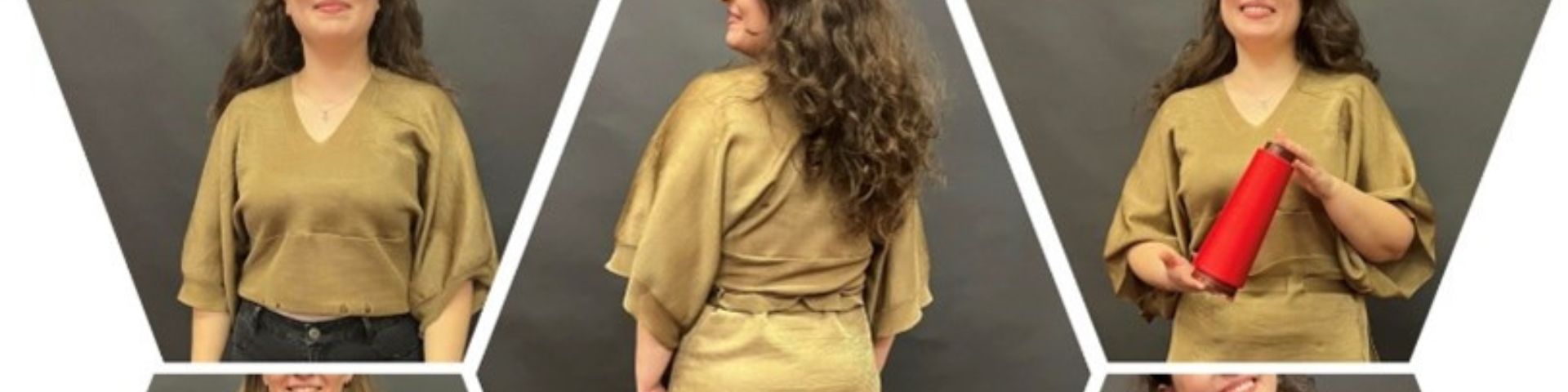
Local, circular, and biobased: towards the textile industry of the future with HEREWEAR
Clothing made from straw or seaweed sounds futuristic, but thanks to HEREWEAR, it might be hanging in your favorite clothing store sooner than you think. The European Horizon2020 project focused on making the entire textile chain more sustainable, from textile fiber to daily use. With this holistic approach, TNO and partners aim to contribute to a new EU economy for locally produced circular textiles and clothing made from biobased sources from waste. But how does it work?
Sustainability in textiles is urgently needed
When Jaap van Hal, senior consultant and innovation manager Biorefinery at TNO, joined HEREWEAR, he delved into the world of textiles for the first time. "It was shocking how much textile is wasted." Most clothing is produced in large quantities in low-wage countries. To be sold in Europe, this clothing then undergoes environmentally harmful transport.
Additionally, almost 90% of all clothing is made from polyester and cotton. Polyester is cheap and strong but oil-based, and cotton, although biological, has a high environmental impact, for example, due to the use of pesticides and a lot of water.
Finally, the textile sector is one of the largest producers of microplastics. These small plastic particles are released when washing and wearing clothes and eventually end up in our drinking water and bodies through the sea. Jaap: "It is unknown what the long-term effects of this will be."
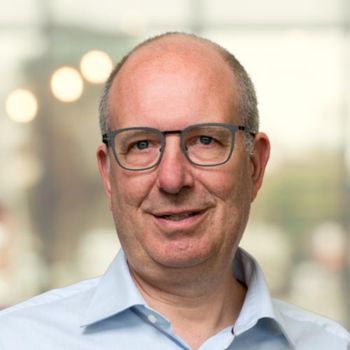
'From TNO, we bring our knowledge, innovations, and expertise in biorefining and recycling with the aim of accelerating the sustainability of the textile industry.'
From straw, manure, and seaweed to usable textiles
Together with the HEREWEAR consortium, TNO developed biobased alternatives for cotton and polyester in collaboration with 15 partners, including Centexbel (Belgian research centre for textiles and plastics) and DITF (German institute for textile and fibre research).
Jaap van Hal: "From TNO, we bring our knowledge, innovations, and expertise in biorefining and recycling with the aim of accelerating the sustainability of the textile industry."
The collaboration results in sustainable technologies for producing biobased textile fibers, for wet and melt spinning of biobased cellulose and biopolyesters (PLA), and for coating and coloring with biobased agents. The overarching process of textile production has been overhauled. Thus, waste products and waste are minimized, and the release of microplastics is drastically reduced.
New textiles from biological waste
One of the main results of HEREWEAR is new textile materials made from biological waste, such as seaweed, manure, and straw. To make textile fibers from these so-called "waste streams," TNO first cleans them using biorefining. They are then split using the FABIOLA process patented by TNO.
Jaap: "The FABIOLA process is a fractionation process. This means that, just like in an oil refinery - where gasoline is a fraction of crude oil - different fractions are extracted from the biomass." In the case of biological waste, these are cellulose, lignin, and hemicellulose. The "cellulose pulp" that remains after removing the remaining minerals can be spun into yarn.
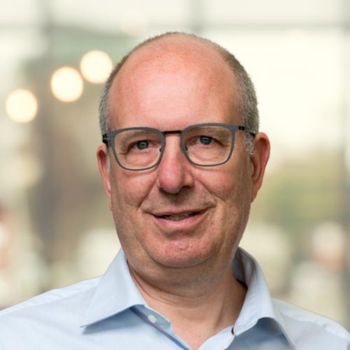
'The Flexi-Dress, the first dress made from sustainable straw, features a QR code that allows you to return the dress and have the textile reused.'
The Flexi-Dress: the first sustainable dress made from straw
The biobased textile is not inferior to conventional textile types and can be used for all kinds of clothing. For example, the Flexi-Dress, the dress with which the HEREWEAR project recently won the Cellulose Fiber Innovation of the Year Award 2024.
The fabric of the Flexi-Dress consists entirely of textile made from cellulose from straw. TNO made cellulose pulp from this, which was spun into yarn by DITF using the HighPerCell process. In this environmentally friendly process, the straw cellulose is dissolved in ionic liquids and spun into yarn using a special wet spinning process. The modular Flexi-Dress was made from the straw textile together with the German clothing brand Vretena.
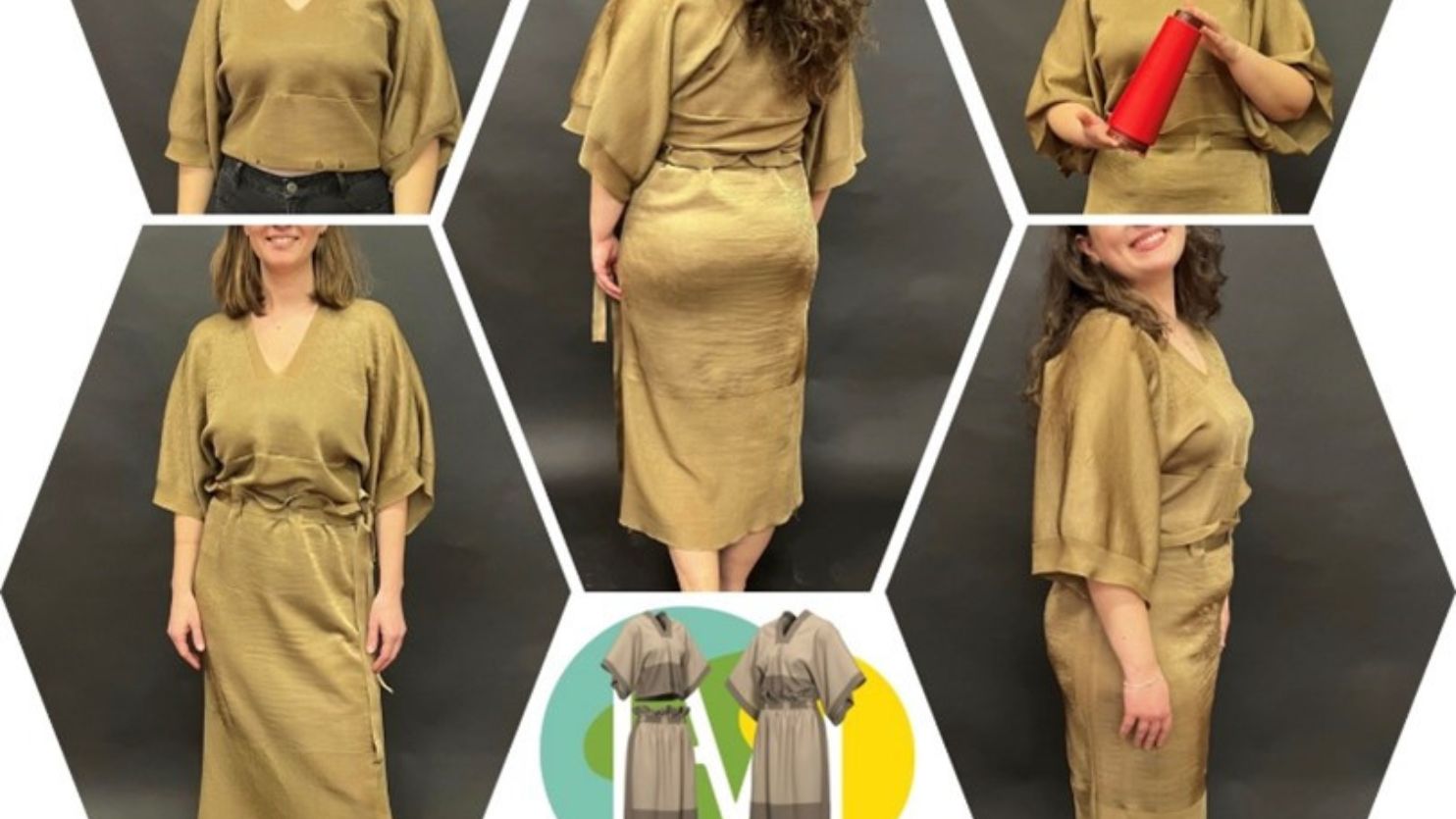
The Flexi-Dress is a good example of HEREWEAR's holistic approach. In making the dress, much attention was paid to the sustainability of both the product and the process, as well as the end user.
"You have many possibilities with the Flexi-Dress," says Jaap. "It can be worn as a dress or as a separate top and skirt, and the skirt can also be worn as a strapless dress." This way, the end user can enjoy the dress longer, as it is multiple garments in one.
Furthermore, Herewear developed digital prototypes to prevent waste, the dress was produced as much as possible in local European microfactory networks, and the rental or resale of the dress is facilitated in Vretena stores.
Jaap: "And there is also a QR code in the dress that allows you to return it if you no longer want it. The textile can then be returned to the raw material to make new filaments."
By joining forces, we make circular textiles possible
The results from HEREWEAR show that the holistic approach to locally produced circular textiles is being adopted by other parties in the textile industry.
Jaap: "To make the implementation of biobased textiles successful, it is essential, in addition to the development of innovations and technology, that all parties in the chain communicate with each other and all disciplines work together." "By interacting between technology, design, and the wishes of the end user, you increase the chance of success and impact," says van Hal.
Want to get started with sustainable textiles?
Parties that want to get started with circular textiles and clothing can turn to HEREWEAR. The project has made an extensive package of instructions, practical examples, and webinars available in the HEREWEAR Hub.
In this hub, interested parties can find each other, collaborate, and discover how to set up the value chain for biobased textiles step by step. For each step, it is described what needs to be done, how you can do it, and which parties you can talk to to get it done.
"Because applied science is all about teamwork," concludes Jaap, "Together, you can achieve things that would be impossible alone."
Get inspired
TNO’s next generation biorefinery accelerates material transition
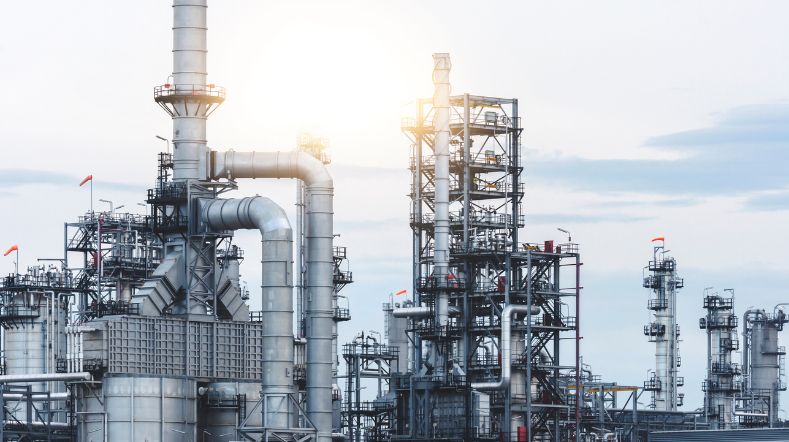
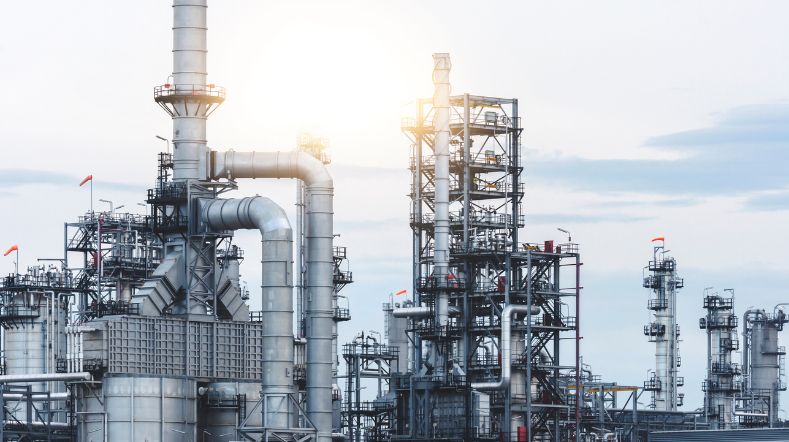
Renewable fuels
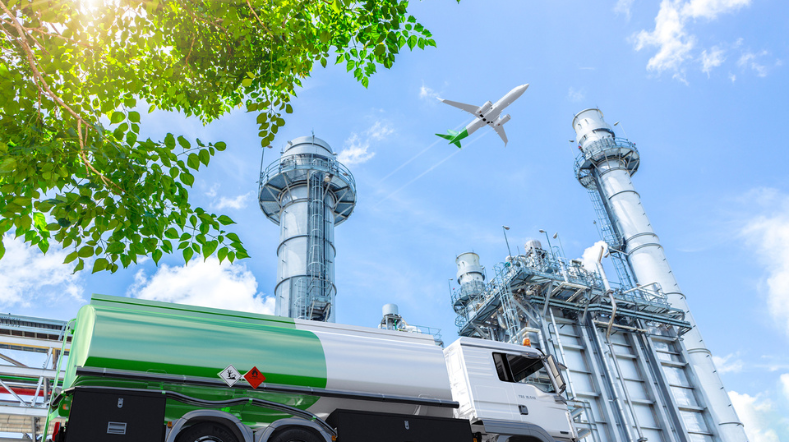
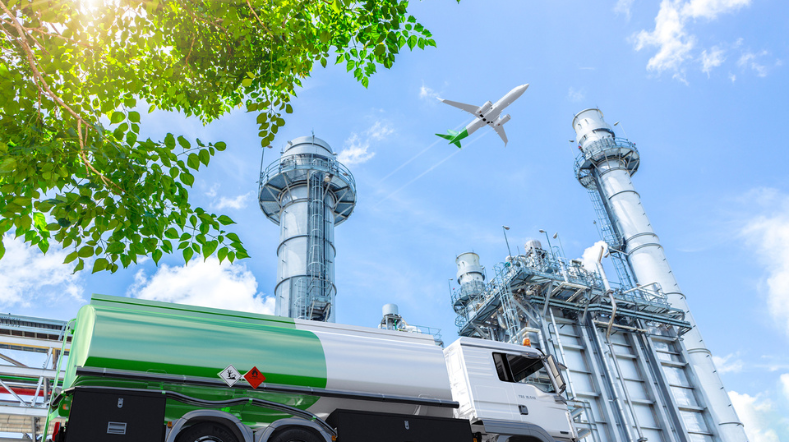
TNO develops method to produce biocarbon


New technology combines biocarbon production for industry with negative emissions
Producing renewable DME using renewable energy and CO2
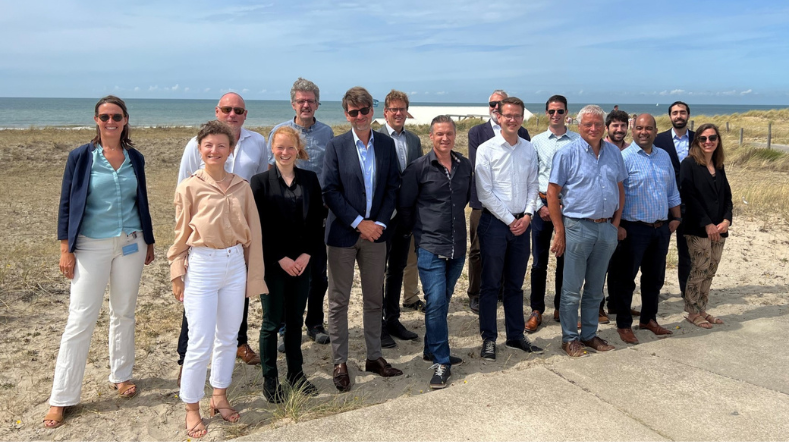
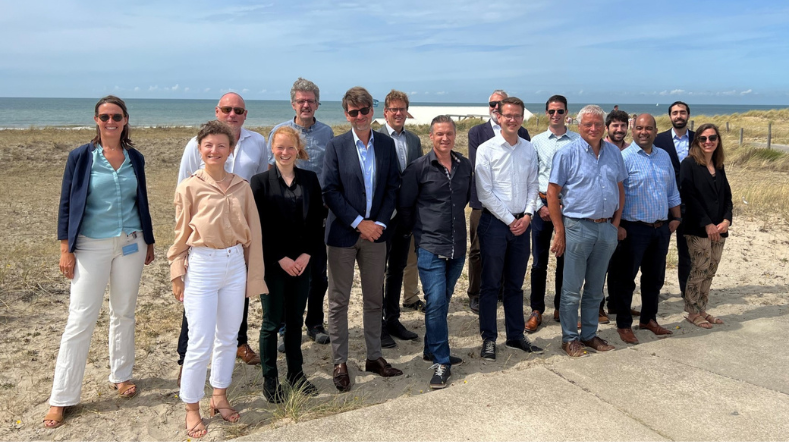