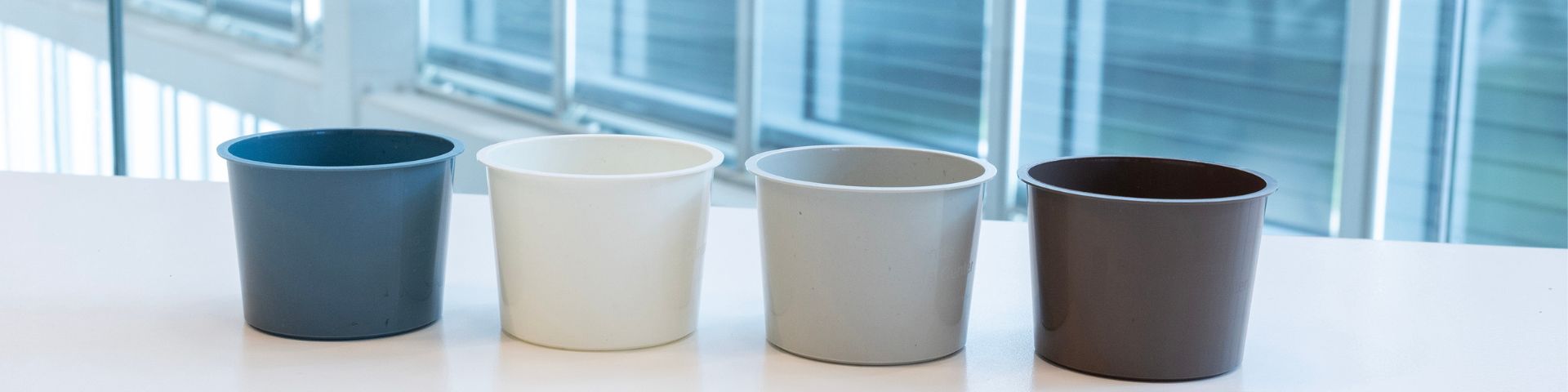
Recycling household waste: upgrading recyclates for seamless integration into manufacturing of plastic products
We all want to recycle more plastic. But how do we ensure that household waste re-entering the production chain is just as good as virgin plastic straight from the factory? TNO and partners are pioneering new ways to upgrade the quality of plastics recyclates so that they integrate seamlessly into existing manufacturing processes.
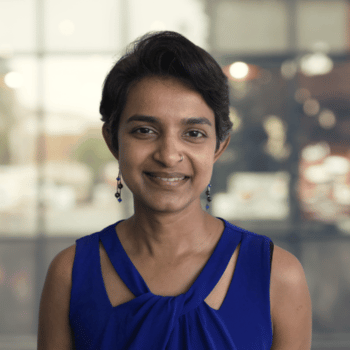
‘Household waste is never consistent. As a result, manufacturers may still prefer to use new plastic.’
Inconsistent recyclates are holding back the transition to circular plastic production
Speed is of the essence in manufacturing, explains TNO circular packaging scientist Nithya Subramanian. ‘If I’m somebody with a factory making plastic buckets, for example, what I want is consistency in the feedstock so that it can be processed without slowing down current operations.’
‘But household waste is never consistent, because there are so many variations in its composition. As a result, the recyclates made from this waste can also be variable. That variability means that I don’t know what settings to put in my machine to ensure that my buckets are always the same.’
As a result, manufacturers may still prefer to use new plastic, even when recyclates are technically a viable (and more sustainable) alternative. ‘We need to demonstrate that recyclate inclusion is feasible even in high-value applications such as thin-walled packaging, which currently need very specific polymer types.’
TNO's method for superior recyclates inclusion
The secret to greater consistency, Subramanian says, is good sorting of the raw waste material before it is recycled, then finding the right additives for the recyclate to ensure that the machinery needs minimal adjustment for each incoming feedstock batch.
‘We make different compounds of recycled polypropylene through colour sorting and additivation, and assess their properties. Then we process the recyclates into different injection-moulded parts. In the sorting we really narrow down the waste material so that we only allow in a specific type of plastic or even a specific colour. If it’s only white, then our product stays white until the end.’
But the real challenge lies in identifying the right mix of additives. Not only is every batch of recycled polypropylene (rPP) feedstock different, but the chemicals added to them perform a variety of functions. ‘Some additives are stabilisers to prevent the plastic from breaking down,’ says Subramanian. ‘Some additives help the material flow better, so that mixing and processing are more efficient. Others protect against UV light, et cetera.’
The additives themselves are not novel – Subramanian and her colleagues take advice from chemical compounding experts on ‘what it would make sense to add’ – but finding the best “recipe” each time is where TNO’s scientific expertise comes into play. Lab testing and pilots at an actual manufacturing facility reveal which mixes of recyclate and addtives are indeed processable and can be integrated successfully into existing production chains without slowing them down.
‘In addition, we have now demonstrated that recyclate inclusion is feasible in high-value applications such as thin-walled packaging. That needs very specific polymer types, as the proportions of additives to recyclate have to be very precise.’
Ensuring food safety is the next challenge
‘However, we’ve found some interesting things about the build-up of additives, which could be problematic to food safety. Right now, these recyclate based feedstocks are suitable for application in outer packaging, for example, and for different injection-moulded parts. For plant holders such as housewares, shampoo bottles, cleaning agent bottles and so on. But they are not yet suitable to make plastics that come directly into contact with food. That is what we will be investigating in the future.
To me, this is our next priority: how do we ensure that we can take food packaging waste and recycle it back into food packaging applications in a safe way – (like as we do with PET bottles) this technology can be made safe for food? Because without that, there is no circularity. Personally, too, I find that a nice challenge.’
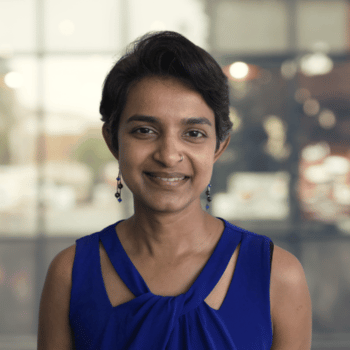
‘In this project we’re trying to bring all those things together. We’re doing technical work but also making recyclates more competitive in the marketplace by upgrading their quality.’
Break barriers
Based at Brightlands Materials Centre in Geleen, Subramanian is a TNO scientist specialising in circular packaging. She is currently involved in the Design for Recycling work package of Syschemiq, a 4-year regional Horizon Europe-backed programme to speed up the circular economy through improved and more efficient plastics recycling. As well as improving rPP feedstock sorting and pretreatment, through Syschemiq stakeholders across the value chain are being challenged to overcome technical and non-technical barriers to a circular plastics economy. From better product design to smarter waste separation by consumers and collection by local authorities.
Subramanian hopes that this concerted approach within Syschemiq will have a real impact. ‘People often ask why we don’t recycle more. Well, we should be able to but sometimes there are technical challenges. What we also need, though, is incentivisation from government and initiative from manufacturers.
In this project we’re trying to bring all those things together. We’re doing technical work but also making recyclates more competitive in the marketplace by upgrading their quality, so that hopefully they become more widely available for higher value applications.’
Would you like to add more consistent recycled content to your packaging without slowing down your manufacturing?