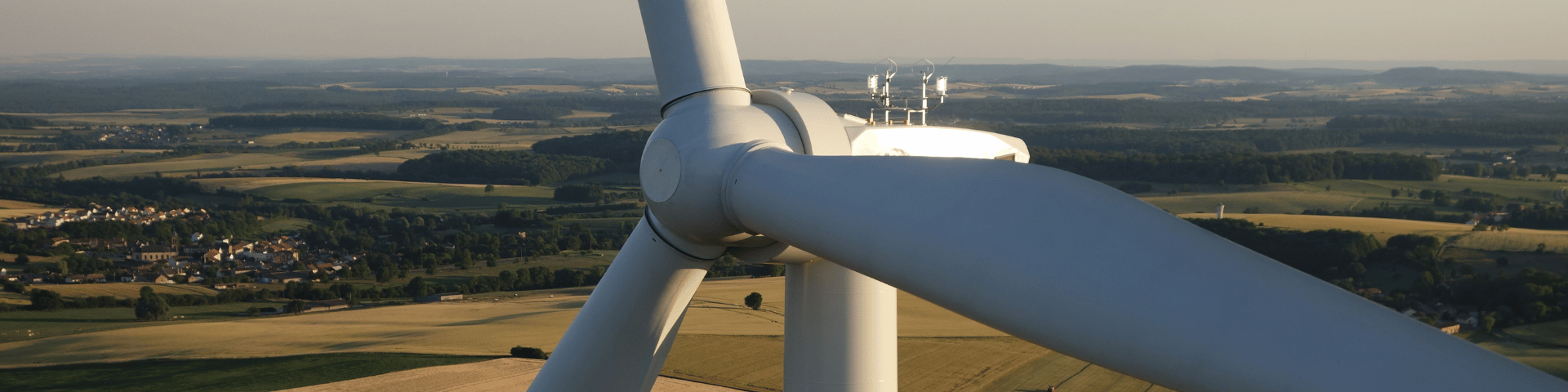
Wind of change in recycling wind turbine blades
Status project
2023 - 2026
In cooperation with
18 partners
The EoLO-HUBs (End of Life through Open HUBs) project aims to find a commercially viable and scalable solution to the looming stockpile of discarded wind turbine blades. TNO and Brightlands Materials Center (BMC) have already developed the initiatory method to recover the composite fibres and upgrade them to recyclable products. A consortium of 18 partners throughout the supply chain are joining forces to make it happen.
End of Life through Open HUBs
EoLO-HUBs is divided into three collaborative hubs. The first is tasked with recovering the glass fibre from composites using chemical reaction called green solvolysis. The second hub does the same by means of thermolysis. The third is a knowledge-sharing hub. Bundling the knowledge and ongoing research studies enhances Europe-wide interaction and offers new opportunities to develop a solution that meets the 2030 circularity goals.
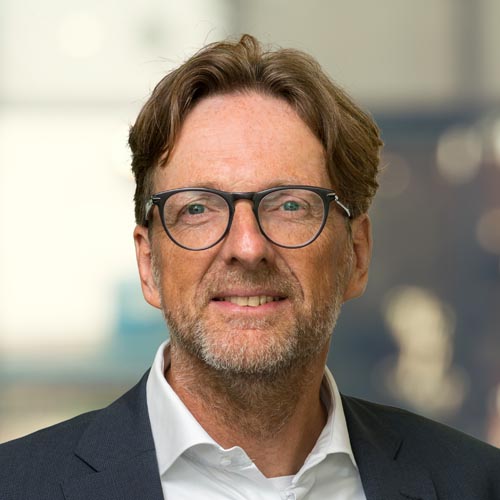
‘We will demonstrate that wind energy – and large off- and onshore wind farms in particular – not only give us green energy, but that their composite components can be fully recycled and broadly commercialised.’
Sustainable business model for industry
Harald van der Mijle Meijer, Senior Consultant for Wind Energy Technology at TNO, is excited that the EoLO-HUBs project has the go-ahead. ‘It involves setting up a platform that clearly shows the added value to potential investors. Decommissioning wind farms is a complex undertaking that goes beyond the standard practices known in, let’s say, the oil & gas industry. But after overcoming the hurdles, this innovation offers real business potential. Together with our partners, we will open demonstration sites that prove the commercial viability of recycling and upgrading the recovered fibre materials from the composites from wind turbine farms.’
Simone Mancini, Project Manager Wind Energy at TNO, emphasises the importance of the project. ‘It’s still a relatively novel and small market. Over the next years, more and more wind turbines will need to be decommissioned and replaced. This is a growing business and it is essential that we start finding solutions today rather than tomorrow.’
Creating fully recyclable products from recovered fibres
TNO is an important link in the EoLO-HUBs project, Simone explains. ‘We are developing an end-of-life tool, for example, to help industries make the most profitable or most sustainable decision. Another tool, which will be incorporated in our cutting-edge UWiSE software, is a detailed modelling tool that will allow users to accurately estimate the costs, performance and requirements of every process in the decommissioning campaign of entire wind farms.’ Part of decommissioning wind turbine blades involves upgrading the recovered fibres to usable and recyclable products.
‘We work closely with our colleagues from TNO’s joint innovation centre at BMC to that end’, Simone explains. ‘They will demonstrate the process of using the recovered fibres in new thermoplastic composite materials. The output comes in the form of pellets, which are applied in common plastic production techniques such as injection moulding in the automotive industry. This process should ensure that recovered fibres find new value as recycled materials in existing market applications.’
‘TNO and BMC are collaborating with Centro Ricerche Fiat,’ Harald adds, ‘to develop a fully recycled composite and demonstrate the benefits for industrial use. The wonderful thing is that the composite material made from the recovered fibre can be recycled again. That’s because it is a thermoplastic composite, which you can reheat and reshape for all kinds of end uses. See it as a double profit: we extract the otherwise discarded fibre from the blades and transform it into a fully recyclable product.’
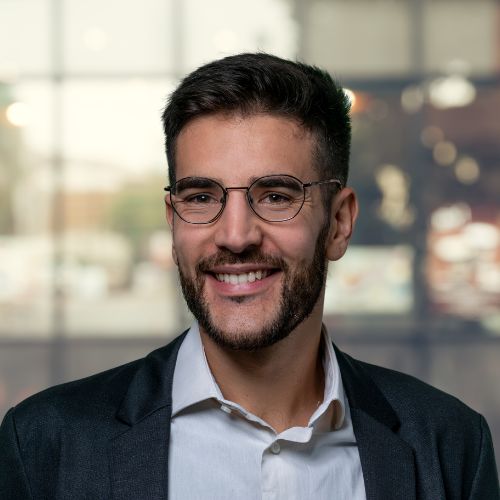
‘It’s still a relatively novel and small market. Over the next five years, more and more wind turbines will need to be decommissioned and replaced. This is a growing business and it is essential that we start finding solutions today rather than tomorrow.’
Europe-wide collaboration
The diversity of partners in the supply chain ensures that the EoLO-HUBs project goes much further than research alone. It aims to actually demonstrate the process – both through thermolysis and solvolysis – and prove its scalability for industrial application.
‘Another unique feature is the knowledge hub’, Harald says. ‘We are connected to similar studies and are very open in sharing data and knowledge. Plus we consider all socioeconomic aspects when ranking and deciding on the best process method.’
The European Union is investing almost 10 million euros in the EoLO-HUBs project as part of its Green Deal. Dutch partners alongside TNO are Jansen Recycling Group and Echt Transition Agency. But the consortium comprises forward-thinking companies, composite centres and universities from all over Europe, such as coordinating party Aitiip Technology Centre in Spain, the Fraunhofer Institute, Mitsubishi Chemicals in Germany, and other participants.
TNO expects to have the first demonstrator ready in three years to show interested parties the real potential of the recovered composites from wind turbine blades.
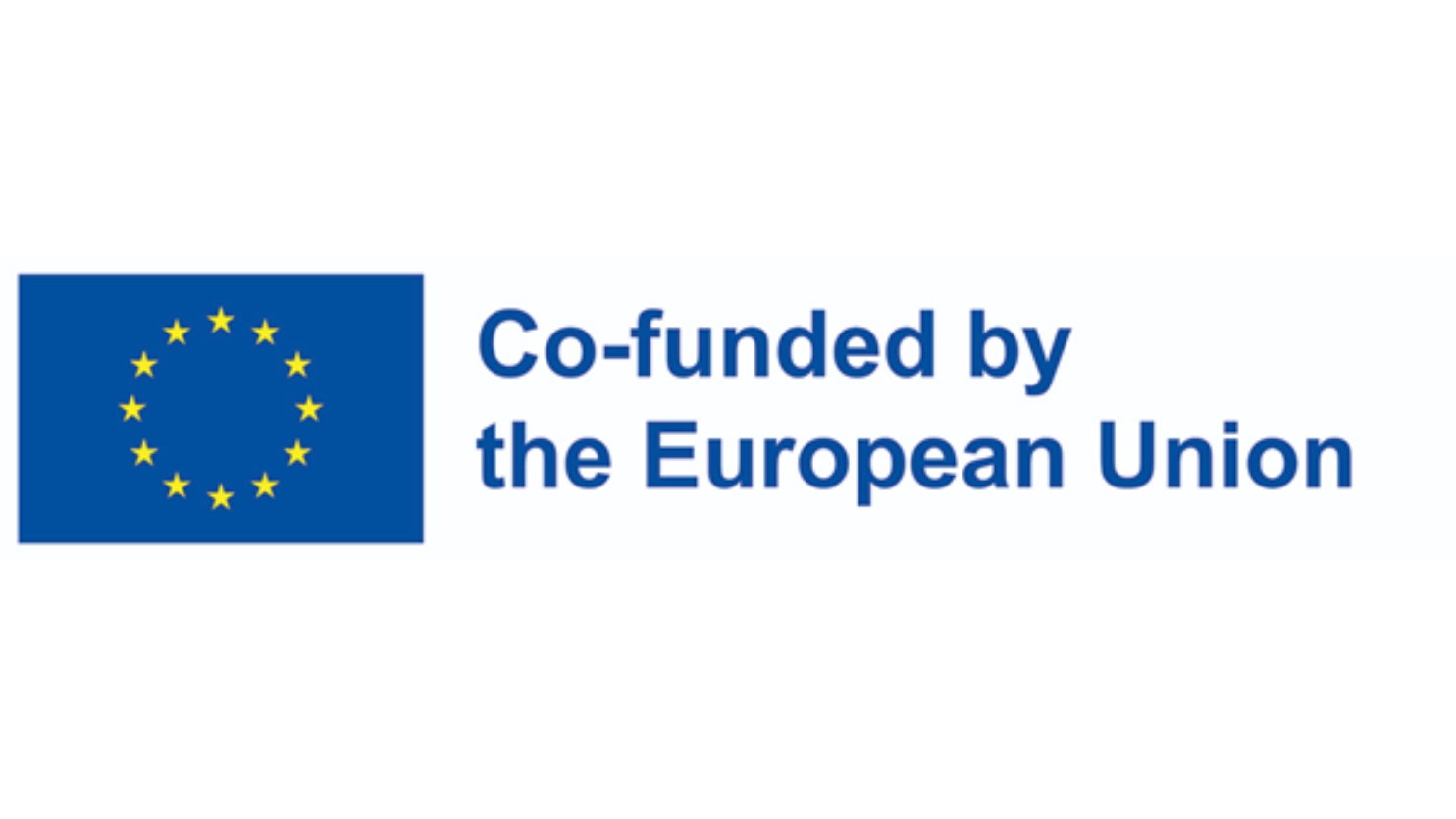
More information
Want to learn more about EoLO-HUBs?
Get inspired
First study on public perception of wind turbine circularity
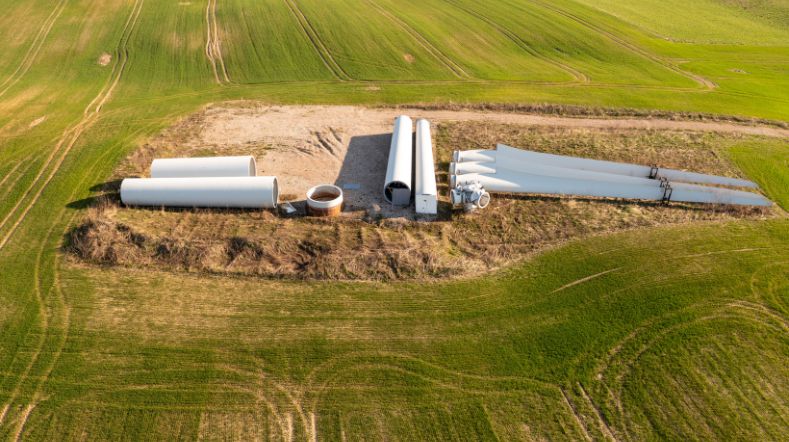
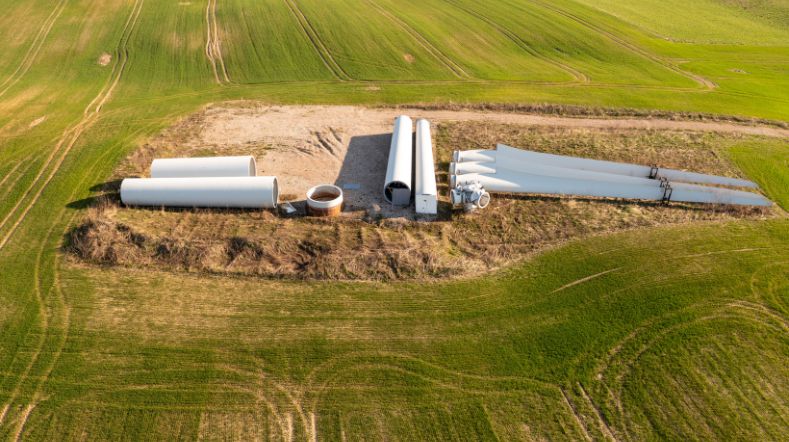
TNO innovation offers discarded wind turbine blades a circular future
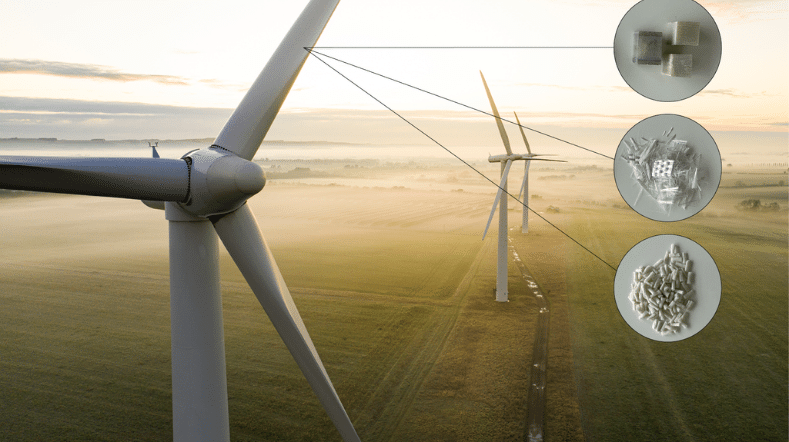
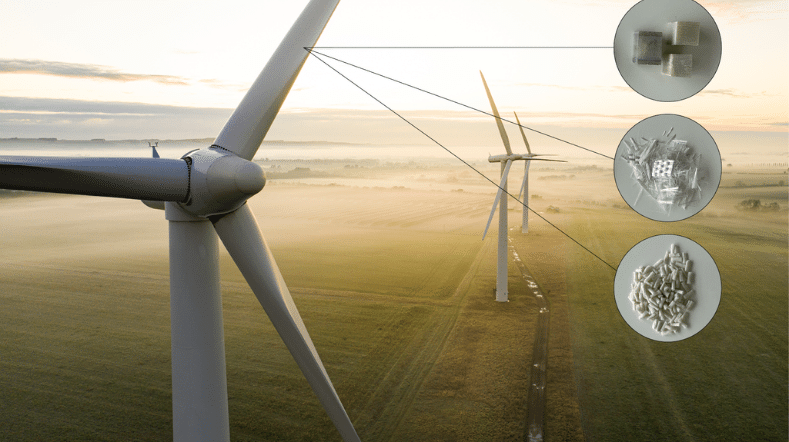
Designing sustainable wind turbines for the circular economy
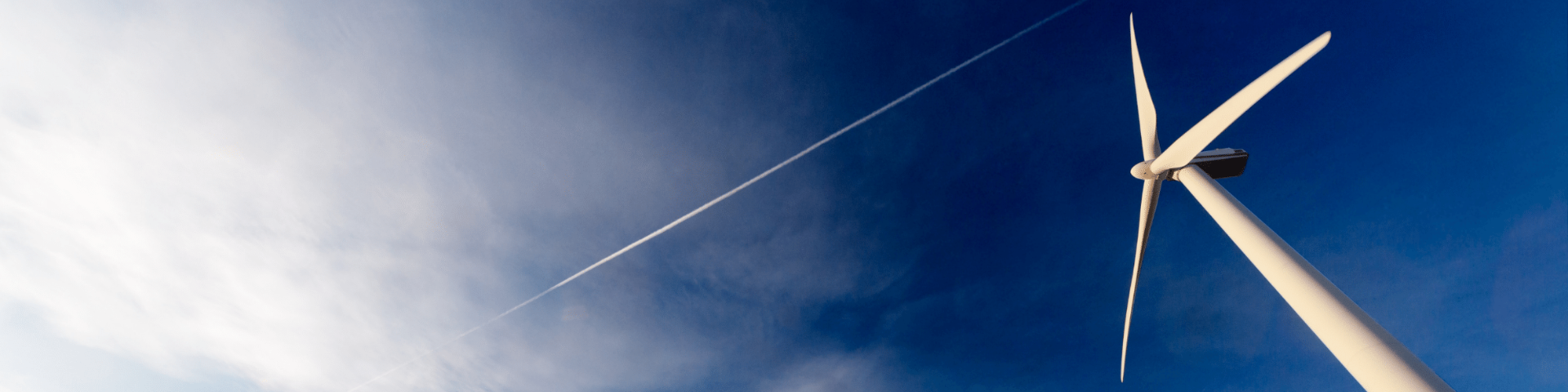
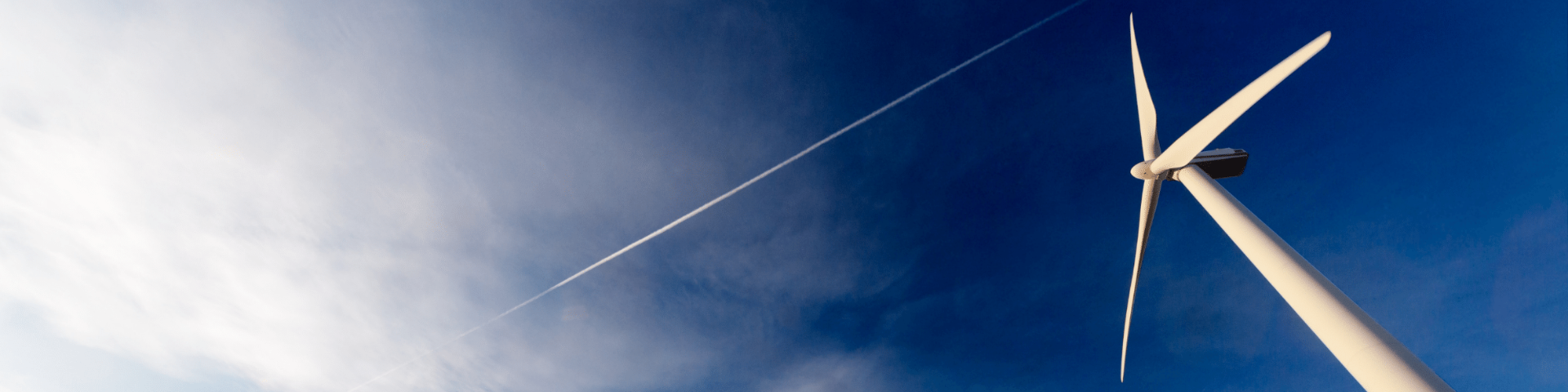