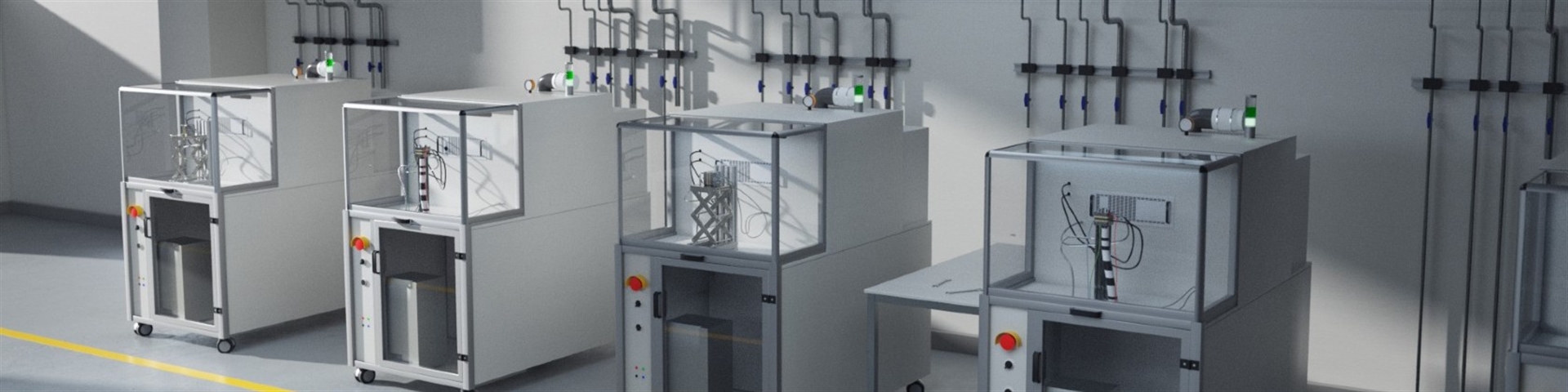
Optimising hydrogen production using electrolysis
Today, we emit a large amount of CO2 during the production of hydrogen. Much remains to be done to stimulate the production and use of green hydrogen, produced entirely from sun and wind. Electrolysis, the splitting of water into oxygen and hydrogen, with electricity from wind and sun is the main option.
We are working in various ways on optimising and reducing the cost of producing green hydrogen. Electrolysis is a proven technology. But there are still several challenges and opportunities for the high-tech manufacturing industry for its large-scale deployment.
Scaling up electrolysis by a factor of a thousand
The capacity of the electrolysers, which we are currently installing in subsidised pilots, is no greater than 1 to 10 megawatts. To supply our country with CO2-free hydrogen, we need to move towards gigawatt-scale electrolysis. This means scaling up by a factor of a thousand. Once these electrolysers are in place, we should use them preferably:
- in sectors that are difficult to make sustainable, such as the steel industry, heavy road traffic, aviation and shipping
- for supplying electricity during periods without wind or sun
- to integrate the large amount of wind at sea into our energy system by converting some of it into hydrogen
Drastically reducing costs
Also, the cost of producing green hydrogen is still 2 to 3 times too high for it to be able to compete with grey hydrogen produced from natural gas. The comparison with today's natural gas, without CO2 capture, is no longer relevant in the long term because it releases enormous amounts of CO2.
The electrolysers need to come down in price because they are in use only part of the time, solely for renewable electricity. In the case of offshore wind, this is approximately 4,000 hours a year. We are working with manufacturers and suppliers on new components, alternative materials and circular designs to significantly reduce costs and increase lifespan. This would remove the barrier to large-scale production of sustainable hydrogen. Would you, as a manufacturer or supplier, like to participate? Then don’t hesitate to contact us.
Breakthrough electrolyser development: 200 times less iridium needed
Researchers at TNO have been the first to develop a method that will require 200 times less iridium where a performance of 25% - 46% of the current generation of electrolysers can already be achieved.
Research and pilot plants
In the Gigawatt Electrolyser project, we are working with companies and universities in our country and beyond to design a new electrolyser. It should be built before 2030.
In Groningen we are working on the Hydrohub. This is an open research centre where 13 parties including the Institute for Sustainable Process Technology (ISPT) and TNO work together to optimise and scale up electrolysis.
In the EU project H2FUTURE, we are closely involved in a demonstration project. Here, a 6-megawatt PEM electrolyser was installed at an Austrian steel company.
In Petten, we have the largest hydrogen research facility in Europe: the Faraday laboratory. Faraday is an open innovation lab focused on optimising low temperature (PEM, alkaline, AEM) and high temperature (SOE) electrolysis technologies. In the Faraday laboratory, we work on technological breakthroughs for upscaling. There is close collaboration between the Hydrohub in Groningen and companies in the chain that have materials and components tested here and which they continue to develop together. This means that they don't need to invest in test facilities themselves.
Avantium and TNO have joint forces in a partnership in manufacturing electolyser test stations to accelerate production Green Hydrogen. Under the partnership with TNO will unlock and deliver technical knowledge and credibility - including design and software – on single-cell and multi-cell lab-scale electrolysis test stations. With this knowledge, Avantium will manufacture, further develop and improve, and commercialize these electrolyser test stations to customers worldwide. This will allow Avantium R&D Solutions to accelerate its electrolysis offering.
Electrolyser production: opportunity for Dutch manufacturing industry
Hydrogen is one of the pillars of the energy transition and can be the growth engine for a new economy. The Netherlands is leading the way internationally as a supplier of electrolysers. This emerges from an exploration we did together with FME, the entrepreneurs' organisation for the technological industry. But there is still some way to go to achieve this. Currently, the Netherlands lacks a fully-fledged industry that can produce electrolysers on a large scale.
Read the report
Read the follow-up report where TNO in the Voltachem programme outlines a plausible future in which the improvement and upscaling of electrolysis technology go hand in hand. The technology generations presented are by no means self-evident. They represent opportunities that, in order to manifest, must be addressed.
Get inspired
Hydrogen in the energy system: The future of sustainable energy in the Netherlands and Europe
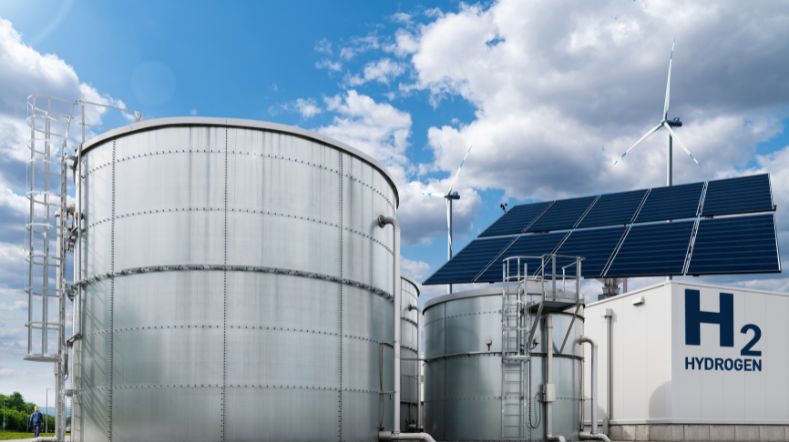
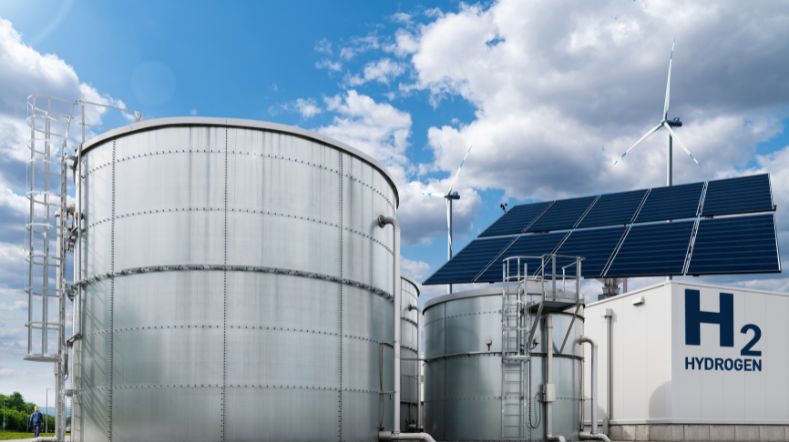
NORCE and TNO are entering into a strategic partnership on hydrogen developments
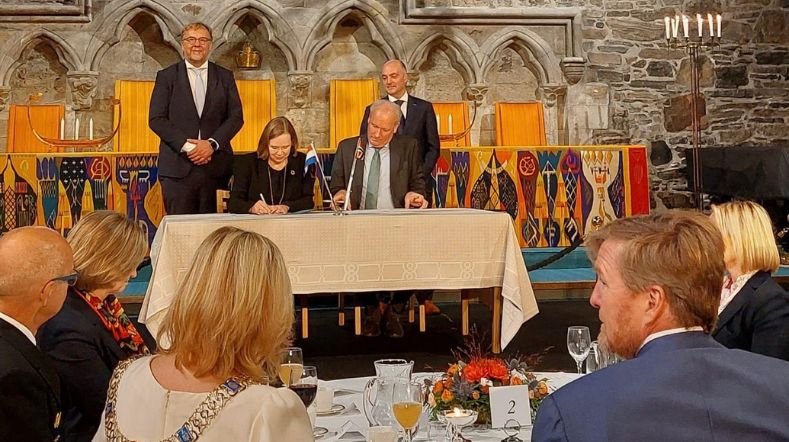
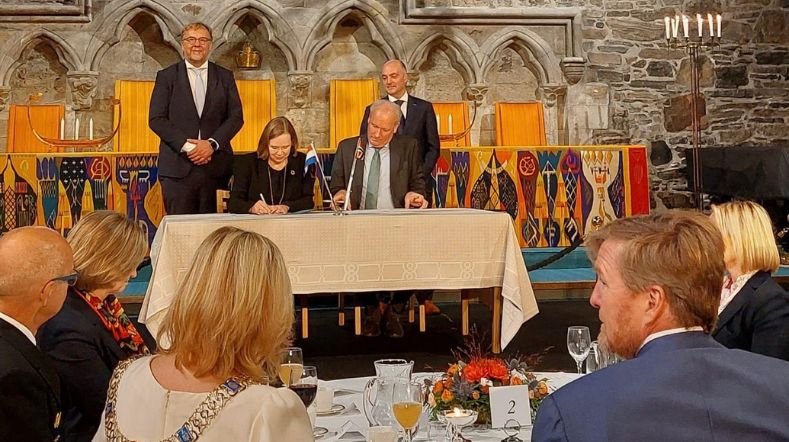
Dutch consortium participates in EU research project on large-scale hydrogen storage in depleted gas fields
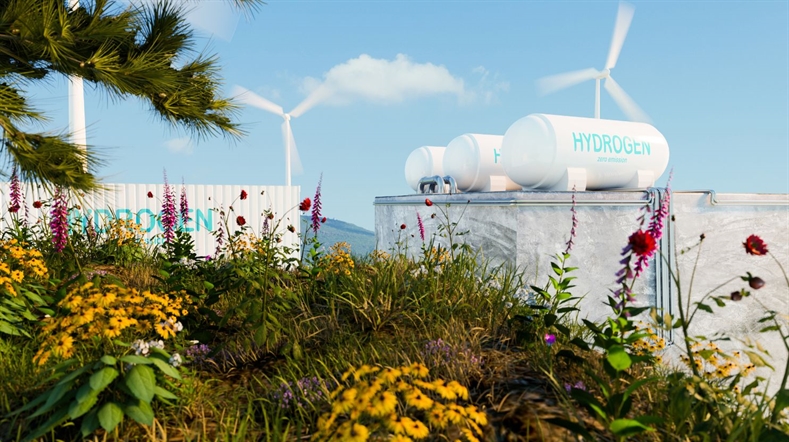
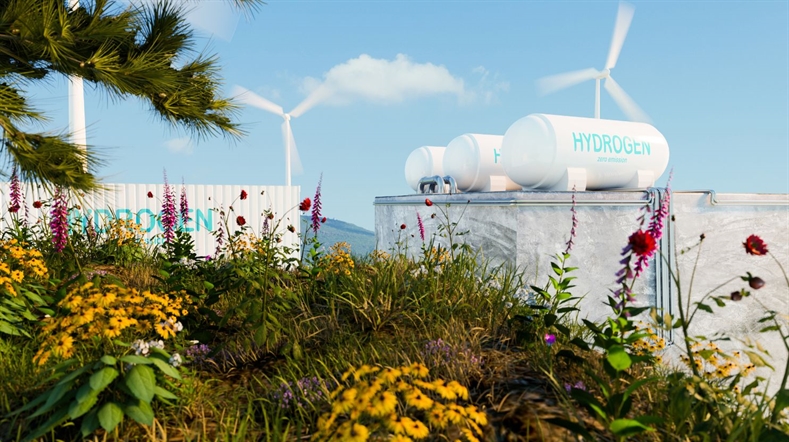
Underground hydrogen storage
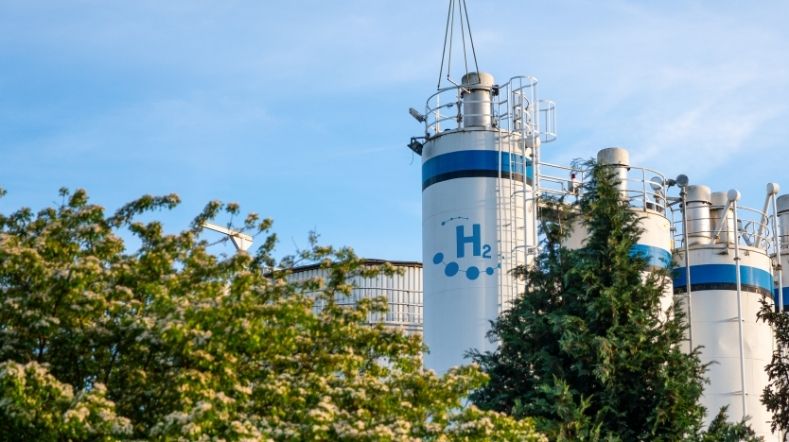
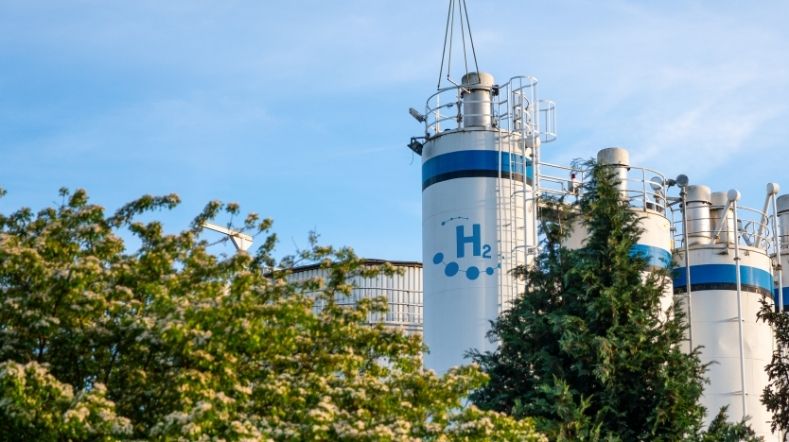
Collaboration TNO and Elcogen for development Solid Oxide Electrification Technology in Europe
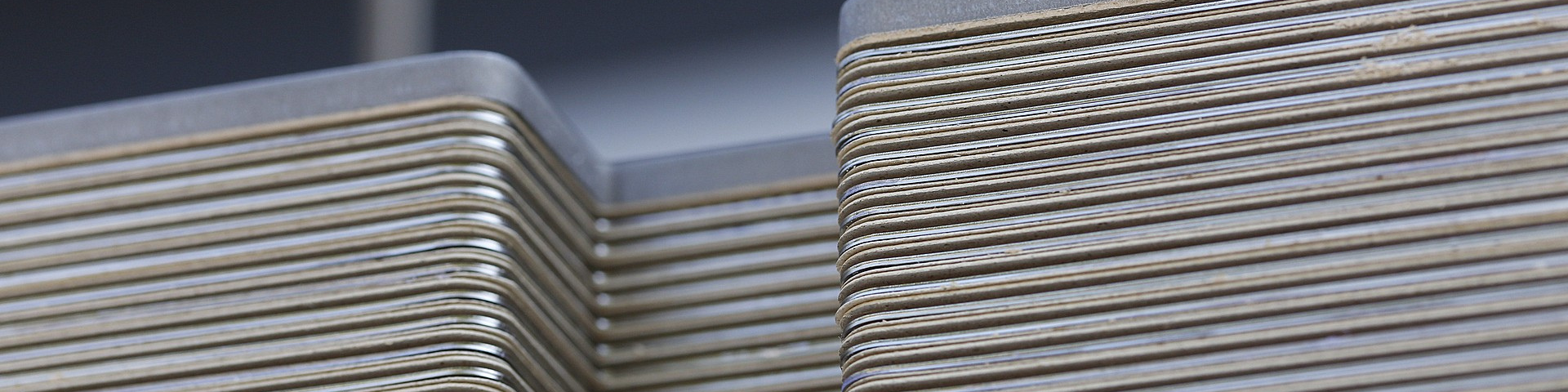
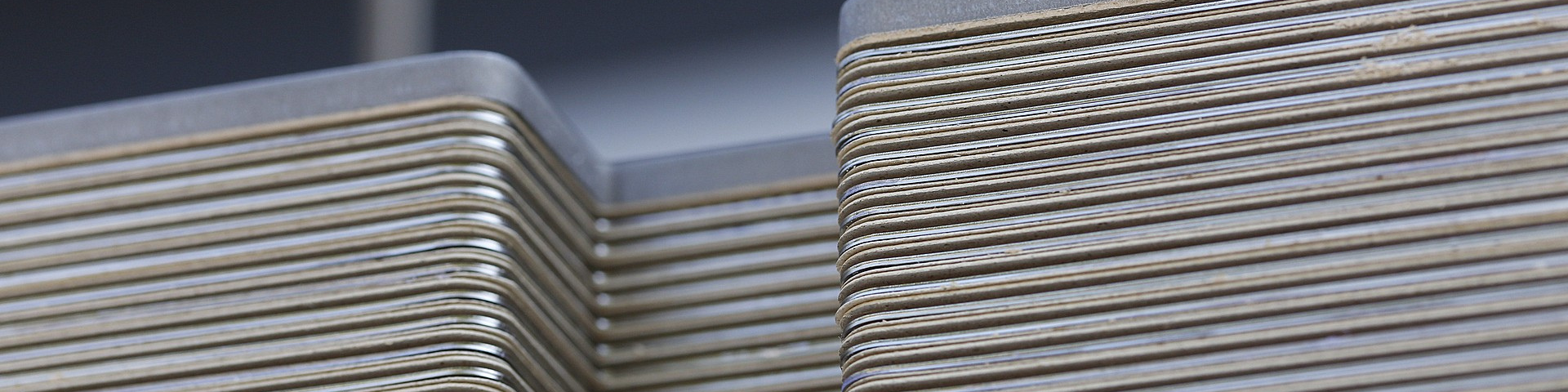