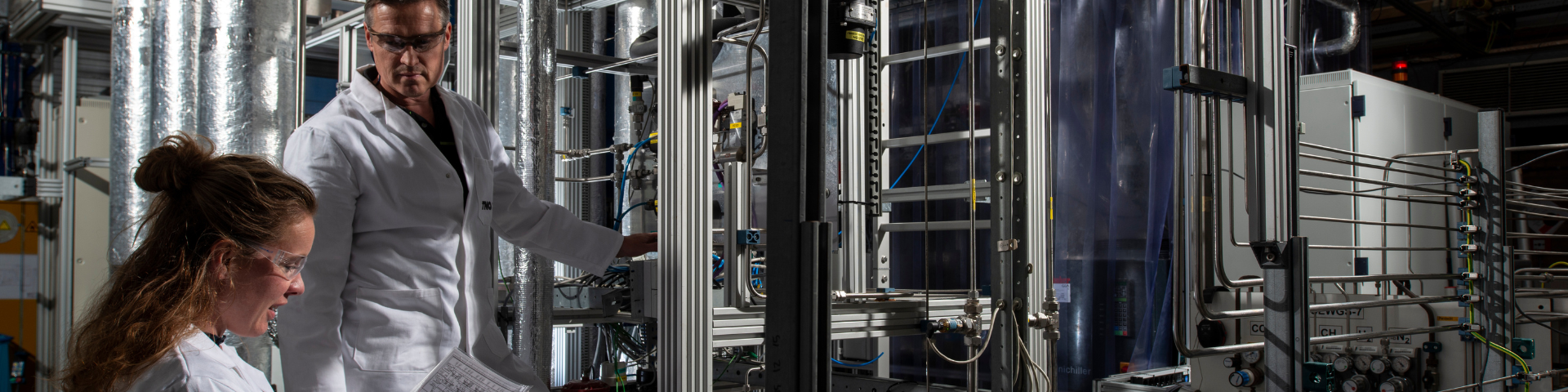
SEWGS: revolutionary technology for CO2 reduction
To make existing industrial production processes cleaner, we developed the SEWGS revolutionary platform technology. With it, you can capture CO2 very efficiently and create blue hydrogen at the same time, which is ideal for industrial residual gases and synthesis gas. This allows the industry to produce hydrogen more cheaply, more energy-efficiently, and on a larger scale than is currently possible with green hydrogen.
How is CO2 created by industry
Nearly all organic substances, both fossil fuels and agricultural waste streams, for example, can be converted into synthesis gas through gasification. This is a mixture of carbon monoxide (CO) and hydrogen gas (H2). Synthesis gas is also created as a by-product in steel production and oil refining. Until now, the industry has been using the gas as a fuel or input for other processes. The disadvantage is that the carbons in the gas enter the atmosphere in the form of CO2.
SEWGS: Sorption Enhanced Water Gas Shift
It is possible to transform and separate synthesis gas in such a way that blue hydrogen and CO2 remain. Blue hydrogen is hydrogen from hydrocarbons, but without CO2 emissions. Industry can use the blue hydrogen as a base material or fuel. The carbon dioxide can be used as a base material for various chemical products, or can be stored underground.
We developed the Sorption Enhanced Water Gas Shift (SEWGS) process for this purpose. This revolutionary combination technology converts synthesis gas into hydrogen and carbon dioxide. The SEWGS process also splits carbon dioxide from hydrogen gas in the same reactor. The combination ensures a more energy-efficient conversion and the virtually complete removal of CO2.
Webinar SEWGS
To make existing industrial production processes cleaner, TNO has developed a technology that captures CO2 very efficiently while producing hydrogen. Watch the webinar and learn more about the SEWGS technology.
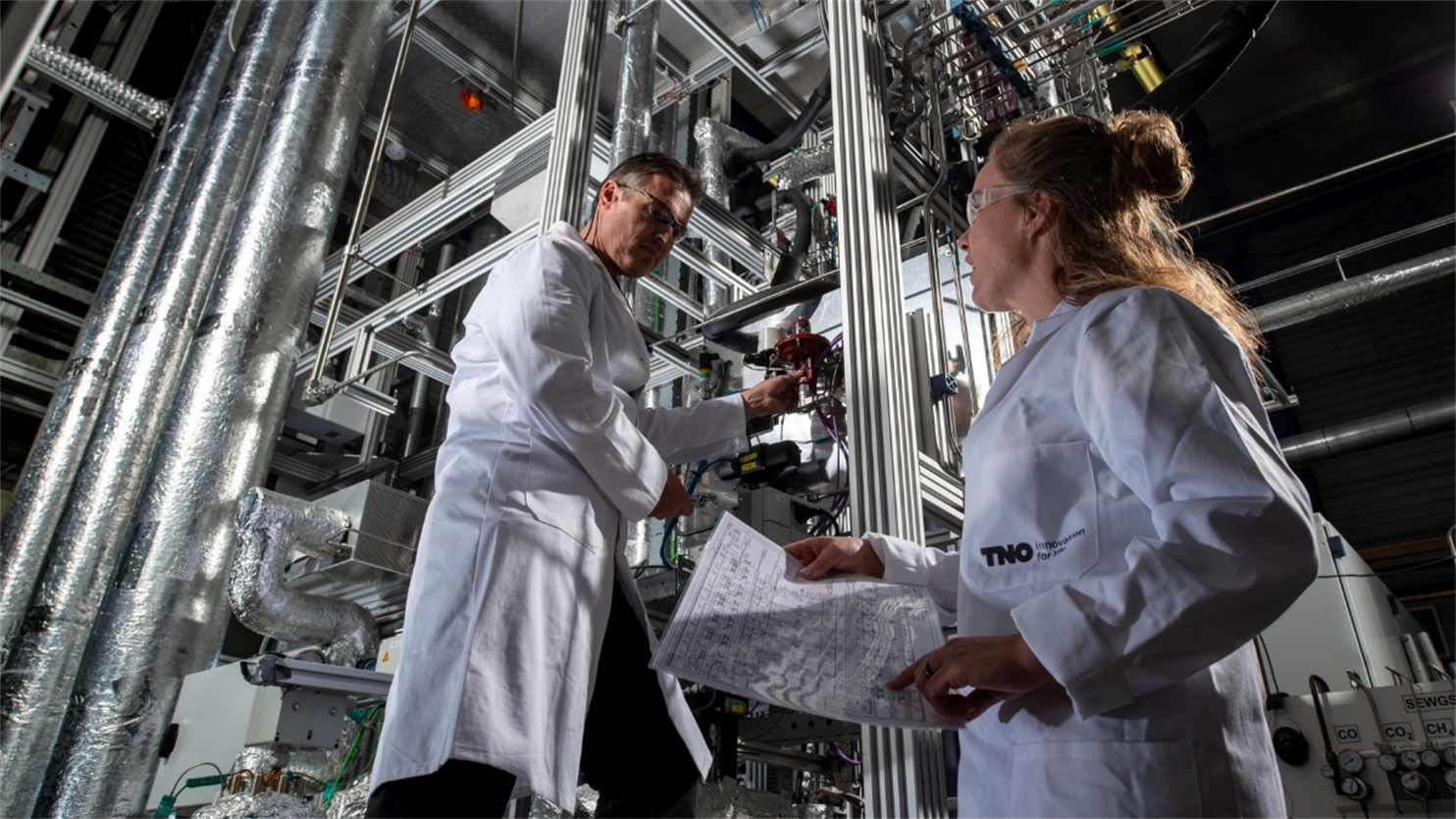
How does SEWGS work?
The SEWGS process combines 2 process steps in one reactor. The first process is known as the water-gas shift reaction. In this reaction, steam (H2O) converts carbon monoxide into carbon dioxide and hydrogen. Because this is a so-called equilibrium reaction, parts of the desired substances (hydrogen and carbon dioxide) revert to undesired substances (water and carbon monoxide). The reaction keeps itself in balance and complete conversion is impossible. To prevent this undesirable backward reaction as much as possible, a conventional process usually uses a great deal of steam.
This isn’t necessary if a company uses the SEWGS process. In fact, the second process prevents this undesirable reaction. Inside the reactor is a solid adsorption material (hydrotalcite enriched with potassium carbonate) that selectively binds acidic substances. Carbon dioxide, also known as carbonic acid, therefore remains attached to the surface of the adsorbent material. This prevents the carbon dioxide from reacting with hydrogen. An additional advantage is that other acidic substances, such as hydrogen sulphide, also bind to the surface of the adsorption material.
Combining these processes in a single reactor results in a much more efficient process, with less energy wasted. The captured carbon dioxide is already largely released when the pressure in the reactor decreases. But the last bit of CO2 that remains in the adsorbent material needs a steam flush. The heat from the process is suitable for this purpose. And because the solid adsorbent can tolerate high temperatures, such a steam flush is quite possible.
How is CO2 created by industry
Nearly all organic substances, both fossil fuels and agricultural waste streams, for example, can be converted into synthesis gas through gasification. This is a mixture of carbon monoxide (CO) and hydrogen gas (H2). Synthesis gas is also created as a by-product in steel production and oil refining. Until now, the industry has been using the gas as a fuel or input for other processes. The disadvantage is that the carbons in the gas enter the atmosphere in the form of CO2.
Want to know more about SEWGS?
We explain what SEWGS is with 10 questions and answers.
SEWGS used successfully
We have already successfully demonstrated the operation of the SEWGS process on an industrial scale at Swedish steel company SSAB. This steel producer retains blast-furnace gas, or synthesis gas, when converting iron ore into steel. Normally, the company uses some of the gas for heating its own processes. What remains goes to a power plant.
In the European Union-supported STEPWISE project, a SEWGS plant processed 800 cubic meters of blast-furnace gas per hour from one of the steel mills. On a daily basis, the pilot plant captured 14 tons of CO2.
The demonstration project shows that industry will save a great deal of costs by using SEWGS technology to capture CO2. The SEWGS process provides a 25% cost reduction compared to other technologies used to capture CO2, which brings the cost price down to about 33 euros per ton of captured CO2.
The BOF2UREA project completed in 2020 also showed that industry can cost-effectively produce urea from another type of steel gas: Basic Oxygen Furnace (BOF) gas. The INITIATE project builds on this with a prototype demonstration on an industrial scale and in an industrial environment. SEWGS plays a major part in this.
SEDMES: from CO2 to useful fuels
In addition to SEWGS, we also developed the SEDMES technology. We use it to convert captured CO2 with green hydrogen into useful by-products, chemicals and fuels (such as dimethyl ether).
Get inspired
Energy infrastructure and transport
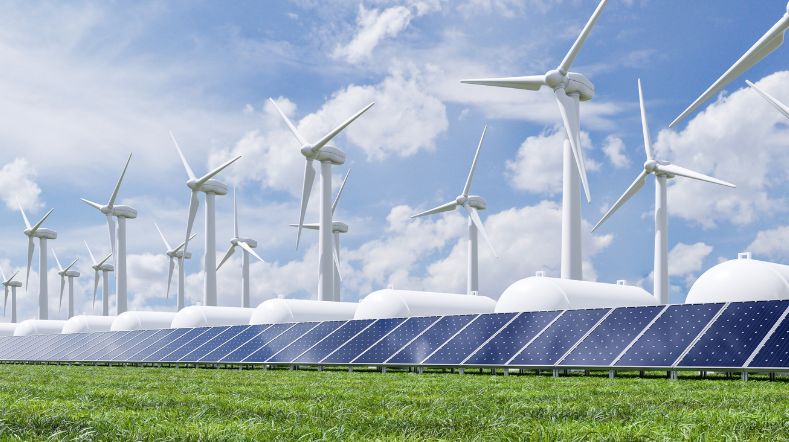
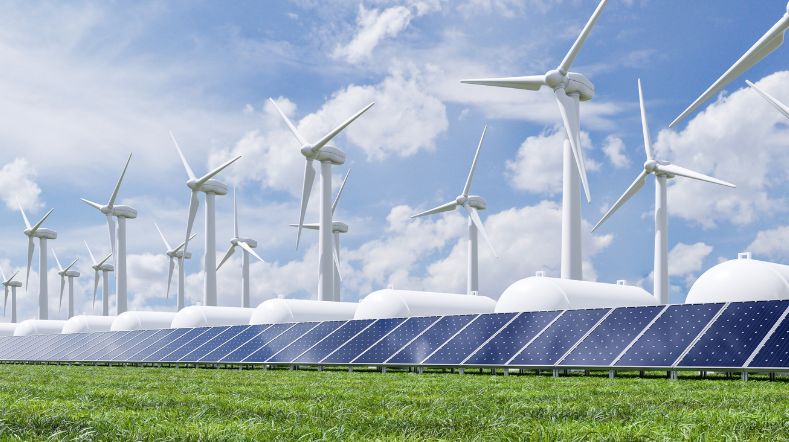
The North Sea as Europe's energy heart requires smart choices
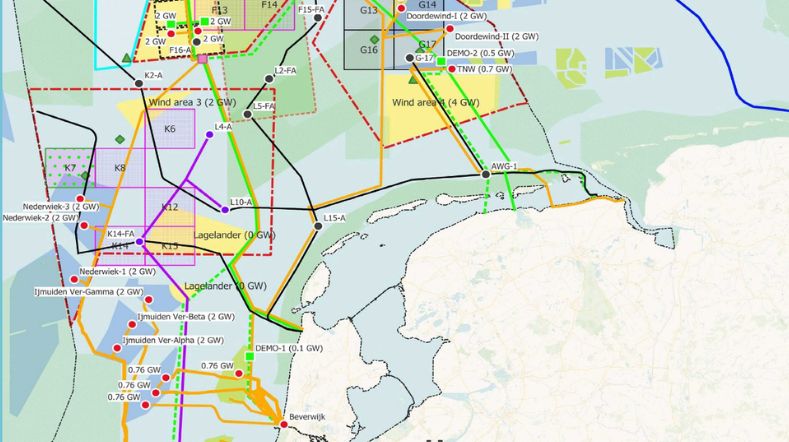
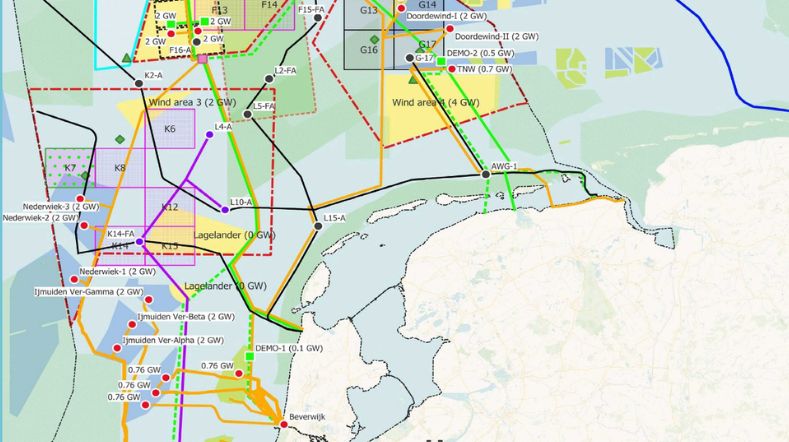
Tomorrow’s hydrogen production and infrastructure: building towards a secure and robust energy system
World Hydrogen Summit 2025
Scaling-up electrochemical technologies for renewable ethylene production
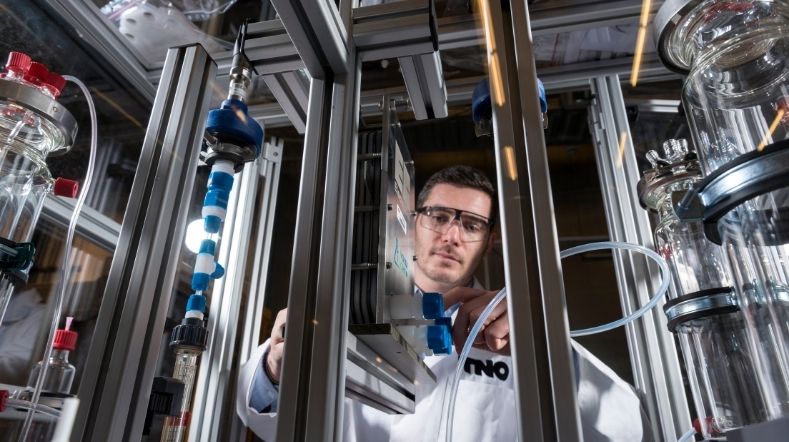
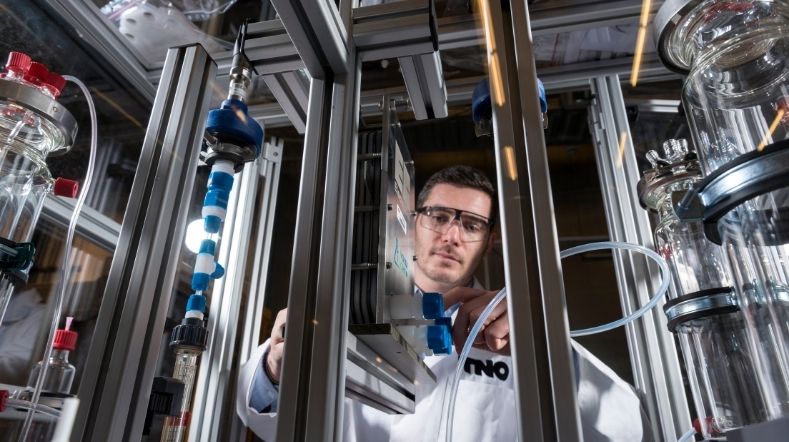