Sustainable vehicle configurations brought to market faster thanks to Modular Energy Management Strategy
The development of new sustainable drive systems for non-road mobile machinery, road transport, and maritime applications involves high R&D costs and is complex due to the wide variety of (vehicle) configurations and components. With the Modular Energy Management Strategy (MEMS), TNO offers developers and engineers an efficient and effective method and software suite that keeps development complexity manageable and reduces the time-to-market.
90% less greenhouse gas emissions from road traffic
The European Green Deal aims to reduce greenhouse gas emissions from road traffic by 90% by 2050. In addition to road transport, non-road and maritime applications, such as construction and agricultural machinery, must also achieve significant CO2 reductions.
In order to achieve this, we are seeing an increasing variety of drive systems: conventional combustion engines with a sustainable fuel, battery-electric solutions, fuel cells, and also hybrid drive systems. Each application often has a (slightly) different drive system for a low Total Cost of Ownership (TCO) and higher productivity.
However, these vehicles and drive systems must have an efficient energy management system to optimally control components such as the combustion engine, electric motor, and battery. The vehicle controller (VCU) continuously determines the optimal distribution of requested power between consumers and energy sources via an Energy Management Strategy algorithm, depending on the application and environmental conditions.
Time-consuming R&D
However, developing such energy management systems for each vehicle, for every application, has become a time-consuming and costly process due to the multitude of drive and energy components.
Jan-Willem Sangers, Business Developer Sustainable Vehicles at TNO: 'This is especially evident in the development of non-road mobile machinery, such as excavators, wheel loaders, and tractors. For each task, there is a specific variant with an optimal configuration for that application. As a result, there are often many different configurations within a product, each with an individual combination of components. Investigating and determining an optimal Energy Management Strategy for each variant, in every configuration, places a significant demand on a manufacturer’s R&D capacity.'
TNO contributes to this challenge with the development of a Modular Energy Management Strategy (MEMS). Paul Mentink, Senior Research Scientist Integrator Powertrains at TNO: 'It is a complete Vehicle Energy Management algorithm that can, in principle, perform energy management for any type of drive system and ensure an optimal distribution between energy consumers and energy storage.'
MEMS in practice
Traditionally, an R&D process for each powertrain configuration, or topology, goes through the same steps, Mentink explains. 'For a new product, say a tractor, this process begins with inventorying the new components. Think of innovative batteries, new electric machines, and combustion engines. Then, the possible topologies are determined: these are the different combinations of components we want to investigate. Ultimately, this results in one topology that meets all the requirements for that specific application.
The unique aspect of the MEMS algorithm is its modular structure. This allows us to compare and calculate many different combinations in a short time. The algorithm maintains the same structure for each configuration, enabling engineers to effortlessly exchange different powertrain components and try out topologies. MEMS allows for a fair comparison between different configurations, as each topology is controlled by an optimal regulator.'
TNO has calculated that this approach saves about 20 percent of time per topology in the development phase compared to conventional algorithms. With multiple configurations and reuse of components, there is an additional saving, as components do not need to be recalibrated.
Advantages of MEMS
TNO has now completed several development projects with equipment manufacturers, including major tractor and excavator manufacturers. According to Mentink, partners see a clear added value in the modularity aspect and the time savings it provides. 'This allows you to quickly gain insights into which configurations do or do not contribute to the desired result, so you can choose the right development direction in a short time. More exotic combinations can also be investigated, giving MEMS more freedom to gain new insights.'
Partners also see the benefits of applying the algorithm in the application itself. 'Throughout the entire development process, the advantage of this method continues: in the R&D phase the method saves time, and in the vehicle itself the method ensures efficiency gains and better performance.'
TNO’s focus with MEMS is on Non-Road Mobile Machinery (NRMM), such as tractors, excavators, wheel loaders, cranes, and even large mining trucks. Mentink: 'NRMM manufacturers have an enormous variety of vehicle and powertrain variations, so equipment comes in all shapes and sizes. This is where the complexity and variation are greatest, and the modularity aspect of MEMS comes into its own.'
However, MEMS can also be interesting for on-road applications. 'Legislation for trucks will also impose requirements on semi-trailers from 2030 to contribute to the joint CO2 reduction in combination with the towing vehicle. For example, by equipping trailers with an electrically driven axle. In addition to the often diesel-powered tractor unit, you then also have a trailer with a drive system, which are mechanically and electronically coupled. Our Energy Management Strategy is also interesting for this, especially if a cooling engine or solar panels are also installed.'
MEMS has now evolved from an algorithm to a complete software suite that TNO teaches its partners to use independently. Jan-Willem Sangers: 'We started developing and validating the mathematical formulation of MEMS around 2005, initially for one configuration. We then developed a start-to-end methodology around it to arrive at such a mathematical model. We have defined a process for this, which nowadays we support with a complete software suite, so our partners can go through that process smoothly on their own. We continuously expand this suite with all kinds of new components available in the market. Think of the latest electric motors, cooling units, or battery packs, but also thermal and hydraulic components. By using components from the library, the development process is even faster, as the customer can reuse knowledge and develop configurations in parallel.'
Also an onsite introductory presentation and demonstration?
TNO provides the Modular Energy Management tool to the end user under a license. Paul Mentink: 'The algorithm is an open mathematical model that the customer can ultimately apply independently in their own engineering for software development and its application in the vehicle. We first demonstrate the added value of the tool and the algorithm in a benchmark project with the customer. For example, we show performance improvements compared to their own algorithm through simulations.'
'During a multi-day on-site workshop, the customer learns to work independently with our method and software, so they can then integrate it into their R&D process. This is often followed by several projects with the customer focused on specific extensions or additional support for other applications.'
Get inspired
Fuel cells crucial for decarbonising heavy-duty transport and non-road machinery
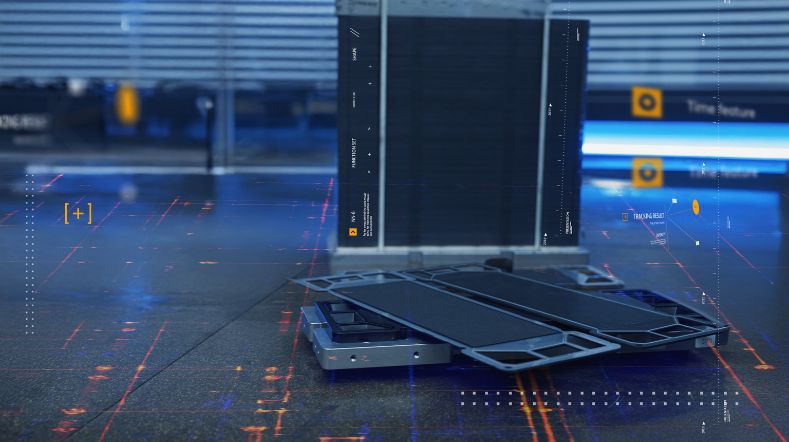
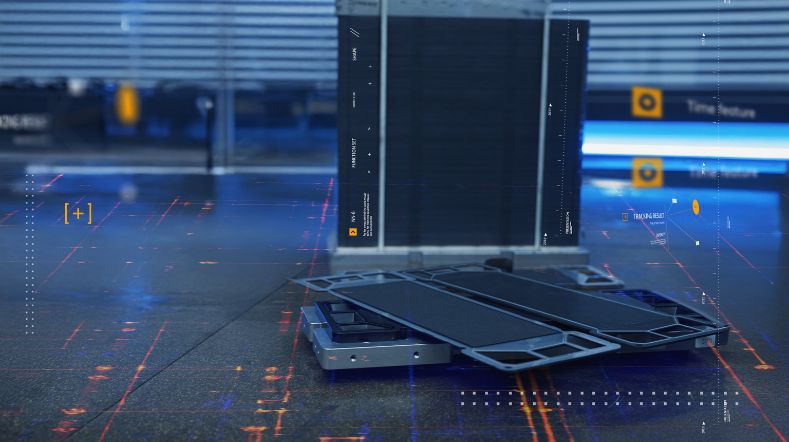
Health of electric bus batteries now measurable on-site via charger
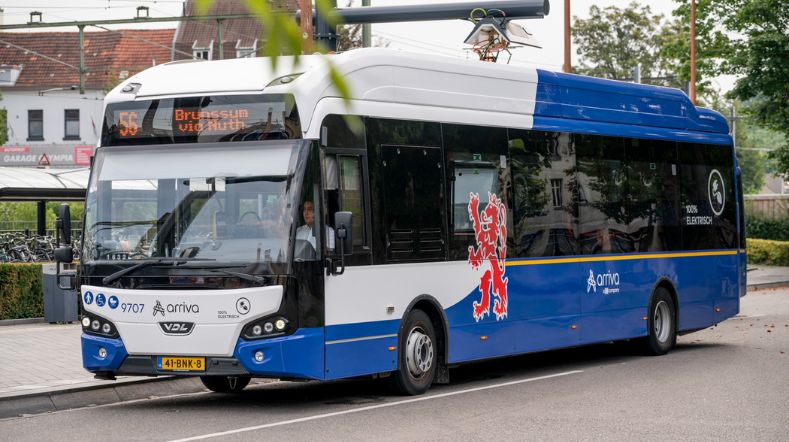
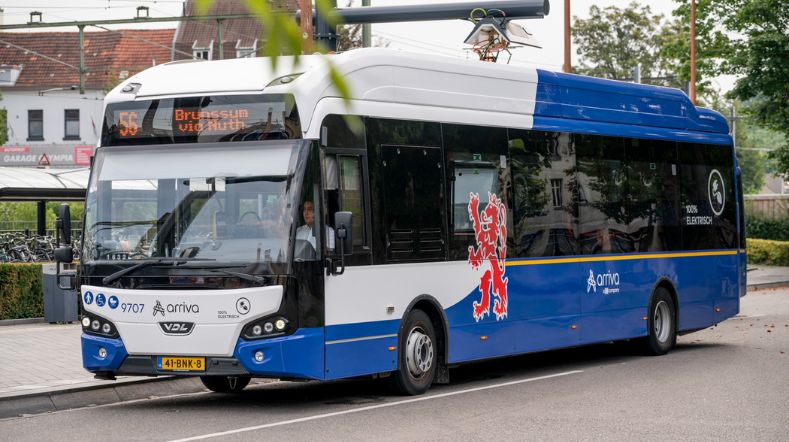
Demonstrations of automated driving and charging for logistics at Maasvlakte
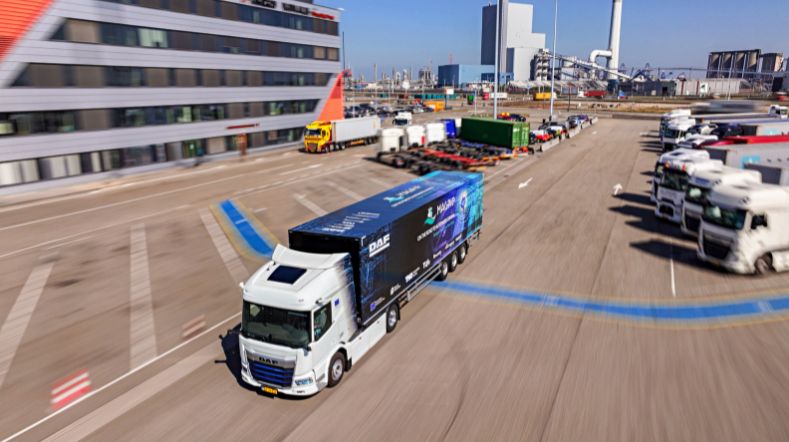
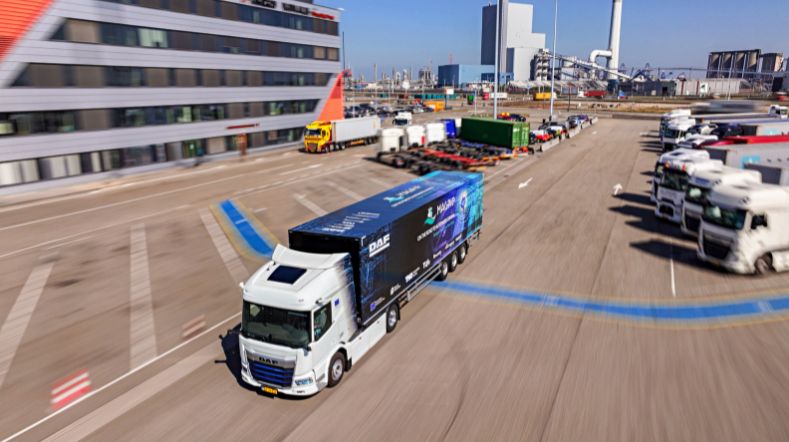
Transition co2 neutral mobility 2050
TNO accelerates electrification of logistics and construction through a deeper understanding of batteries
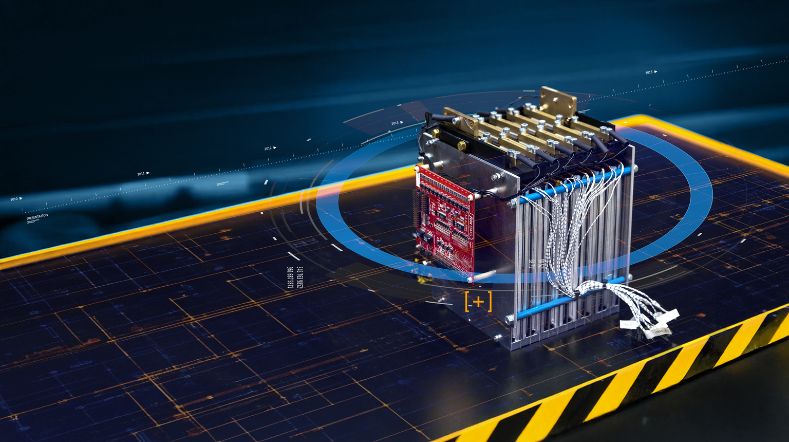
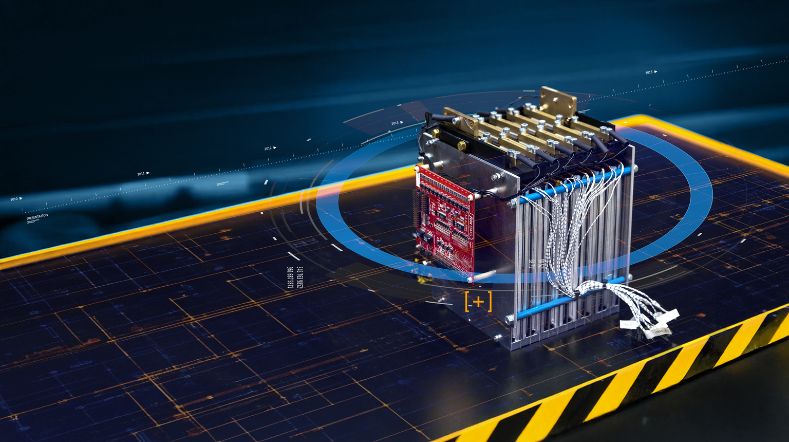