Colorado Flow Loop: Unique test facility for safe and reliable transport and injection of CO2
CO2 capture and storage is crucial in combating climate change, but transport presents unique challenges. At the advanced Colorado Flow Loop test facility, we perform research into these challenges. The facility offers the flexibility to research any process of flowing CO2 relevant to CCS at relatively low cost. The Colorado flow loop contributes to more reliable, efficient and cost-effective transport solutions for the industry and ultimately assist the industry in meeting their climate goals.
What is the Colorado Flow Loop?
The Colorado Flow Loop is a cutting-edge outdoor test facility at TNO in Rijswijk, the Netherlands. It was specifically developed for the research of flowing CO2 in processes or equipment in the transport and injection of CO2.
The facility has the capability to perform tests on pure CO2, or in combination with certain contaminants (CH4, CO, N2, H2, Ar). This facility stands out due to its high flexibility and low-cost design, allowing for a wide range of experimental setups.
The added value of the Colorado Flow Loop
The Colorado Flow Loop contributes to the safe and reliable transport and injection of CO2 through experimental research into operational challenges in the field. It also validates predictive models and CFD calculations, ensuring accurate and reliable data for CO2 transport and storage solutions.
Some partners about the facility:
- Coen Rensma (Harbour Energy): 'The TNO Colorado flow loop will help the industry to build knowledge on more efficient and safe transport and injection of CO2. I believe the contributions from TNO as an independent research organization will also greatly help towards public acceptance.'
- Wouter Schiferli (EBN): 'There has to be a knowledge base in place outside of oil & gas companies to build a knowledge base on CCS specifically for the Netherlands, which is unique with depleted oil and gas fields. The TNO facility fits into this larger goal to create that sort of environment.'
- Ruud Henkes (Shell): 'It is very important to Shell to have a CCUS research environment embedded in the Netherlands, where many operators and a solid scientific community are close by. It is of further importance to confirm if models developed in the past are relevant and applicable to the CO2 market.'
Test section design on request: high flexibility at low cost
The design of the flow loop is aimed at maximum flexibility: any type of process, geometry, or equipment can be researched through the design and construction of tailor-made test sections. The low viscosity of CO2 allows for the reproduction of field flow behavior and patterns in smaller pipes, making the flow loop both flexible and cost-effective.
Topics of research
The flow loop is currently used for research into:
- Dynamic forces on bends from multiphase CO2 flow
- Pressure and temperature effects from the occurrence of vapour collapse
- The effects from contaminants on pressure losses in horizontal and vertical pipe flow
- The flow of CO2 through porous media
- Flashing and choking effects from CO2 flow through (choking) valves
Key components
The flow loop consists of a CO2 process module and a (customized) test section. The process module controls the flow, pressure, and temperature of the fluid that flows into the test section. The process module includes a separator, pump, compressor, heat exchangers, various control valves and instrumentation.
Data acquisition
The process conditions in the CO2 conditioning system are monitored and controlled by a central computer system. The measurement section can be equipped with various types of pressure sensors (absolute, differential, dynamic) and temperature sensors.
Furthermore, the facility includes the possibility to survey the (bulk) density of the CO2 fluid by means of non-intrusive gamma-ray densitometry. Measurement data from the test section can be sampled by several modules:
- TRION 1850 Multi 4D multifunctional modules with high-speed simultaneous sampling up to 100 kHz
- 8-channel high-precision voltage CPAD3-V8 modules at 100 Hz
- 8-channel high-precision temperature XR-TH8 thermocouple modules
Specifications
- Pipe material: Stainless steel AISI 316/316L
- Fluid: pure CO2 or with any combination of contaminants CH4,CO,N2,H2,Ar
Design pressure 100 bar - Temperature range -40 ˚C to 40 ˚C
- Compressor 23 kW mass flow up to 0.5 kg/s
- Pump 18.5 kW Bran Luebbe double acting diaphragm metering pump, differential pressure 1.5-40 bar
Collaborate?
Are you involved in the development or implementation of a CCS (Carbon Capture and Storage) project? Do you have concerns or questions about CO2 transport and storage?
We are happy to think along with you. Discuss your challenges with us, start a CO2 research project, or develop a research proposal. Together, we contribute to sharing knowledge through the CCS network.
Get inspired
Scaling-up electrochemical technologies for renewable ethylene production
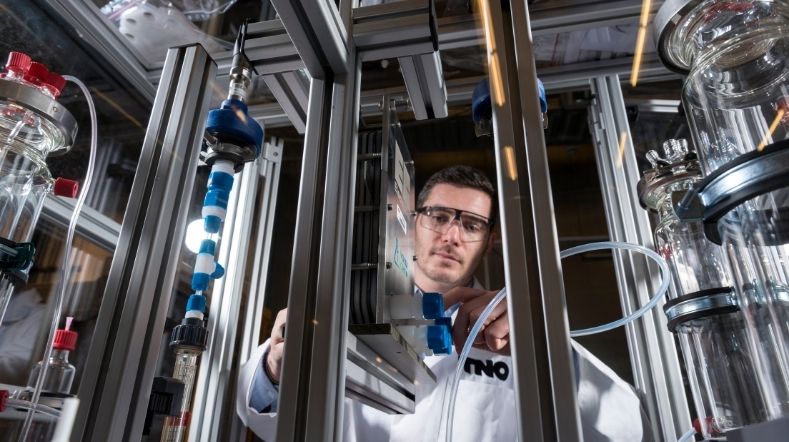
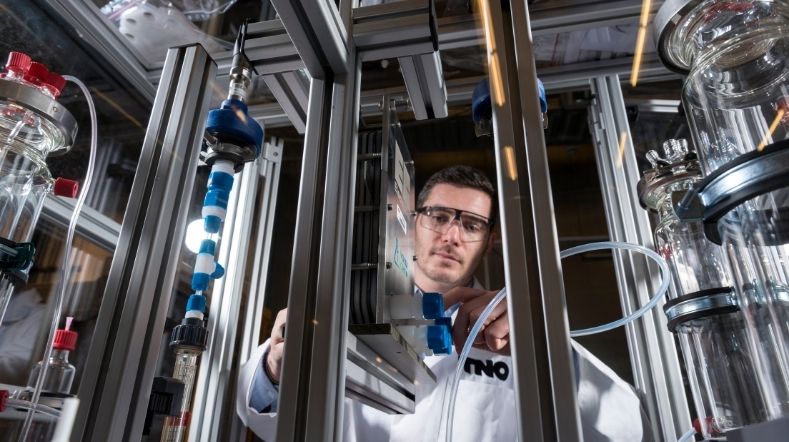
CO2 infrastructure and transport


Carbyon: the TNO spin-off innovating in CO2 filtration technology
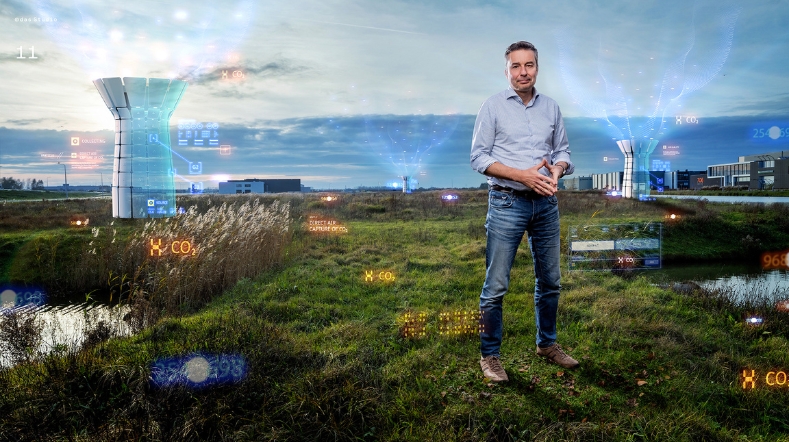
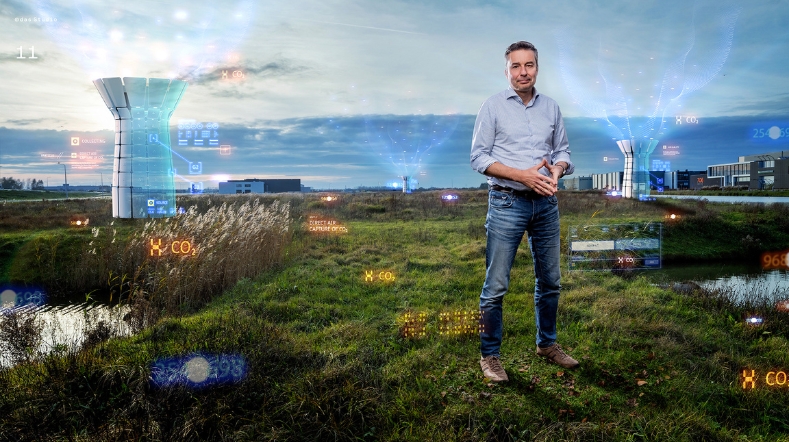
TNO’s next generation biorefinery accelerates material transition
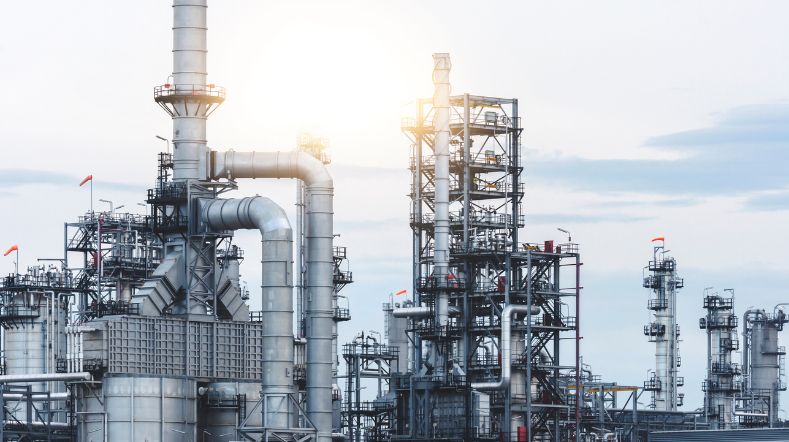
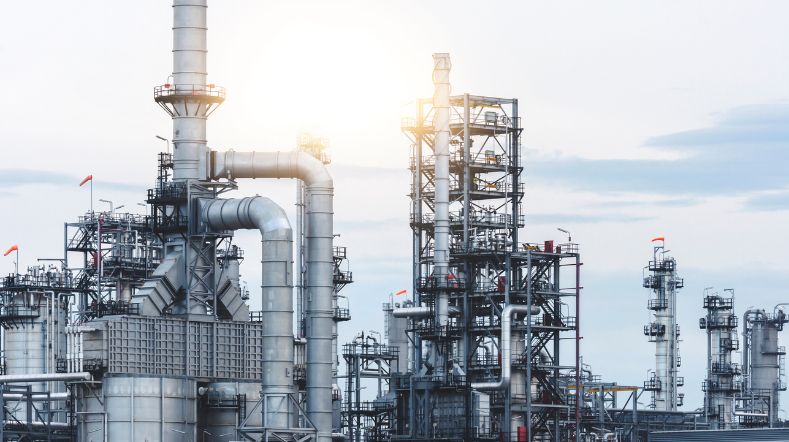
Port of Rotterdam as a key European hub for sustainable carbon
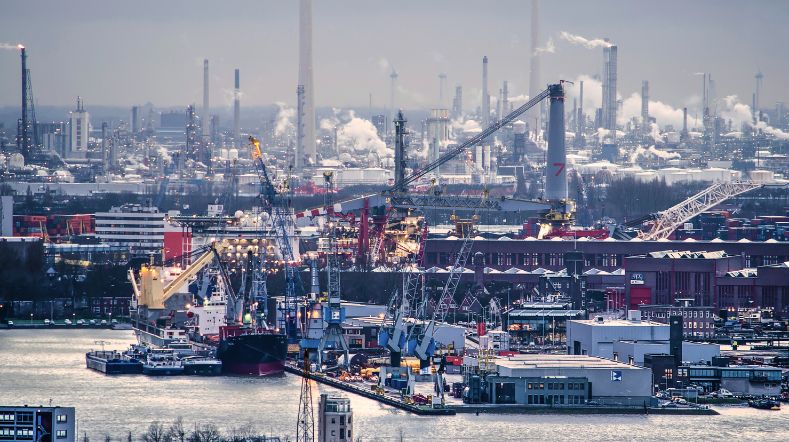
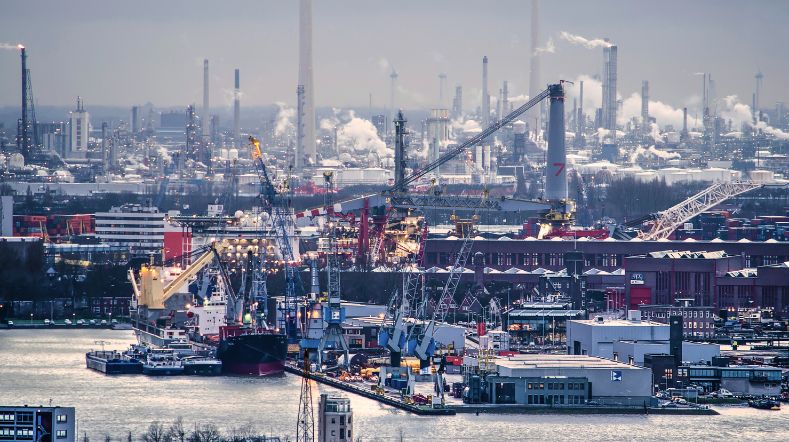