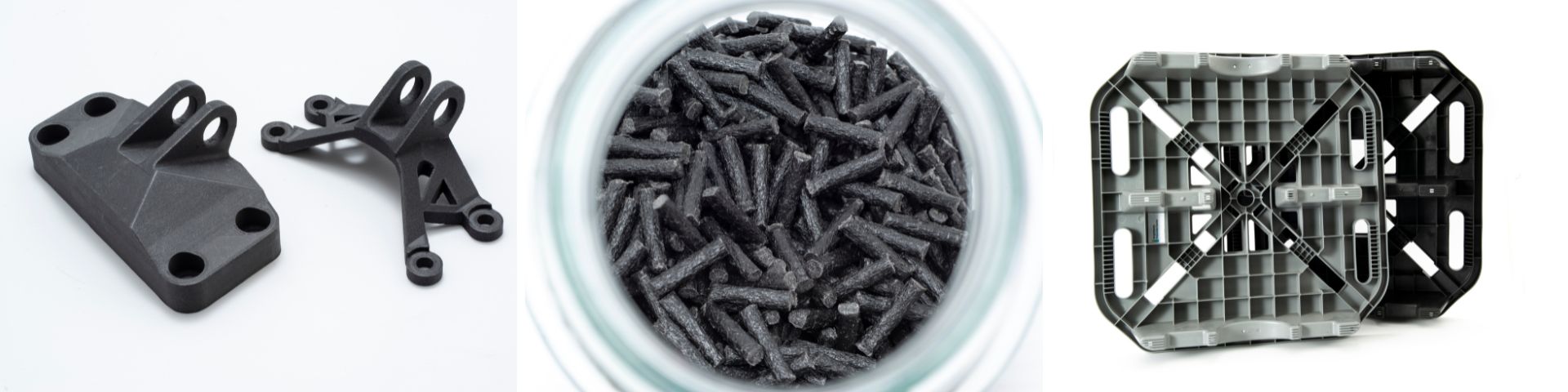
Thermoplastic composites: strong as metal, light as plastic
Thermoplastic composites (TPC) are already found in many vehicles. This material combines the strength of metal with the lightness of plastic. At a time when climate change and CO2 emissions are important themes, this material plays a crucial role in sustainability. At TNO, we are working with partners on high-quality recycled TPCs. To this end, we are investigating how to recover waste material and TPC from products after their use phase and reuse them in new products, while maintaining as much of the original quality as possible.
Applications in sports equipment, household appliances, and vehicles
For products and applications where normal plastics are not strong enough, thermoplastic composites are often used. Examples are sports equipment such as tennis rackets and hockey sticks. A hockey stick made of normal plastic would break quickly. Parts of household appliances, such as washing machines and dryers, are also often made of TPC. However, the principal use of TPC is in aircraft and car parts.
Composition: plastic reinforced with fibres
Thermoplastic composites are plastics with added fibres, such as glass or carbon fibres. These significantly strengthen the plastic, making the material much stronger and resistant to impact or breakage. This is essential in structural parts of vehicles, such as dashboard mounts, interior parts of doors, under the bonnet and in the fans of the cooling system. Moreover, thermoplastic composites do not rust and last longer than metal.
Recycling and reuse
The advantages of TPC are clear but recycling the material is a challenge. The problem is that during recycling, products and materials are reduced in size to be processed. The reinforcing fibres in the TPC are broken, thus becoming shorter, which reduces the strength of the composite material. The recycled composite can then no longer be used for high-quality applications.
TNO has developed a process to preserve fibre length as much as possible during the recycling process, maintaining the highest possible quality. With this method, dozens of kilograms of TPC can currently be processed per hour. The goal is to convert the TPC parts back into new materials for vehicles.
We are working on this in the Composites - NXTGEN Hightech project by applying a whole series of measures and optimising the process, so that the fibres break as little as possible.
Innovation in the manufacturing process
In addition to recycling TPC, TNO is also developing innovative new manufacturing processes for thermoplastic composites. Most short-fibre TPC materials are processed using an injection moulding process, but applications that require very high strength call for much longer fibres.
Other manufacturing processes are needed for this purpose. TNO is working on a new method that uses additive manufacturing – also known as 3D printing – to apply continuous fibres in unique designs of products and thus produce very lightweight components.
Lightweight technology
In the Multhem project, TNO is investigating together with value chain partners whether continuous fibre 3D printing technology can be used for small electric drones.
The advantage of 3D printing is that the design can be optimised, resulting in much lighter parts. Lighter vehicle parts reduce energy consumption and lower CO2 emissions.
Collaborating on a circular chain
From supplying TPC waste to reusing high-quality recycled TPC, we are striving to create a circular value chain. In that context, we welcome partners to join us in working on this material transition challenge.
Are you looking for help in recycling TPC production waste? Are you interested in reusing recycled materials? Or are you working on applications with complex, heavy shapes that are difficult to make?
Get inspired
New method also considers environmental impact of microplastics
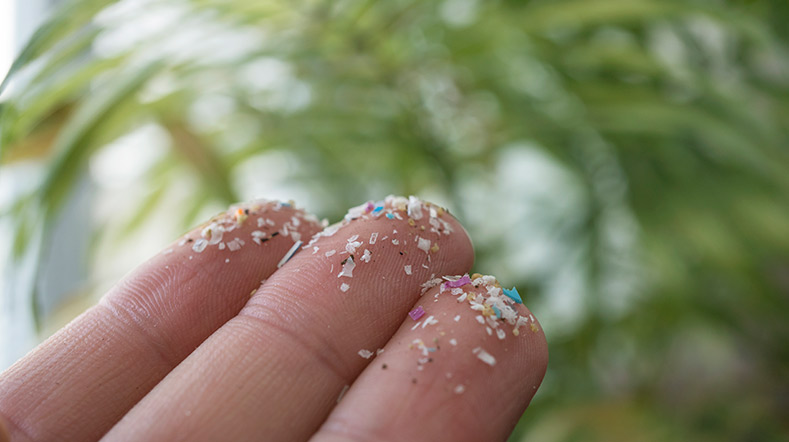
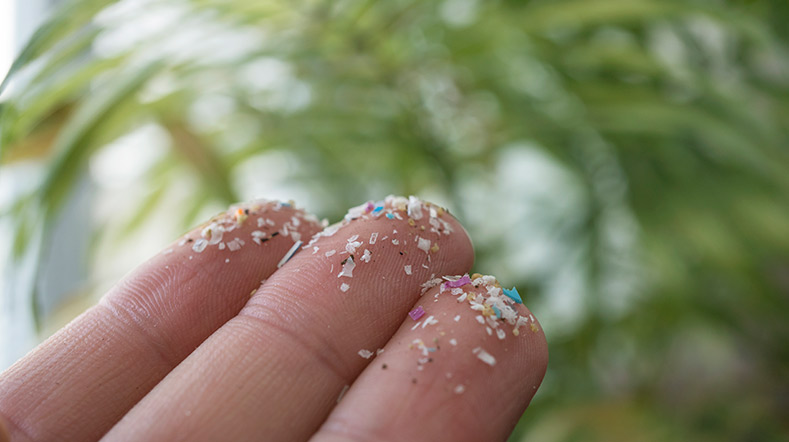
Microplastic aquatic impacts included in Life Cycle Assessment
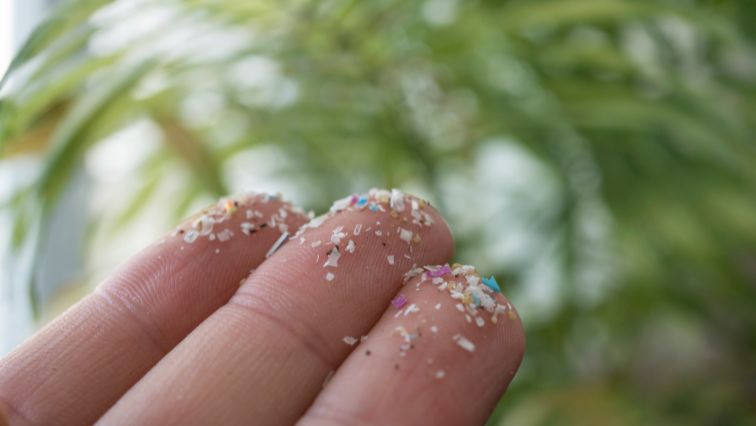
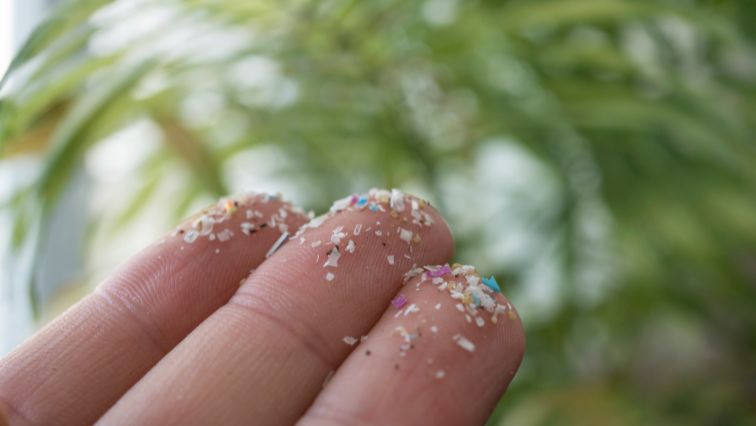
Microplastics and packaging: reduction is achievable
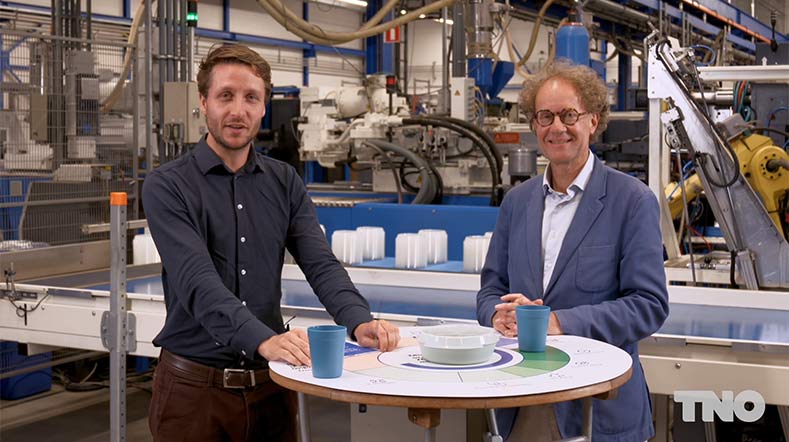
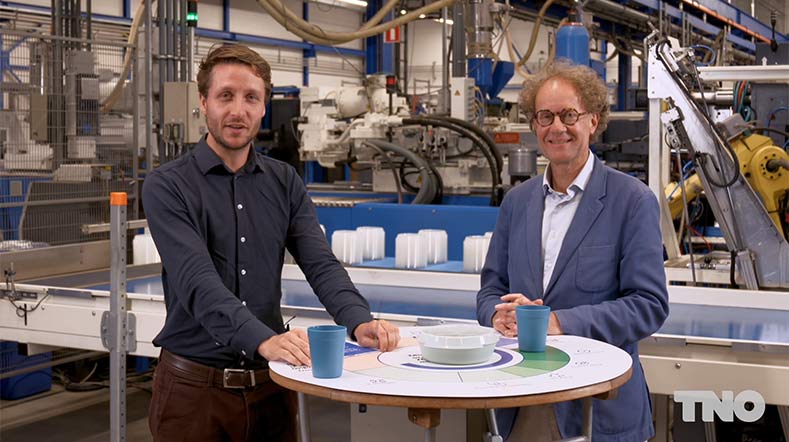
Time setters during the Ocean Race: a healthier world without microplastics
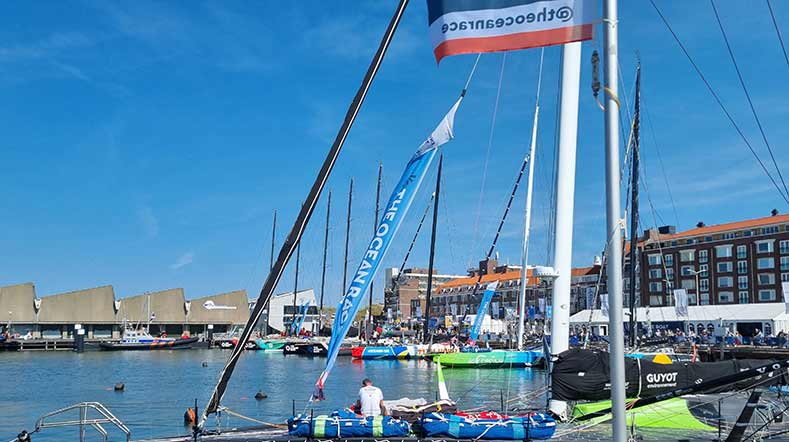
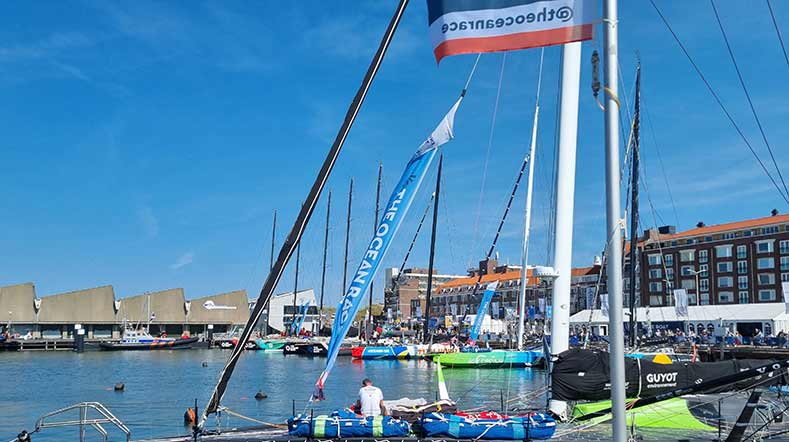
Surprisingly, in addition to packaging, car tyres and agricultural plastic biggest sources of microplastics in the Netherlands
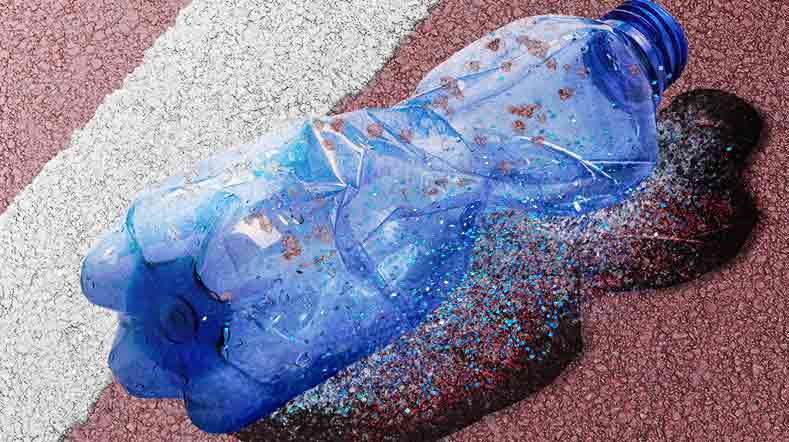
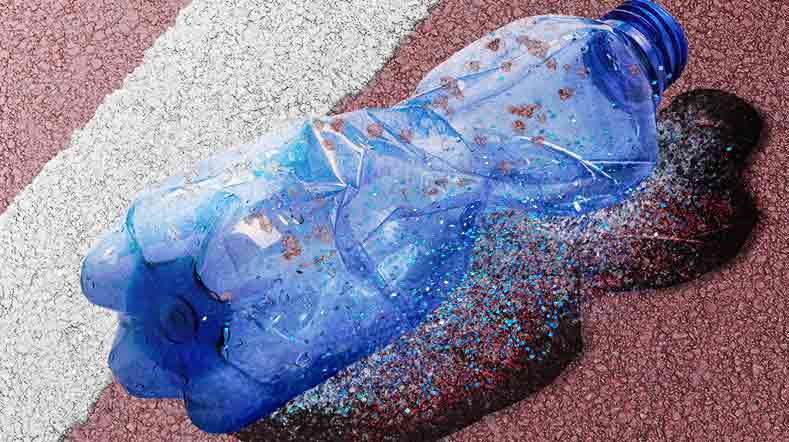