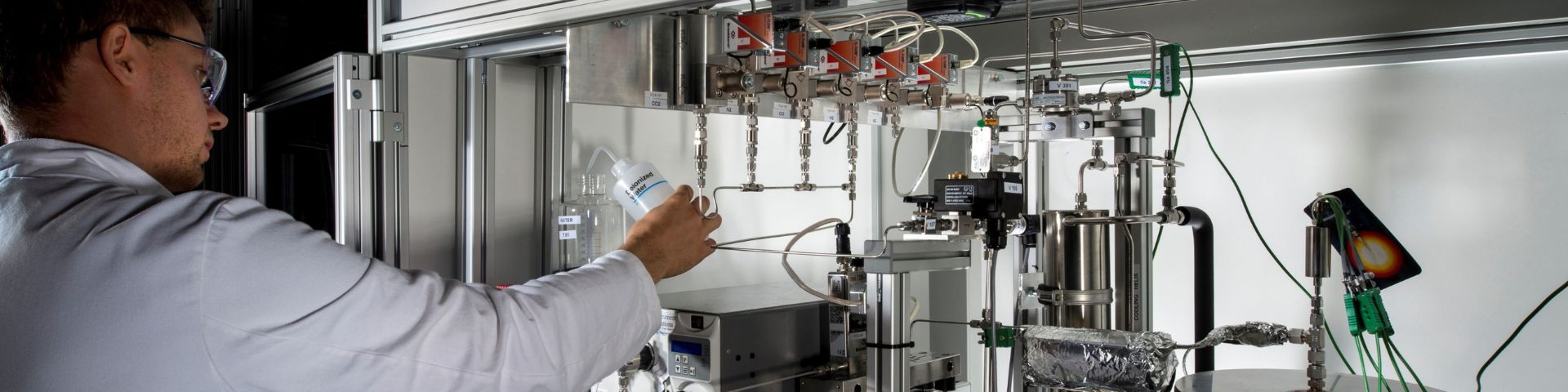
CO2ART: CO2 becomes a green resource
In cooperation with
Dunlop, Huntsman, Escher en Ecovyst
The production of aromatics, such as benzene, toluene, and xylene (BTX), causes significant CO2 emissions because they are primarily made from fossil fuels. However, these are essential substances for the industry, used daily in numerous products like food packaging (PET bottles), insulation materials, sportswear, and shoes. To reduce CO2 emissions and the industry's dependence on these fossil fuels, TNO and partners developed an innovative process in the CO2ART project. This process converts captured CO2 into sustainable aromatic building blocks.
Groundbreaking solution for a reliable process
In the CO2ART- project (Conversion of CO2 to sustainable ARomatics applying innovative reactor Technology) we work on a groundbreaking solution by converting CO2 into sustainable aromatic building blocks using hydrogen. This project focuses on the direct conversion of CO2 with sustainable hydrogen into BTX, using a bi-functional catalyst.
This technology not only provides a sustainable source of aromatics but also aims for higher efficiency and less carbon residue buildup (cokes) on the catalyst, which is essential for a long-lasting and reliable process.
Reusing CO2 as a circular solution
The transition to sustainable sources for aromatics is essential to reduce dependence on fossil fuels. This project fits into the broader context of circular carbon solutions, where CO2 is reused instead of emitted.
The CO2ART project plays a crucial role in this transition by developing new technologies that help the chemical industry move towards a more sustainable future.
CO2ART project partners
As the coordinator of the project, TNO is responsible for the development of reactor innovation, process optimisation, modelling, and techno-economic evaluations. For this, we collaborate with:
-
Huntsman: A globally leading chemical company that uses aromatic raw materials in Rotterdam for the production of polyurethanes. Polyurethanes are used in home and refrigerator insulation, as well as in lightweight cushioning materials for cars, furniture, and shoes.
-
Dunlop: A world leader in protective footwear and boots, aiming to further reduce the carbon footprint of their products with sustainably produced polyurethanes.
-
Escher Process Modules: A leading process technology company specialising in the design, engineering, and realisation of high-quality process modules for the industry. In CO2ART, Escher uses its expertise to scale up the technology.
-
Ecovyst: A leading supplier of catalysts, involved in the development and scaling up of the bi-functional catalyst that forms the innovative heart of the CO2ART process.
Towards commercial feasibility
The CO2ART project has achieved promising results and proposed reactor configurations. The goal is to increase the Technology Readiness Level (TRL) from TRL2 to TRL4 by the end of the project, meaning the technology is conceptually proven and ready for pilot-scale tests.
This project takes an important step towards a sustainable and circular chemical industry, offering innovative solutions for today's climate challenges.
Get inspired
The North Sea as Europe's energy heart requires smart choices
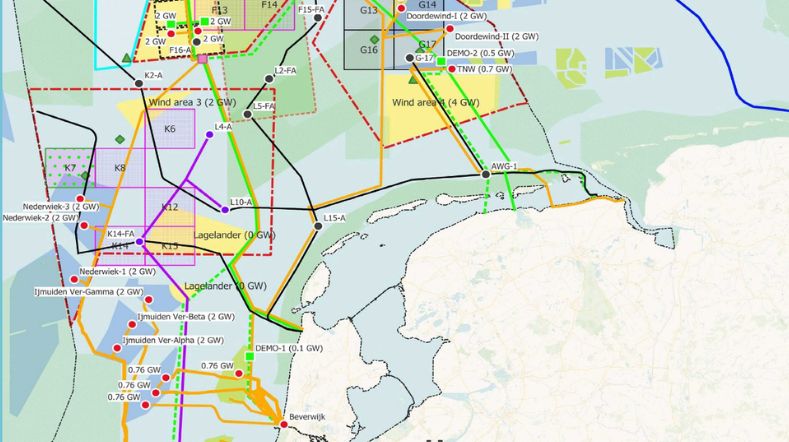
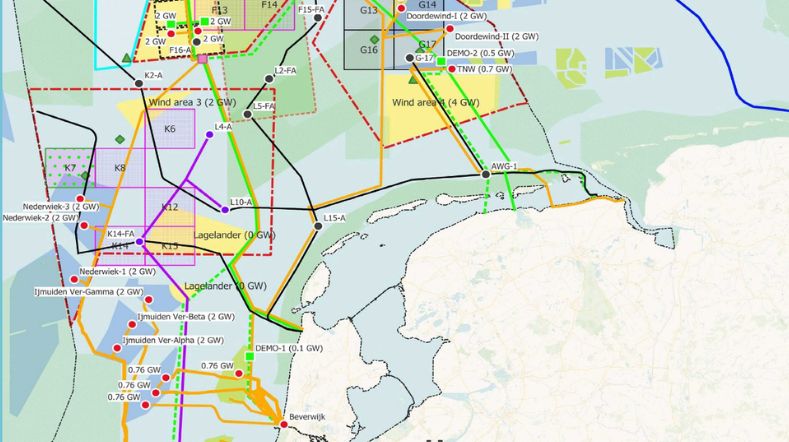
Tomorrow’s hydrogen production and infrastructure: building towards a secure and robust energy system
World Hydrogen Summit 2025
Scaling-up electrochemical technologies for renewable ethylene production
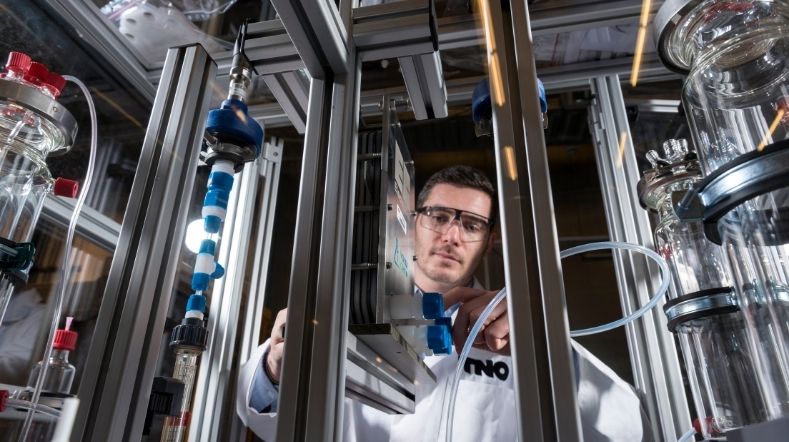
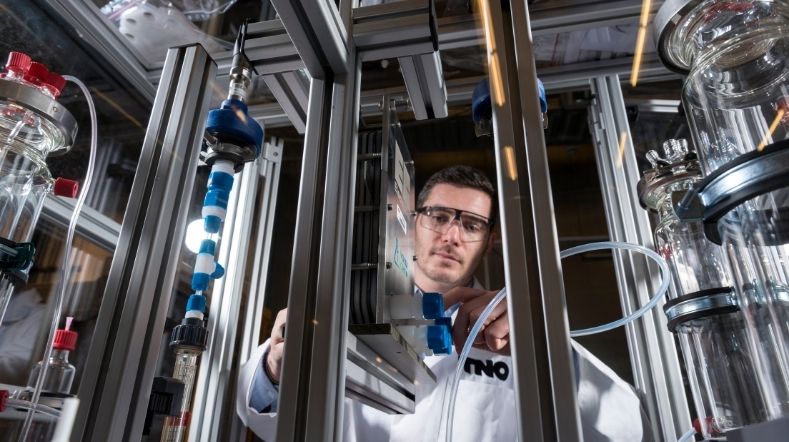
CO2 infrastructure and transport

