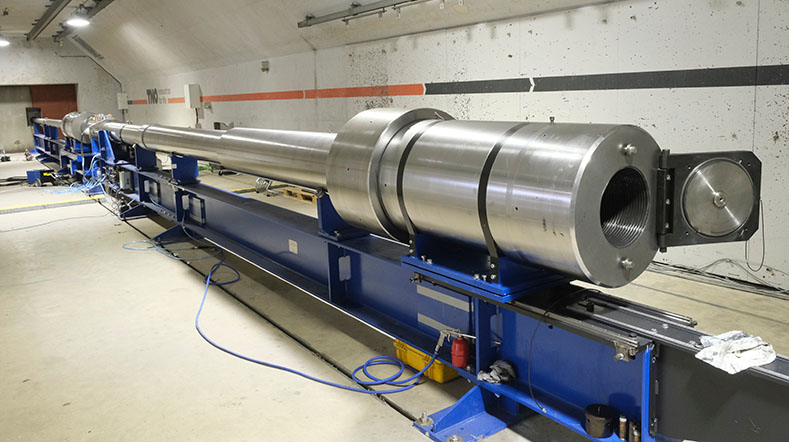
Goals for the Future
‘With the results of our research on the floor plate and the studies conducted elsewhere in Europe on composite doors and hatches, we hope to soon start L-AMPV 3,’ Amaral resumes. ‘The plans for this phase are still in the works, but logically we will focus on research to implement the components in real vehicles rather than working with models.’
‘Actual application in (military) practice is and remains the ultimate goal of all the research we conduct. It is essential that all parties stay on board because we need the industry’s support. An investment in this project will provide companies with valuable ‘know-how’ for creating composite products in the field of safety, and sectors like European yacht building and the automotive industry can also benefit from it.’