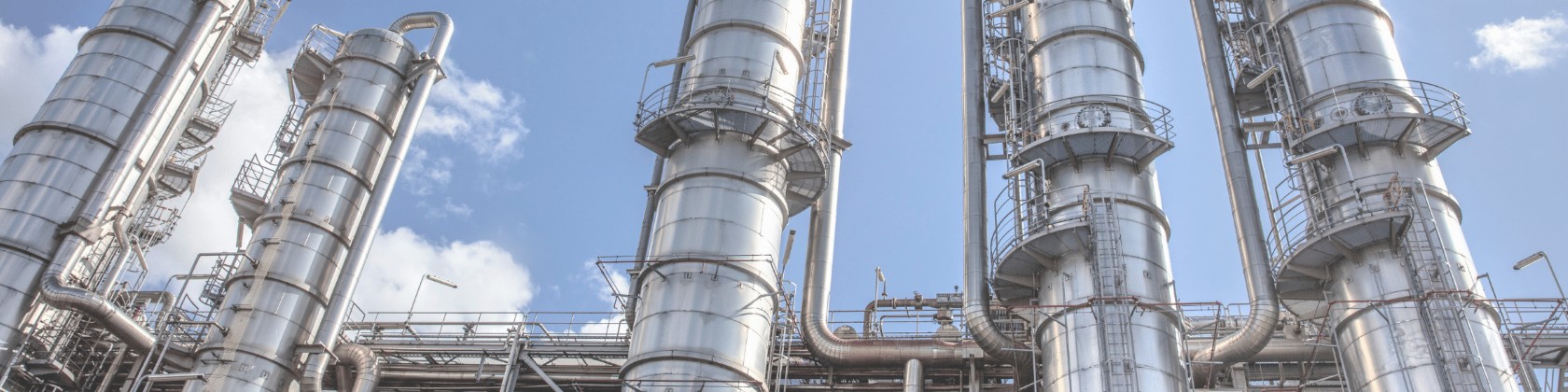
SEDMES: efficient technology to convert CO2 to useful product
To improve climate change, industrial processes, products and feedstock need to become climate neutral, and industrial cycles have to be closed. The SEDMES technology provides an essential element in closing industrial cycles and contributing to a circular carbon economy by converting CO2 efficiently to dimethyl ether (DME), a potential renewable fuel and chemical building block.
Sorption Enhanced DME Synthesis (SEDMES)
SEDMES converts CO2 and (green) H2 to DME in one reactor step with high conversion rates and high efficiency thanks to the in-situ separation of water. The conversion rate from CO2 increases from ~10% to ~85%, significantly reducing recycles and downstream processing.
The novel Sorption-Enhanced DME Synthesis (SEDMES) process, comprising in-situ steam removal with a solid adsorbent, ensures high CO2 conversion efficiency to DME in a single unit operation. The in situ removal of steam, shifting the equilibrium to the product side, has proven to enhance catalyst lifetime and boost process efficiency, specifically in the case of diluted CO2-rich gas streams.
What is DME?
DME is a friendly combustible gas, which is currently best known for its use as aerosol propellent in hairspray. DME is a commodity with modest market size, but has - in the current energy transition – the potential to grow to a large commodity chemical as it can replace diesel and LPG, and (as dehydrated methanol) is likely to become a major intermitted feedstock for chemical industry:
- DME is a good replacement of diesel, as diesel engines do not have to be modified to use DME as fuel. Just the fuel tank, fuel injection and control (outside the engine block) needs to be DME specific. A diesel engine is able to change fuel (from diesel to DME and vice versa) and combust a mixture. The combustion of DME is soot free, which is an additional advantage for the environment.
- DME is a good replacement of LPG (propane/butane). It is stored under similar pressures and as such is likely to be able to use the LPG infrastructure with minimal changes. LPG is widely used as energy supply to off grid locations.
- In methanol-to-chemicals (olefins, paraffins, aromatics) DME, dehydrated methanol, is an intermittent product. Currently a modest market, the conversion of methanol to products is widely seen as the cornerstone of a circular carbon chemical industry. DME can be readily adopted in various methanol-to-chemicals schemes for the production of high-value monomers or aromatics.
How does SEDMES work?
The SEDMES process combines two process steps in one reactor. The first is the conversion of CO2 and hydrogen into DME and the by-product water. Because this is a so-called equilibrium reaction, the wanted product (DME) will react back into the undesired substances (carbon dioxide) and it is impossible to achieve complete conversion. The second process prevents this undesired reaction by adsorbing the by-product water with an adsorbent material. The combination of these processes in one reactor results in a higher yield and much more efficient process.
Advantages of SEDMES
The adsorption enhanced DME production technology ensures high CO2 conversion efficiency to DME in a single unit operation. SEDMES enables the use of CO2 as a feedstock for DME production instead of syngas (CO and H2) used in the conventional production route and can even be used without capture of the CO2 from industrial gases. The in situ removal of steam, shifting the equilibrium to the product side, has proven to enhance catalyst lifetime and boost process efficiency, specifically in the case of diluted CO2-rich gas streams.
SEDMES is demonstrated to be a powerful power-to-X technology for efficient conversion of green H2 into DME. It is anticipated that the multi-column process can handle dynamic operation (based on the intermittent nature of renewable energy) exceptionally well.
Development in projects
The SEDMES technology is successfully tested on lab and bench scale, making use of existing infrastructure of other sorption enhanced processes (SEWGS). Starting with the European project Fledged in which TRL5 experimental testing of the complete SEDMES operating cycle has been concluded, supported by SEDMES cycle modelling for operation mode design and optimization. In the Interreg E2C project the first dedicated SEDMES facility has been designed and engineered in-house by TNO and built. Watch the video of the construction.
The unit is currently being used for testing at TNO in Petten in the recently started iDME project. This project focusses on energy and cost efficient reuse of residual gases, by SEDMES. The economic perspective and the environmental impact of the iDME concept, without the requirement of CO2 capture prior to its utilisation, will be investigated and further improved by process design and development. Subsequently, the SEDMES unit will be transported to the field lab industrial electrification in Rotterdam (FLIE), where it is to be connected to an 100kW electrolyser, and commissioned.
Get inspired
Ten things to know about carbon capture and storage (CCS)
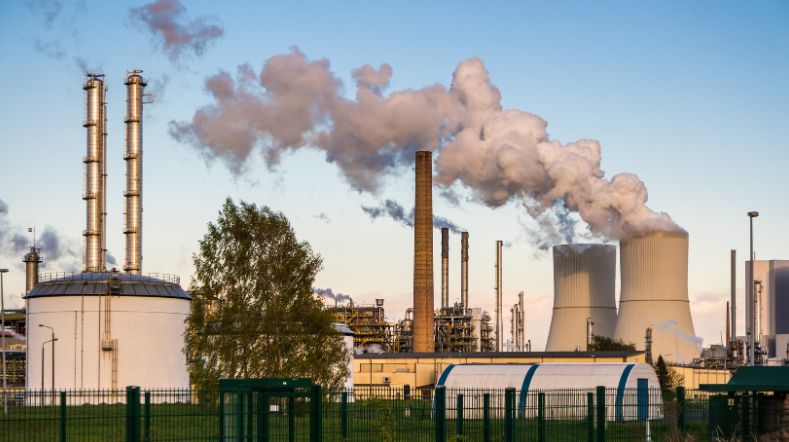
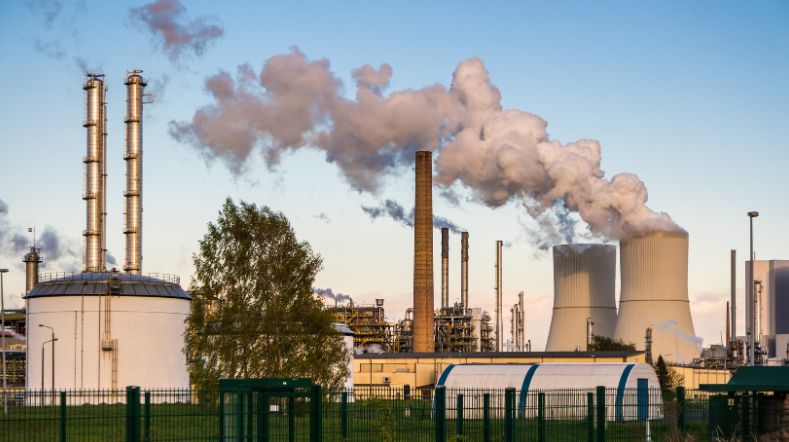
Unique test installation for CO2 capture and conversion to green chemicals
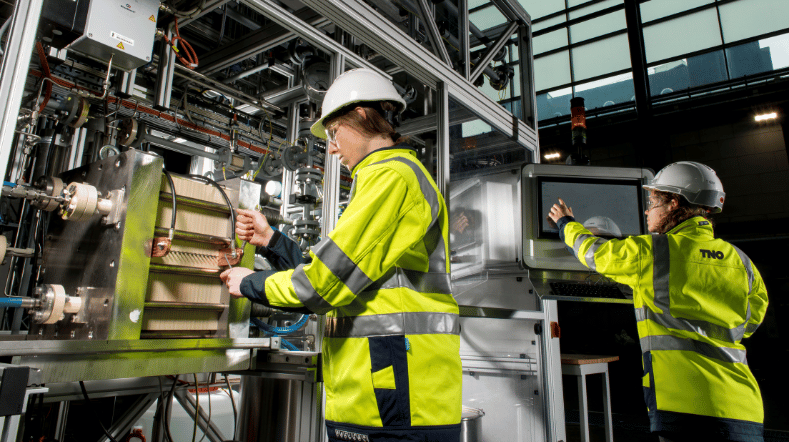
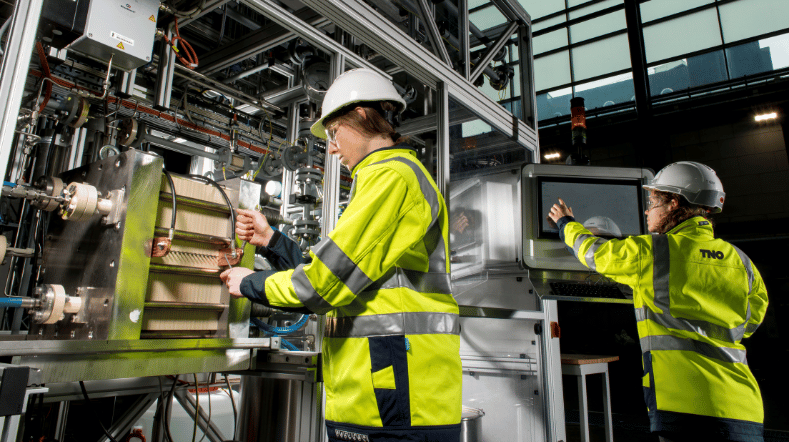
SEWGS: revolutionary CO2-reduction technology
SEWGS
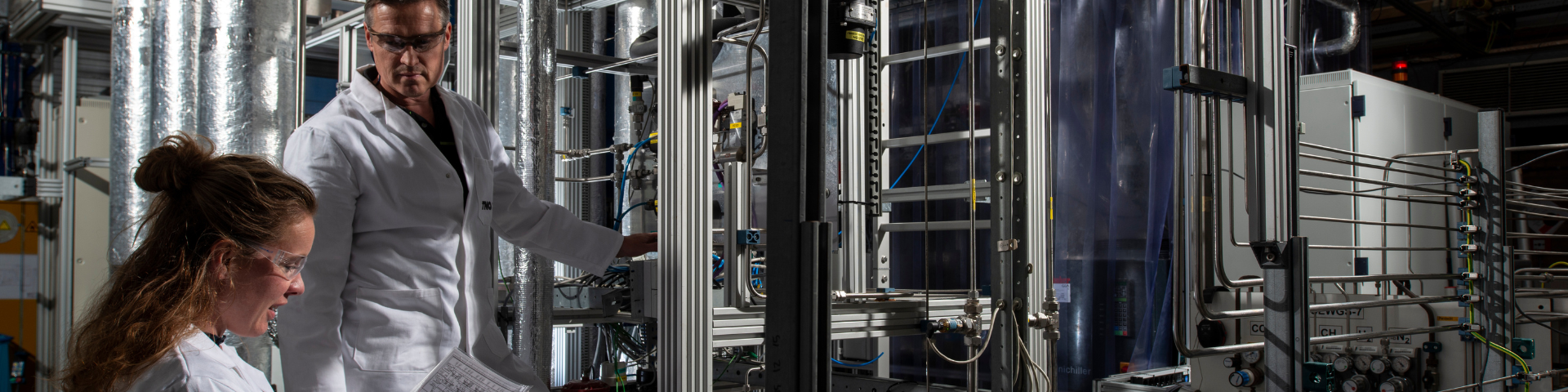
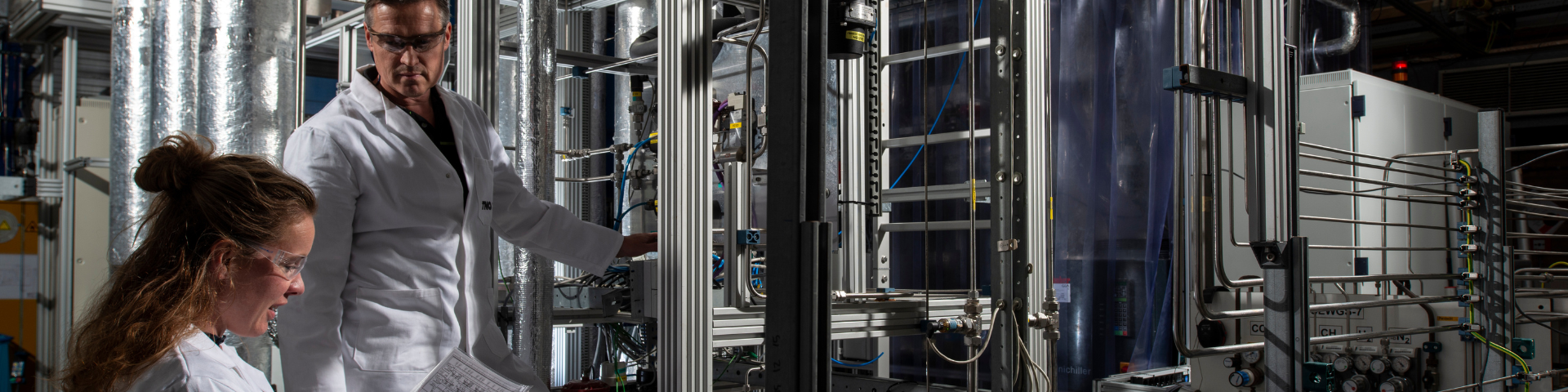
Capturing carbon emissions
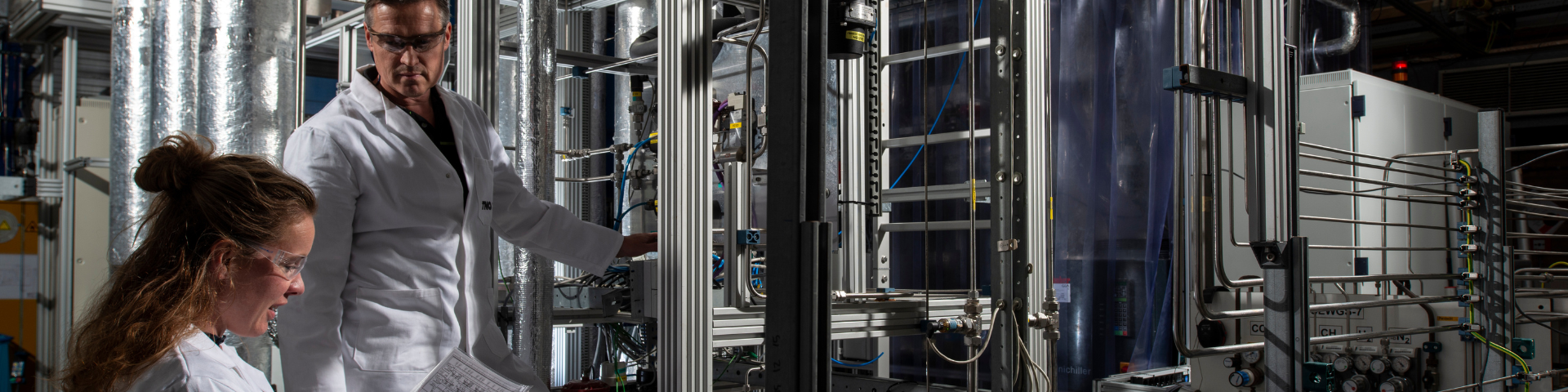
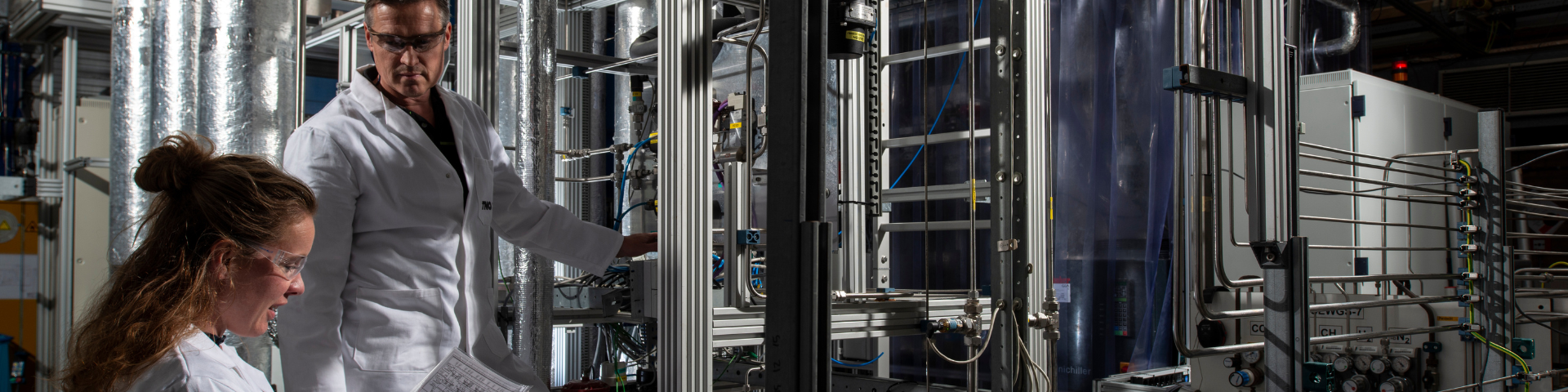