
23 questions about biobased plastics in a sustainable society
Biobased plastics are a promising step towards a more sustainable future. But what exactly are biobased plastics? How do they differ from traditional plastics, and what environmental benefits do they offer? In this article, our TNO experts answer the most frequently asked questions about biobased plastics, their applications, and their role in the material transition. Discover how these innovative materials can contribute to a sustainable society.
Basic information and definitions
Biobased plastics are plastics that are made entirely or partially from biological resources such as sustainably grown biomass and bio-waste. Examples include bio-polyethylene from sugarcane or corn and PLA from plant sugar.
Biodegradable plastics can be broken down by microorganisms into water, carbon dioxide (or methane), and biomass under specific conditions. A common misconception is that biobased plastics are always biodegradable or compostable, but non-biodegradable durable biobased plastics also exist.
For instance, a chemical coating for housing might be biobased but not biodegradable, whereas food packaging materials like tea bags and coffee cups would benefit from being biodegradable.
Biobased plastics can be produced in different ways, namely as 'drop-in' biobased plastics and 'new biobased alternatives':
- ‘Drop-in’ biobased plastics are plastics where biomass, material from plant or animal origin, is used to create the same chemical building blocks and polymers currently derived from fossil fuels. The production process is similar, apart from the feedstock preparation, and the resulting plastics are identical to existing materials.
- A ‘novel biobased alternative’ is a biobased polymer with a different chemical structure but similar or better properties, fulfilling the same function as existing fossil-based plastics. Note that the term ‘novel’ is optional, as some biobased polymers, like PLA, were discovered as early as 1920.
CO2-based plastics use captured CO2 (combined with green hydrogen) to create the same chemical building blocks and polymers currently derived from fossil fuels, making it a drop-in pathway. Like synthetic fuels, polymers from CO2 are sometimes called ‘synthetic’ or ‘syn-’ polymers.
In a mass balance approach, biobased feedstocks (e.g., bio-naphtha or bio-methanol derived from biomass) are introduced into conventional petrochemical production processes, often mixed with fossil-based feedstocks. Since these inputs are blended at an early stage, it is not physically possible to separate the biobased components in the final product. Instead, the share of biobased content is accounted for and allocated to specific products via a certified chain of custody system.
The pathway comparison framework presented in the whitepaper ‘Pathways to sustainable plastics’ does not consider fossil feedstocks as a pathway. The mass balanced share of a final product that is produced from biomass would follow a ‘drop-in biobased’ route in the comparison. Mass balancing is thereby considered in the framework for only that share that is biobased. Sustainability impact results would have to be attributed to the products in proportion.
Sustainability and environmental impact
Biobased plastics are expected to play a significant role in global plastic sustainability. Using biomass, a renewable carbon source, for plastics can help mitigate greenhouse gas emissions and, under certain conditions, act as a carbon sink when integrated into durable products.
Determining the best mix of renewable carbon (biomass and CO2) for sustainable plastic production is challenging. Not every renewable carbon application is automatically the most sustainable, but fossil fuel-based production is not sustainable. The share of biobased plastics in a fully non-fossil plastics system is difficult to predict due to dependencies on regulation, approval, adoption, and matching the right feedstocks and conversion technologies with the right products and applications in the right locations.
The 3-step plan presented in the whitepaper ‘Pathways to sustainable plastics’ allows users to compare renewable carbon-based options for plastics for specific applications, identifying where biobased plastics are best used and unlocking opportunities for them.
Recycling plays a significant role in achieving plastic sustainability. It effectively uses plastic waste feedstock, conserving resources. Both mechanical and advanced recycling should be maximised.
However, even if global recycling rates reach their theoretical maximum, only about 60-70% of total volumes can be produced from recycled plastic feedstock.
This estimation accounts for losses during production, usage, collection, biodegradation, and recycling process yield losses. Thus, significant sustainable virgin plastic production will still be required to replace losses and meet growing demand.
A small proportion can be replaced by natural biopolymers such as cellulose, starch, and their derivatives. The production of biobased plastics from biomass and CO2 can help bridge the gap between the amount of recycled plastic and the total demand for plastic. They are the only remaining options for the sustainable production of new plastic and play an important role in the transition to a more sustainable and circular plastic system.
The sustainability of biobased plastics has been debated among experts. They are diverse and can be used for nearly all existing plastic applications. Using biomass as a feedstock for plastics holds promise in reducing greenhouse gas emissions and, under specific conditions, can act as a carbon sink in durable products.
Considerations around biomass use for plastics include competition with feed/food for first-generation feedstocks, land use changes, water use, biodiversity impact, collection and logistics complexity, and competition from fuels and energy. It is crucial that the feedstock is sourced sustainably and that the full life cycle of these plastics is examined to ensure benefits beyond reducing fossil feedstock use
A variety of biomass types can be utilised to produce bioplastics. Typically, biomass feedstock is categorised into first, second, and third generation feedstocks:
- The first generation biomass includes readily fermentable sugars from edible polysaccharide sources (e.g., maize, sugarcane) and edible (vegetable) oils. The use of first-generation biomass remains a topic of debate, primarily due to ethical concerns regarding competition for food resources and changes in land use. However, some studies suggest that sustainable co-production of biomass for both food and materials is feasible.
- The second generation biomass consists of non-edible biowastes such as agricultural and food waste (e.g., non-edible oils, forest residues, agricultural residues, organic waste). Second generation biomass provides a less contentious, more affordable, and widely available feedstock for bioplastics, although it does come with the challenges of complexity and the need for additional pre-treatments.
- The third generation biomass refers to novel biomass feedstocks being explored for use, such as algae. For the global use cases in this whitepaper, all biomass types are currently included, with an emphasis on the importance of focusing on second- and third-generation feedstocks for bioplastics production.
Microplastics are formed during degradation of plastics in use or end-of-life (e.g. tire-wear, road marking paint, textile). The current portfolio of fossil-based plastics is notorious for generating microplastics. Using biomass to produce durable ‘drop-in’ biobased polymers (like bio-PET or bio-PE) will not solve this problem. Hence, to address this issue, biomass should be used to produce biodegradable polymers like PLA, PHA, PBAT. Such polymers typically break down more completely under the right conditions, resulting in a lower overall microplastic burden.
The challenge of microplastics is a broad challenge of the plastics industry. To tackle this challenge, a holistic approach is needed. It involves material innovation, regulatory standards, and improved waste management. For example eco-design principles that optimize controlled degradation could be applied in novel biobased polymer design.
Finally, the Safe and Sustainable by Design (SSbD) approach encourages materials that are not only functional but also non-toxic and environmentally benign throughout their life cycle. While microplastic formation remains an issue, biobased biodegradable polymers, combined with smart design and recycling infrastructure, may offer an improvement compared to fossil-based plastics.
Regulations on biobased polymers vary globally, with the EU leading through frameworks like the Renewable Energy Directive (RED II) and the Single-Use Plastics Directive, promoting biobased content and sustainability claims.
- The European Commission’s ‘Sustainable Carbon Cycles’ strategy sets an aspirational target for at least 20% of carbon in chemical and plastic products to come from sustainable non-fossil sources by 2030, with strict sustainability criteria for biomass use.
- The Netherlands is advancing with the Nationale Circulaire Plastic Norm (2027), introducing recycled and biobased polymer obligations. In the US, a market-driven approach is reinforced by the USDA BioPreferred Program, while the country aims to meet 30% of its chemical demand through sustainable biomanufacturing within 20 years.
- China mandates biodegradable plastics in certain packaging applications and has set production targets for specific biopolymers.
- Japan and South Korea support voluntary certification schemes, such as Japan’s Biomass Mark.
These regulations differ in biobased content thresholds, certification requirements, and sustainability criteria, creating a diverse and evolving global regulatory landscape.
Separation and recycling of biobased and CO₂-based polymers require a design-for-recycling approach to ensure compatibility with existing recycling streams. Many biobased polymers, like bio-PET and bio-PE, are chemically identical to their fossil-based counterparts and can be recycled together. However, novel materials such as PLA or PHA may require separate collection and dedicated recycling processes to avoid contamination.
To enhance recyclability, a platform chemical approach—where biobased and CO₂-based polymers are designed to break down into valuable monomers or feedstocks—can support closed-loop systems. Innovations in chemical recycling and advanced sorting technologies, with AI-supported spectroscopic techniques beyond NIR (near-infra red), can further optimize separation. Standardizing labeling and integrating biobased polymers into established mechanical and chemical recycling streams will be crucial for a circular system.
The choice between drop-in vs. novel biobased polymers is a complex discussion with trade-offs between functionality, compatibility, and system-wide impacts. Drop-in biobased polymers, such as bio-PET or bio-PE, are chemically identical to fossil-based plastics and integrate seamlessly into existing production and recycling infrastructure, minimizing adoption barriers.
However, they do not offer significant new functionalities, such as enhanced biodegradability. Moreover, in view of the so-called conversion factors of biomass into platform chemicals – as precursors to polymers, drop-in polymers will require more feedstock compared to novel polymers produced from oxygenated platform chemicals.
On the long-term, with sufficient scale for novel biobased polymers, these will become more cost-effective than drop-in polymers. Additionally, novel biobased alternatives, like PLA or PHA, provide opportunities for improved properties, including end-of-life (EOL) biodegradability, but face challenges in scalability, regulatory acceptance, and recycling compatibility.
Their adoption follows a chicken-and-egg problem, where limited supply and infrastructure hinder widespread use. A fact-based comparison of sustainability and economic feasibility is essential to determine the best applications for each approach. On a system level, considerations like practicality, regulation, and availability of recycling infrastructure must be evaluated.
To enhance circularity, recyclability, biodegradability, and overall system complexity should guide material selection. A key step in future material development is to limit the number of unique monomers (platform chemicals) to simplify processing and improve efficiency in recycling and reuse.
The availability of green hydrogen and renewable electricity is currently insufficient for CO2-based polymers to play a significant role, this will inevitably change as a result of the ongoing energy transition globally. This might lead to a share of CO2-based polymers of 10-20% of the future plastic demand in 2050 (roughly 1000 Mt).
The feasibility of CO2-based polymers indeed highly depends on the availability of green hydrogen and renewable energy, since the conversion of CO2 into products is an energy-intensive process. The availability of CO2 itself is less of an issue, with estimates on global availability of captured CO2 in the order of 5,500 Mt, the majority originating from point sources.
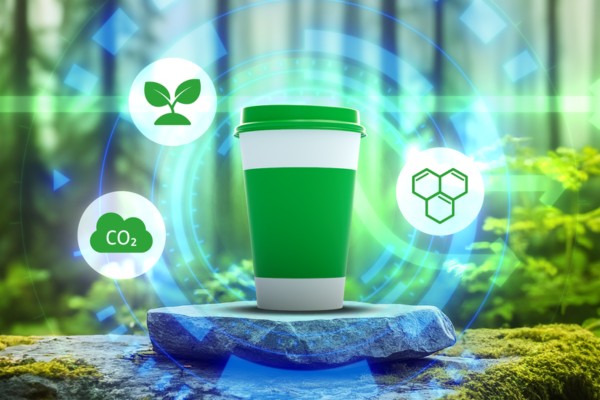
Want to know more?
Download our latest whitepaper to explore the pathways to sustainable plastics and watch our webinar from 11 March 2025 on demand for exclusive insights and expert discussions.
Application and implementation of TNO’s 3-step plan towards more biobased plastic
It is inevitable that we will continue to produce new plastic. To do this in a sustainable way, we must replace fossil carbon as a raw material with renewable (CO2 or biobased) carbon. This may seem simple, but the choice between sustainable alternatives is complex.
TNO has developed a 3-step plan towards biobased plastics, which helps companies choose the best path to a sustainable alternative. This supports companies in selecting the most sustainable and economically viable option.
Plastics serve various functions in society across different applications, ranging from long-lasting construction materials to single-use packaging and mixed waste.
Currently, these functions are fulfilled by 9 common (fossil) polymer materials, which account for 80-90% of today’s global plastic volume:
- LDPE (Low-density polyethylene);
- HDPE (High-density polyethylene);
- PP (Polypropylene);
- PS (Polystyrene);
- PVC (Polyvinyl chloride);
- PET (Polyethylene terephthalate);
- PUR (Polyurethane);
- PA (Polyamide);
- ABS (Acrylonitrile Butadiene Styrene).
The 3-step plan presented in the whitepaper can be applied to all these materials to create a systemic view of pathways to sustainable plastics. Additionally, it is possible to add a polymer material when relevant.
The 3-step plan can be applied to your situation. For industry players, this enables the determination of the best pathway for renewable carbon-based production and material selection for your products.
The whitepaper presents the application of the 3-step plan for four global use cases, showcasing how it works. By setting precise input parameters and defining constraints (such as biomass availability or supplier products), stakeholders like brand owners, polymer producers, and plastic compounders can make informed material choices.
The 3-step plan can be tailored to your situation, incorporating specific input parameters and constraints. It allows companies to assess the impact of potential changes in their production pathways, such as switching from first-generation to second-generation feedstock for the same biobased plastic material.
To specify a novel biobased alternative pathway, the first question is: ‘Which novel biobased alternative polymer can be applied here?’. TNO developed a method to compare the properties of (novel) biobased polymers with existing polymer products in various applications.
A list of over 1,000 potential novel biobased polymers was assessed and compared to existing fossil materials on five key properties: modulus, tensile strength, elongation at break, oxygen transmission rate, and impact strength.
Based on a match in properties, a novel biobased alternative is identified as a close substitute for a specific product application. Initial analysis shows that novel biobased polymer alternatives can potentially fulfil most existing applications, with at least a 90% match in properties. Where no suitable novel biobased alternative exists, biobased polymer design by machine learning could be applied.
The assessment procedure for matching properties of (novel) biobased alternative polymers with existing fossil-based polymers can easily be extended to include additional material or processing properties. This is especially important since replacing a fossil-based polymer with a novel polymer requires modifications in processing conditions or even the purchase of specialized equipment. To design for processability and compatibility with existing production equipment, the following properties should be included in the search algorithm described above: melting point, glass transition temperature, melt flow index, and thermal stability.
The search algorithm is developed such that these adjustments can be made fairly easy. Furthermore, weighting factors have been included to put emphasis on certain properties, these can be finetuned for each specific application. The so-called quality threshold of 90% can be adjusted as well on the application level. This is important because some plastics are overengineered, while others require an even more stringent approach (e.g. specialty applications).
The resulting best pathway from the framework assessments will need to be validated in various consecutive steps, one of them being testing actual production processes (at lab and pilot scale) like extrusion, injection molding or film blowing. It is reassuring that most of the novel biobased polymers are polycondensates or polyesters in particular and could be produced using obsolete facilities for PET-production.
Yes, to compare pathways on environmental sustainability, a sustainability impact assessment tool was developed, combining Material Flow Analysis (MFA) and LCA inventories. Environmental sustainability impact includes multiple indicators such as global warming potential, cumulative energy demand, land use, water depletion, and feedstock input required. It is important to include indicators beyond CO2 emissions, as biomass production for plastics can significantly impact water use and biodiversity.
The 3-step plan provides an approach applicable to various scopes. It can incorporate specific situations or potential future scenarios in terms of production processes, technology, or energy/feedstock inputs. It offers a robust tool for assessing the impact of technical advancements on the plastics production system.
As new production pathways for biobased or synthetic polymers emerge or are refined, the 3-step plan allows for immediate assessment and comparison with existing alternatives. It also highlights non-viable or less sustainable pathways, providing insights into areas needing innovation. The 3-step plan can evaluate the impact of technological developments or novel innovations within specific production steps, analysing different technological scenarios like learning curves, yield improvements, and future energy mix assumptions.
Applying the 3-step plan to all major plastic products in the global plastics system can determine optimised pathways towards a sustainable circular plastics system. This approach enables stakeholders to identify the most suitable renewable carbon-based production pathway for each plastic type and application, providing clear guidance on necessary decisions and actions.
Compiling the results allows users to draw conclusions on the overall share of biobased versus CO2-based plastics and identify product applications where bioplastics make the most sense, unlocking market opportunities.
TNO’s 3-step plan supports industry players and policymakers in transitioning to renewable carbon-based plastics by finding the most sustainable and economically feasible solution for their products.
Practically, we will work together through the three steps of the 3-step plan for your situation during a project. We will discuss and agree on parameters, biomass types, technologies, and materials to include or exclude, and iteratively optimise the value chains to be compared.
We will also determine constraints and relevant scenarios to advise on the optimal pathway for your products.
The framework as presented in the whitepaper was developed under the assumption that the pathway of recycling is maximized, reaching 60-70% circularity by 2050. Although ambitious, this is much needed given the constraints on availability of renewable carbons (biomass and CO2) and renewable electricity (hydrogen, to convert the CO2 into platform chemicals).
For the 30-40% losses (from waste mismanagement, recycling, degradation, etc.), virgin plastics are needed. The goal of this whitepaper was to find the best allocation of renewable carbon feedstocks for virgin plastic production. Therefore, initially the framework compares sustainable virgin production pathways only.
However, from a producer or off-taker perspective, recycled plastics are part of the option space. Generally, recycled plastics would score comparable in sustainability to the other options and are often slightly cheaper.
In further developing and applying the framework, TNO will include recycling pathways, based on TNO expertise on plastic recycling technologies. As such, organizations can compare recycling pathways with other pathways to sustainable plastics.
Get inspired
Collaboration for sustainability: better results through joint innovation
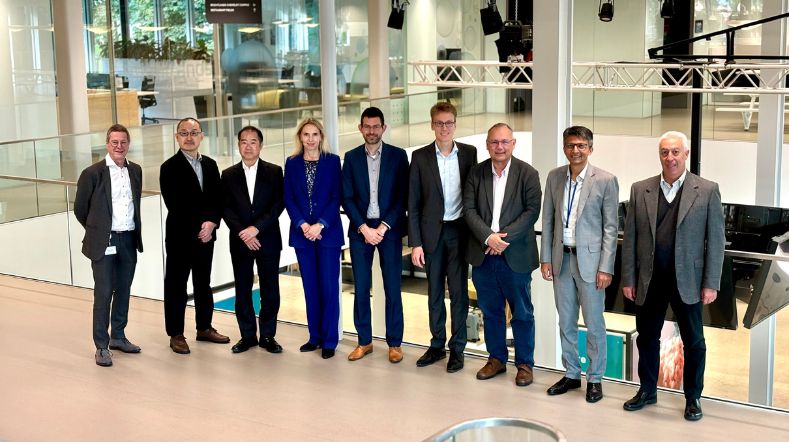
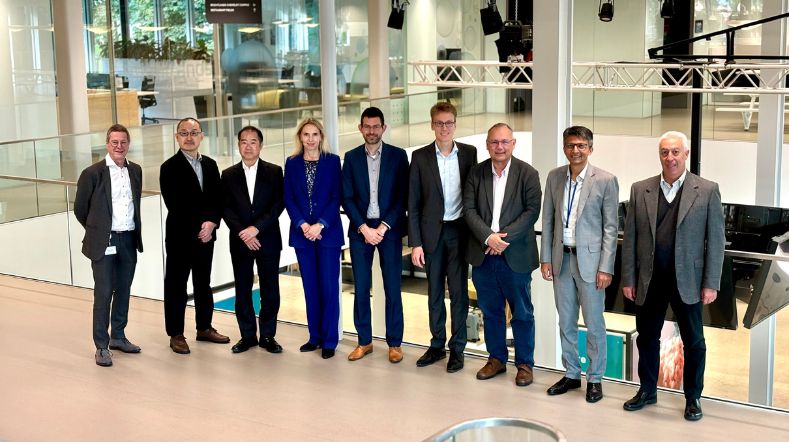
Webinar: Biobased plastics in a sustainable future
Biobased plastics
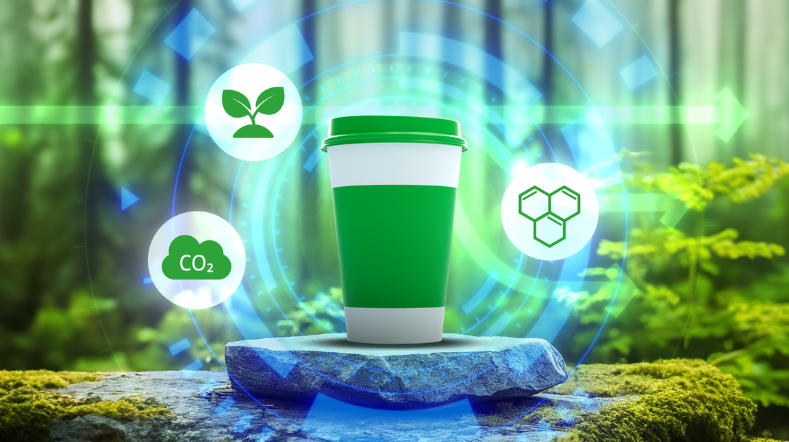
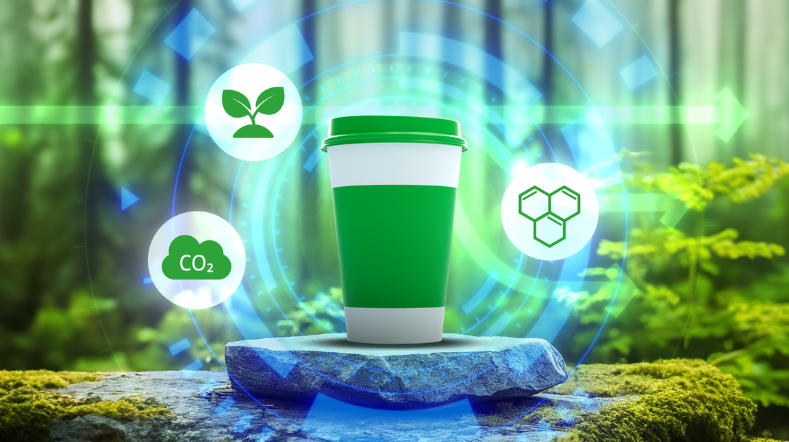
The challenge of choosing between sustainable materials for textiles
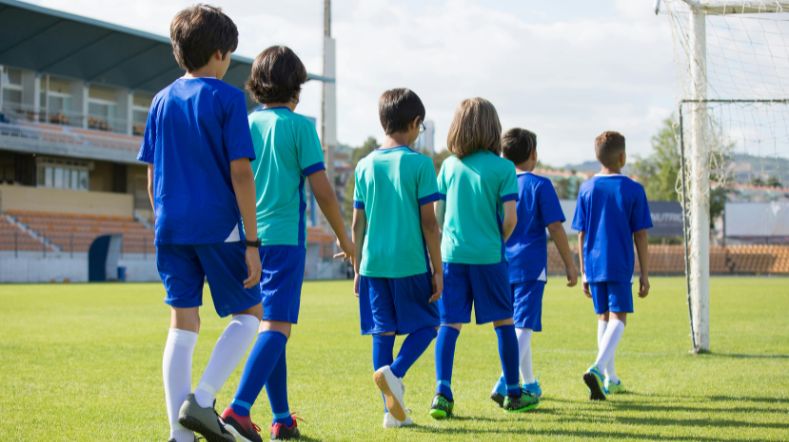
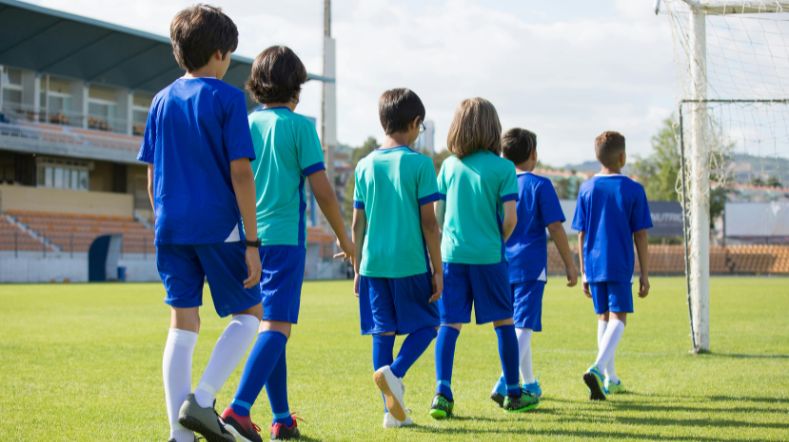
Working on biodegradable plastic
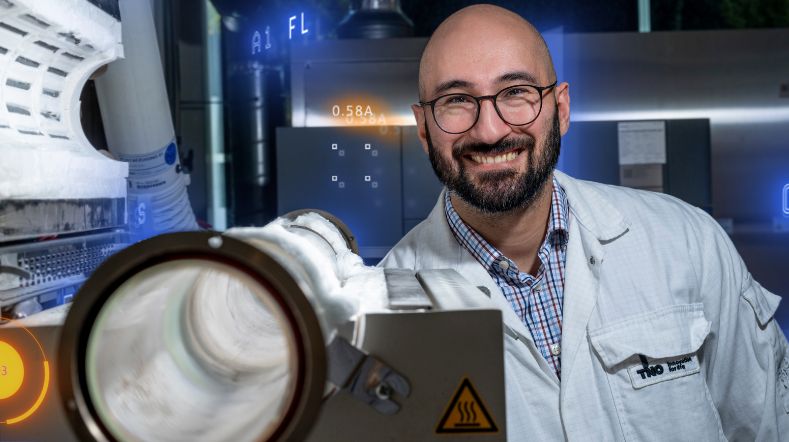
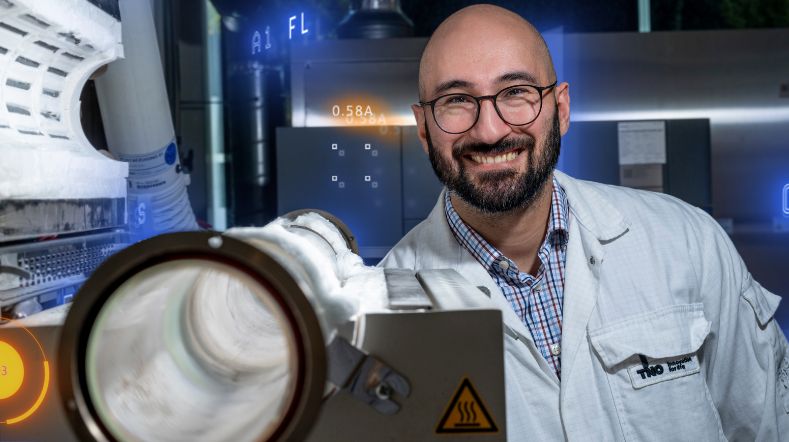