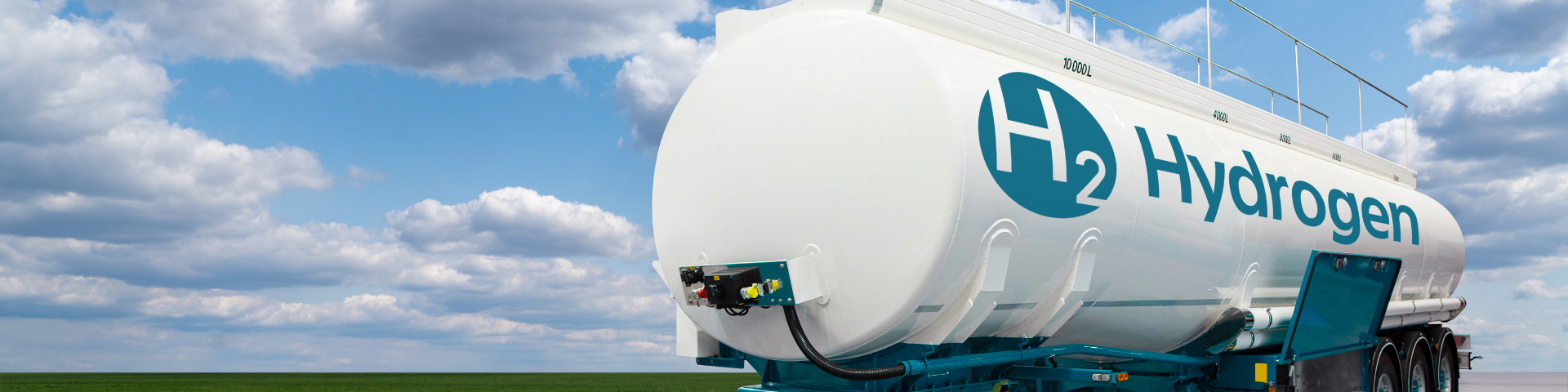
From blue hydrogen to green hydrogen
Hydrogen plays a key role in the energy transition because its use does not release any greenhouse gases into the air. Green hydrogen is not yet available in large volumes and is still expensive. Blue hydrogen is a cheaper alternative in which the CO2 released during production is stored underground.
What is green, grey and blue hydrogen?
In order to differentiate between different production methods of hydrogen the same molecule was assigned different colours. Just as energy suppliers offer grey and green electricity, companies also produce grey and green hydrogen.
Green hydrogen is produced by splitting water molecules (H2O) into hydrogen (H2) and oxygen (O2) by electrolysis. Only when the electricity required for this comes from renewable sources is it called green hydrogen.
With grey hydrogen, natural gas (CH4) and steam (H2O) are split into hydrogen (H2) and carbon dioxide (CO2). At present, the carbon dioxide released in the production of grey hydrogen escapes into the air. Storing this greenhouse gas underground prevents additional global warming. The hydrogen gas produced in this way is called blue hydrogen.
Want to know more about hydrogen?
Read the 15 things you need to know about hydrogen
How does the production of blue hydrogen work?
In principle, the production method of blue hydrogen is no different to grey hydrogen. The industrial 'steam methane reformers' (SMR) or 'auto thermal reformers' (ATR) that currently produce grey hydrogen can also produce blue hydrogen. However, more efficient systems for separating synthesis gas are now available. Such as our SEWGS technology, which not only saves costs, but also removes more CO2.
The SEWGS process combines 2 process steps in one reactor: a water-gas-shift reaction and CO2 capture with a solid absorber. The combination ensures a more energy-efficient conversion, and an almost total removal of CO2.
We have already successfully demonstrated the operation of the SEWGS process on an industrial scale at Swedish steel company SSAB. In the European Union-supported STEPWISE project, a SEWGS plant processed 800 cubic meters of blast-furnace gas per hour from one of the steel mills.
Carbon capture and storage
The biggest challenge for blue hydrogen is the transport and underground storage of the captured CO2. This is also called 'carbon capture and storage' (CCS). The CO2 is piped to empty gas fields, and the gas is injected into deep underground sandstone layers. The CO2 can also be used as a nutrient in greenhouses, or as a raw material for chemical products and plastics. This is called carbon capture and usage (CCU).
Cost of producing blue hydrogen
Blue hydrogen currently makes a greater contribution to a rapid and affordable energy transition than green hydrogen. Green hydrogen is only truly sustainable if the electricity for the electrolysis process comes from renewable sources. At the moment, there is still too little green electricity available. Moreover, electricity is twice as expensive as natural gas. The high cost of the electrolyzers that split the water also makes this technology less attractive for the time being.
Blue hydrogen remains cheaper than green in all scenarios and is the only form of hydrogen that directly reduces CO2 emissions. There is enough natural gas to last for years, and residual gases from refining or biogas, for example, can be split into hydrogen and CO2 in the same way.
However, it is expected that towards 2050, the supply of green electricity will increase and electrolyzers will become cheaper through innovation and mass production. Until then, blue hydrogen is paving the way for a mature, affordable hydrogen market and infrastructure.
Blue hydrogen projects
Meanwhile, several parties are looking into the possibilities of blue hydrogen and CCS.
This is how H-Vision, a partnership between TNO and the Rotterdam industry, wants to quickly achieve a significant reduction in the amount of CO2 with blue hydrogen. Companies such as BP, Shell and ExxonMobil want to make large-scale blue hydrogen production possible.
Part of the plan is the The Porthos project that will transport captured CO2 by sub-sea pipelines to a gas production platform in the North Sea. From the platform, the CO2 is pumped into an empty gas field. Porthos was awarded a subsidy by the Dutch government that may amount to as much as EUR 2 billion.
In the North Sea Canal area, a consortium of which we are a part is also investigating the feasibility of CCS by the name Athos. Consortium partner Tata Steel can use blue hydrogen in the production of steel. Moreover, the company is able to produce blue hydrogen from its own process gases generated by burning coke.
The H2Gateway Consortium unveiled plans for a hydrogen facility. These plans focus on a blue hydrogen plant in Den Helder. The Port of Den Helder cooperates with the Port of Amsterdam and Groningen Seaports in Hydroports with the aim of contributing to the optimisation of infrastructure for the hydrogen economy.
Get inspired
The Netherlands takes the lead in development of third-generation electrolyser


North Sea countries unite forces to accelerate offshore hydrogen production
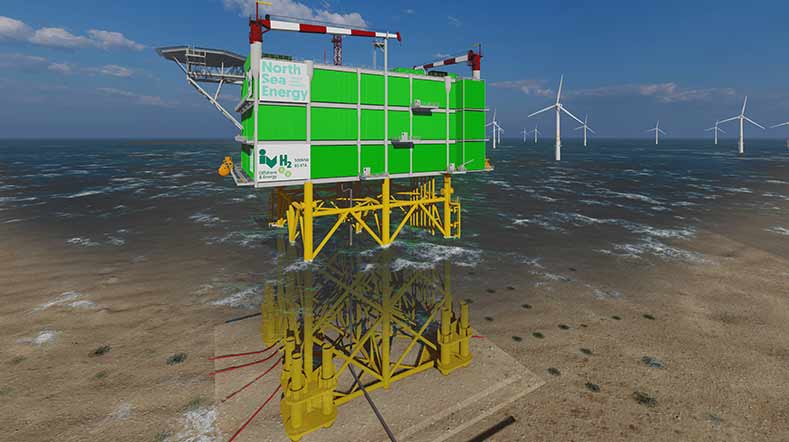
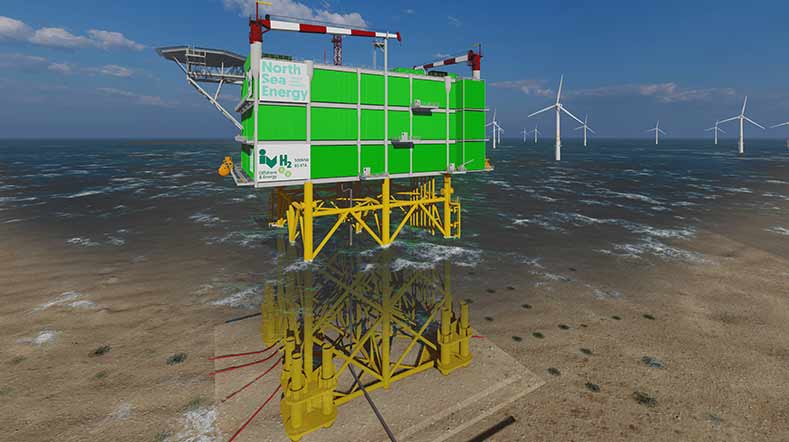