Processing of propellants, explosives and pyrotechnics
Societal challenges such as geo-political complications, rising global tensions, foreign dependency and material scarcity urge nations to ensure that their armed forces are optimally equipped to defend, both today and for the foreseeable future. That’s why MoD’s and other stakeholders in the defense industry typically turn to us for innovative solutions related to improvement of performance and costs reduction of munition articles.
For example traditional propellant and warhead production technologies, which were developed over more than 60 years, have more or less reached the end of its development cycle. With the advent of 3D printing technologies it becomes possible to produce propellants and warheads that have significantly better performance than the traditionally produced propellants.
Propellants, Explosives and Pyrotechnics: Our customer focus
With clients including the Netherlands Ministry of Defence and foreign authorities, as well as manufacturers, we focus on improving range, accuracy and effect, and reducing collateral damage, with increased cost effectiveness.
As an independent R&D institute, we work hard to maintain and extend its leadership in the field of propellants, explosives and pyrotechnics, which gives us a unique position from which to provide support and consulting services that run the entire gamut from the procurement process to the subsequent stages of actual use, maintenance and disposal.
Alternative material research, climate and sustainability
Climate protection and sustainability policies are getting more important for the defense industry. In certain countries, some ingredients used in the manufacturing process of energetic materials are banned. These include lead- and heavy metal-based ingredients, as is the use of chemicals and materials that are associated with health and/or environmental risks. Therefore we strongly focus on developing improved and less environmentally harmful production methods and new less harmful energetic formulations.
Also, certain ingredients are scarce, they are simply no longer available in the developed world. A material such as TNT, for example, can currently only be sourced from a single country in the western world. And even that nation is now evaluating whether to continue manufacturing TNT, so it is vital to gain access to alternative materials with equal effectiveness. We are solving this by apply industry 4.0 technology to make small scale production costs effective and less harmful for the environment. Making on site production possible and so nations and industry independent of suppliers.
Printing materials
Seven years ago, we started researching 3D printing as a new production method for energetic materials. We are a world leader and innovation pioneer in this field. Among the major benefits of 3D printing are the complex shapes and internal functional gradients that can be achieved.
Other institutes are now also recognizing its potential and are following our lead. Today, our 3D prints energetic materials such as gun and rocket propellants, as well as explosives. We are also investigating the potential for pyrotechnics and are eventually aiming to produce complete munition-systems using this innovative technology.
In house expertise broader than energetic materials
Clients in the defense industry rely on our expertise with regard to production technologies and the development of new energetic materials and munitions, but also come to us because of our knowledge base. We are at the front end of all major technological developments in the world.
To solve problems or overcome challenges, we call upon in-house expertise in other areas when the need arises. An excellent example of this is the use of in house 3D printing technology to accelerate knowledge 3D printing of energetic materials development, such as the printing of ammunition.
Unique facilities
We have a knowledge base covering the entire spectrum of the materials vital to the development, production and use of munition items and beyond. This is complemented by unique facilities making TNO perfectly placed to conduct R&D on the actual energetic formulations.
For example compared to similar organizations in Europe, we are able to achieve a much higher Technology Readiness Levels (TRL) in projects with our industrial partners.
Get inspired
How the use of passive radars and satellite signals can detect and identify aerial threats
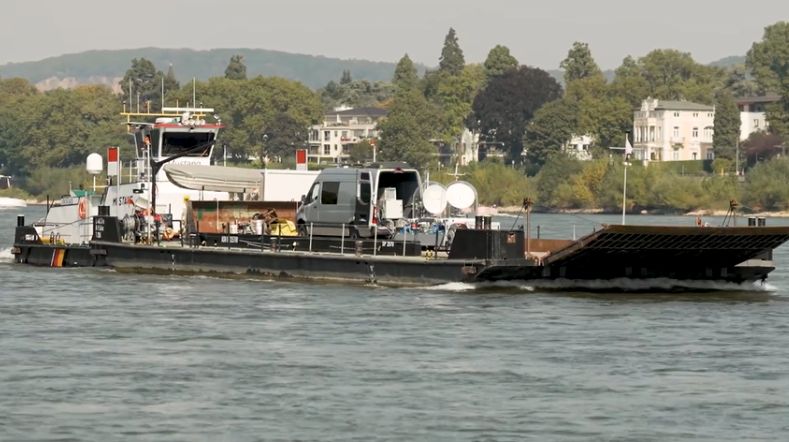
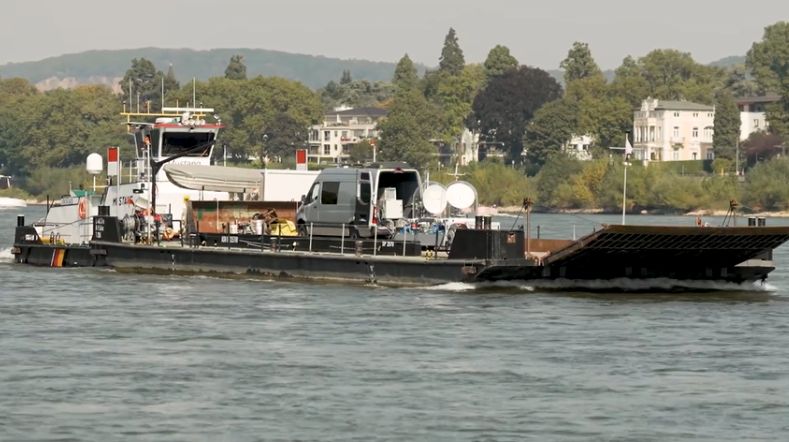
Responsible for safety: the crucial role of the range operator in bulletproof protection
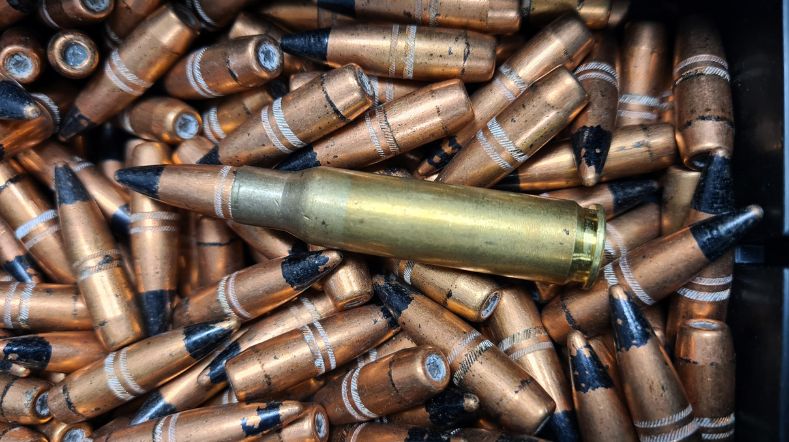
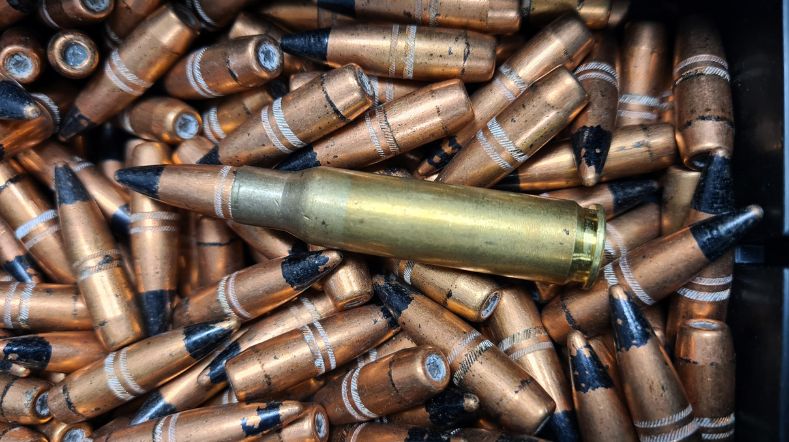
Is the race between protection and weight of Defence vehicles changing?
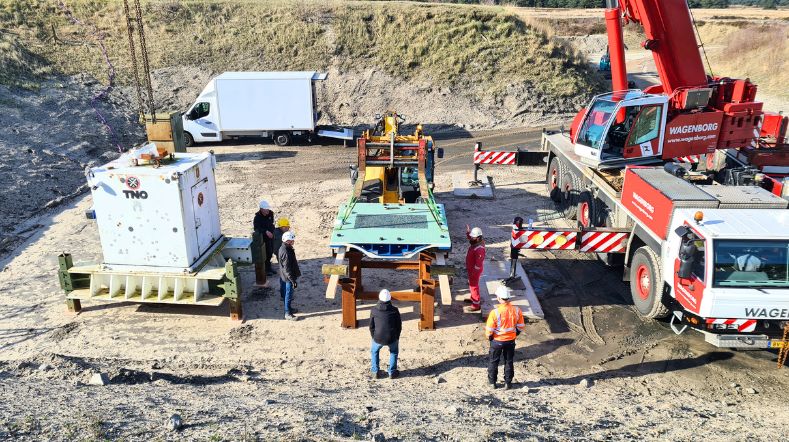
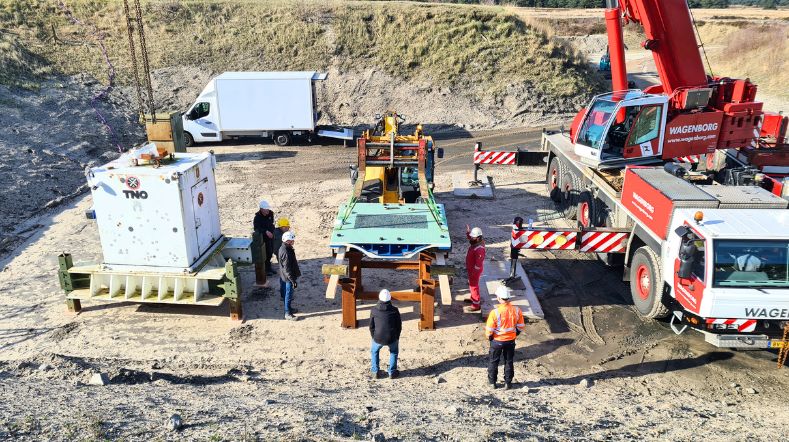
Prevent mild brain damage (mTBI) in the military? TNO is helping to build knowledge
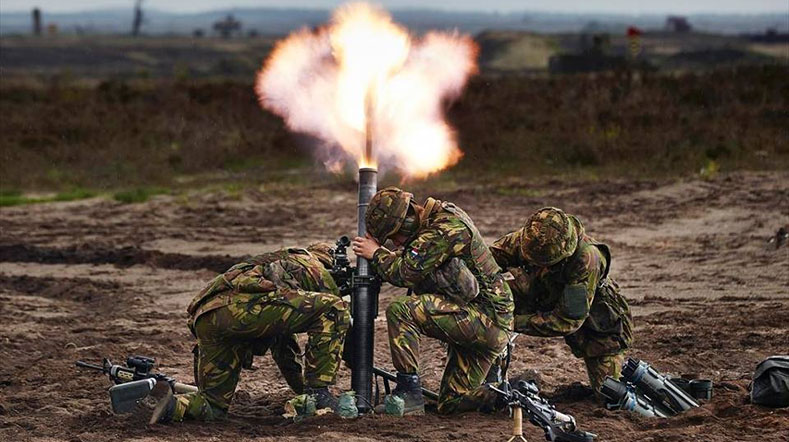
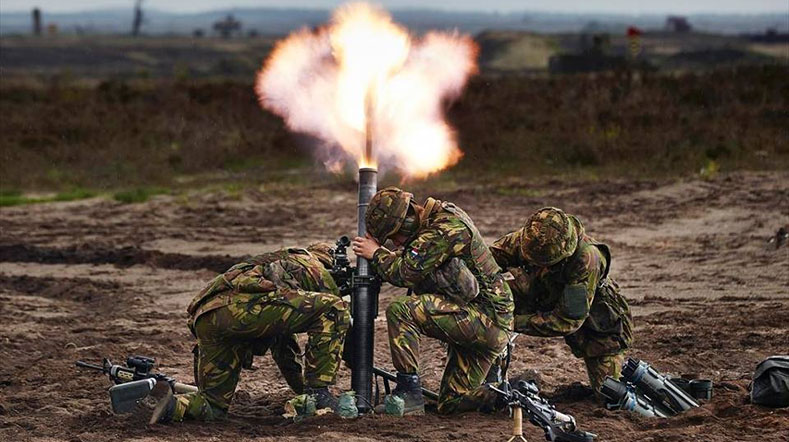
How does TNO help protect us from hypersonic weapons?
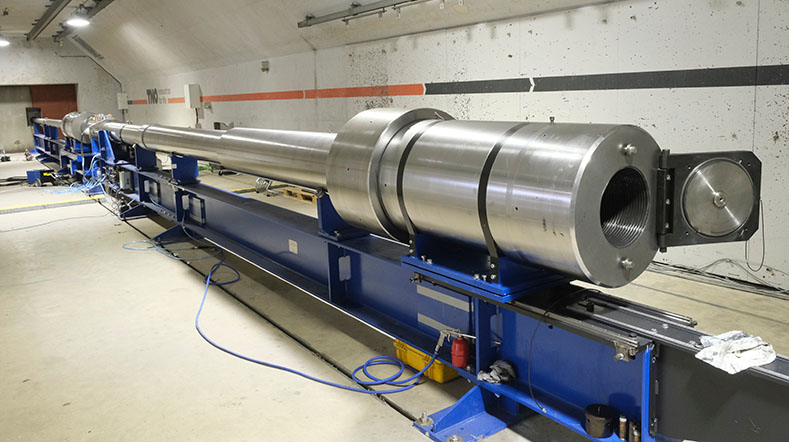
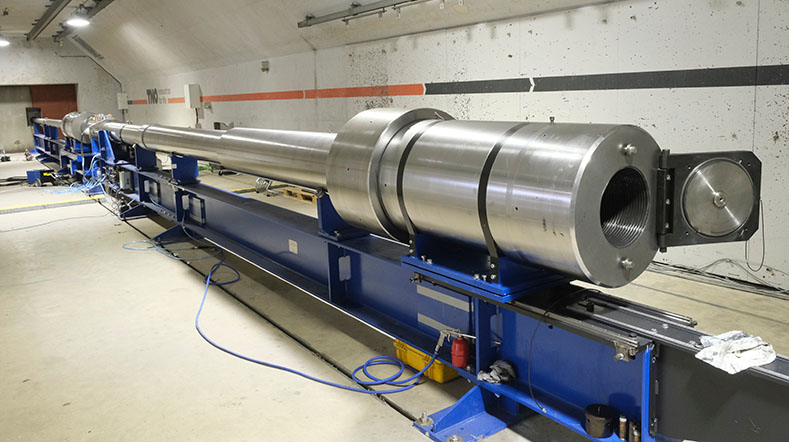