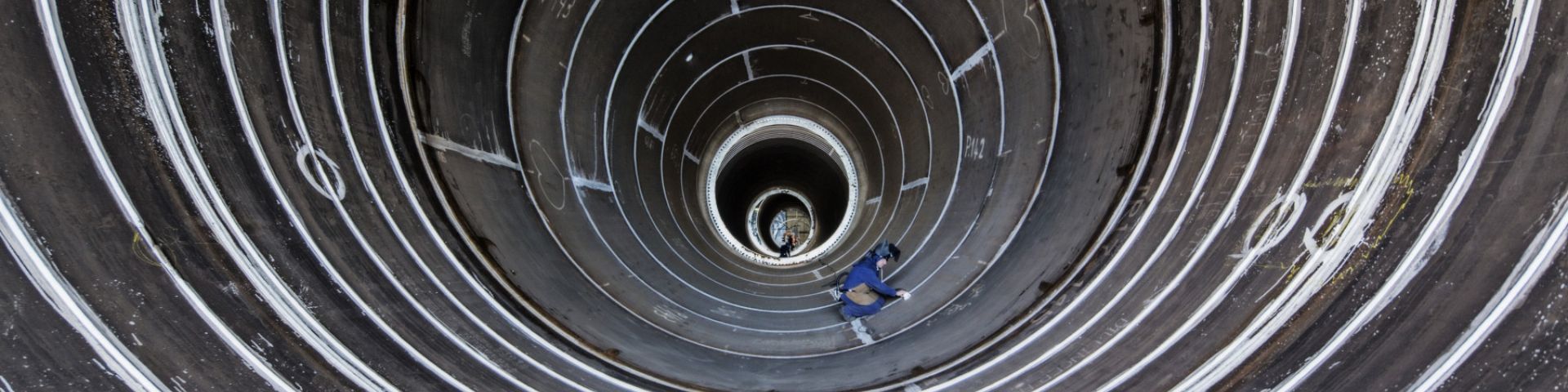
Corrosion Fatigue Life Optimisation (C-FLO)
In cooperation with
Ministerie van Economische Zaken en Klimaat, Deltares, TU Delft, Vattenfall, DNV, Ørsted, Eneco, Van Oord en Parkwind
The C-FLO project aims to develop an integrated corrosion-fatigue model to predict the lifespan of offshore wind turbine foundations in the North Sea. This model provides valuable insights to optimize foundation design and maintenance, ultimately reducing operational costs.
Heavy load on offshore wind turbine foundations
Offshore wind turbine foundations are exposed to extreme conditions, both underwater and above the waterline. These harsh environmental factors, coupled with the cyclic loads from the turbines, can lead to corrosion and fatigue cracking, which shortens the life of the foundations. Predicting the lifespan of these foundations, as well as the effectiveness of protective measures, is essential for reducing both design and maintenance costs.
The primary stakeholders involved in this project include offshore wind farm developers, engineers, government bodies, and companies engaged in the construction and maintenance of wind parks, such as TNO, Deltares, Vattenfall, Ørsted, and others. The outcomes of this project are crucial for the offshore wind industry and contribute to cost reductions and the sustainable development of wind energy projects.
The final public report of the project can be found on the GROW website via the link: C-FLO - Final public report.
Corrosion-fatigue model
The C-FLO project, carried out between 2019 and 2023 and supported by a subsidy from the Dutch Ministry of Economic Affairs and Climate, focused on developing a combined corrosion-fatigue model for predicting the lifetime of monopile foundations in offshore wind farms.
These foundations are subjected to both the corrosive marine environment and mechanical loads from the wind turbines, which can lead to fatigue cracks over time. The project was conducted by a consortium of TNO, Deltares, TU Delft, Vattenfall, DNV, Ørsted, Eneco, Van Oord, Parkwind, Sif, RWE, Shell, Posco, PPG Coating, and Rijkswaterstaat within the framework of the GROW program for offshore wind energy.
The project has led to the creation of two models: a corrosion-fatigue model and a more fundamental model for corrosion pit growth. The corrosion-fatigue model captures the effect of corrosion pit growth, the initiation of fatigue cracks from these pits, and the subsequent propagation of the cracks.
The fundamental model accounts for the electrochemistry of the corrosion process within the pits and integrates the influence of mechanical loading on corrosion.
Test-setups
The images below show the test samples used during the conducted experiments.
Figure 1: Test specimens pre-corrosion in artificial seawater
Figure 2: Test set-up of the large scale fatigue tests in artificial seawater
Figure 3: Test set-up of the small scale experiments in artificial seawater
To validate the models, several experiments were conducted, including corrosion tests in artificial and microbiologically active seawater, small-scale experiments on steel specimens with artificial corrosion pits, and large-scale fatigue tests in artificial seawater. These experiments provided valuable data to refine the models and improve their predictive accuracy. Additionally, the project generated customized S-N curves, which are used to optimize both corrosion protection measures and the design of monopile foundations.
Towards cost reduction in design and maintenance
After the completion of the C-FLO project, the focus will shift to further validating and refining the developed model to ensure its practical applicability for offshore wind farm design and maintenance. The next steps include expanding the model with additional experimental data and integrating the results into the standard design processes for offshore wind farms. By improving the predictability of corrosion and fatigue, the model will help reduce maintenance costs and enhance the sustainability of offshore wind projects.
The corrosion-fatigue model has the potential to offer significant cost savings by enabling more precise predictions for foundation lifetime, allowing for optimized maintenance schedules and corrosion protection strategies. It will also support the design of more cost-effective monopile foundations, tailored to specific environmental conditions, and contribute to a more sustainable offshore wind industry.
Collaborate together?
The C-FLO project presents opportunities for further collaboration and knowledge sharing. Companies and research institutions interested in implementing the corrosion-fatigue model or contributing additional expertise are encouraged to get in touch for more information and potential partnership opportunities.
Get inspired
Wind energy webinars
The transition to sustainable shipping
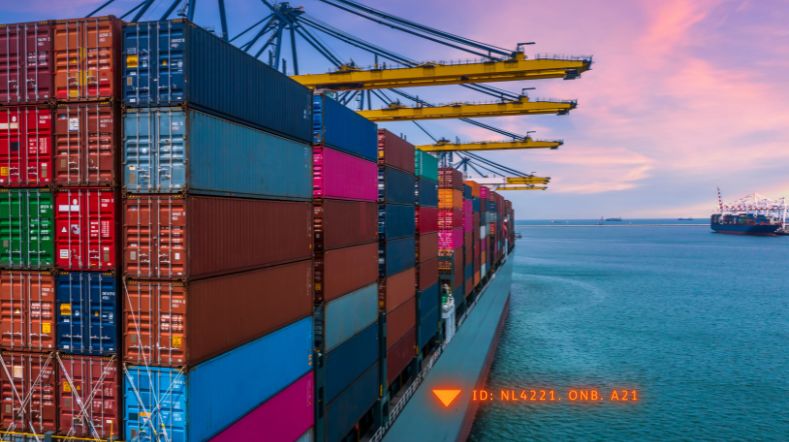
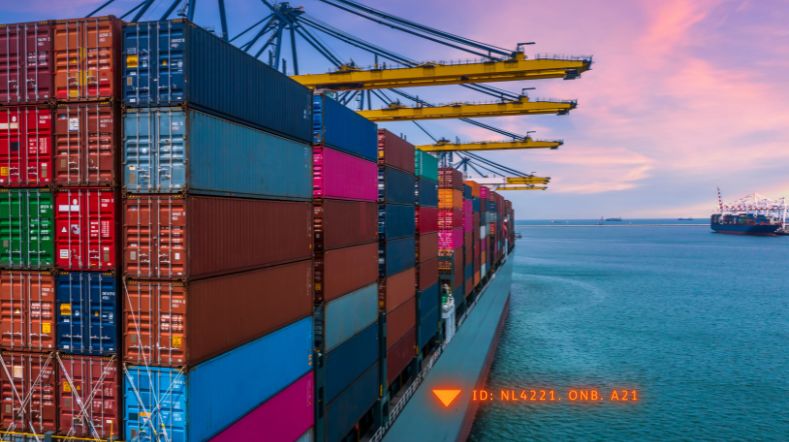
Ship materials and structures
Naval and Offshore Structures
TNO develops detection system to protect cables and pipelines on seabed
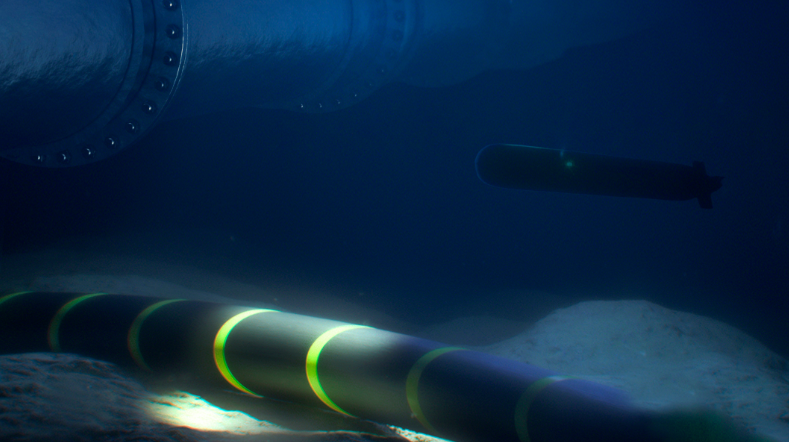
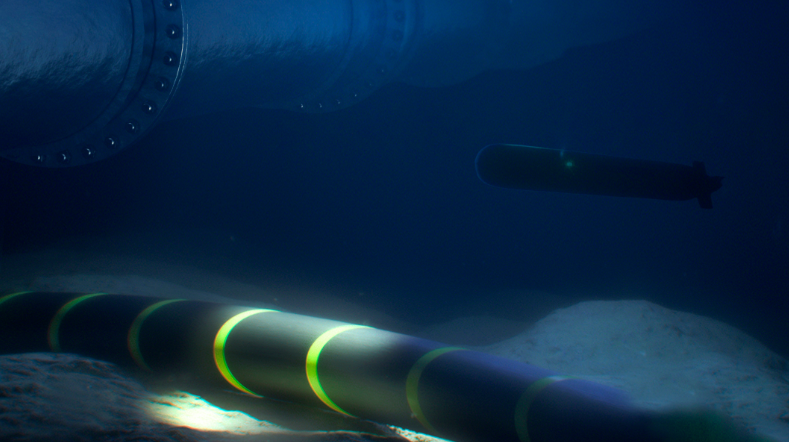