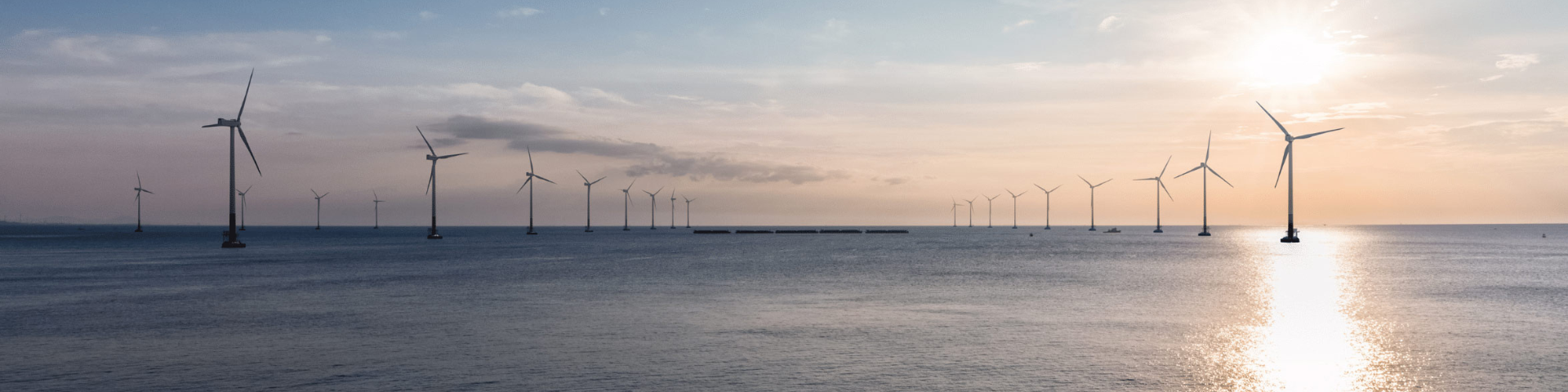
Applying robotics increases safety and reduces maintenance costs
Maintenance of wind turbines is labour-intensive and therefore expensive. There are also safety risks associated with working on wind farms, which are being located further and further away from the coast. Automation and robotisation can offer a solution here. TNO is developing and testing concepts to automate and digitise maintenance. Ultimately, it should be possible to carry out maintenance without, or at least with minimal, human intervention.
Replacing hazardous work
The technical possibilities are endless with, for example, augmented reality (AR) or virtual reality (VR) and robotics in combination with fast network connections. However, their application for these offshore activities is still in its infancy. Today, drones are able to fly around wind turbines to inspect the blades by taking pictures, but much more can be done to reduce or replace hazardous human tasks. TNO is investigating how offshore inspection and maintenance tasks can be further automated using new technologies. Here we differentiate between the turbine blades, the nacelle and the subsea foundations.
Remote viewing
We carry out tests using sensors, robots and AR. For example, we carried out a test where a remotely controlled drone flies inside the wind turbine taking recordings for inspection. The images can be assessed in real time by an onshore expert via a very fast and secure 5G connection. We have also carried out trials in which technicians in the turbine wear special glasses that record and transmit images, allowing a colleague to view these images remotely and advise on complex maintenance or repair work. In the future, it is quite conceivable that drones with robots will fly to the wind turbine to carry out maintenance.
Damage by precipitation
TNO is conducting tests with drones to identify damage to wind turbine blades caused by rain and hail. In combination with fast and reliable data communication, decisions on whether or not to carry out maintenance can be made faster and more reliably. By installing sensors at strategic points in the turbine blades, wear and tear data can be read remotely and appropriate action can be taken. This work is carried out in, for example, the AIRTub project.
Multidisciplinary research
A number of TNO disciplines come together for this research. Knowledge of drones obtained from the safety domain, of AR/VR and data communication obtained from ICT expertise, of maritime, offshore, electronics, and all of these disciplines combined. In TNO's approach, the required maintenance tasks are first identified, after which it’s established which ones can be automated and how. After weighing up efficiency, risks and costs, human labour remains preferable in some cases. By assessing all the factors carefully, there is much to be gained, both financially and in terms of safety.
Get inspired
X-ray drone technology and digital twin to detect sub-surface defects within turbine blades
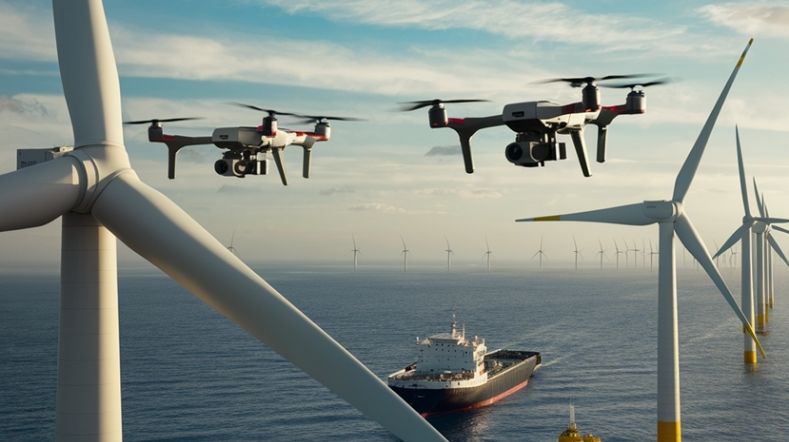
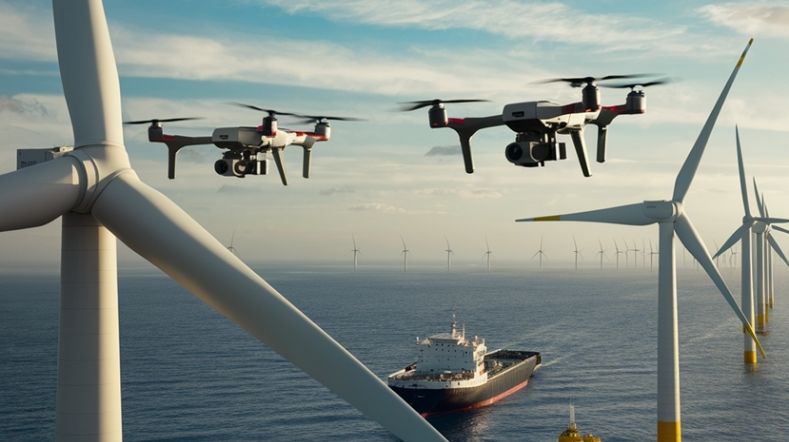
Advancing wind turbine blade reliability through innovative monitoring and digital twin technology
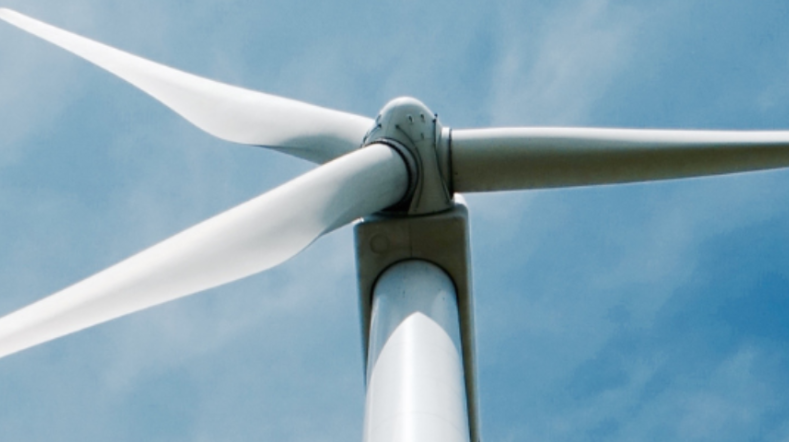
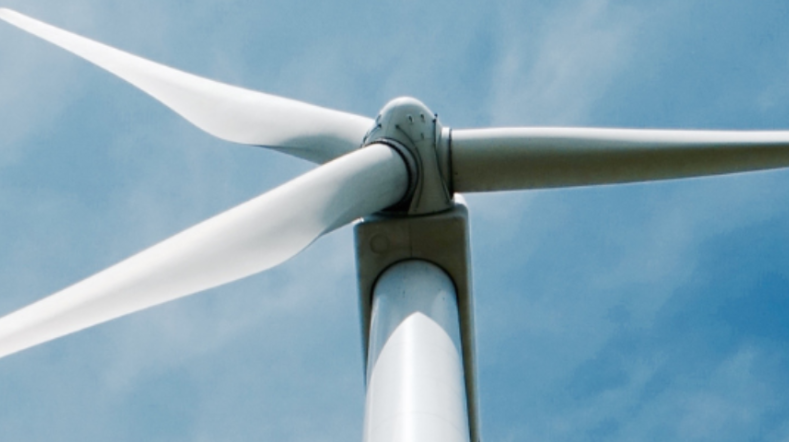
Consortium explores positive wake effects of floating wind turbines
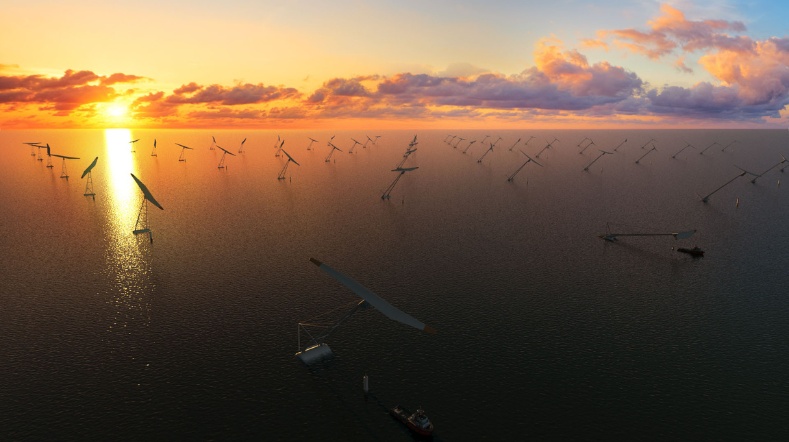
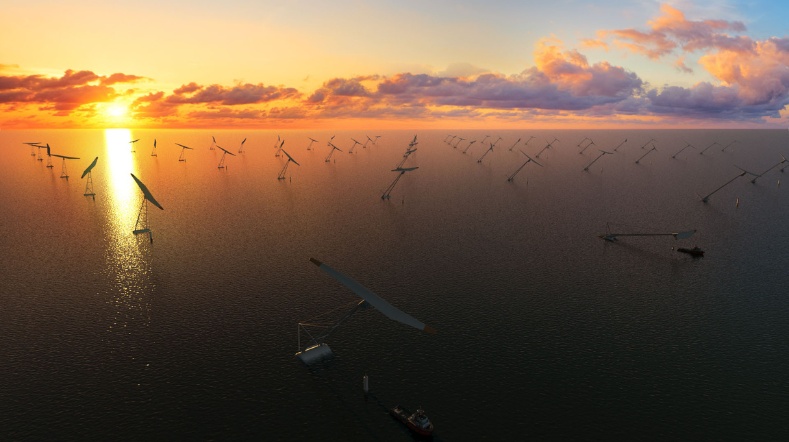
Wind turbine inspections with autonomous drones and digital twin modelling
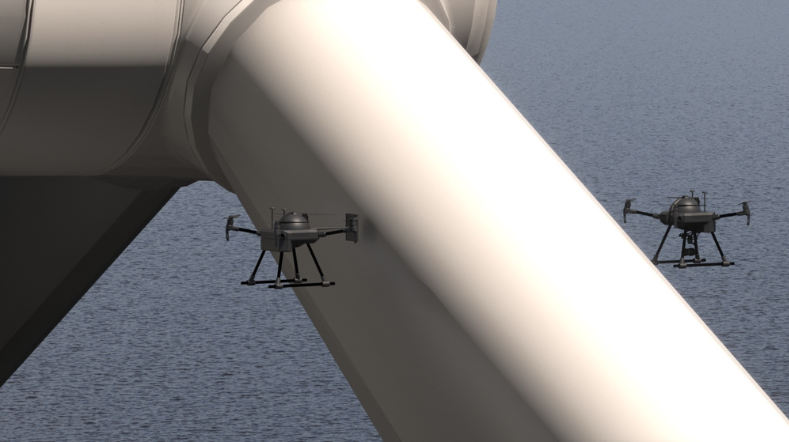
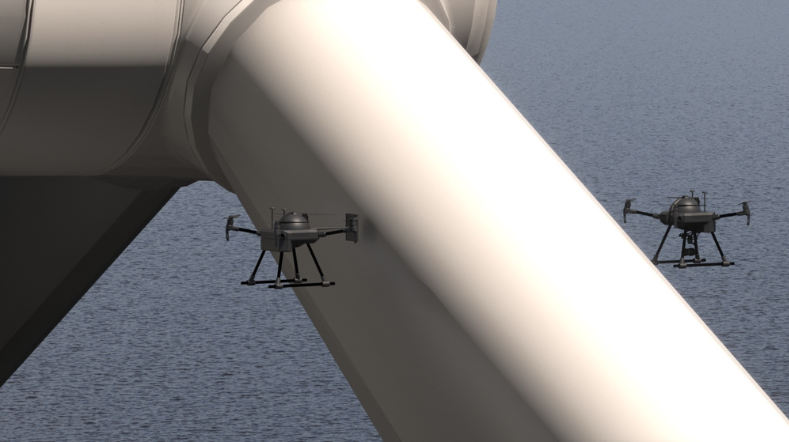